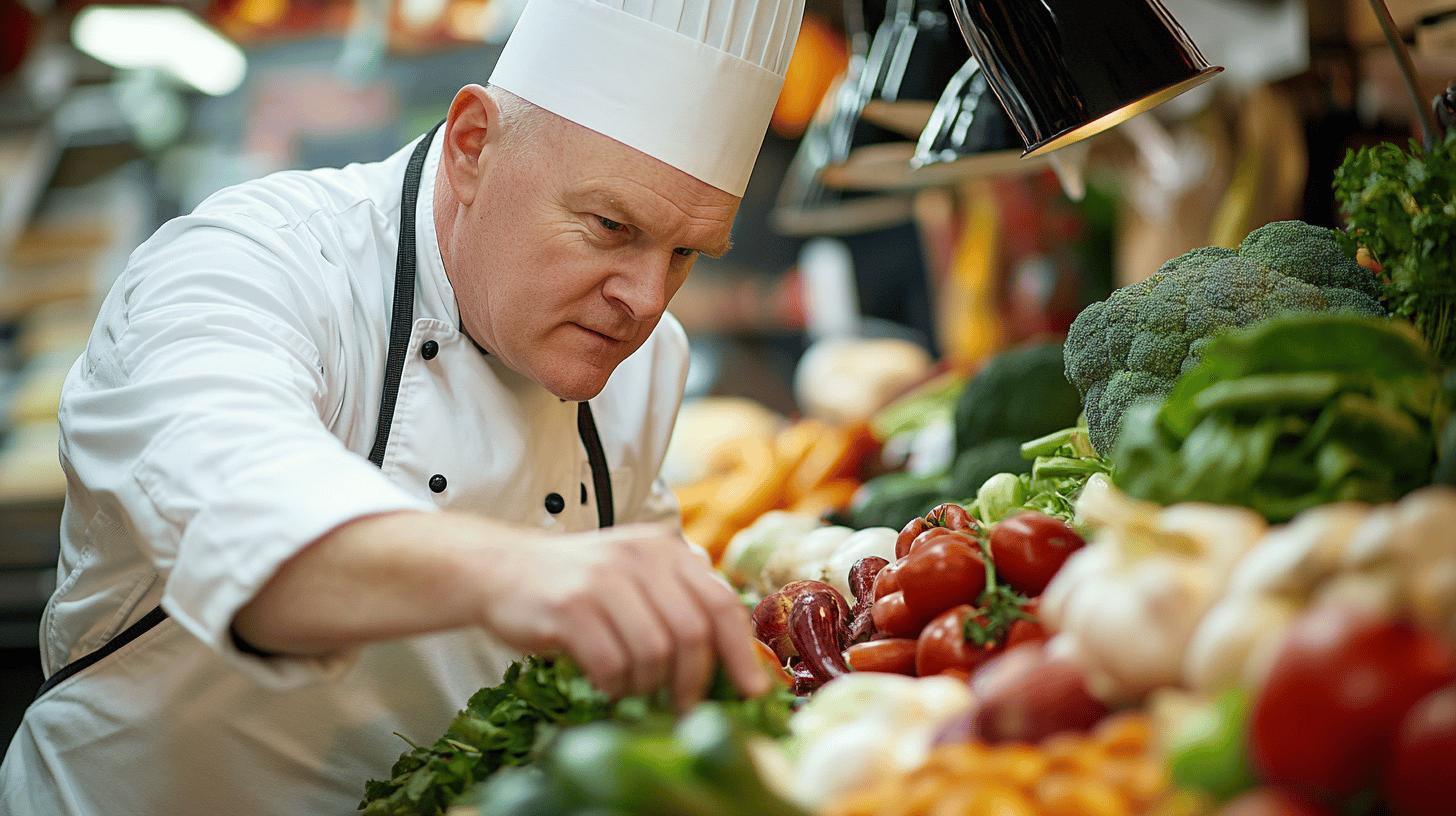
ERP Integration Elevates Food Safety and Quality Assurance
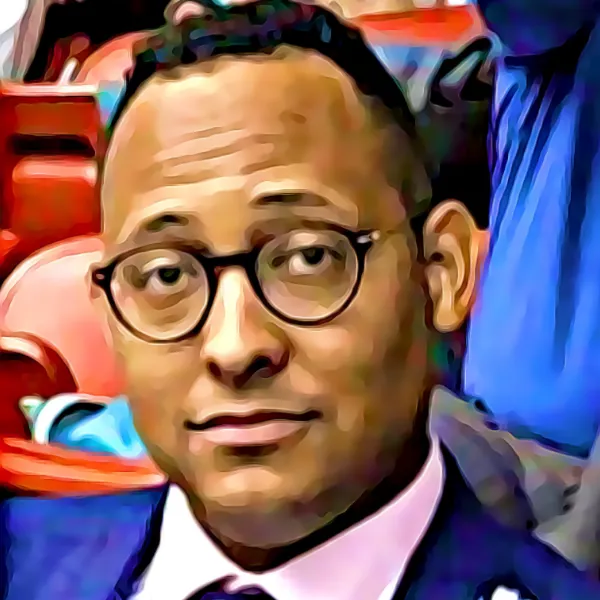
ERP Integration: Transforming Product Safety in Food Production
ERP integration advancing product safety and quality assurance measures in food production represents a fundamental shift in how manufacturers approach safety management. Q-Hub's expertise in digital transformation shows that unified software systems can replace fragmented methods that lead to errors and safety breaches. By centralising critical safety protocols, manufacturers gain unprecedented control over their production processes while meeting rigorous compliance standards.
ERP systems specifically designed for the food industry, such as erp integration in food industry, have redefined operational safety. Their specialized focus ensures that automation and integration are not only efficient but are tailored to address unique challenges in food production, reinforcing quality assurance from production to distribution.
When properly implemented, ERP systems reduce food safety incident response times by up to 80% while improving traceability accuracy to nearly 100%.
The impact of centralised safety management extends throughout the entire production chain. Consider a scenario where an ingredient recall occurs - with an integrated ERP system, you can instantly trace that ingredient's journey through your production process down to specific batches affected, allowing for precise, targeted recalls rather than costly blanket actions.
The Hidden Power of Real-Time Safety Monitoring
