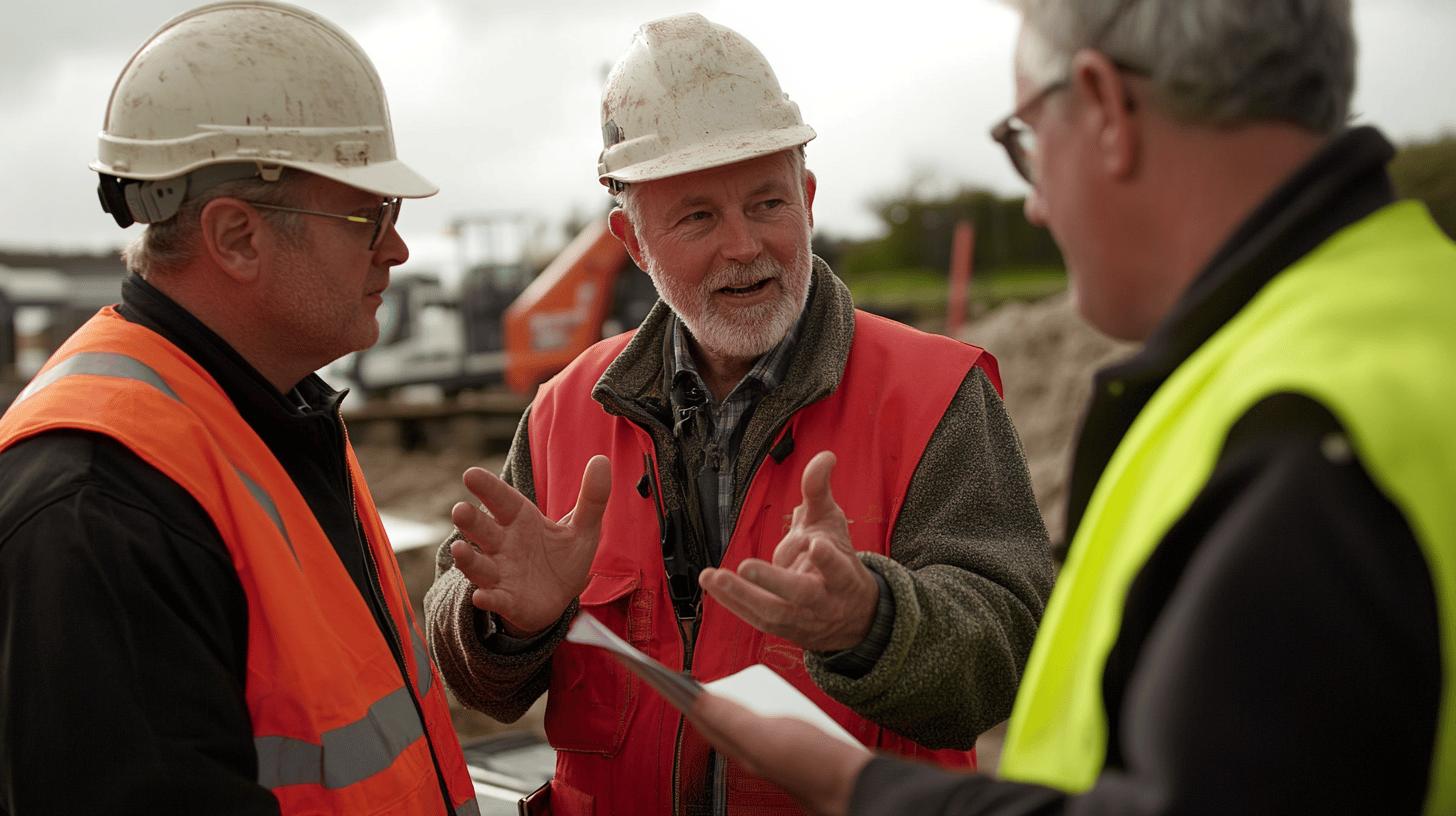
Supplier and Contractor Management: Reinforcing Safety Protocols
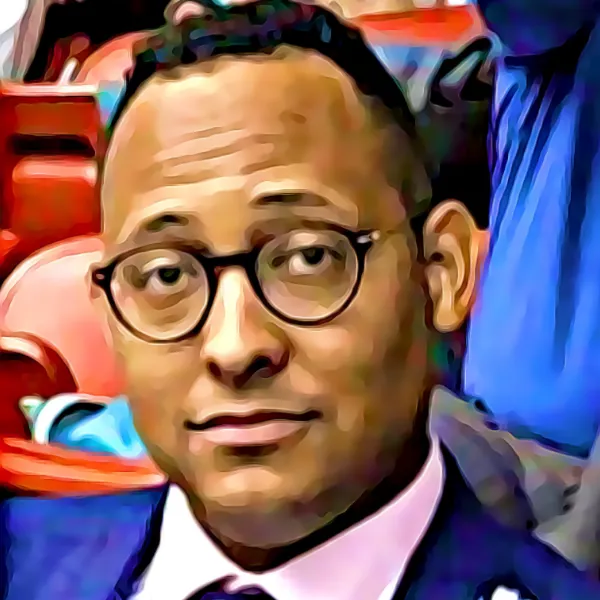
The Role of Supplier and Contractor Management in Reinforcing Safety Protocols in Food Sourcing
Managing suppliers and contractors effectively is crucial for maintaining rigorous safety protocols in food sourcing. Q-Hub recognises that whether called supplier management or vendor oversight, the goal remains consistent: ensuring every supply chain link upholds safety and quality standards. Without proper evaluation processes, businesses risk contamination issues, compliance failures, and reputation damage. Effective third-party management integrates compliance verification and risk mitigation at every stage, creating a comprehensive safety net that protects both companies and consumers.
In this context, learning more about supplier and contractor management can further enhance your understanding of how integrated systems support safety protocols. The comprehensive approach demonstrated in the linked article mirrors the need for robust supplier evaluation processes in maintaining high safety standards.
Suppliers and contractors directly impact critical food safety aspects, from ingredient quality to workplace standards. When a supplier fails to meet safety expectations, the entire supply chain faces disruption. Today's food businesses are increasingly turning to digital solutions to enhance monitoring capabilities, streamline compliance tracking, and maintain real-time visibility across supplier activities—transforming what was once merely regulatory compliance into an operational advantage.
