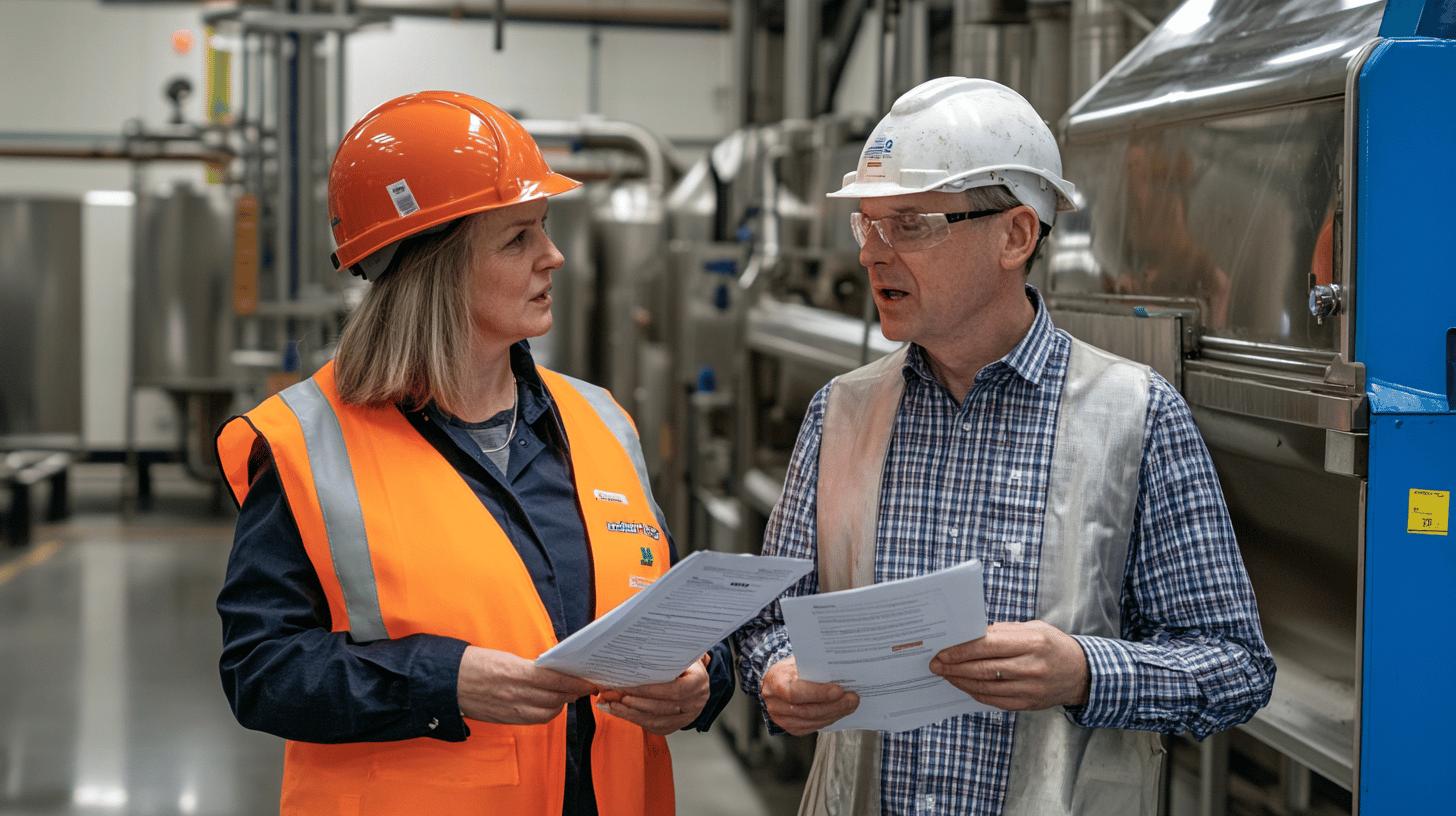
Supplier and Contractor Management Enhances Food Safety
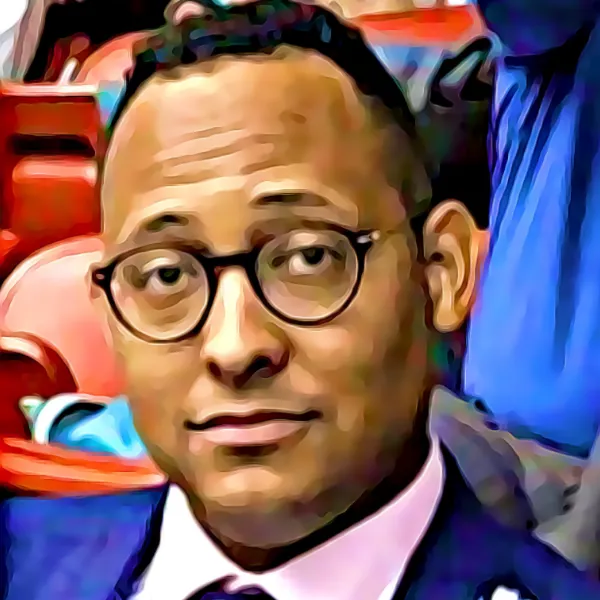
The Role of Supplier and Contractor Management in Ensuring Food Product Safety and Quality
Effective supplier and contractor management is fundamental to food safety and quality assurance. By overseeing vendors meticulously, businesses safeguard compliance with HACCP and ISO standards while building trusted partnerships. Without robust management systems, regulatory lapses can compromise product integrity and potentially harm consumers. Q-Hub's digital solutions help food businesses transform their supplier management processes, replacing fragmented paper-based systems with streamlined digital workflows.