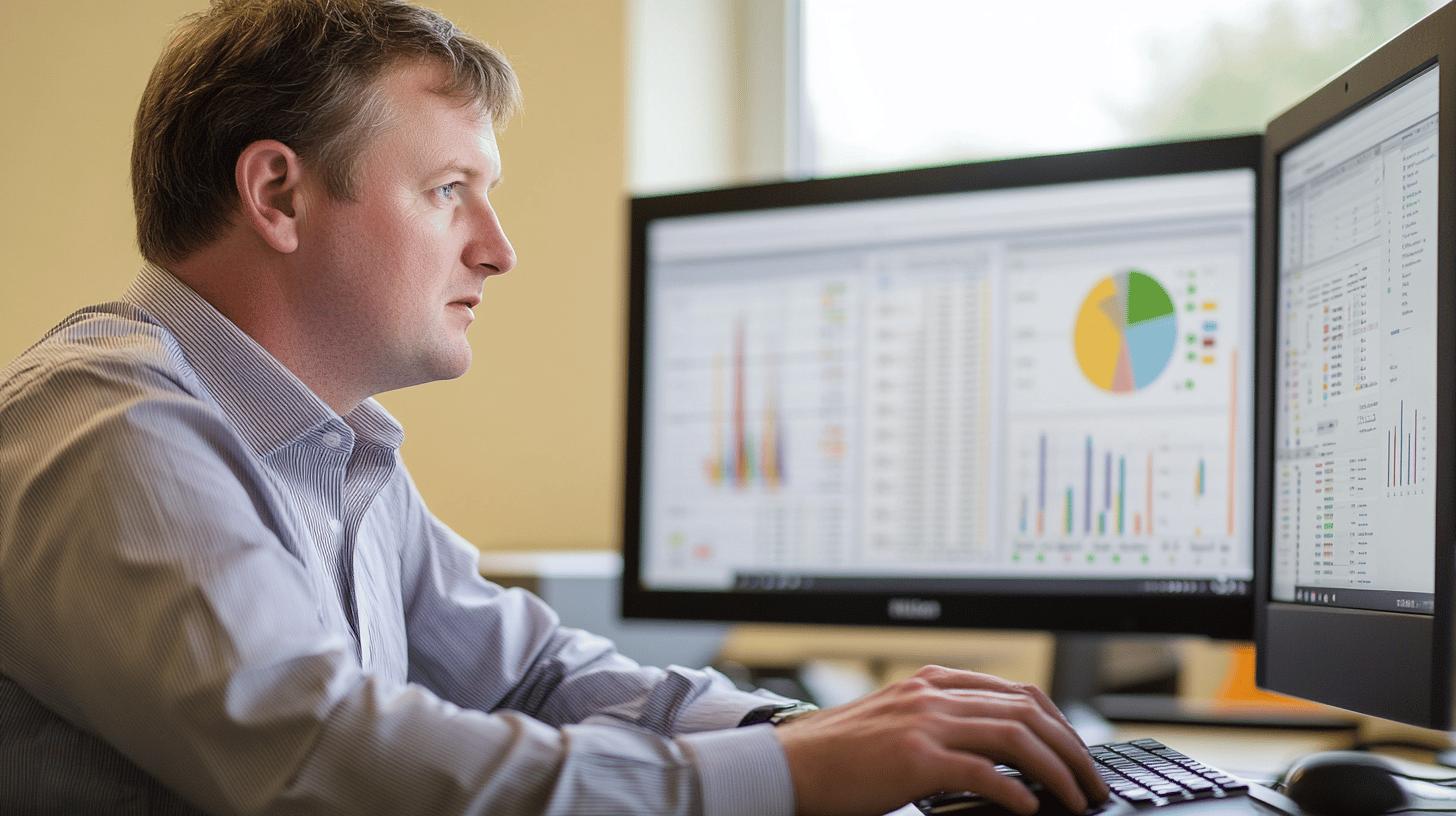
Traditional safety monitoring relies on manual checks and paperwork – approaches that Scottish Leather Group found increasingly inadequate as they expanded operations. After implementing Q-Hub's digital solutions, they transformed disconnected paper-based systems into automated workflows with real-time monitoring capabilities.
Modern ERP systems elevate food safety by automating tasks prone to human error.
In the realm of food manufacturing, implementing custom automation tools food manufacturing can be seen as a natural extension of digital transformation. These tools work hand-in-hand with ERP integrations to minimize errors and enhance precision, ensuring that every stage of production meets the highest standards of safety and quality control. Critical control point monitoring becomes continuous rather than periodic, with instant alerts for deviations from safety parameters. This proactive approach prevents small issues from becoming major safety incidents.
The benefits extend beyond immediate safety concerns. ERP systems deliver comprehensive data for analysis, helping identify recurring patterns and systemic vulnerabilities. This intelligence allows manufacturers to strengthen their safety protocols proactively rather than reactively.
<table border="0"> <tr><th>Safety Management Metric</th><th>Before ERP Integration</th><th>After ERP Integration</th></tr> <tr><td>Time to Trace Product</td><td>Hours to Days</td><td>Minutes</td></tr> <tr><td>Recall Scope Accuracy</td><td>Broad/Imprecise</td><td>Highly Targeted</td></tr> <tr><td>Compliance Documentation</td><td>Manual/Fragmented</td><td>Automated/Centralised</td></tr> </table>Creating a Culture of Continuous Quality Assurance
Beyond basic safety, ERP integration revolutionises how manufacturers approach overall quality control. Rather than relying on end-product inspections, integrated systems enable continuous quality monitoring throughout the production process - a transformation Rocal Insulating Panels experienced firsthand when they moved from paper-based quality documentation to Q-Hub's digital platform.
The real advantage comes from the data-driven approach that modern ERP systems enable. When a product's quality deviates from set benchmarks, the system immediately flags the issue, allowing for rapid intervention before problems cascade. This proactive approach has proven far more effective than traditional reactive methods.
Key functionalities supporting quality assurance include:
- Real-time alerts for quality standard deviations
- Automated documentation for transparent quality metrics
- Predictive analytics to identify potential issues
- Root cause analysis tools to address recurring problems

With these tools, food producers establish clear quality benchmarks, monitor compliance continuously, and adapt quickly to variations. For instance, as seen in Fowlers of Bristol's implementation of Q-Hub's solutions, automated quality reporting not only ensures audit-ready records but significantly reduces time spent on manual documentation – allowing quality teams to focus on improvement rather than paperwork.
