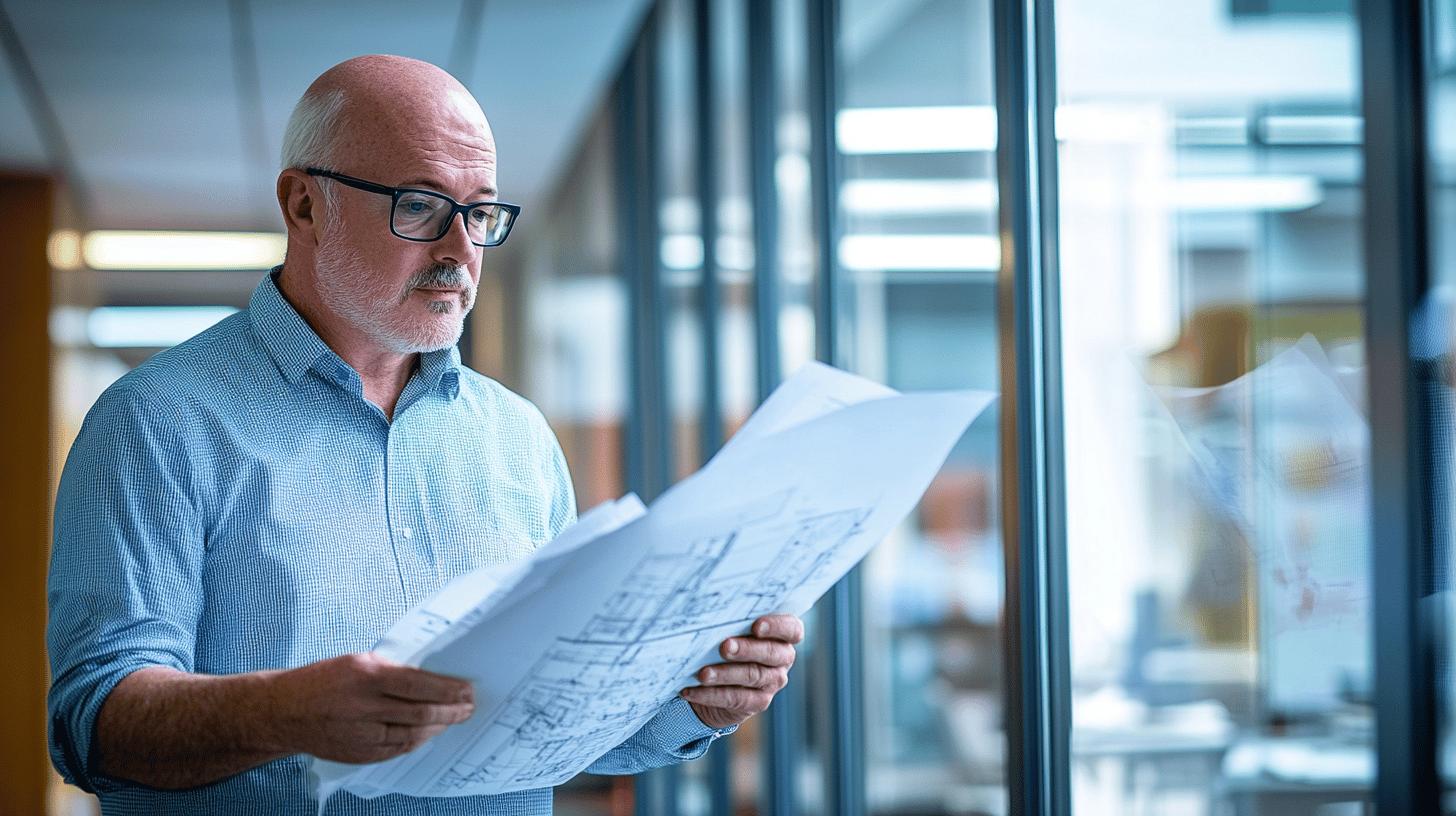
Custom Development Projects Address Unique Facilities Risks
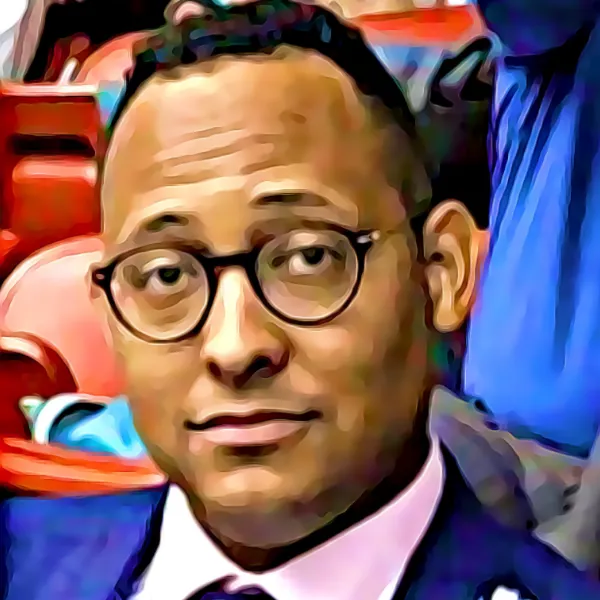
The Role of Custom Development Projects in Addressing Risk Management Challenges in Facilities Operations
Custom development projects are essential for tackling unique risk management challenges in facilities operations.
By utilizing our custom development projects, organizations can build tailored systems that not only address specific operational risks but also enhance overall safety and compliance. This specialized approach helps companies transition from generic solutions to robust, risk-focused strategies that reflect their unique operational needs. Unlike off-the-shelf software, these tailored solutions address specific operational risks such as compliance gaps and resource inefficiencies. Q-Hub's bespoke systems enable organisations to maintain operational efficiency, enhance safety, and meet regulatory requirements in ways that standardised tools simply cannot achieve.
