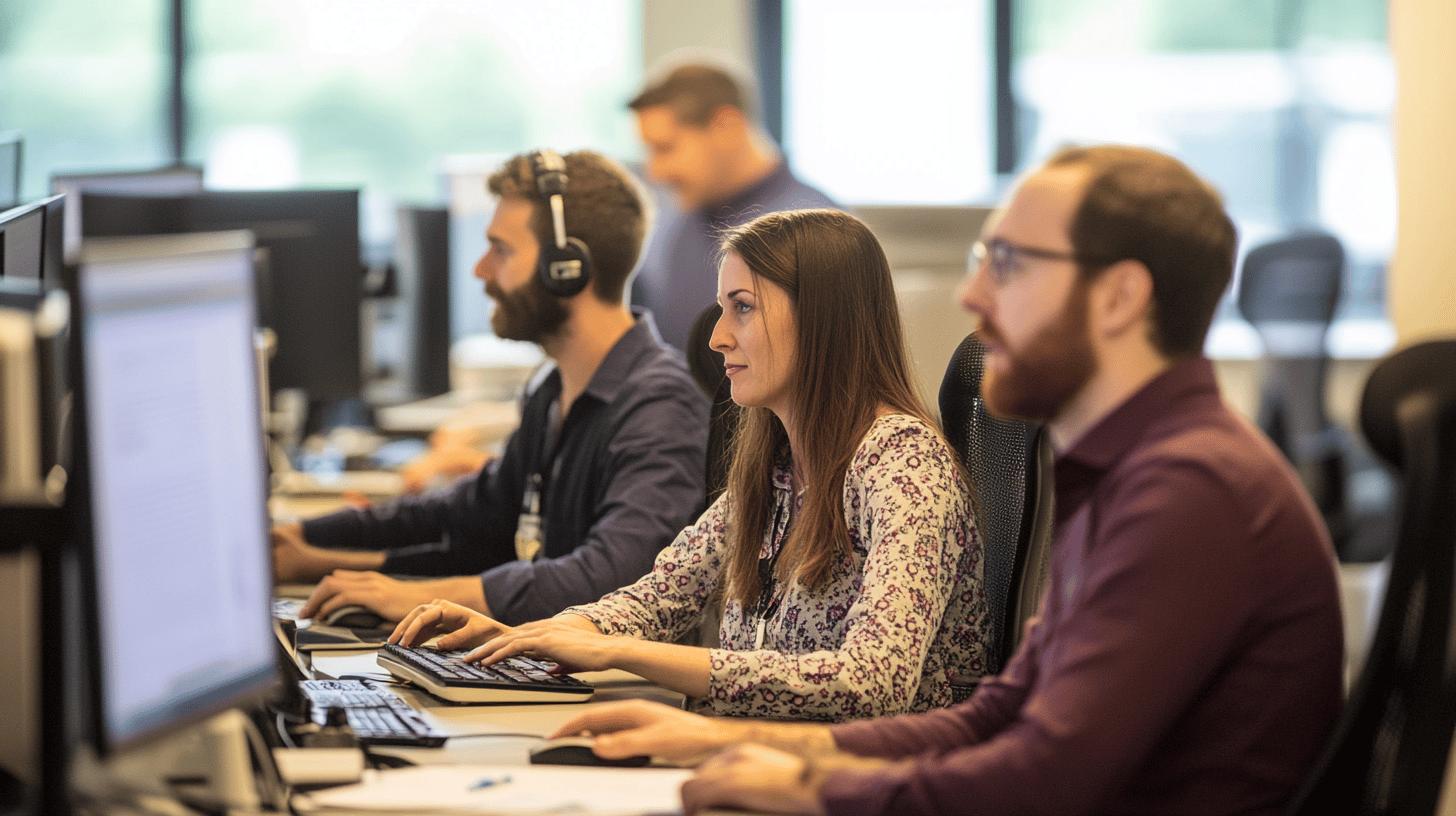
Integration with ERP Systems Boosts Small Facilities Workflows
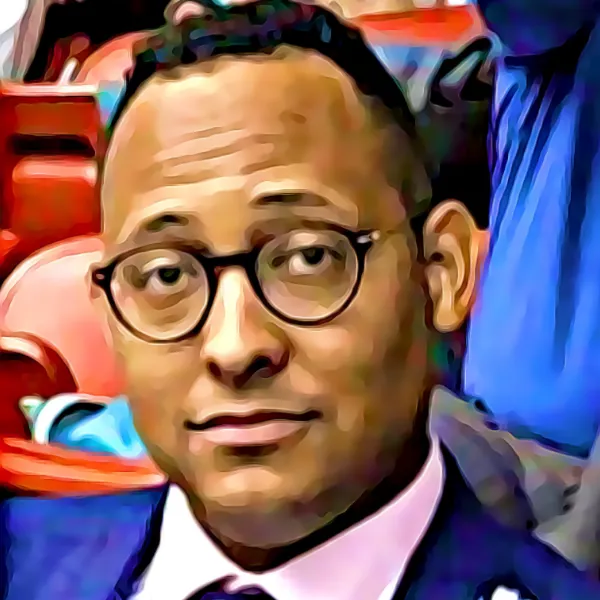
How ERP Systems Enhance Workflow Efficiency in Small Facilities Management Enterprises
Integration with ERP systems improving workflows for small facilities management enterprises creates transformative operational change. By centralising processes through a unified platform, these systems eliminate inefficiencies and create a foundation for streamlined operations. ERP solutions act as a control hub, bringing financial management, human resources, inventory tracking, and customer relationships under one roof, providing real-time data access across departments.
