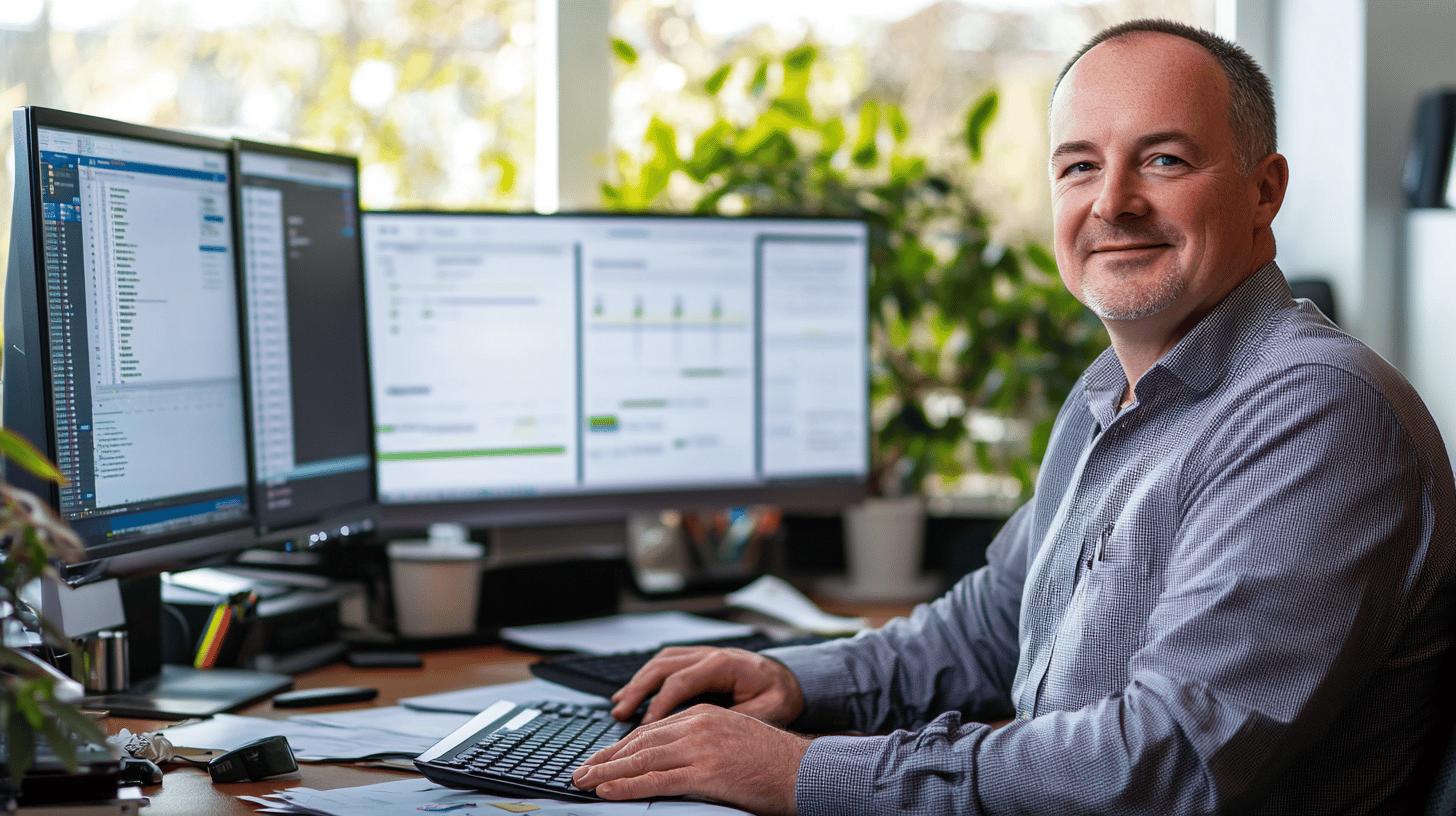
Integration with ERP Systems Enhances Engineering Workflows
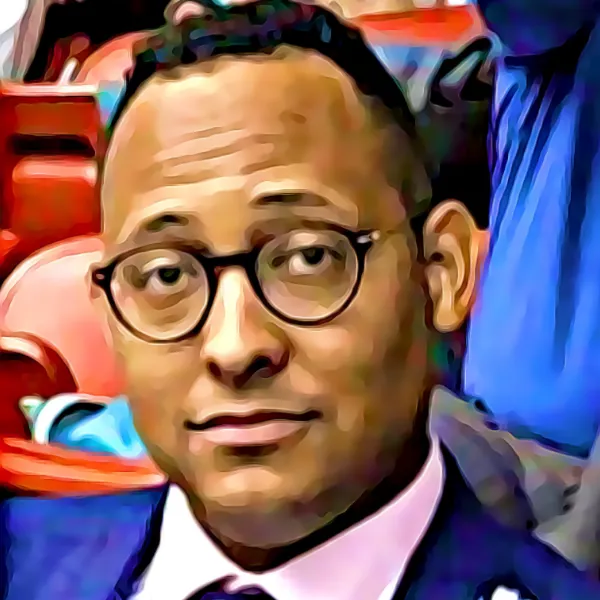
How ERP System Integration Streamlines Engineering Management Workflows in Facilities Supply Chains
Integrating ERP systems into engineering management workflows transforms how facilities supply chains operate. This digital convergence eliminates silos and connects previously fragmented processes into a cohesive whole. Q-Hub's expertise in digital transformation enables organisations to leverage these powerful tools, creating a central nervous system for operational management that delivers measurable improvements in efficiency and collaboration.
ERP systems bring diverse elements together—finance, inventory, human resources, and supplier management—into a unified platform where real-time data flows freely between departments. This connectivity means engineering teams can instantly access critical information like inventory levels or budget constraints when scheduling maintenance, preventing delays from outdated information and resolving potential issues before they escalate.
When engineering and supply chain systems are properly integrated, companies typically see 25-30% improvements in project delivery timeframes and significant reductions in operational costs.
