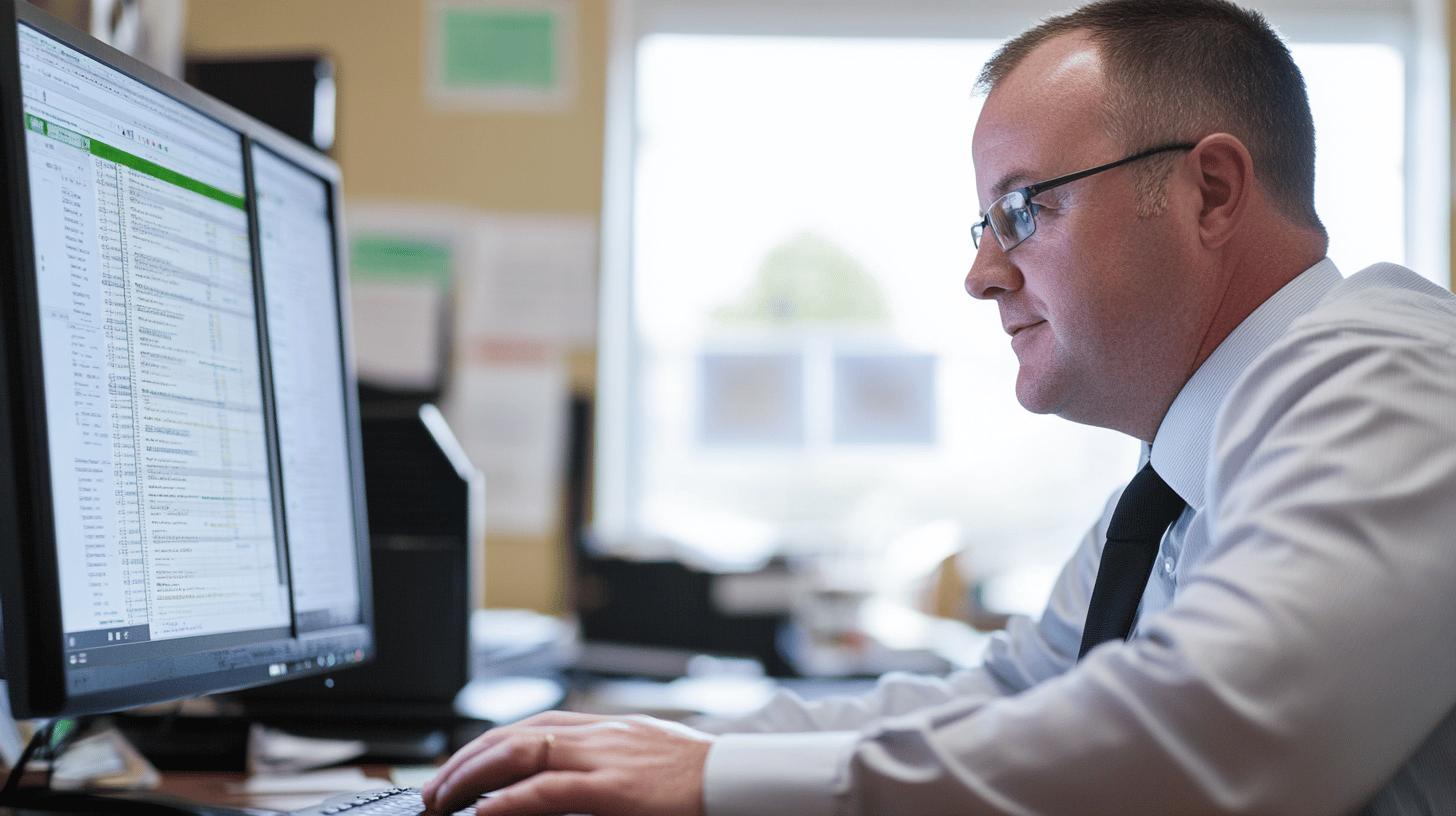
Integration with ERP Systems Enhances Incident Reporting
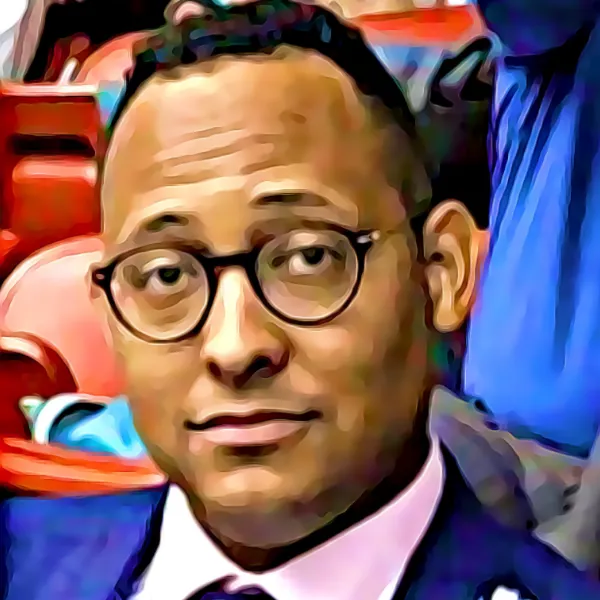
How ERP System Integration Streamlines Incident Reporting for Engineering Supply Chains
Integrating ERP systems into incident reporting processes transforms how engineering supply chains manage safety and compliance.
By adopting integration with ERP systems, organisations not only streamline their incident reporting but also enhance overall system connectivity and risk management. This integration builds a robust framework for quick data transfer, ensuring that every incident is recorded and tackled proactively, much like connecting the gears of a well-oiled machine. Q-Hub's specialised software solutions make this integration seamless, connecting previously isolated systems into a cohesive operational framework. Without this unified approach, organisations often struggle with delayed reporting, information gaps, and inconsistent compliance—issues that directly impact operational efficiency and safety standards.
