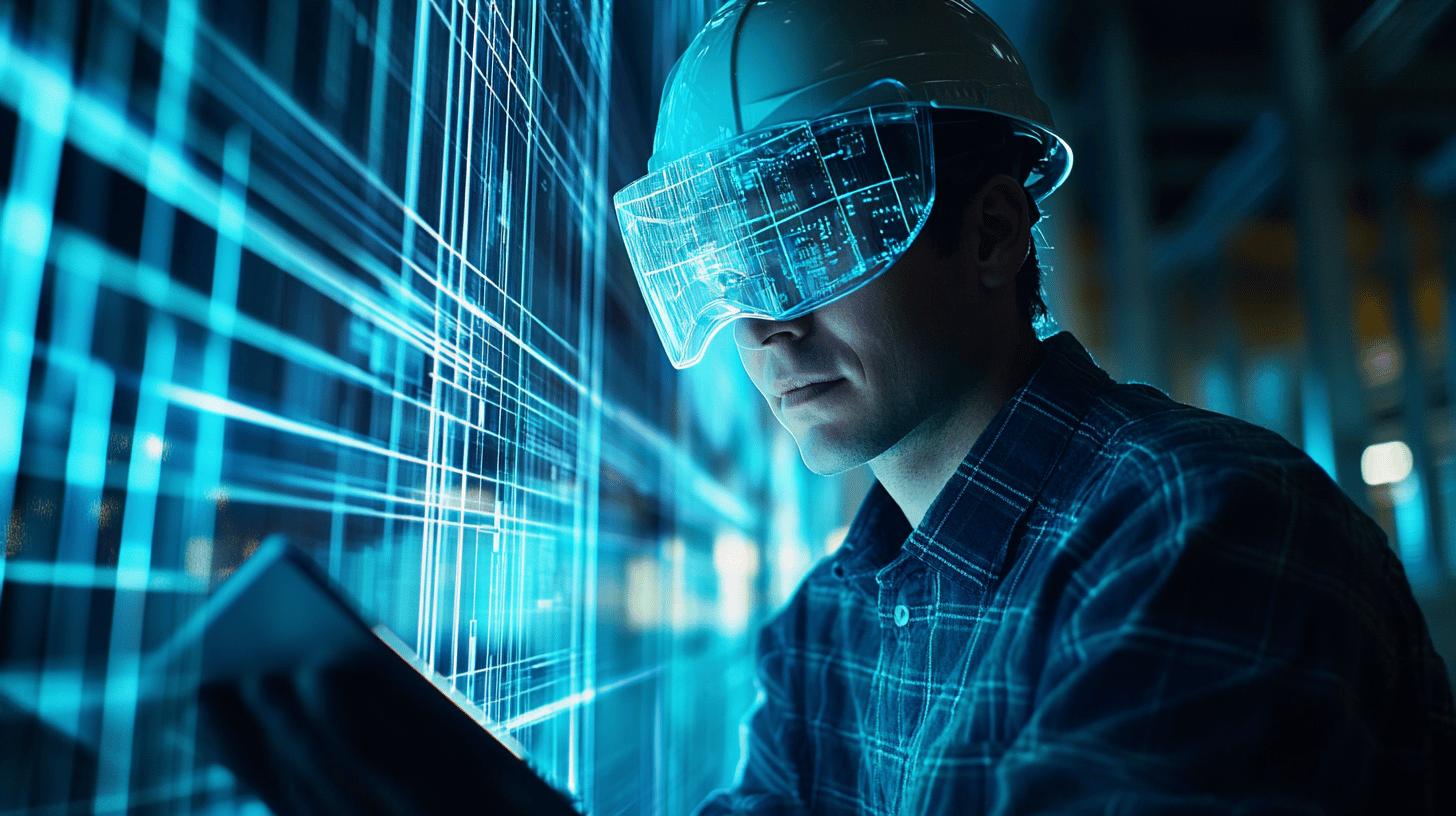
Integration with ERP Systems Boosts Engineering Safety
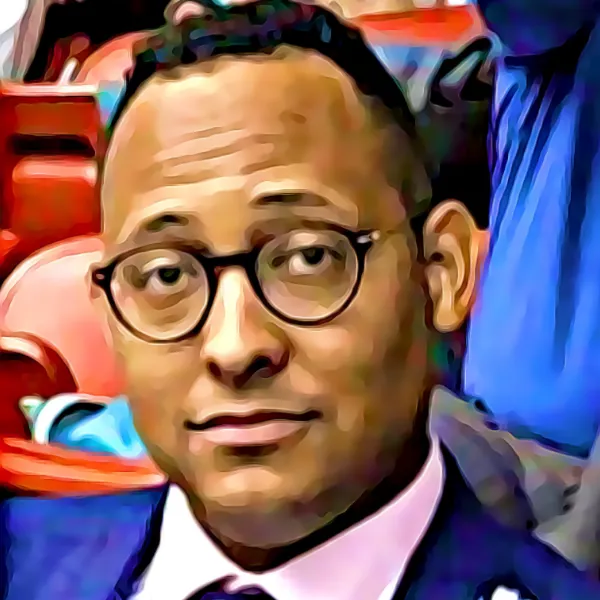
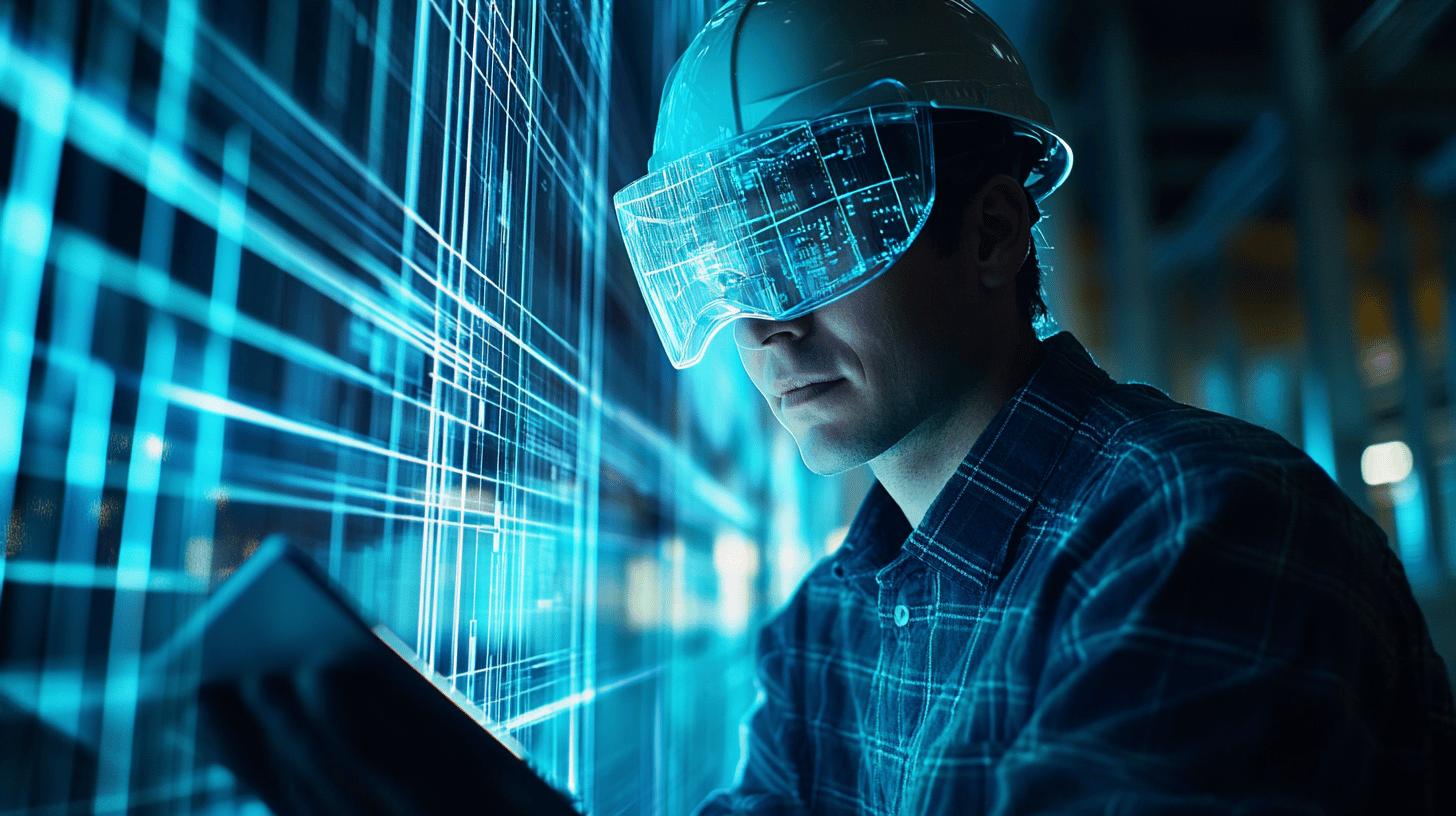
Integration with ERP Systems Boosts Engineering Safety
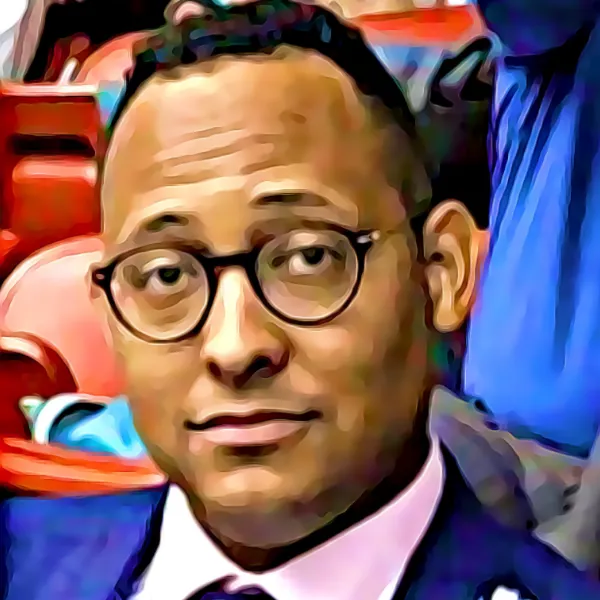
The Role of ERP Integration in Refining Safety Management Workflows for Engineering Supply Chains
Integrating ERP systems into safety management workflows has revolutionised how engineering supply chains operate, offering a seamless blend of automation, compliance, and efficiency. By embedding these tools, organisations transform safety management from an afterthought into an inherent part of operations. Q-Hub's approach to digital transformation helps bridge data silos, enhance visibility, and enable better risk assessment—creating a streamlined, proactive approach to hazard prevention that safeguards both employees and operations.
With centralised data and automated processes, engineering firms can demonstrate regulatory adherence with minimal effort. This ensures continuous compliance readiness while significantly reducing the time and resources traditionally spent on safety administration.
When we implemented Q-Hub's QHSE software at Weston Aerospace, we saw dramatic improvements in efficiency and compliance management. Processes that once consumed hours each week became seamless with the Audit Hub.