Consider resource planning before ERP integration: static spreadsheets and disconnected tools created constant misalignment between project requirements and supply chain capabilities. With integrated systems, resource planning becomes dynamic and precise. Teams track availability, forecast demand, and allocate materials while maintaining compliance with schedules and budgets—drastically reducing waste and improving overall efficiency.
Transforming Project Management Through Connected Workflows
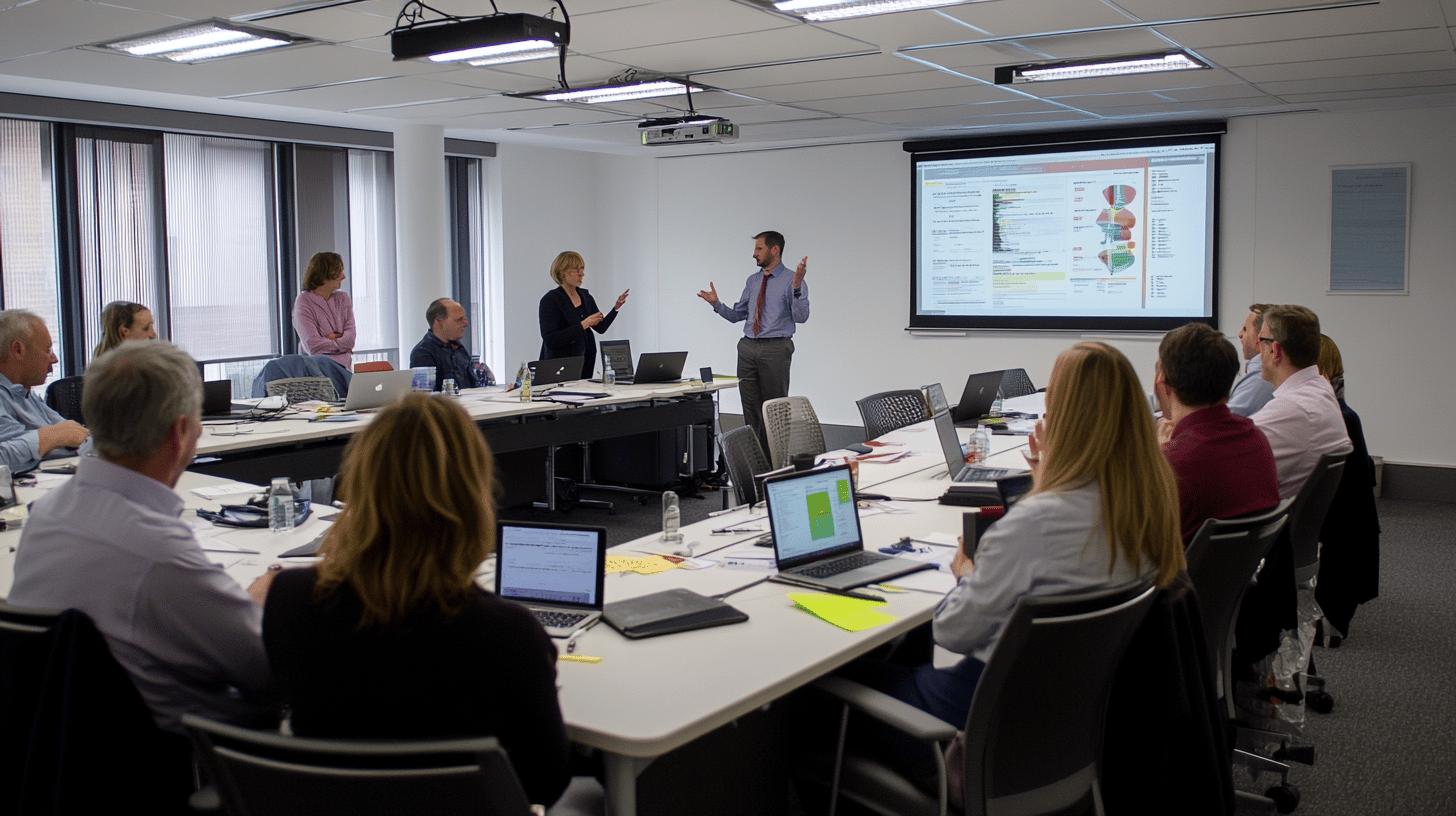
Large-scale facility upgrades illustrate the power of integrated systems. Without ERP connectivity, tracking progress, costs, and resource usage becomes chaotic. A properly implemented system enables all stakeholders—from engineers to procurement managers—to monitor milestones, make real-time adjustments, and collaboratively resolve issues as they arise.
This transparency does more than keep projects on track; it creates accountability across departments and transforms engineering management into a strategic operation where communication flows freely and data-driven decisions become the norm.
Key Features of ERP Systems That Enhance Engineering and Supply Chain Coordination
When refining engineering workflows in facilities supply chains, certain ERP capabilities stand out for their transformative impact. Q-Hub's solutions leverage these features to create seamless operations where previously disconnected processes now work in harmony, eliminating the manual errors and fragmented communication that plague traditional systems.
Real-Time Data Access: The Backbone of Efficient Engineering Operations
Inventory management becomes remarkably more precise with ERP integration. Engineering project success often hinges on having the right parts at the right time—something Q-Hub's solutions excel at facilitating. Real-time inventory tracking enables automatic reorder points and prevents the costly delays caused by stock shortages that derail project timelines.
Predictive analytics transforms supply chain operations from reactive to proactive. By analysing historical data patterns, ERP systems can forecast future requirements with remarkable accuracy. This capability is particularly valuable for preventing both overstocking (which ties up capital) and understocking (which causes operational delays)—common problems that Q-Hub's clients have successfully overcome.