When incident data flows automatically between departments, the benefits are immediate and significant. For instance, when a safety incident occurs on a production line, an integrated ERP system instantly alerts relevant teams, initiates response protocols, and begins documentation for compliance purposes—all without manual intervention.
Engineering companies that implement integrated incident reporting systems see up to 60% reduction in response times and significant improvements in compliance adherence. Source: Scottish Leather Group case study findings
Breaking Down Data Silos for Enhanced Visibility
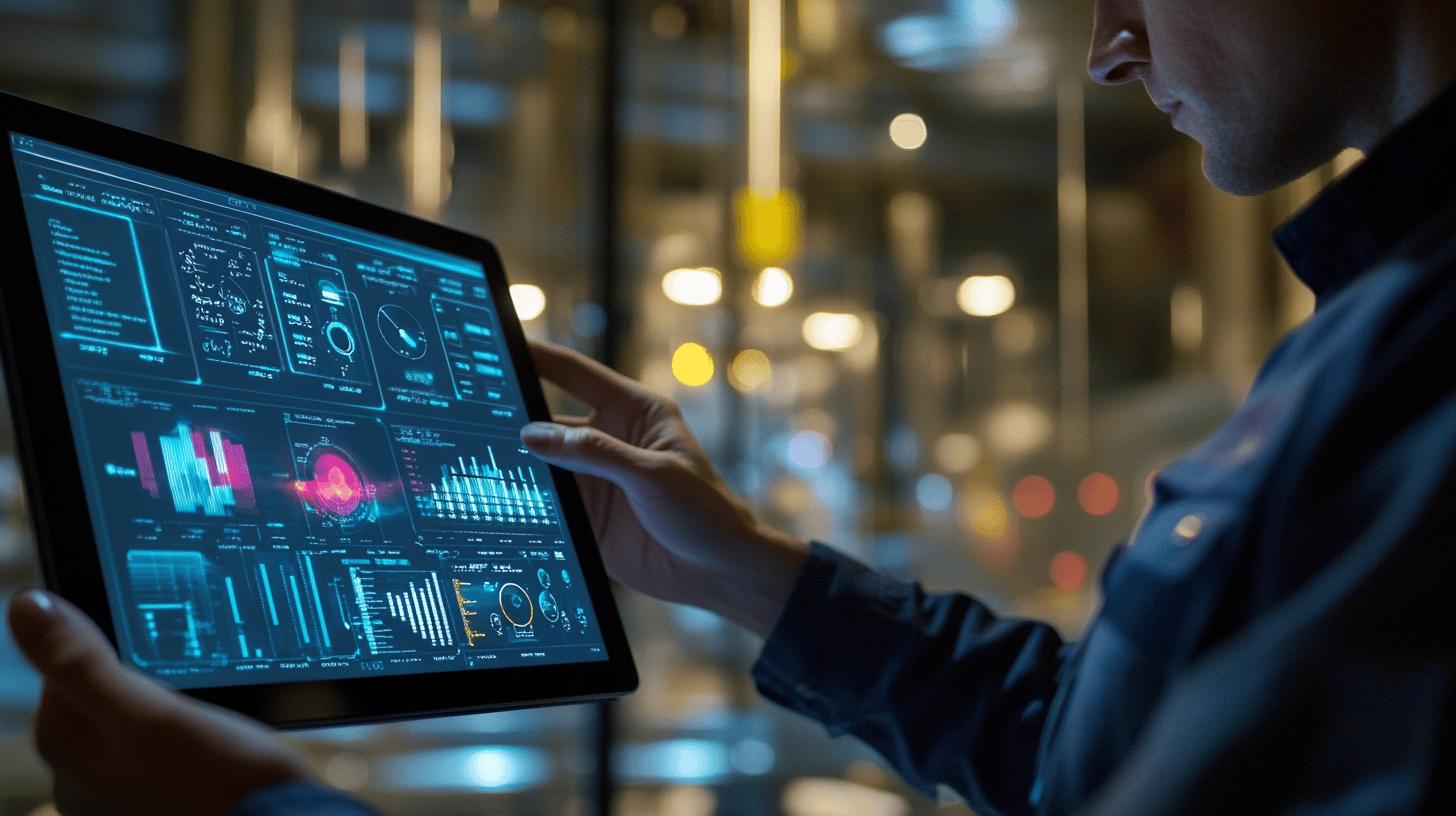
The heart of effective incident management lies in breaking down information barriers between departments. When engineering supply chains operate with fragmented systems, crucial safety data gets trapped in departmental silos, preventing timely responses and comprehensive analytics.
ERP integration eliminates these barriers by creating a single source of truth. When a component failure happens in production, the information doesn't just stay with the production team—it automatically updates inventory records, alerts procurement to potential supplier issues, and feeds into compliance reporting systems.
This connectivity isn't just convenient—it's transformative. Companies like Weston Aerospace discovered that breaking down these information silos led to significantly faster incident resolution and more proactive risk management.
Automating Compliance for Regulatory Peace of Mind
For engineering supply chains, regulatory compliance isn't optional—it's essential. Manual compliance processes are not only time-consuming but prone to errors that can result in penalties and reputational damage.
Integrated ERP systems automate compliance reporting by capturing required data points in real-time and formatting them according to regulatory standards like RIDDOR.
Integrating ERP integration food safety quality assurance into operational workflows further illustrates how technology can elevate safety across industries. This approach ensures that whether in food processing or engineering supply chains, quality assurance steps are enhanced, reflecting a clear connection between proactive risk management and regulatory compliance. This automation ensures nothing falls through the cracks, even as regulations evolve and become more complex.
The benefits extend beyond just meeting requirements. With automated compliance processes, engineering teams can spend less time on paperwork and more time on value-adding activities that improve safety and operational performance.