Companies embracing ERP integration for safety management typically experience:
- Centralised data enabling real-time safety decision-making
- Enhanced traceability and automated compliance monitoring
- Streamlined safety checks with minimal manual intervention
- Improved cross-departmental collaboration on safety initiatives
- Predictive analytics capabilities that identify risks before incidents occur
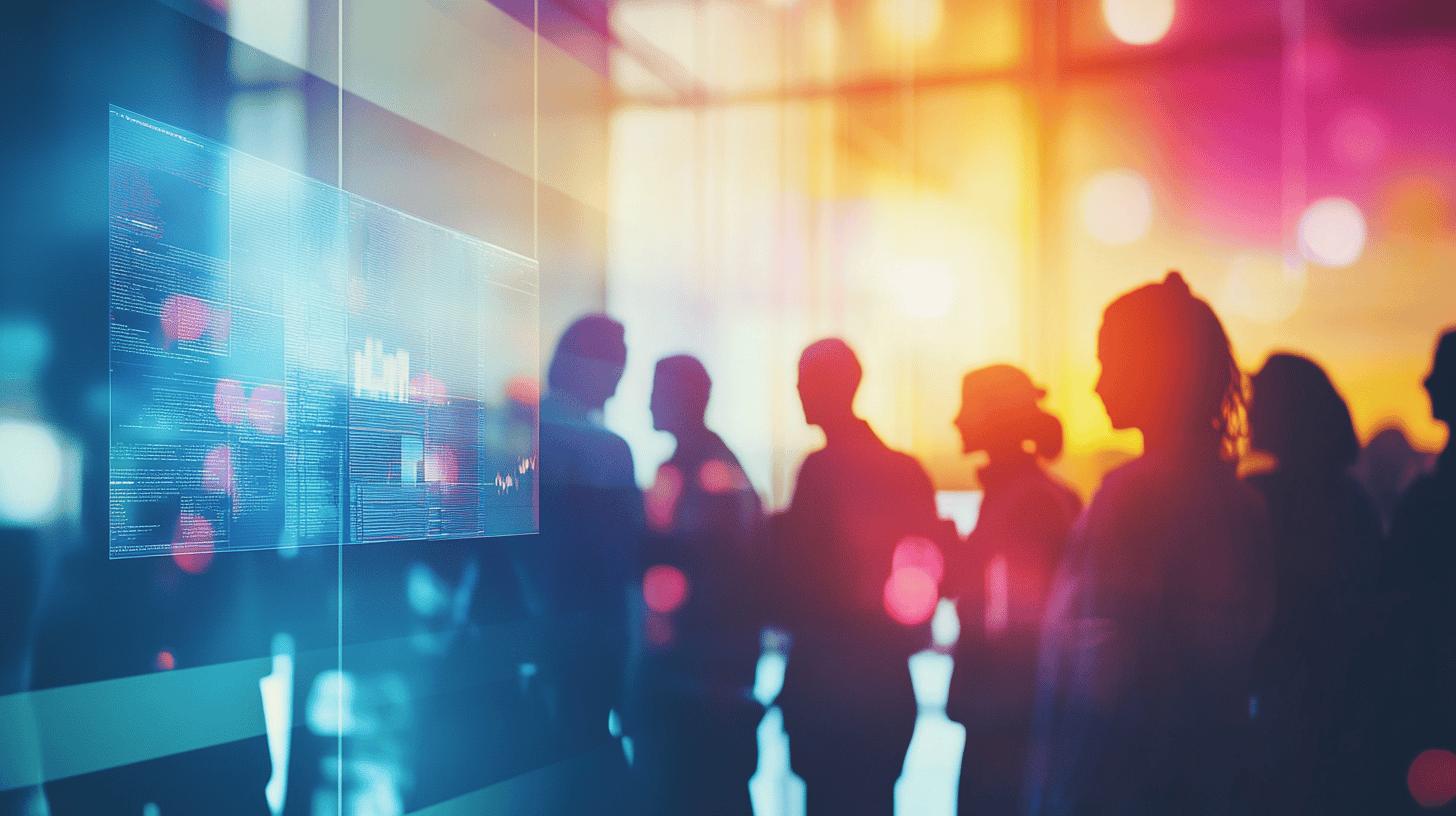
Transforming Manual Processes into Digital Safety Ecosystems
When it comes to engineering supply chains, the integration of ERP systems creates a digital safety ecosystem that eliminates the bottlenecks of manual workflows. Before implementing Q-Hub's solutions, Anglia Cathodic Protection relied on fragmented paper and spreadsheet-based systems that hindered their ability to effectively manage compliance across multiple sites.