Supplier relationship management gains new dimensions through centralised communication platforms. Instead of juggling spreadsheets and email chains, teams access a single interface for tracking orders, managing contracts, and resolving issues quickly. This streamlining of vendor relationships has proven particularly valuable for facilities with complex supply chains.
The following capabilities make the most significant difference in engineering and supply chain operations:
- Automated workflow management that eliminates repetitive tasks and human error
- Real-time inventory control systems that prevent shortages and excess stock
- Predictive demand forecasting for precise resource planning
- Centralised vendor management to optimise supplier performance
- Integrated data analytics that support informed decision-making
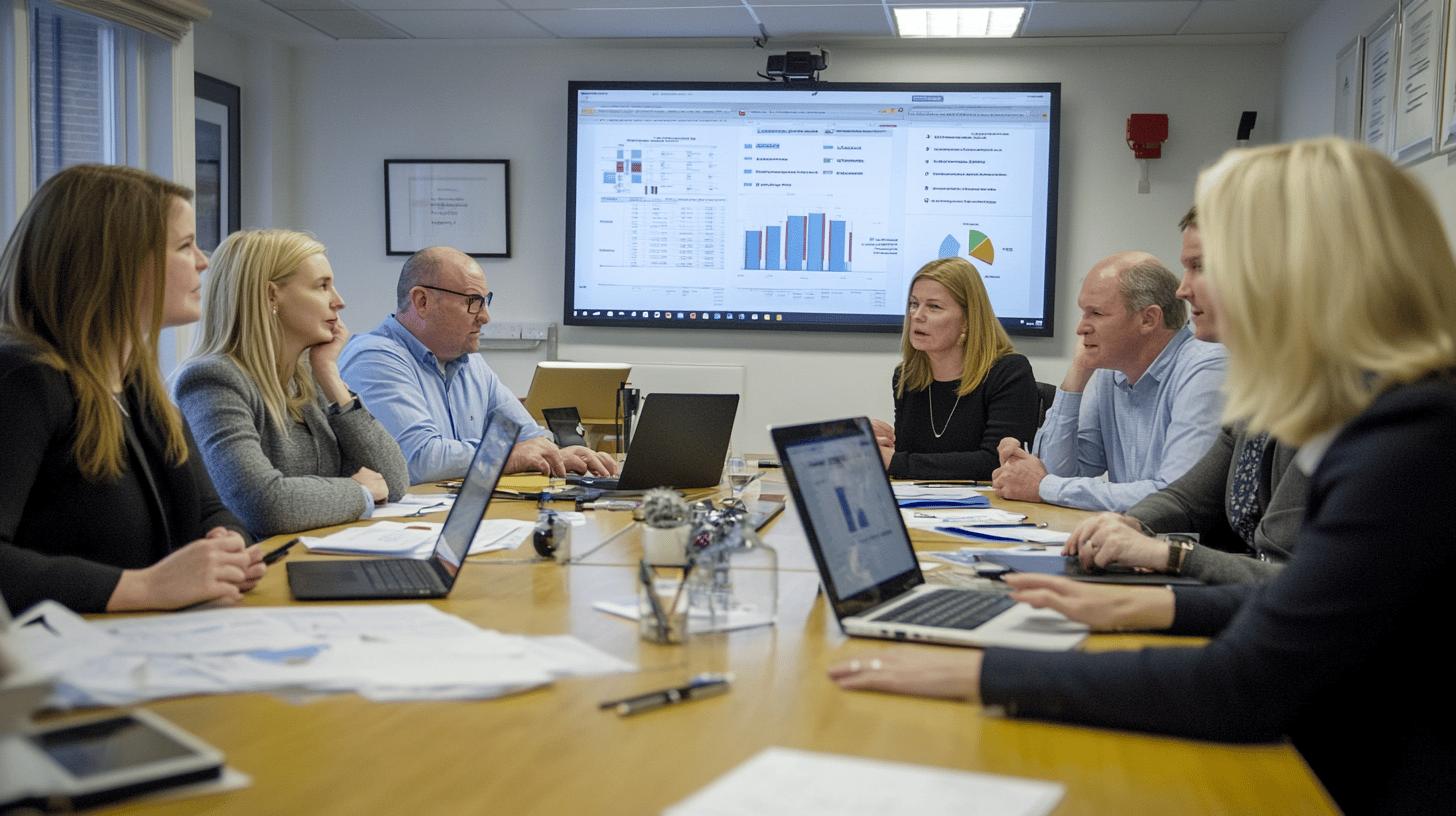
By implementing these features through platforms like Q-Hub, engineering teams transform fragmented processes into cohesive operations where data flows freely and decision-making becomes more strategic and proactive.