Consider these crucial capabilities that integrated systems provide:
- Real-time incident capture with automatic notification to relevant stakeholders
- Structured workflows that ensure consistent investigation and follow-up
- Automatic generation of compliance documentation for regulatory bodies
- Historical trending and analysis for proactive risk management
- Integration with training records to identify potential knowledge gaps
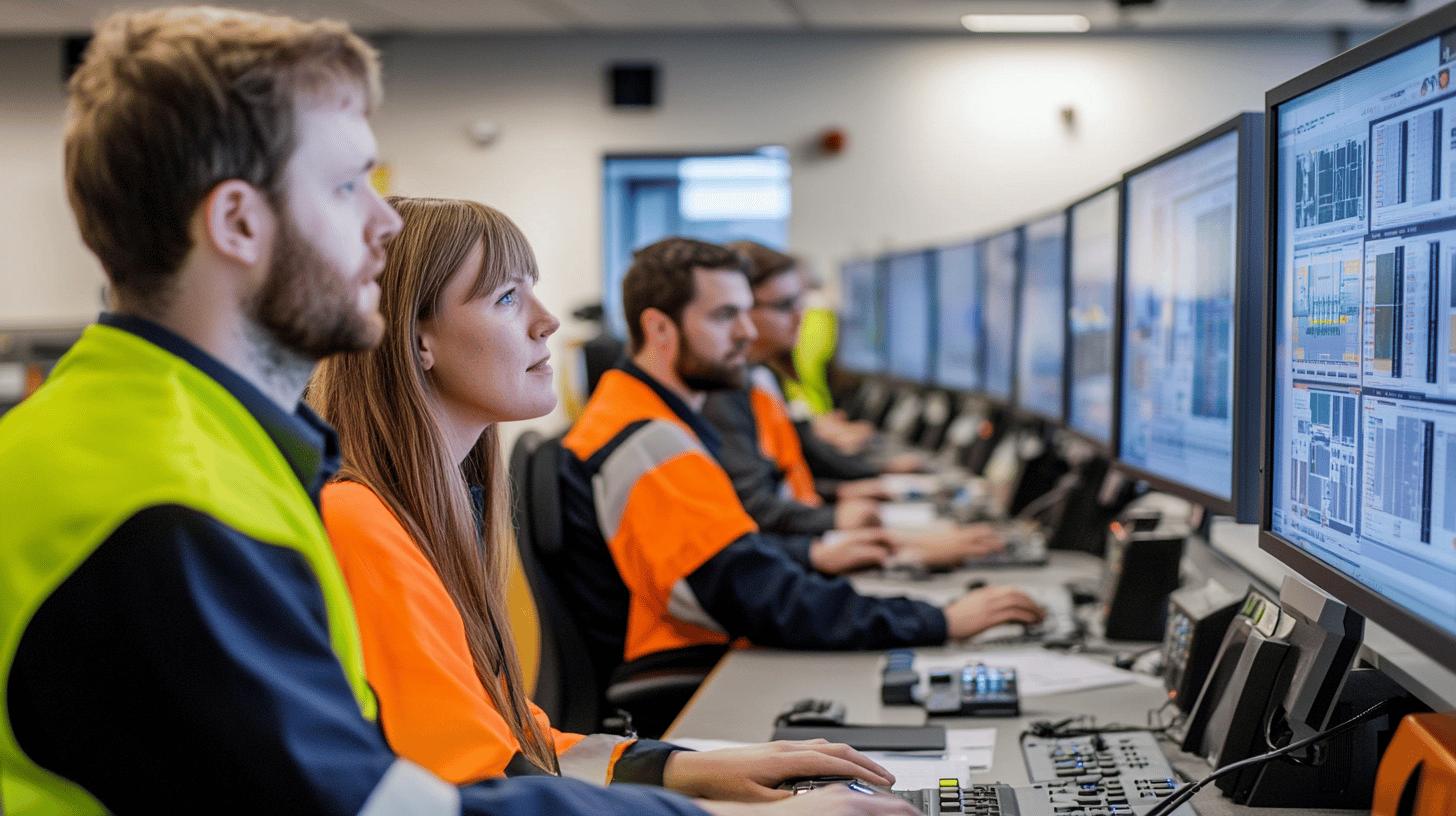
From Reactive to Proactive: The Power of Integrated Analytics
Perhaps the most significant advantage of ERP-integrated incident reporting is the shift from reactive to proactive safety management. Traditional systems wait for incidents to occur before taking action. Integrated systems use data to predict and prevent problems before they happen.