Effective supplier management isn't just about avoiding problems—it's about building resilience into your food safety system through collaborative partnerships that prioritise transparency and continuous improvement.
Digitising Supplier Evaluation for Enhanced Safety
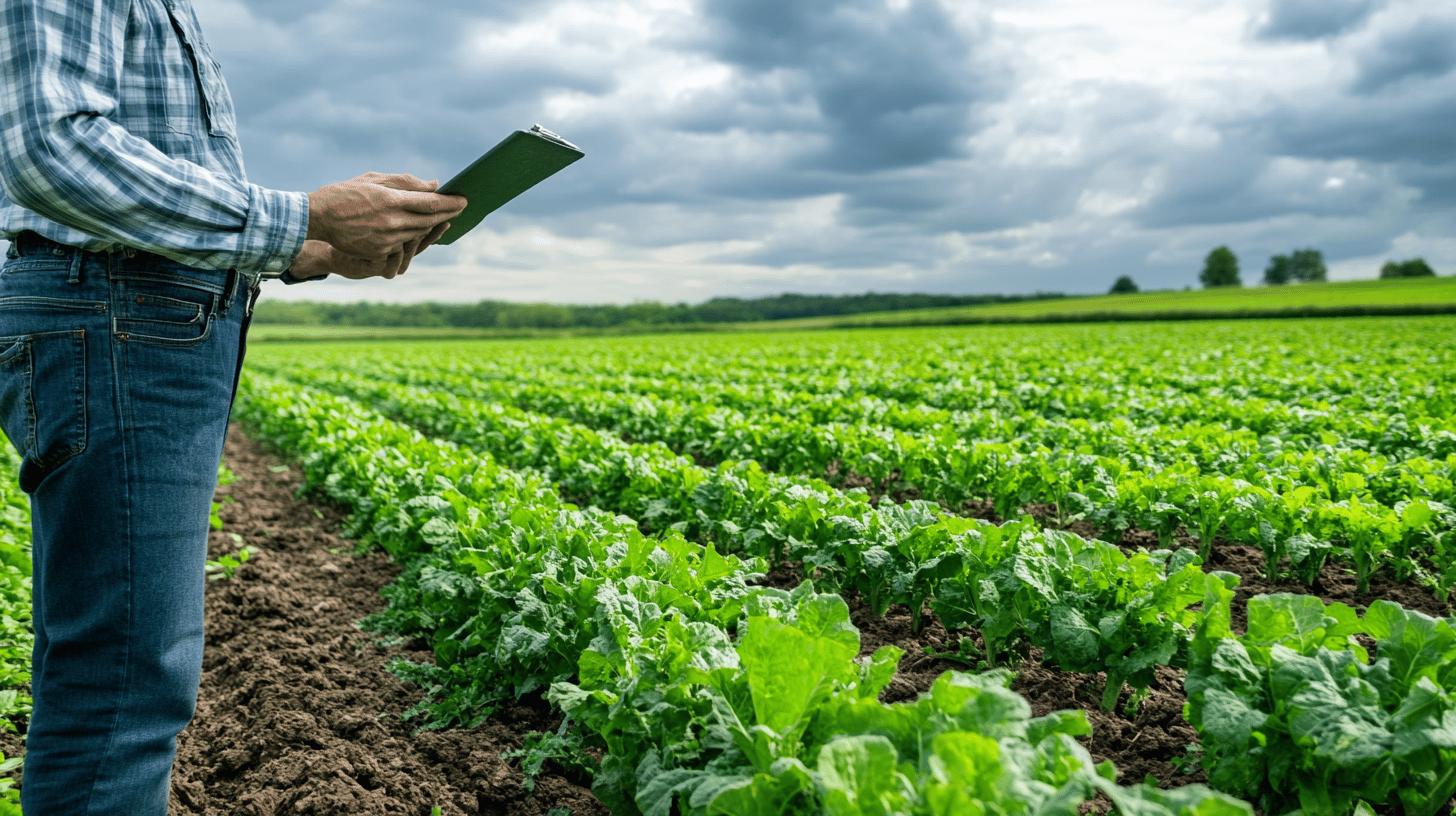
The key to effective supplier evaluation lies in establishing measurable, transparent criteria. While certifications like ISO 22000 provide a strong foundation, businesses need more than just documentation to ensure real safety. Q-Hub's digital solutions enable food companies to move beyond manual checklists to comprehensive, data-driven assessment systems.
Take Rocal Insulating Panels, for instance. Before implementing Q-Hub's digital platform, their document management relied on cluttered shared drives, leading to difficulties finding critical files and compliance gaps. With a centralised digital library offering version tracking and instant access, they eliminated hours of wasted time and significantly improved compliance monitoring for their suppliers and contractors.
A truly effective supplier relationship goes beyond basic compliance to foster accountability and collaboration. By treating suppliers as partners rather than mere vendors, businesses create alignment with safety protocols that extends throughout the supply chain. This collaborative approach proved transformative for Scottish Leather Group, who leveraged Q-Hub's platform to unify processes across multiple sites and achieve seamless compliance with various ISO standards.
Risk-Based Contractor Selection That Delivers Results
Selecting contractors for food-related operations demands a risk-based approach. Evaluating candidates based not only on technical capabilities but also on safety regulation adherence creates a foundation for reliable partnerships.
Further insights can be gained by exploring supplier and contractor management, where the focus is on enhancing food safety through systematic oversight. The article provides an analogous framework by highlighting how strategic partnerships and continuous monitoring serve as cornerstones in achieving operational excellence. Contractors should demonstrate proven experience with frameworks like Hazard Analysis and Critical Control Points (HACCP), and prioritise ongoing safety training for their workforce.
Compliance verification shouldn't end after initial selection. Ongoing assessments through site inspections, documentation reviews, and incident tracking help ensure contractors continue meeting expectations. BMC Analysis discovered this when they transformed their previously manual, error-prone quality management operations with Q-Hub's Process Hub. The centralised digital platform enabled automated tracking of non-conformances with suppliers and contractors, ensuring faster resolution and better oversight.