Managing suppliers in the food industry presents unique challenges. Suppliers may display proper certifications yet fail actual compliance checks, while contractors might compromise on safety protocols to reduce costs. These challenges intensify with global supply chains, where oversight becomes increasingly complex. An effective management approach must include continuous evaluation and real-time monitoring to maintain safety standards.
Transforming Supplier Oversight with Digital Solutions
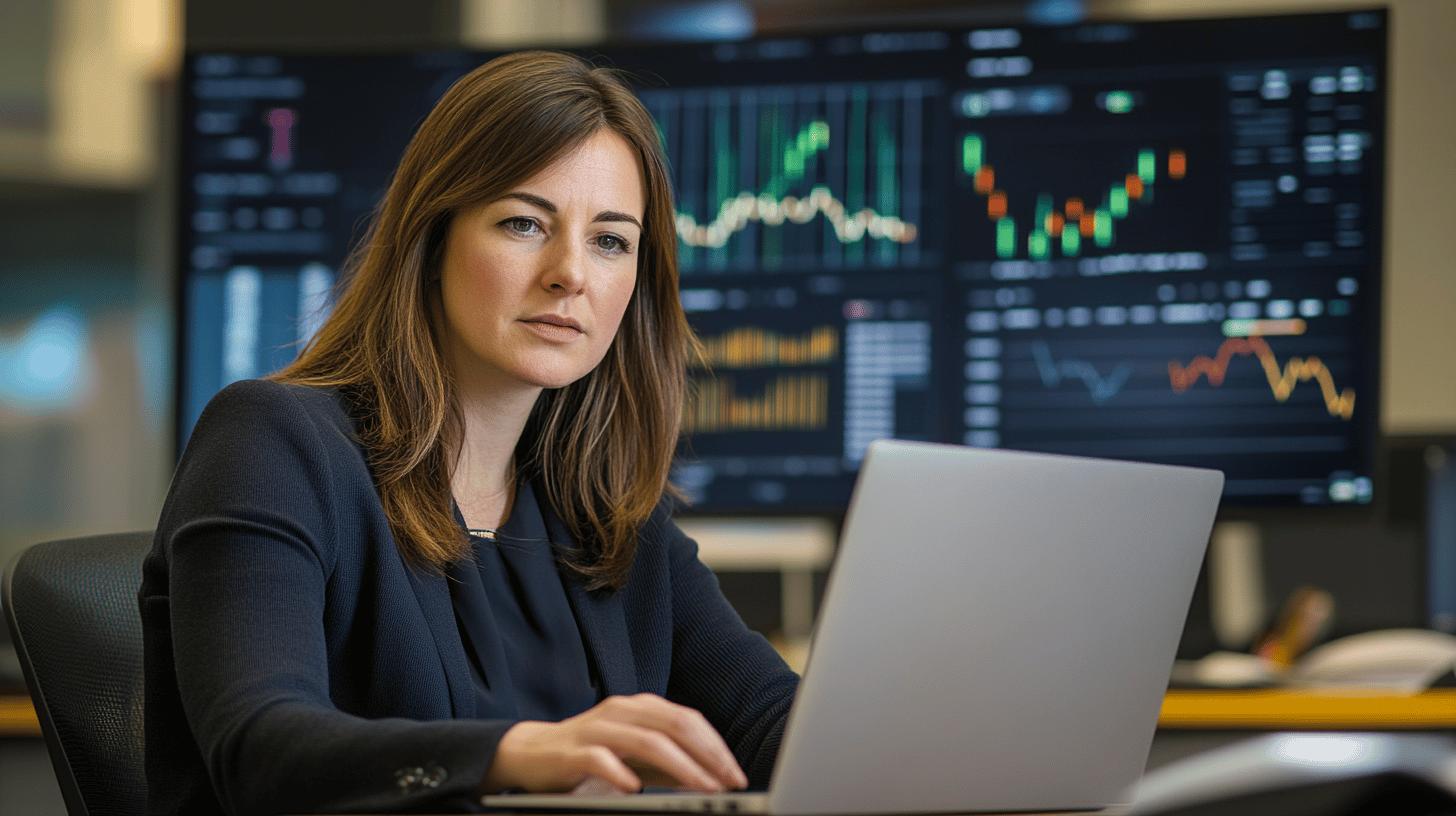
The days of managing food suppliers using manual processes are rapidly disappearing. Modern digital platforms like Q-Hub's Process Hub allow businesses to centralise and automate critical supplier management tasks. With Scottish Leather Group, for example, Q-Hub implemented a digital transformation that unified previously fragmented compliance processes across multiple sites, creating a cohesive quality management system.