Risk management in facilities operations requires identifying, analysing, and mitigating threats that could disrupt business continuity or safety. Custom projects excel by integrating preventive measures like regular inspections and predictive maintenance into operational frameworks. This approach reduces downtime while ensuring compliance with UK regulations including the Health and Safety at Work Act 1974. Real-time risk dashboards and IoT-enabled monitoring systems further empower teams to be proactive rather than reactive.
Why Facilities Operations Need Tailored Risk Solutions
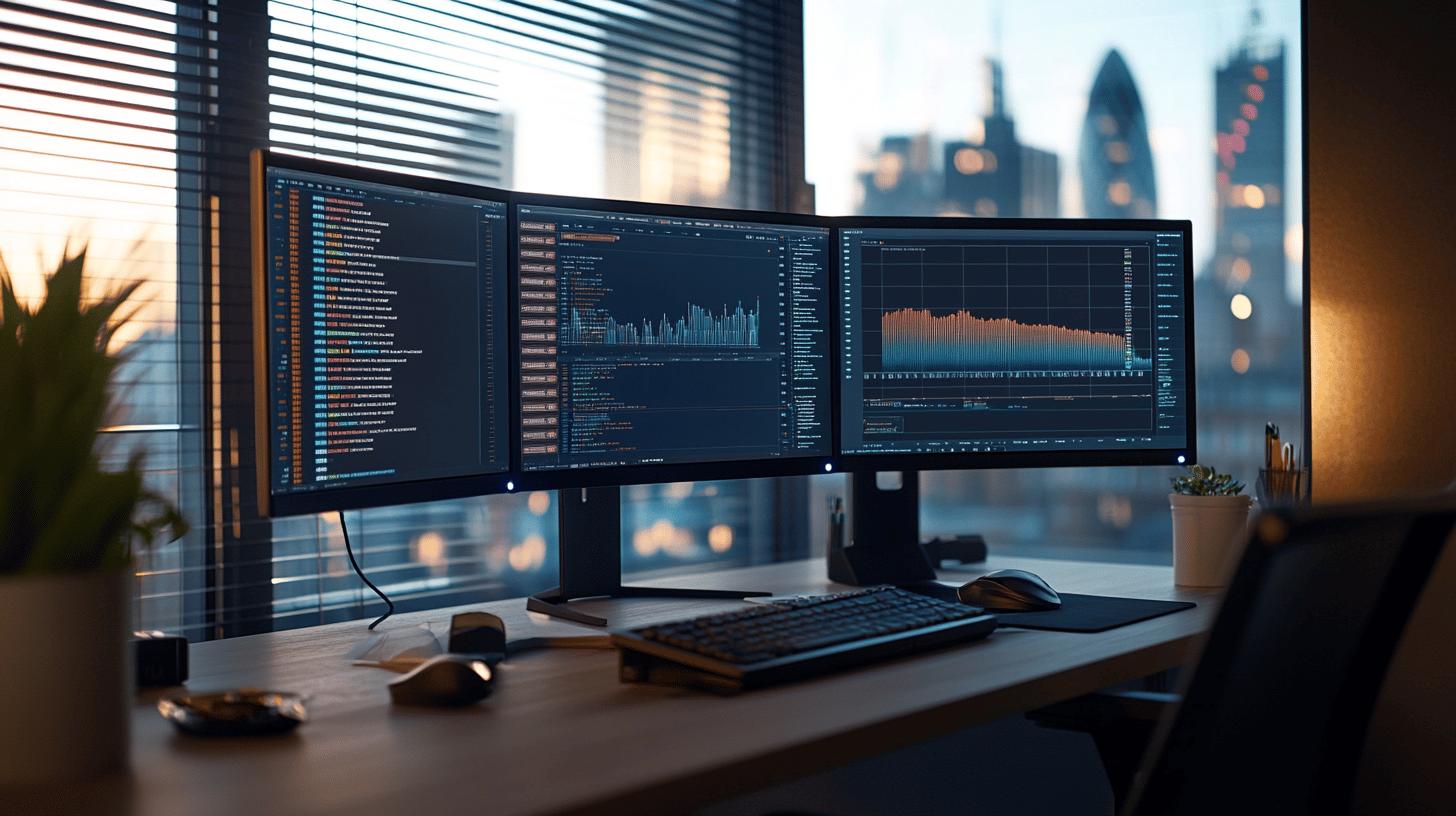
The one-size-fits-all approach simply doesn't work when it comes to facilities risk management. Each operation faces unique challenges that require specific solutions. From manufacturing plants to commercial buildings, the risk landscape varies dramatically based on industry, scale, and regulatory requirements.
Consider the common challenges facilities face: equipment failures causing unexpected downtime, emergency preparedness gaps, inefficient resource allocation, outdated risk assessment protocols, and lack of integration with modern technologies. Generic solutions often fail to address these specific pain points, leaving organisations vulnerable.
While generic solutions might tick compliance boxes, custom development delivers what operations truly need—a framework designed specifically for their unique challenges and growth trajectory. Source: Weston Aerospace case study
Real-World Transformation Stories
Scottish Leather Group (SLG) faced significant challenges managing compliance across multiple sites with paper-based systems. By implementing Q-Hub's custom solution, they unified processes, streamlined compliance, and digitised critical workflows. The transformation included tailored audit management, asset tracking, and document control systems.
Similarly, Anglia Cathodic Protection Services turned to Q-Hub when their paper and spreadsheet-based systems couldn't handle increasing workloads. Their fragmented processes hindered effective compliance management across multiple sites. Q-Hub's platform digitised these processes, making them more accessible and actionable while eliminating bottlenecks.
At Rocal Insulating Panels, paper-based accident reporting and investigation created significant obstacles to efficiency. Managers struggled with incomplete records and lengthy delays in closing investigations. Q-Hub's automated workflows transformed this process, enabling quicker resolution and better involvement of department managers.