For facilities management businesses, the automation of repetitive tasks like invoice generation and compliance tracking significantly reduces manual input while minimising errors.
When integrating ERP systems, companies often embrace continuous improvement programmes to continually refine their processes. This approach not only aligns with the goal of enhanced efficiency but also empowers facilities to adapt swiftly to evolving operational demands, ensuring every step moves towards a more robust, error-free system. Studies show ERP implementation can boost productivity by up to 20%—a substantial gain for small enterprises operating within tight margins.
- Reduced manual errors for greater operational accuracy
- Faster completion of routine tasks through automation
- Centralised data access for improved decision-making
- Enhanced resource allocation efficiency
Breaking Down Operational Silos with Unified Systems
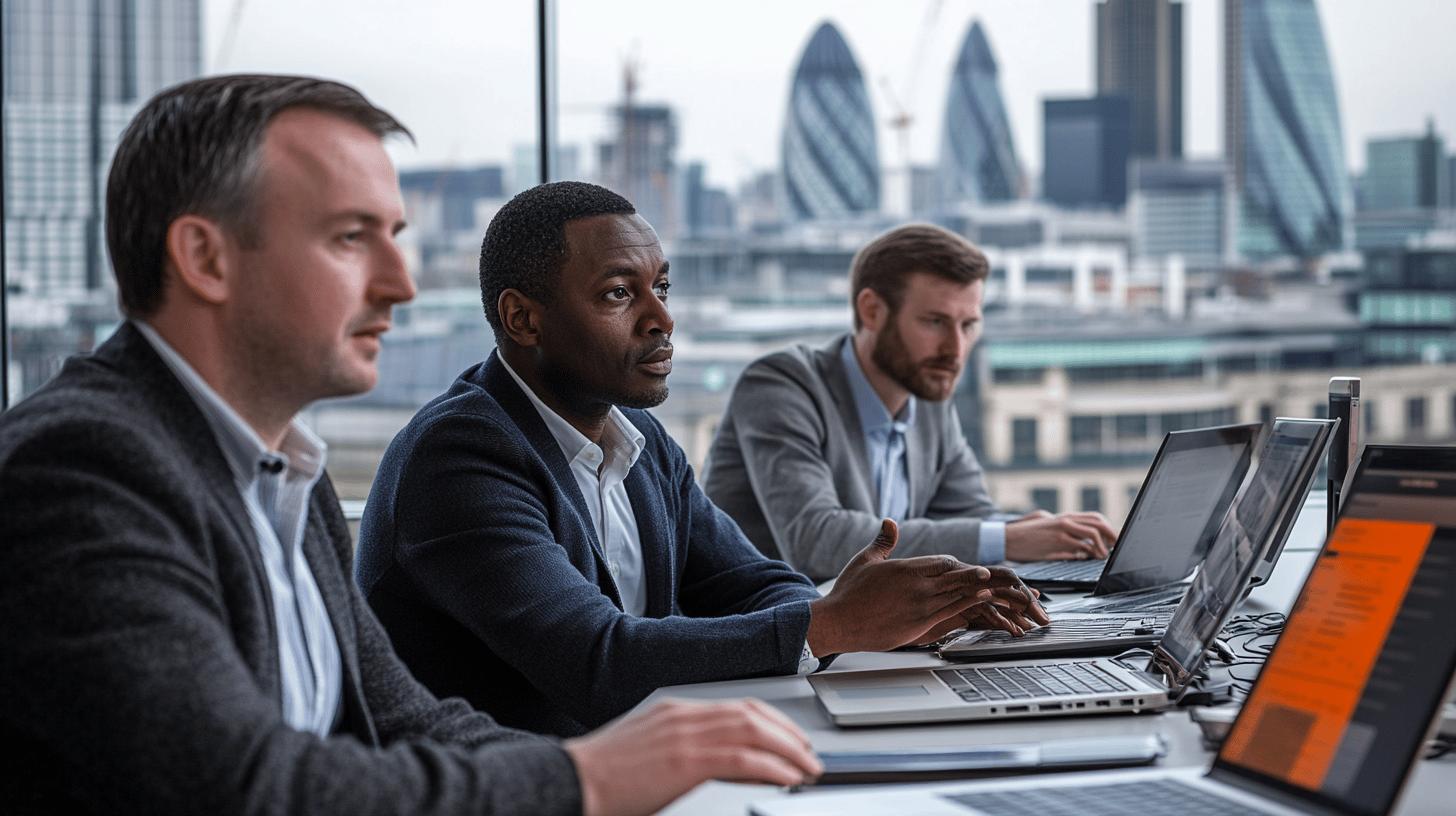
When small facilities management enterprises implement ERP systems, they break down operational silos that once fragmented their processes. Traditional setups often involve disconnected tools—finance software in one place, inventory management in another, and project data somewhere else entirely. This fragmentation creates confusion and slows decision-making.