By unifying these processes through ERP integration custom development projects have been instrumental in tailoring safety solutions to meet the distinct needs of each engineering environment. In many cases, bespoke projects enable organisations to bridge the gap between generic ERP capabilities and the specific requirements of safety protocols, demonstrating how adaptable and innovative digital solutions can transform traditional safety practices into agile, future-proof systems., organisations eliminate redundancies and create a seamless flow of safety information. This transformation aligns daily operations with broader compliance goals while creating a foundation for continuous improvement.
The benefits extend beyond basic efficiency. Resource allocation becomes more precise, cutting costs while ensuring safety-critical tasks are prioritised. In the end, it's about creating a safety-first culture that supports operational excellence.
Safety Management Process | Before ERP Integration | After ERP Integration |
---|---|---|
Audit Preparation | Days of manual compilation | Hours with automated reporting |
Incident Response | Delayed by paperwork | Immediate with digital workflows |
Compliance Monitoring | Periodic manual checks | Continuous automated oversight |
Risk Identification | Reactive after incidents | Proactive with predictive analytics |
Unlocking Real-Time Safety Intelligence with Advanced Monitoring
Real-time monitoring has become a cornerstone of effective safety management in engineering supply chains. Using advanced sensors and data collection tools, ERP platforms provide live updates on safety performance metrics that transform how organisations respond to potential hazards.
Scottish Leather Group experienced this transformation firsthand when they implemented Q-Hub's Audit Hub. The system enabled efficient management of audits and compliance across multiple ISO standards, including ISO 9001 for quality management and ISO 45001 for health and safety.
For engineering firms with complex supply chains, having real-time insights can make the difference between a minor issue and a major disruption. The ability to track hazardous conditions as they develop allows for immediate intervention before situations escalate.
Future-Proofing Safety with Predictive Analytics
The most sophisticated ERP systems now incorporate predictive analytics that go beyond monitoring to actually anticipate potential safety risks. Using historical data and advanced algorithms, these systems identify patterns that might indicate future hazards before they materialise.
For instance, if a specific machine component shows a repeated failure pattern, the system can automatically flag it for maintenance before it causes an incident. This capability not only enhances safety but also minimises costly downtime that can disrupt supply chain operations.
Q-Hub's implementation at Fowlers of Bristol demonstrates how predictive capabilities can drive a "Zero Defects" approach by providing tools to measure and manage quality effectively. Dashboards track KPIs while linking actions to forms and registers streamlines the identification and resolution of issues.
Best Practices for Implementing ERP Systems in Safety Management Workflows
Strategic planning forms the backbone of successful ERP integration for safety management. Q-Hub's experience working with engineering firms has shown that without deliberate planning, integration can disrupt workflows and create inefficiencies rather than solving them. The key lies in aligning digital frameworks with existing safety protocols to create a synergistic relationship between technology and safety culture.
Understanding Your Unique Safety Landscape
Before diving into ERP implementation, conducting a thorough safety ecosystem assessment is essential. This critical step identifies potential hazards, compliance gaps, and operational vulnerabilities that need to be addressed in your digital transformation strategy.
For example, when BMC Analysis partnered with Q-Hub, they identified that tracking Non-Conformance Reports (NCRs) through Word documents and fragmented email communication was a major pain point. This insight allowed them to focus on implementing Q-Hub's Process Hub specifically to revolutionise this workflow.
With these insights, ERP systems can be configured to incorporate automated maintenance schedules and real-time alerts that address your specific challenges. This proactive approach ensures that safety risks are addressed at their root, significantly improving workflow reliability.
Designing User-Centric Safety Workflows
Generic ERP solutions rarely deliver optimal results in specialised engineering environments. Customisation is key to success. Tailoring ERP modules to match the specific safety needs of your engineering processes ensures the software supports rather than hinders daily operations.