Revolutionising Recall Management Through End-to-End Traceability
Perhaps the most critical advancement from ERP integration is the transformation of traceability systems. Before Q-Hub's implementation at BMC Analysis, tracing components through production was tedious and often incomplete. Now, with integrated lot tracking and electronic batch records, manufacturers can follow materials through the entire supply chain with unprecedented precision.
Consider this scenario: a frozen food manufacturer discovers potentially contaminated ingredients from a supplier. With robust ERP traceability, they can immediately identify which production runs used that specific lot, where finished products were shipped, and issue targeted recalls before products reach consumers – transforming what could have been a brand-damaging recall into a precise, efficient response.
This level of transparency extends beyond crisis management. Consumer demand for provenance information continues to rise, and ERP systems enable manufacturers to provide verified information about ingredient sources, production methods, and quality standards – building consumer trust in an increasingly competitive marketplace.
Streamlining Regulatory Compliance in a Complex Landscape
Food safety regulations grow increasingly complex each year, with manufacturers often navigating multiple standards simultaneously. ERP systems simplify this compliance maze by centralising management of all regulatory requirements in one platform.
For example, HACCP compliance requires rigorous monitoring of critical control points and detailed record-keeping. Modern ERP systems automate these processes, ensuring every CCP is monitored in real-time while generating audit-ready reports automatically – eliminating error-prone manual documentation.
The automation extends to adapting to regulatory changes. When standards evolve, as they frequently do, ERP systems can be updated centrally rather than requiring changes to multiple disconnected processes – ensuring continued compliance without operational disruption.
Beyond Safety: Unlocking Operational Efficiency
While safety and compliance drive many ERP implementations, the operational benefits are equally compelling. Anglia Cathodic Protection Services discovered this when implementing Q-Hub's digital platform – automating repetitive tasks freed staff to focus on higher-value activities while dramatically reducing errors.
One standout benefit is inventory optimisation. ERP systems provide real-time visibility into ingredient levels, usage rates, and shelf life, significantly reducing waste from overstocking or expired products. Similarly, production scheduling becomes more precise, with automatic adjustments based on changing variables like ingredient availability or equipment status.
The financial impact is substantial. Manufacturers using integrated ERP systems typically report:
- 15-25% reduction in inventory costs
- 10-20% decrease in production waste
- Significant reduction in labour costs for manual data entry and compliance management
Navigating Implementation Challenges: Lessons from Success Stories
While the benefits are clear, implementing ERP systems in food production environments presents challenges. Data migration often proves daunting – transferring legacy information into centralised systems requires meticulous planning to ensure accuracy and completeness.
System interoperability presents another hurdle. Many manufacturers use specialised software for different functions, and ensuring these systems communicate effectively with new ERP platforms requires careful integration planning.
Scottish Leather Group's successful implementation of Q-Hub's platform offers valuable lessons for overcoming these challenges:
- Begin with a phased rollout, starting with high-priority modules
- Provide comprehensive, role-specific training to build staff confidence
- Clean and validate data before migration to prevent carrying forward inaccuracies
- Work closely with ERP vendors to customise solutions for your specific processes
Stakeholder engagement emerged as the critical success factor across all case studies. When teams understand the benefits and participate in implementation planning, resistance decreases dramatically and adoption accelerates.
The Future: Smart Manufacturing Through Advanced Integration
Looking ahead, Q-Hub's digital solutions are paving the way for even more sophisticated integration between food safety systems and production environments. The next generation of ERP systems leverages IoT technology – connecting equipment, sensors, and production lines to deliver unprecedented visibility and control.
Imagine automated temperature sensors that not only record critical control point data but automatically adjust equipment settings to maintain optimal conditions. Or vision systems that inspect products in real-time, instantly flagging quality deviations and documenting compliance.
Artificial intelligence represents another frontier, with ERP systems increasingly employing AI to analyse production data, identify patterns, and recommend optimisations. These systems move beyond reactive monitoring to predictive intelligence – anticipating potential issues before they occur.
By embracing these integrated approaches to food safety management, manufacturers don't just comply with standards – they establish new benchmarks for operational excellence. Q-Hub's expertise in tailored software solutions positions food producers to navigate this digital transformation successfully, ensuring both product safety and operational efficiency in an increasingly complex regulatory landscape.
<