When Anglia Cathodic Protection Services faced challenges with their paper-based supplier processes, Q-Hub's solution digitised these workflows, making compliance monitoring accessible and actionable for all employees. This resulted in improved operational oversight and eliminated communication bottlenecks that previously hindered effective supplier management.
"Qhub's ability to share necessary documents and track 'read and understood' acknowledgments was transformative. The entire workforce could access the tools and information needed to perform their roles effectively."
Key responsibilities in effective supplier management include:
- Evaluating supplier qualifications and certifications
- Conducting regular supplier audits with digital tracking
- Monitoring performance metrics through centralised dashboards
- Ensuring compliance with food safety standards
- Building sustainable supplier relationships
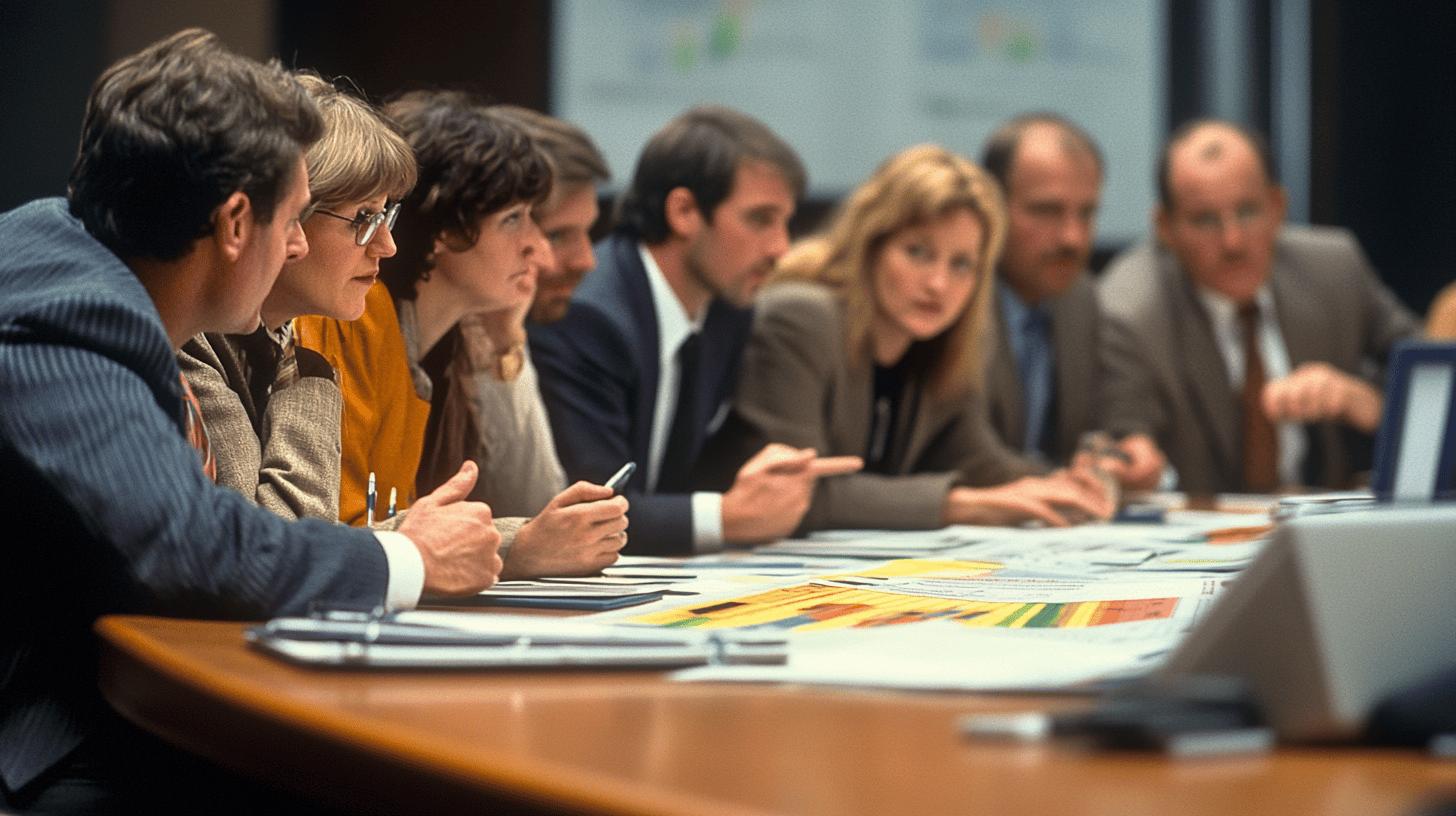
Streamlining Compliance Through Systematic Audits
Supplier audits are critical for maintaining food safety standards and regulatory compliance. Q-Hub's Audit Hub enables systematic evaluation of suppliers against HACCP protocols and hygiene practices, creating a digital trail of accountability. For Weston Aerospace, implementing Q-Hub's audit tools significantly reduced preparation time while enhancing audit thoroughness.