Critical Capabilities That Drive Operational Excellence
Custom risk management solutions offer several standout features that address operational challenges directly. Risk dashboards provide real-time visibility into hazards, allowing swift action. Predictive analytics identifies risks before they materialise, enabling proactive management rather than reactive firefighting.
Compliance tracking modules ensure adherence to evolving regulations, minimising the risk of fines. Workflow automation streamlines processes and reduces errors, while IoT integration enhances monitoring capabilities across assets. Custom reporting tools transform raw data into actionable insights for effective resource prioritisation.
Companies embracing these innovations typically experience the following benefits:
- Real-time risk visibility through customised dashboards
- Proactive issue identification via predictive analytics
- Automated compliance monitoring with regulatory updates
- Streamlined workflows reducing manual intervention
- Enhanced asset monitoring through IoT integration
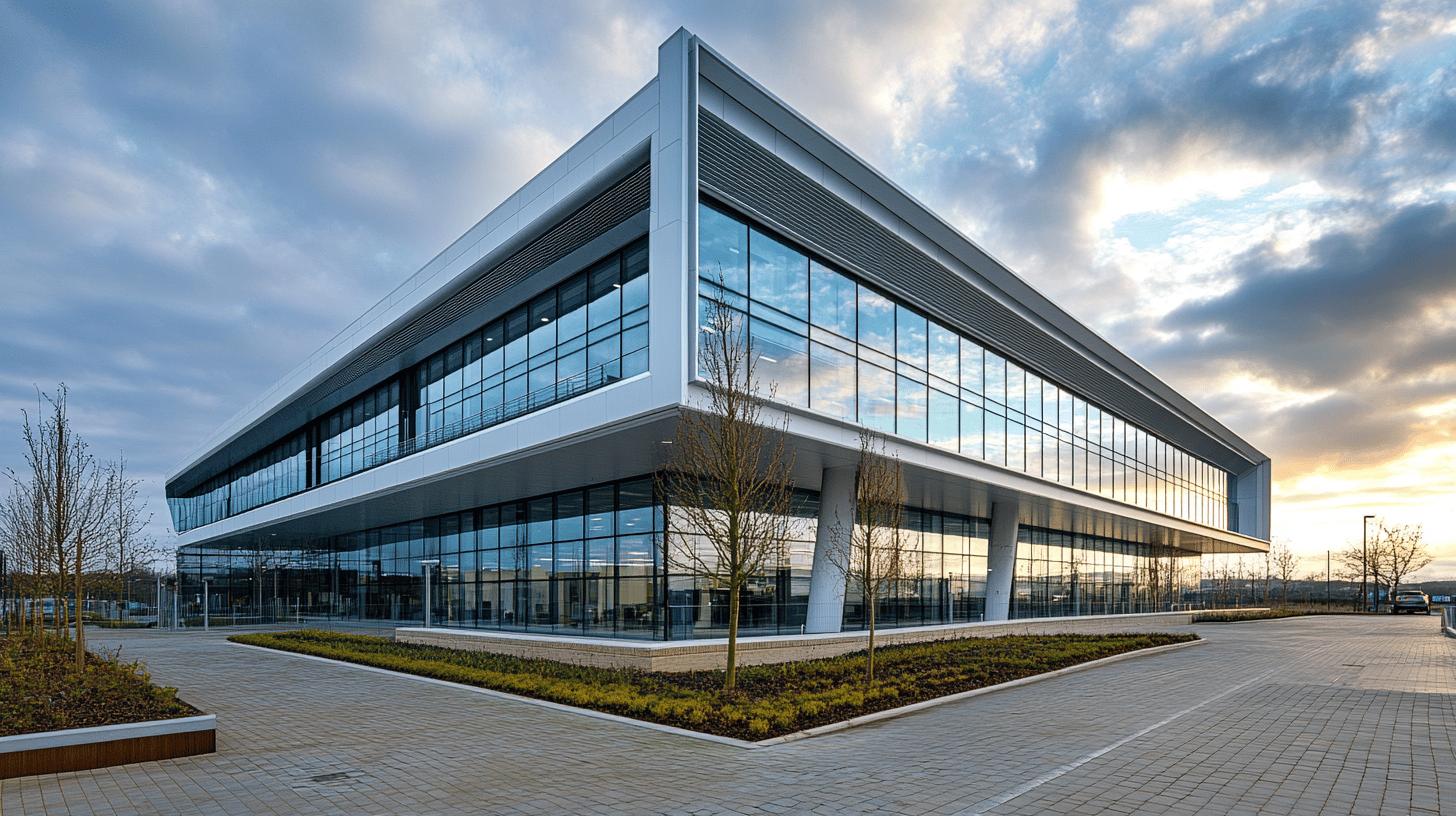
Implementation Strategies That Ensure Success
When implementing custom development projects for facilities risk management, success hinges on a clear, actionable roadmap. Effective implementation strategies such as phased rollouts and stakeholder collaboration reduce risks and ensure smooth adoption. A phased approach allows testing and refinement before scaling up, minimising disruptions and aligning with operational goals.