Rocal Insulating Panels experienced this benefit when they transformed their paper-based accident reporting system with Q-Hub's automated workflows. The customised solution enabled quicker resolution and better involvement of department managers, making reporting faster and more detailed.
By focusing on user experience and workflow design, organisations can enhance their ability to meet both safety and regulatory demands seamlessly while encouraging widespread adoption.
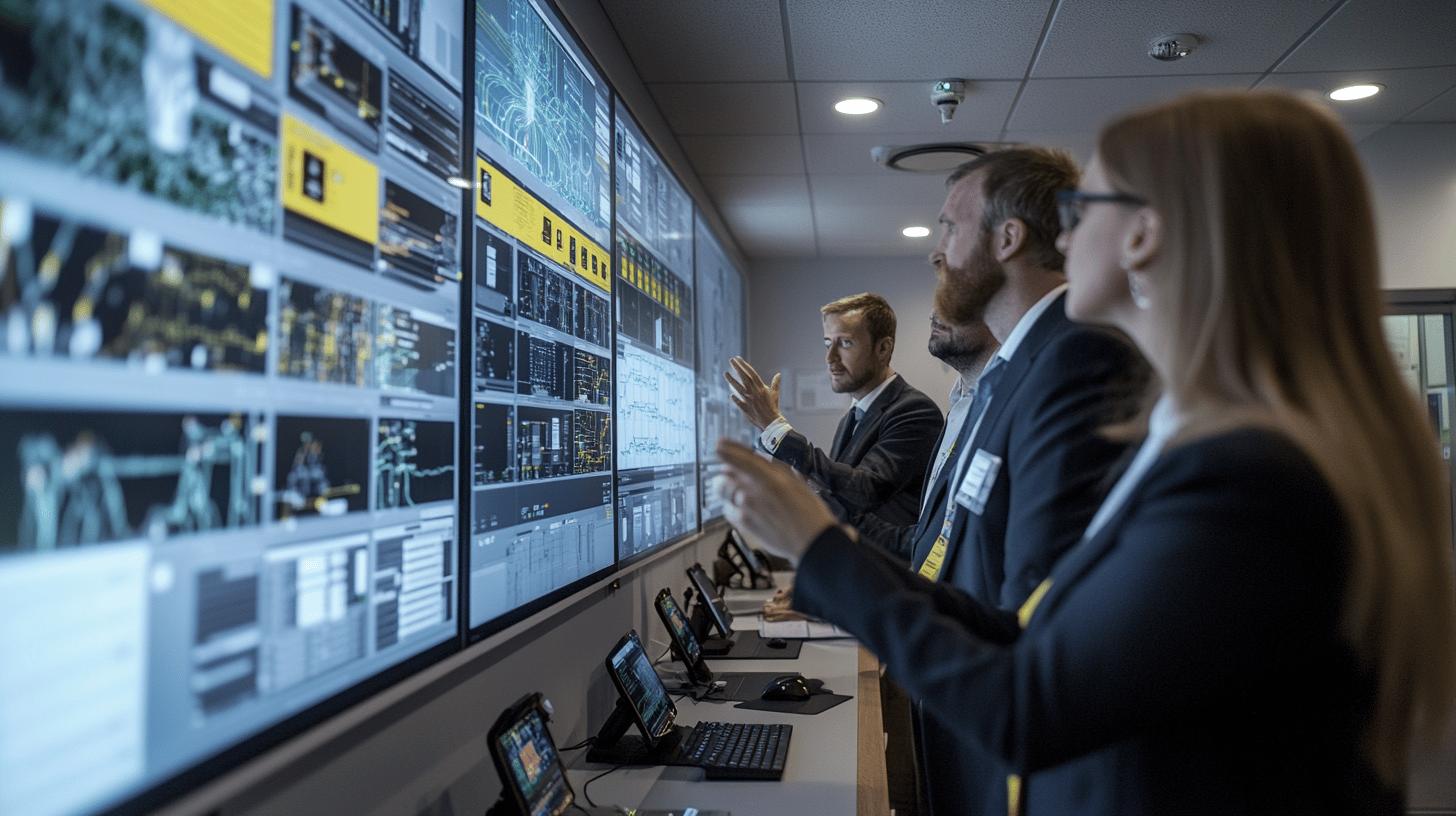
Overcoming ERP Integration Challenges in Engineering Safety Workflows
Integrating ERP systems to refine safety management workflows is transformative yet complex. The process often faces several hurdles that can hinder the creation of truly integrated safety systems. For engineering supply chains, addressing these challenges proactively is essential for building workflows that are both efficient and compliant.