Here's how effective supplier management transforms food safety outcomes:
- Identifies potential safety gaps through thorough digital risk assessments
- Aligns contractors with industry standards through targeted safety training
- Ensures regulatory compliance via automated audit scheduling and tracking
- Maintains consistency through digital quality control monitoring
- Enhances traceability with real-time visibility of supplier activities
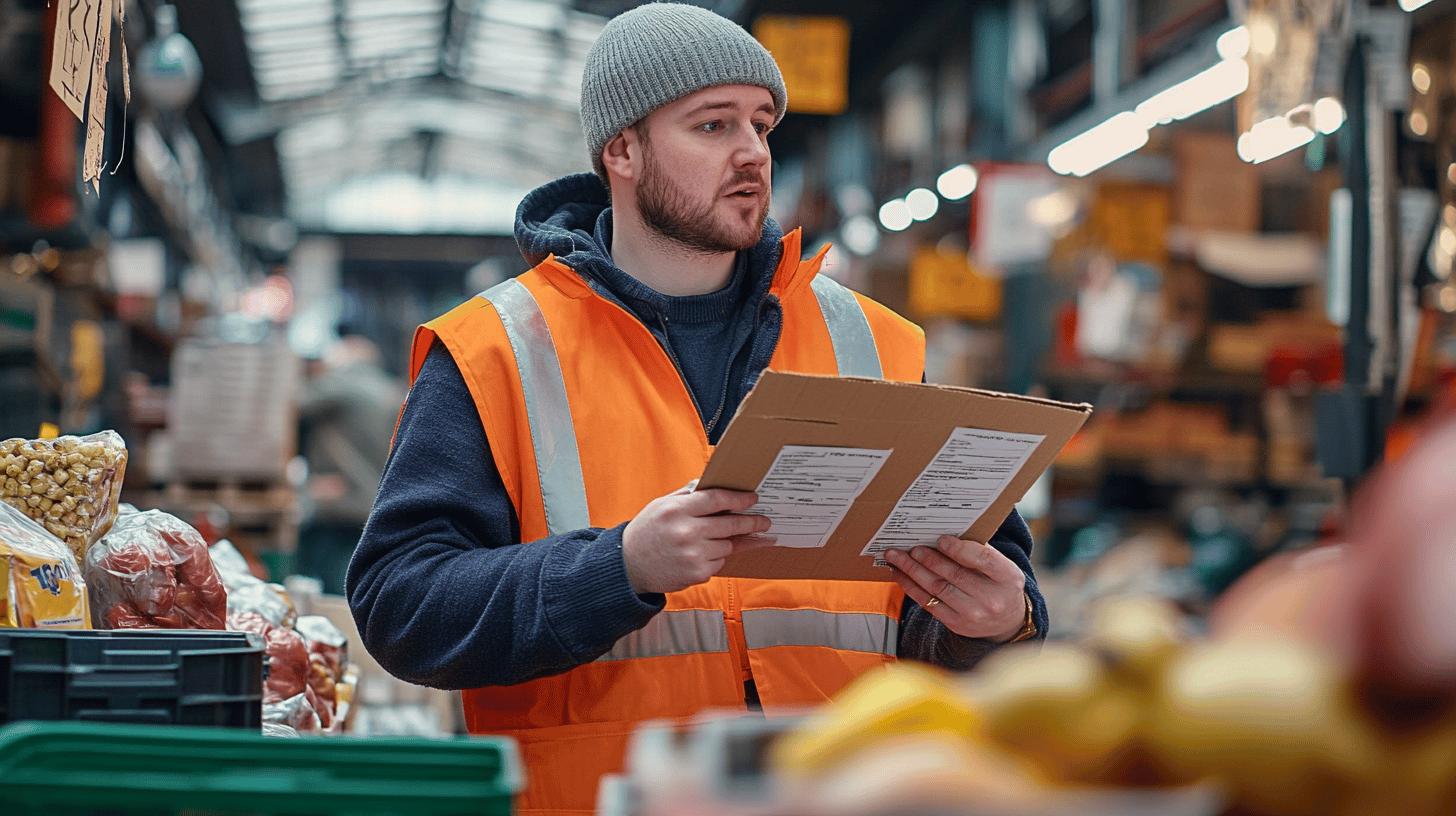
Regulatory Compliance Made Seamless
Food sourcing operates in a highly regulated environment with frameworks like FSMA 204 and the UK Modern Slavery Act setting safety compliance benchmarks. These regulations help prevent contamination, eliminate unethical practices, and minimise supply chain disruptions. Failure to comply not only endangers consumers but leads to legal penalties and reputational damage.