By analysing patterns across operations, these systems can identify recurring issues or emerging risks. For example, if certain equipment consistently generates near-miss reports, the system can flag this trend for investigation before a serious incident occurs.
Fowlers of Bristol experienced this transformation firsthand after implementing Q-Hub's integrated solution. Their "Zero Defects" initiative became measurably more effective when supported by real-time data and trend analysis from their integrated systems.
Real-World Impact: Transformation in Action
The practical benefits of ERP integration for incident reporting become clear when examining real-world implementations. Consider these examples from organisations that have embraced integrated approaches:
<table border="0"> <tr><th>Metric</th><th>Before Integration</th><th>After Integration</th></tr> <tr><td>Incident Response Time</td><td>Hours to Days</td><td>Minutes to Hours</td></tr> <tr><td>Compliance Reporting</td><td>Manual, Error-Prone</td><td>Automated, Accurate</td></tr> <tr><td>Cross-Department Visibility</td><td>Limited/Delayed</td><td>Real-Time/Comprehensive</td></tr> <tr><td>Risk Identification</td><td>Reactive</td><td>Proactive/Predictive</td></tr> </table>When BMC Analysis integrated their incident reporting processes, they transformed how they managed non-conformance reports (NCRs). What was once a disjointed process involving Word documents and email chains became a streamlined workflow with automated tracking and clear accountability. The result was faster resolution times and improved visibility across their entire organisation.
Best Practices for Successful Implementation
While the benefits of integration are compelling, successful implementation requires careful planning. Based on Q-Hub's experience helping companies like Anglia Cathodic Protection transform their operations, here are key best practices:
- Start with a clear assessment of your current systems and processes to identify integration points and potential challenges
- Involve all stakeholders early in the planning process to ensure the system meets everyone's needs
- Implement in phases rather than attempting a complete overhaul all at once
- Invest in thorough training to ensure all users understand and can effectively use the new system
- Monitor and optimize the system continuously based on user feedback and performance metrics
These practices helped Rocal Insulating Panels navigate their transition from paper-based processes to an integrated digital system. Their methodical approach minimized disruption while maximizing adoption across their organisation.
Overcoming Common Integration Challenges
Despite the clear benefits, integration projects often face obstacles. Recognizing these challenges in advance helps ensure successful implementation:
- Legacy system compatibility: Older systems may require custom connectors or middleware solutions
- Data migration complexities: Historical incident data needs careful cleaning and validation during transfer
- Resistance to change: Staff accustomed to existing processes may need extra support and training
- Process standardization: Different departments may need to align their incident handling approaches
The Scottish Leather Group overcame these challenges by working closely with Q-Hub's implementation team to develop tailored solutions for their unique needs. Their success demonstrates that with proper planning and support, these obstacles can be effectively addressed.
The Future: AI-Enhanced Incident Prevention
Looking ahead, the integration of ERP systems with incident reporting is evolving to incorporate artificial intelligence and machine learning. These technologies will further enhance the predictive capabilities of integrated systems, moving beyond pattern recognition to genuinely anticipatory risk management.
Future systems will likely feature:
- AI-driven risk assessment that identifies potential incidents before they occur
- Natural language processing to extract insights from unstructured incident reports
- Automated root cause analysis to identify systemic issues
- Augmented reality interfaces for on-site incident investigation and reporting
As these technologies mature, the gap between organisations using integrated systems and those relying on manual processes will widen further, making the business case for integration even more compelling.
Q-Hub continues to lead this evolution, developing solutions that help engineering supply chains not just manage incidents more effectively but prevent them altogether. By combining deep industry expertise with cutting-edge software capabilities, Q-Hub enables organisations to achieve new levels of safety, compliance, and operational excellence through streamlined, integrated incident reporting systems.