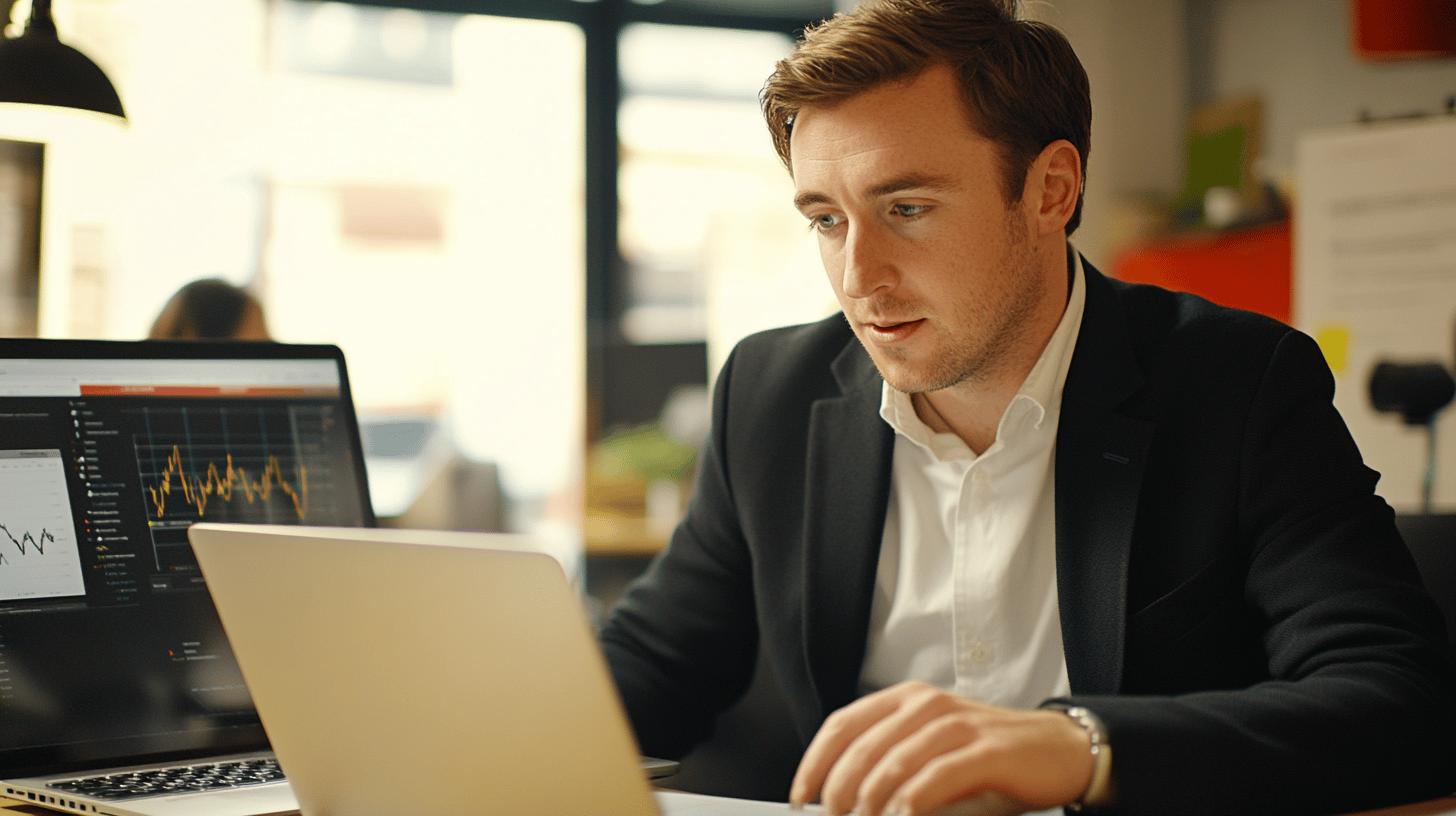
Integration with ERP Systems Boosts Risk Management
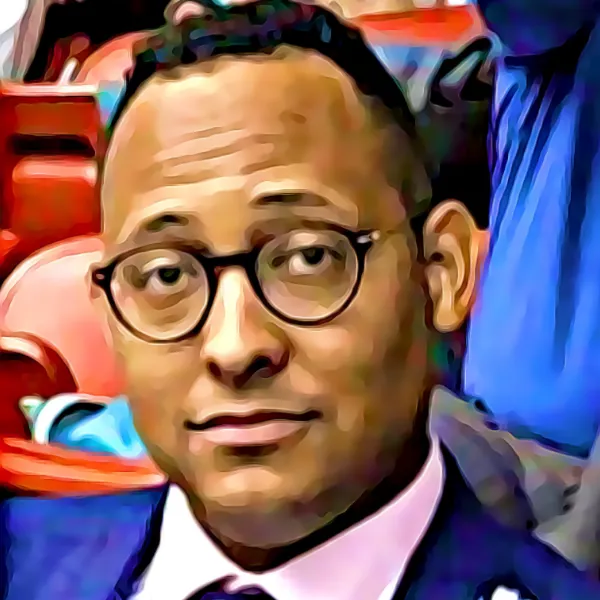
The Role of Integration with ERP Systems in Enhancing Risk Management in Facilities Supply Chains
Integrating ERP systems into facilities supply chains transforms risk management workflows by creating a unified operational platform. Q-Hub's specialised software solutions streamline this integration, centralising finance, logistics, and compliance reporting to deliver real-time visibility across the entire supply chain. This consolidation empowers facilities managers to access crucial data instantly – from inventory levels to transportation schedules – enabling informed decisions that reduce risk and optimise efficiency in ways that fragmented systems simply cannot achieve.
Modern ERP systems excel by automating compliance processes, significantly reducing human error while creating reliable audit trails for regulatory reporting. For instance, when ensuring adherence to the Health and Safety at Work Act 1974, an integrated ERP solution can automatically track compliance metrics and flag potential issues before they escalate. Meanwhile, predictive analytics capabilities identify supply chain vulnerabilities early, allowing teams to address risks proactively rather than reactively managing problems after they occur.
- Automates compliance processes, ensuring consistent regulatory adherence
- Provides real-time visibility across inventory, operations, and logistics
- Delivers predictive analytics for early risk identification