Q-Hub's implementation experience across various engineering environments has identified several common obstacles and effective strategies to overcome them:
- Breaking Down Data Silos: Before implementing Q-Hub, Weston Aerospace struggled with legacy systems that created disconnected information pools. The solution lies in adopting integrated platforms that centralise data management, ensuring real-time access to safety metrics.
- Bridging System Compatibility Gaps: Engineering supply chains often rely on a mix of legacy systems and modern tools. Implementing flexible APIs and middleware can bridge these gaps, enabling smooth communication between disparate systems.
- Fostering User Adoption: Resistance to new technology is natural. When Scottish Leather Group implemented Q-Hub, comprehensive training and focused change management initiatives proved essential for encouraging widespread adoption across all levels of the organisation.
- Managing Implementation Investment: For smaller engineering firms, phased implementation with scalable, modular ERP components allows organisations to start small and expand as needs and budgets allow.
Stakeholder collaboration remains the cornerstone of addressing these challenges. By involving key decision-makers, IT teams, and end-users throughout the integration process, organisations can ensure that ERP systems align with safety goals while addressing unique operational needs.
Building a Culture of Digital Safety Excellence
Even the most advanced ERP systems are only as effective as the people using them. Employee training is therefore a cornerstone of successful safety management transformation. Q-Hub's implementation at Anglia Cathodic Protection demonstrates how proper training leads to increased engagement and accountability across teams.
The platform's ability to share necessary documents and track "read and understood" acknowledgments was transformative. The entire workforce, from shop floor employees to remote workers, gained access to the tools and information needed to perform their roles safely and effectively.
This functionality not only improved compliance but also encouraged a stronger culture of safety accountability and engagement that transcends the technology itself.
The Future of ERP in Safety Management for Engineering Supply Chains
Digital transformation in supply chains continues to evolve, creating new possibilities for safety management workflows. Q-Hub's approach to integrating ERP systems with safety protocols has paved the way for cutting-edge advancements that go beyond automating repetitive tasks. These developments establish predictive and adaptive frameworks that address risks before they occur.
Leading engineering organisations are already implementing several advanced capabilities:
- AI-Driven Risk Prediction: Artificial intelligence now analyses historical and real-time data to predict equipment failures and safety issues before they manifest, allowing for preventative action.
- IoT-Enabled Safety Monitoring: Internet of Things sensors provide continuous updates on critical safety metrics, enabling immediate responses to potential hazards in real-time.
- Advanced Compliance Analytics: Modern ERP systems simplify regulatory adherence by automating the generation of detailed safety audit reports, ensuring organisations remain aligned with evolving standards.
As these technologies continue to evolve, safety management in engineering supply chains will transform even further. Q-Hub's solutions position ERP systems not just as operational tools but as strategic assets that empower organisations to anticipate risks, ensure compliance, and streamline workflows in increasingly complex supply chains.
Ready to transform your engineering safety workflows with integrated ERP solutions? Discover how Q-Hub's tailored digital transformation approach can help you build more efficient, compliant, and proactive safety management systems that support your organisation's long-term growth.
Start using Q-Hub today
- Manage compliance in one place
- Streamline your teams and tasks
- Use Q-Hub free for 30 days