ERP systems unify these scattered functions into a cohesive database, ensuring all teams access consistent, real-time information.
Moreover, the evolving landscape of digital solutions emphasizes the role of integration with ERP systems in enhancing risk management. By seamlessly connecting data streams across various departments, businesses can swiftly identify and address operational risks, much like how a well-oiled machine identifies and corrects any inefficiencies in real time. This alignment significantly reduces miscommunication risk and eliminates duplicate efforts that waste valuable resources.
The cost benefits are equally compelling. By consolidating multiple software subscriptions into one solution, businesses reduce licensing costs and simplify IT management. The automation of routine tasks frees team members to focus on strategic initiatives instead of administrative busywork.
Tailored Solutions for Unique Business Challenges
Small facilities management enterprises thrive with customised ERP solutions that fit their specific operational needs. Modular platforms like Odoo or Microsoft Dynamics 365 offer flexible implementation options—businesses can start with essential modules for asset management and scheduling, then expand as operations grow.
This modularity ensures companies only pay for features they actually need, keeping costs manageable while delivering powerful functionality. Anglia Cathodic Protection Services experienced this benefit firsthand when they implemented Q-Hub's digital platform to replace their outdated paper and spreadsheet systems.
By digitising fragmented compliance and quality processes, we eliminated bottlenecks and enhanced operational oversight, making our systems more accessible and actionable for all employees.
Scalability remains perhaps the most critical advantage. As facilities management demands fluctuate, ERP systems can expand or contract without requiring complete overhauls, protecting long-term investments and ensuring competitiveness as businesses evolve.
Navigating Implementation Challenges Successfully
While ERP integration delivers significant benefits, small facilities management businesses often face challenges during implementation. Data migration presents a common hurdle—transferring historical information from legacy systems can be complex when dealing with inconsistent formats or incompatible structures.
System compatibility issues compound this problem, especially for businesses relying on older software. If the new ERP system cannot communicate effectively with existing platforms, it risks creating new silos rather than eliminating them—precisely the opposite of the intended outcome.
Employee resistance often becomes another significant obstacle. Staff accustomed to traditional workflows may hesitate to adopt new systems, fearing disruption to established routines. This is where comprehensive training becomes essential, turning scepticism into enthusiastic adoption.
For successful implementation, consider these proven strategies:
- Conduct thorough needs assessments before selection to ensure alignment with business requirements
- Verify compatibility with existing systems to prevent integration roadblocks
- Develop comprehensive training programmes to boost user confidence
- Implement phased rollouts to minimise operational disruptions
Real-World Transformation: Measurable Results
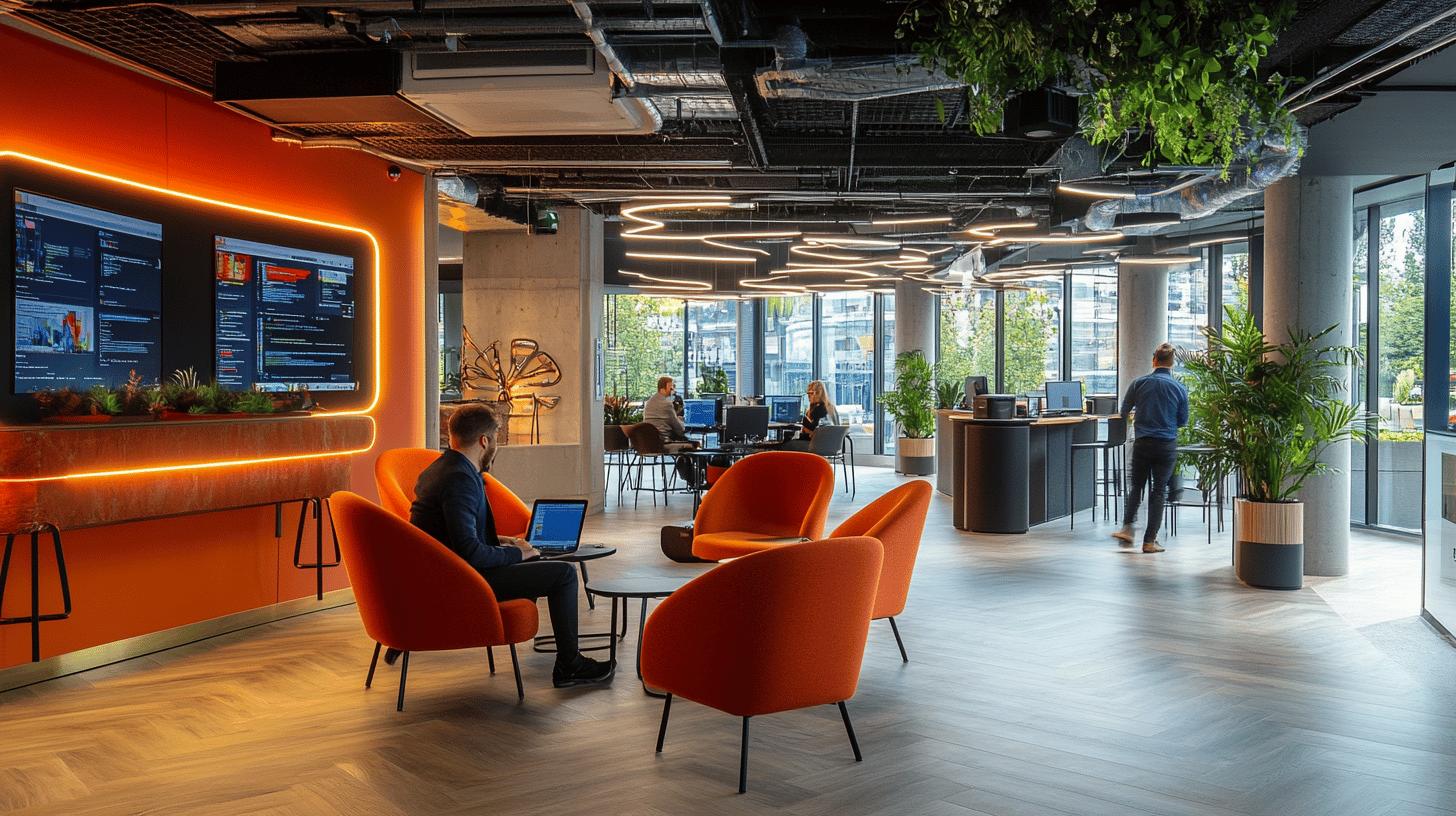
The impact of ERP integration becomes clear when examining real-world applications. One facilities management company struggled with manual workflows, slow task completion, and inefficient communication before implementing a cloud-based ERP solution.
The results were remarkable, as shown in this performance comparison:
<table border="0"> <tr><th>Performance Metric</th><th>Before Integration</th><th>After Integration</th><th>Improvement</th></tr> <tr><td>Manual Processes</td><td>60%</td><td>20%</td><td>40% reduction</td></tr> <tr><td>Task Completion Time</td><td>72 hours</td><td>54 hours</td><td>25% faster</td></tr> <tr><td>Client Response Time</td><td>2 days</td><td>1 day</td><td>50% faster</td></tr> </table>Similar transformations occurred at Fowlers of Bristol, where Q-Hub's implementation centralized communications and data management. As their experience demonstrates, replacing fragmented processes with unified digital systems creates immediate operational improvements.
The Future: Smart Technologies Reshaping ERP Capabilities
The evolution of ERP systems for facilities management continues with emerging technologies that promise even greater efficiencies. AI and IoT integration are revolutionising how businesses approach maintenance planning and asset management.
Predictive analytics now enables companies to anticipate equipment failures before they occur. IoT-enabled sensors monitor performance in real-time, feeding data directly into ERP systems to trigger automated maintenance scheduling or alerts. This shift from reactive to proactive management significantly reduces downtime and unexpected repair costs.
Mobile applications represent another transformative trend, providing anywhere access to critical data. Field teams can update, review, and execute tasks remotely, accelerating decision-making and improving coordination. Cloud-based systems further enhance this flexibility while ensuring data security and accessibility.
Q-Hub continues leading this digital transformation by developing customised QHSE software solutions that help facilities management enterprises streamline operations and ensure compliance. Their cloud-hosted platforms enable businesses to centralize workflows, unify communications, and implement data-driven decision-making—essential capabilities for today's competitive environment.
Whether you're struggling with fragmented processes or seeking to optimize existing operations, the right ERP solution can transform your facilities management enterprise into a more efficient, responsive, and profitable business. Explore how Q-Hub's tailored software solutions can help you achieve these operational improvements while supporting sustainable growth.