- Creates reliable audit trails for enhanced accountability
- Streamlines cross-departmental communication and decision-making
Transforming Visibility and Response Through Real-Time Data
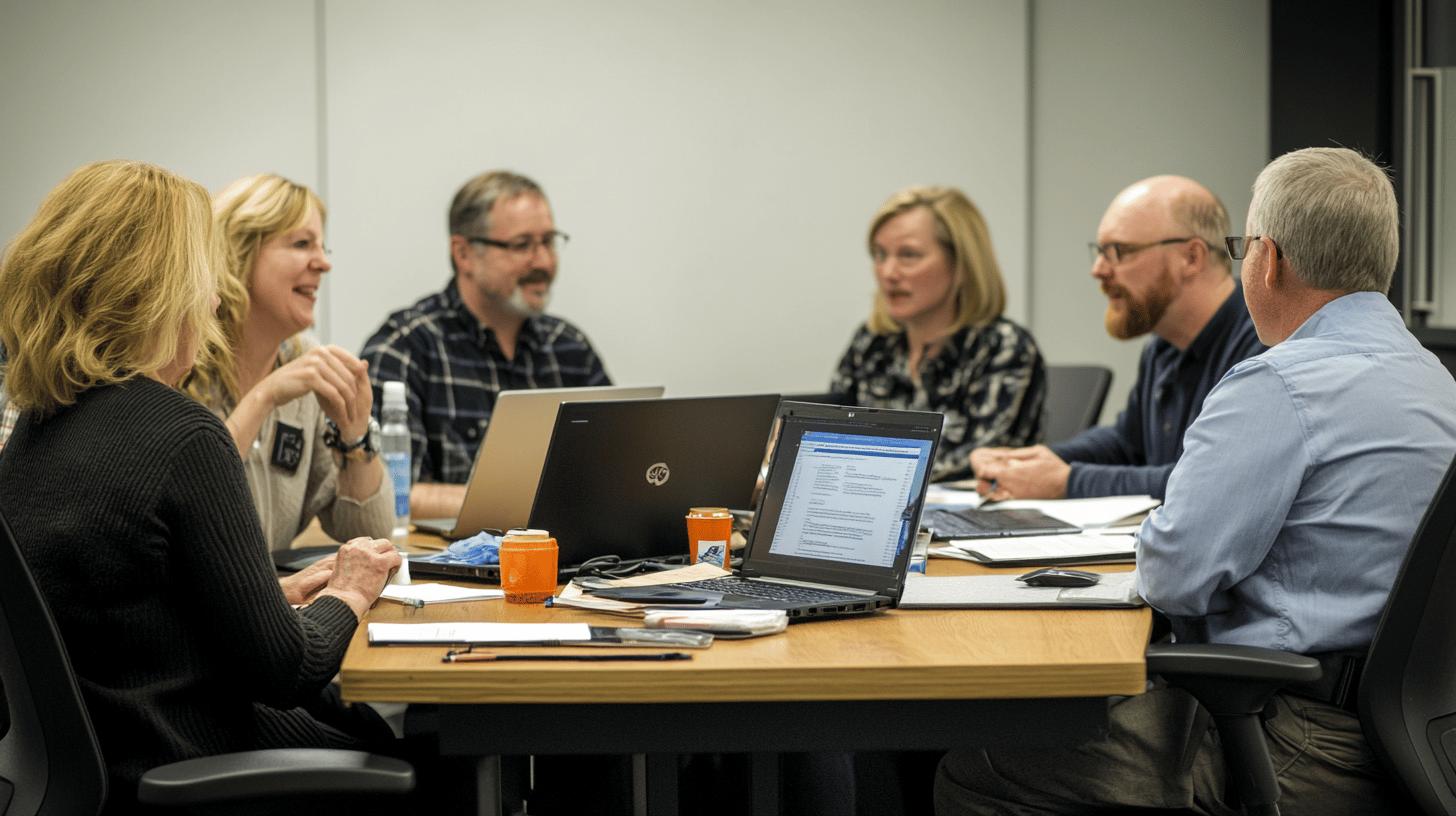
One standout benefit of ERP integration is comprehensive real-time data visibility. This matters because timely access to accurate information forms the backbone of effective risk management. When inventory levels, production schedules, and supplier performance metrics are available at a glance, businesses can respond instantly to potential disruptions.
Consider Anglia Cathodic Protection's experience after implementing Q-Hub's solutions. Their previous fragmented processes and paper-based systems created significant blind spots across multiple sites. With Q-Hub's digital platform, they gained immediate visibility into compliance issues and operational inefficiencies, enabling them to identify and address risks before they affected service delivery.
"Before Qhub, managing compliance and quality processes was a manual, disjointed effort. Documents were stored across spreadsheets and paper-based systems, leading to miscommunication and errors." Source: Anglia Cathodic Protection Case Study
Automation represents another critical advantage. By automating routine compliance processes, ERP systems significantly reduce human error while increasing reliability. Scottish Leather Group leveraged Q-Hub's platform to transform their ISO compliance management across multiple standards simultaneously, freeing valuable resources from administrative tasks while ensuring nothing slipped through the cracks.
Overcoming Integration Challenges with Strategic Implementation
While the benefits are substantial, organisations often face significant hurdles when integrating ERP systems. Data migration presents perhaps the most critical challenge, as transferring large volumes of information from disparate formats can lead to inconsistencies that compromise both operational efficiency and risk management accuracy.
The solution lies in methodical planning and phased implementation. Fowlers of Bristol overcame these challenges by first centralising their communication and data management through Q-Hub's intuitive portal. This approach brought critical workflows, datasets, and communications into a single digital space before proceeding with more complex integrations.
System interoperability presents another common obstacle, as most facilities supply chains rely on a mixture of legacy systems and modern software tools. Rather than complete system overhauls, middleware solutions often provide efficient bridges between incompatible systems, enabling seamless data exchange while minimising disruption.
Resistance to change frequently undermines ERP implementations when not properly addressed. Weston Aerospace countered this by involving stakeholders early in the process and providing comprehensive training. Their phased approach helped teams adapt to digital workflows gradually, building confidence and demonstrating value before expanding to more complex processes.