Weston Aerospace faced significant challenges in meeting these requirements through outdated systems. Their legacy processes created bottlenecks in key operations, with compliance teams bogged down by repetitive manual tasks. After implementing Q-Hub's modular platform, they achieved dramatic improvements in compliance management. Automated audit scheduling, real-time dashboards, and digitised workflows transformed their supplier oversight, freeing staff to focus on strategic priorities rather than administrative burdens.
Regular compliance audits and comprehensive traceability initiatives form the backbone of regulatory alignment. By integrating these practices through digital tools, businesses build resilient supply chains that protect both public health and company reputation. As Fowlers of Bristol discovered, centralising critical workflows, datasets, and communications into a single digital space enables real-time access to compliance data and fosters collaboration between teams.
Technology That Transforms Supplier Management
In today's food industry, supplier management has evolved from tedious manual processes into technology-driven systems essential for reinforcing safety protocols. Digital platforms like Q-Hub offer unprecedented precision and efficiency in supply chain oversight. These solutions aren't optional luxuries—they're fundamental tools for ensuring compliance, improving transparency, and safeguarding food quality.
Artificial intelligence is revolutionising supplier risk identification and mitigation. By analysing vast datasets including certifications, performance history, and even external factors like regional risks, AI pinpoints vulnerabilities that traditional methods might miss. This precision enables businesses to focus attention where most needed, significantly reducing disruption risks.
For Anglia Cathodic Protection, automation transformed their previously fragmented compliance processes. Before implementing Q-Hub, managing quality processes involved disjointed spreadsheets and paper systems, leading to miscommunication and errors. By digitising these processes, they eliminated bottlenecks and enhanced operational oversight—particularly for non-conformance tracking and supplier audits.
<table border="0"> <tr><th>Process</th><th>Before Automation</th><th>After Automation</th></tr> <tr><td>Supplier Audit Preparation</td><td>Days of manual document gathering</td><td>Hours of automated verification</td></tr> <tr><td>Non-Conformance Resolution</td><td>Weeks with frequent follow-up</td><td>Days with automated tracking</td></tr> <tr><td>Document Control</td><td>Manual version tracking and distribution</td><td>Instant access with automated updates</td></tr> <tr><td>Supplier Performance Monitoring</td><td>Quarterly manual reviews</td><td>Real-time dashboard visibility</td></tr> </table>Building Resilience Through Collaborative Partnerships
When supplier collaboration thrives, it transforms traditional certification processes into proactive partnerships. These relationships foster shared accountability, stronger safety systems, and improved food safety outcomes. Joint training programmes, integrated management systems, and shared certification models deliver measurable improvements in safety protocol adherence.
Consider how Fowlers of Bristol revolutionised their approach to quality management using Q-Hub's digital platform. By centralising communication and data management, they brought critical workflows and datasets into a single space, fostering instant collaboration between engineering teams, shop floor workers, and compliance managers responsible for supplier oversight.
The pattern is clear: collaboration builds resilience. By treating suppliers as partners rather than separate entities, businesses align safety goals, establish consistent standards, and drive continuous improvement. The result is safer food sourcing, stronger compliance, and a supply chain prepared for long-term success.
Sustainable Sourcing: The New Safety Imperative
Sustainability and ethical sourcing practices are now operational necessities in food supply chain management. Supplier oversight that prioritises transparency and accountability not only meets growing consumer and regulatory demands but actively reinforces safety protocols by reducing risks associated with unethical practices, environmental degradation, and supply chain disruptions.
By embedding traceability systems into supplier management processes, businesses can track every supply chain stage, ensuring adherence to environmental, social, and governance standards. These systems provide critical insights into supplier behaviours, allowing early risk identification and mitigation. This visibility fosters stakeholder trust, strengthens compliance efforts, and enhances long-term supply chain sustainability.
Implementing a continuous improvement approach keeps safety protocols relevant and effective. Regular audits uncover blind spots, identify compliance gaps, and evaluate supplier performance—but companies achieving the best results pair this with strong feedback loops where suppliers actively share insights. This collaborative approach transforms data into actionable improvements, building both accountability and innovation.
Q-Hub's digital transformation solutions provide the foundation for this evolution in supplier management. By streamlining processes, enhancing visibility, and fostering collaboration, our platform enables food businesses to build safer, more resilient supply chains that adapt to emerging challenges while maintaining the highest safety standards. Ready to transform your supplier management approach? Discover how Q-Hub's customised QHSE software solutions can help you reinforce safety protocols while driving operational excellence.
<