Overcoming Common Challenges in ERP Integration for Facilities Supply Chains
While integration with ERP systems offers tremendous benefits for engineering management workflows, the implementation journey isn't without obstacles. Companies that successfully navigate these challenges, especially with guidance from specialists like Q-Hub, achieve transformative results that justify the initial effort.
Breaking Through Legacy System Barriers
System interoperability represents the most common technical hurdle when implementing ERP solutions. Many facilities rely on older systems that weren't designed to communicate with modern platforms. This incompatibility creates fragmented workflows—exactly what ERP integration aims to eliminate.
The solution isn't immediate replacement but strategic connection. Q-Hub's approach typically involves identifying critical systems for initial integration and deploying custom APIs or middleware to bridge compatibility gaps. This creates functional connections without disrupting essential operations or requiring complete system overhauls.
Controlled testing environments allow teams to verify these integrations before full deployment, significantly reducing implementation risks and ensuring smooth transitions between legacy and new systems.
Managing the Human Element of Digital Transformation
Technology implementation is only half the battle—change management often determines success or failure. Resistance to new systems is natural, especially when they disrupt familiar workflows that teams have relied on for years.
Comprehensive training and clear communication form the foundation of effective adoption. When staff understand how ERP systems simplify their daily responsibilities and improve outcomes, resistance naturally diminishes. Early stakeholder engagement builds momentum and creates champions who help drive the implementation forward.
Here's how organisations typically address the most common ERP integration challenges:
Challenge | Impact | Solution |
---|---|---|
System Interoperability | Data silos and workflow fragmentation | Custom middleware and phased connection strategy |
Legacy System Integration | Compatibility issues with modern platforms | Targeted APIs and incremental upgrades |
Change Management | Staff resistance and low adoption rates | Comprehensive training and clear benefits communication |
Implementation Planning | Project delays and budget overruns | Detailed roadmaps with defined milestones |
Data Migration | Information loss or corruption | Systematic testing and robust backup protocols |
The most successful implementations don't try to solve everything at once. Instead, they follow a carefully orchestrated sequence that builds confidence and delivers incremental wins while working toward comprehensive integration.
Case Studies: Successful ERP Integration in Engineering and Supply Chains
Real-world examples demonstrate how integration with ERP systems transforms engineering management workflows in facilities supply chains. The following cases highlight the tangible benefits organisations achieve when implementing comprehensive solutions like those offered by Q-Hub.
From Fragmented to Unified: Scottish Leather Group's Digital Transformation
Scottish Leather Group faced significant challenges managing compliance and operations across multiple sites with paper-based systems. Their quality, health and safety, and operational processes struggled to keep pace with growth and regulatory requirements across various ISO standards.
After implementing Q-Hub's modular platform, they achieved remarkable improvements. The Audit Hub simplified management of multiple ISO standards, while the Asset Hub streamlined equipment calibration and maintenance workflows. Document control processes that previously caused delays became efficient with digital approvals and automated review reminders.
The results were transformative: "Audit hub has significantly reduced audit preparation time, freeing resources for value-added activities," reported a senior manager. Communication between departments and sites improved dramatically, with shop floor employees gaining direct access to reporting tools and compliance information.