An effective audit approach follows these key steps:
- Define audit objectives and criteria - Clearly outline specific compliance goals, whether checking HACCP adherence or traceability systems
- Review supplier documentation - Examine food safety certifications and quality control records digitally
- Conduct on-site inspections - Assess operations firsthand with mobile audit tools
- Document non-conformances - Use digital systems to track and manage findings
- Implement corrective actions - Schedule follow-up audits through automated systems
These digitised audit processes not only verify compliance but drive continuous improvement. As demonstrated in Rocal Insulating Panels' implementation of Q-Hub, moving from paper-based to digital audit systems eliminated hours of wasted time in preparation and follow-up.
Harnessing Technology for Enhanced Traceability
Technology has revolutionised how food companies manage suppliers and contractors. Modern systems provide unprecedented visibility into supply chains, enhancing both safety and efficiency. Consider these transformative technologies:
<table border="0"> <tr><th>Technology</th><th>Traditional Process</th><th>Digital Transformation</th></tr> <tr><td>Supplier Audits</td><td>Paper forms, manual tracking</td><td>Digital schedules, real-time reporting</td></tr> <tr><td>Compliance Verification</td><td>Periodic inspections</td><td>Continuous monitoring, alerts</td></tr> <tr><td>Documentation</td><td>Physical filing systems</td><td>Centralised digital repositories</td></tr> </table>Fowlers of Bristol experienced these benefits firsthand when they implemented Q-Hub's document management tools. Their system transformed from manual tracking to automated workflows with version control, ensuring every team had access to the latest information. This reduced errors and administrative burdens while improving food safety compliance.
Building Resilient Supplier Partnerships
Sustainable supplier relationships require more than transactions—they demand shared objectives and transparent communication. BMC Analysis found that moving supplier management to Q-Hub's centralised platform significantly improved communication clarity and streamlined NCR management, strengthening vendor relationships.
Effective supplier engagement thrives on active feedback and development. Regular performance reviews through digital dashboards allow businesses to identify improvement areas quickly. When paired with targeted training, these insights significantly enhance supplier capabilities and compliance rates.
The benefits of well-managed supplier relationships include:
- Consistently higher product quality
- Reduced supply chain disruptions
- Improved compliance with safety standards
- Greater innovation and adaptability
- Enhanced brand reputation and customer trust
Digital tools play a crucial role in sustaining these relationships. Q-Hub's Process Hub provides a framework for continuous improvement, enabling collaborative problem-solving between food companies and their suppliers rather than merely policing compliance.
Preventing Risks Through Proactive Management
Food sourcing carries inherent risks—contamination, supply disruptions, and regulatory non-compliance chief among them. Effective digital supplier management systems help mitigate these risks through early detection and preventive controls.
Three essential preventive strategies include:
- Supplier diversification - Reducing dependency on single sources minimises vulnerability
- Real-time performance monitoring - Digital dashboards provide instant visibility into supplier metrics
- Robust traceability systems - Digital tracking enables rapid response during potential recalls
When Scottish Leather Group implemented Q-Hub's digital platform, they transformed their ability to monitor compliance across multiple sites, significantly reducing risk exposure while improving efficiency. The unified system allowed them to identify potential issues before they became serious problems.
Ready to transform your supplier management approach? Q-Hub offers comprehensive digital solutions that streamline compliance, enhance traceability, and strengthen supplier relationships. Our customised QHSE software helps food businesses ensure product safety and quality while reducing operational costs through efficient, digital workflows.