Stakeholder collaboration is equally important. Involving cross-functional teams ensures that all operational perspectives are considered, improving usability and fostering buy-in. For example, BMC Analysis struggled with tracking non-conformance reports (NCRs) through Word documents and fragmented email communication. Q-Hub's Process Hub revolutionised this workflow by offering a centralised, digital platform with automated tracking and reporting.
The implementation process must include these critical elements:
<table border="0"> <tr><th>Implementation Strategy</th><th>Impact on Success</th></tr> <tr><td>Phased Rollout</td><td>Reduces disruption by allowing refinement before full deployment</td></tr> <tr><td>Stakeholder Engagement</td><td>Ensures system meets actual user needs across departments</td></tr> <tr><td>Continuous Feedback</td><td>Enables adaptation to evolving operational requirements</td></tr> <tr><td>Comprehensive Training</td><td>Maximises user adoption and proper system utilisation</td></tr> </table>Measurable Impact on Operational Performance
Custom development projects deliver tangible improvements in operational efficiency and compliance. By focusing on specific pain points in facilities management, these bespoke systems transform how organisations work. Real-time data analysis has been shown to reduce operational risks by up to 25% in certain implementations.
Efficiency improvements come through automation of repetitive tasks, system integration, and actionable insights from predictive analytics. Facilities leveraging custom solutions often report reduced costs and fewer downtimes. For instance, Fowlers of Bristol implemented Q-Hub's document management tools and saw significant reduction in errors and administrative effort through robust version controls and linked documents.
Compliance management also improves dramatically. When Scottish Leather Group implemented Q-Hub, they gained seamless management of multiple ISO standards within a single platform. The Audit Hub significantly reduced audit preparation time, freeing resources for value-added activities while ensuring consistent regulatory compliance.
The Future of Facilities Risk Management
The landscape of facilities risk management continues to evolve with technological advancements. AI-driven analytics, IoT-enabled systems, and predictive maintenance are reshaping how organisations approach risk mitigation. These technologies allow facilities to not only respond to issues but anticipate and prevent them before they occur.
Q-Hub's development of these advanced capabilities allows organisations to future-proof their operations. By adopting scalable and adaptive technologies, facilities can prepare for increasingly dynamic risks and more stringent regulations.
Exploring custom development projects further illustrates how bespoke digital solutions are central to evolving risk management strategies. This innovative approach not only anticipates future regulatory demands but also transforms the way organizations safeguard their operations, blending cutting-edge technology with strategic planning. The focus shifts from merely addressing today's problems to building resilience against tomorrow's challenges.
As facilities operations become more complex, the need for custom development projects to address unique risk management challenges will only grow. Q-Hub's tailored digital solutions continue to evolve, helping organisations transform their approach to operational safety, compliance, and efficiency through innovative software that meets their specific needs.
Ready to transform your facilities risk management with tailored digital solutions? Discover how Q-Hub's custom development projects can address your unique operational challenges while delivering measurable improvements in efficiency, compliance, and safety.