Streamlining Operations: Anglia Cathodic Protection's Efficiency Gains
Anglia Cathodic Protection Services Limited experienced rapid growth that stretched their paper and spreadsheet-based systems beyond capacity. Their fragmented processes hindered effective management of compliance across multiple sites, creating inefficiencies across quality management, operations, and health and safety departments.
Q-Hub's implementation digitised these disconnected processes, making compliance management accessible and actionable for all employees. The Process Hub provided centralised non-conformance tracking, linking issues to audits and ensuring clear accountability throughout resolution workflows.
The platform's ability to share necessary documents and track "read and understood" acknowledgments transformed workforce engagement. Both shop floor employees and remote workers gained access to the tools and information needed to perform effectively, fostering stronger accountability across the organisation.
These cases demonstrate how properly implemented ERP systems create measurable improvements in operational efficiency, compliance management, and cross-departmental collaboration.
The Role of Workflow Customisation in ERP Systems for Engineering Management
Standard "off-the-shelf" ERP implementations often fail to deliver their full potential in engineering environments. Q-Hub's approach emphasizes that workflow customisation is crucial for refining engineering management processes in facilities supply chains. This adaptability enables organisations to address specific operational challenges while significantly improving efficiency.
Tailoring Systems to Match Unique Operational Needs
Without customisation, ERP workflows frequently remain rigid and misaligned with engineering teams' unique requirements. When tailored properly, these systems not only streamline processes but optimise them for long-term success—a key differentiator in Q-Hub's implementation methodology.
Customisation allows businesses to align ERP functions with organisational objectives. For example, engineering managers often struggle with regulatory compliance tracking. By tailoring workflows to integrate ISO 9001 or ISO 45001 checkpoints, teams ensure standards adherence without adding administrative burdens.
Similarly, project-specific workflows can be designed for large-scale facility upgrades, providing precise resource allocation and timeline tracking that adapts to changing conditions. This flexibility proved critical for Weston Aerospace, where customised audit workflows significantly reduced compliance management time.
Consider these high-impact workflow customisations for engineering environments:
- Compliance tracking workflows tailored to specific industry certifications
- Dynamic project management workflows with automated milestone notifications
- Real-time inventory modules customised for multi-project resource allocation
- Risk assessment processes with built-in mitigation tracking
- Predictive maintenance scheduling based on equipment-specific parameters
The right customisations ensure that ERP systems work for your specific processes—not the other way around. This approach helps organisations like Fowlers of Bristol, who implemented Q-Hub solutions to drive their "Zero Defects" quality initiative through customised dashboards tracking "Right First Time" performance metrics.
Best Practices for Seamless ERP Implementation in Facilities Supply Chains
Successful ERP integration requires more than technology—it demands a methodical approach to change management. Q-Hub's implementation expertise has identified several critical success factors that significantly increase adoption rates and operational improvements when integrating enterprise systems with engineering workflows.
Building Strong Foundations Through Inclusive Planning
The most successful implementations begin with comprehensive stakeholder engagement. This means involving everyone who will interact with the system, from engineers and procurement managers to maintenance staff and IT personnel. These individuals bring invaluable insights into existing workflows and potential friction points that might otherwise go unnoticed.
Start by forming a cross-functional project team with clear roles for representatives from engineering, supply chain, finance, and IT departments. Establish regular communication channels where updates are shared, concerns addressed, and all voices heard throughout the implementation process.
When BMC Analysis implemented Q-Hub's system to address their NCR management challenges, this inclusive approach ensured that the solution addressed the real needs of quality teams rather than imposing predetermined workflows that wouldn't fit their operation.
Reducing Risk Through Graduated Implementation
Full-scale ERP deployment often leads to overwhelming change and potential disruption. A phased approach significantly reduces these risks while building confidence in the new system. Begin with a pilot deployment in a single department or facility where impacts can be carefully monitored and adjustments made.