- Conduct thorough audits of existing systems before integration
- Implement phased data migration to minimise errors and disruptions
- Deploy middleware solutions when needed to bridge legacy system gaps
- Develop robust change management plans addressing employee concerns
- Invest in comprehensive training across all staff levels
- Engage experienced consultants for complex integration scenarios
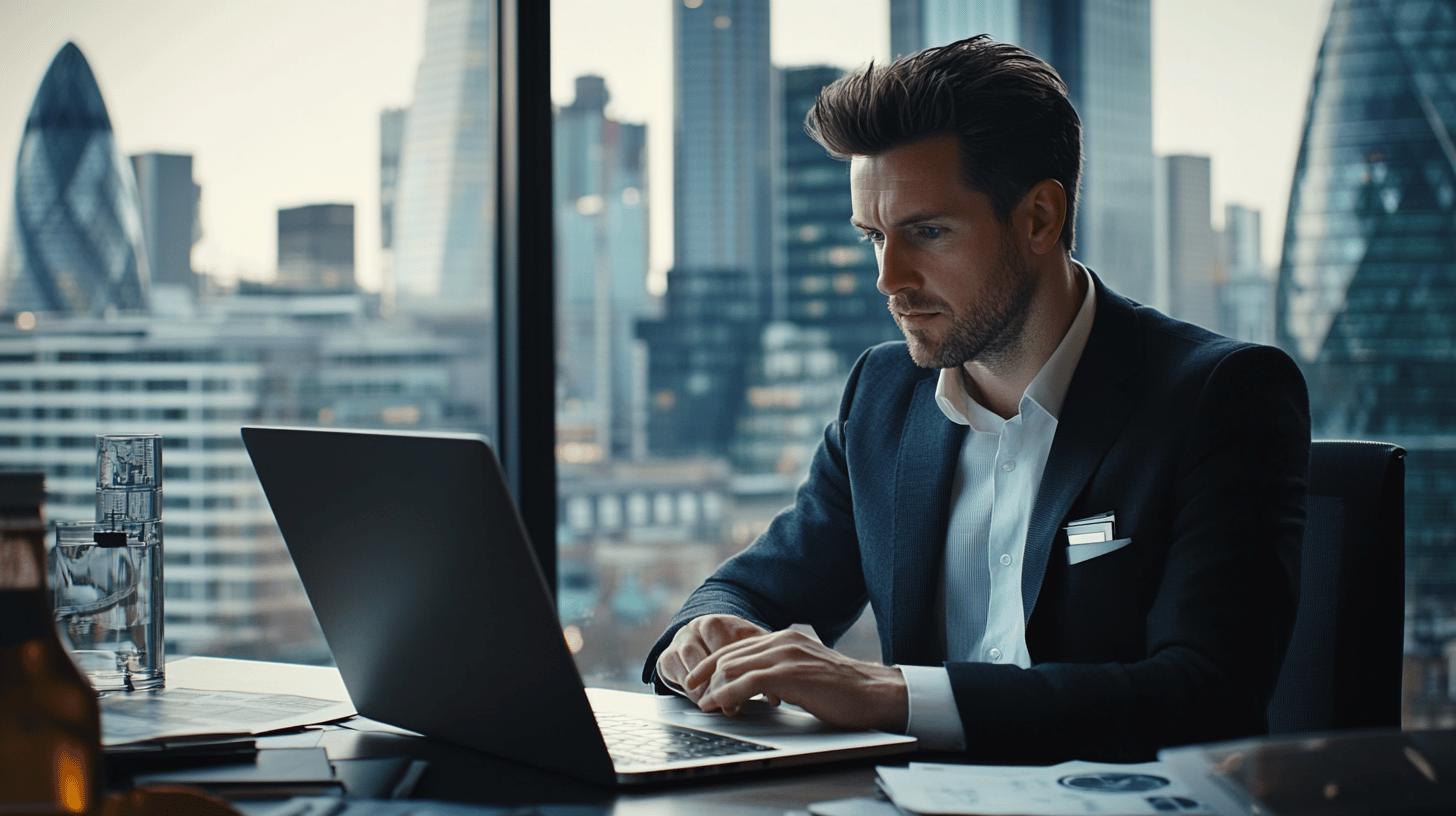
Building Data Security Foundations for Sustainable Integration
Data security and governance must remain central priorities during ERP integration. Without proper safeguards, sensitive operational information becomes vulnerable to cyber threats. Encryption both in transit and at rest provides essential protection, while role-based access controls ensure employees only interact with information relevant to their responsibilities.
BMC Analysis addressed these concerns by implementing Q-Hub's Document Library with structured permissions and version control. This approach not only secured sensitive information but also created clear audit trails showing exactly who accessed what information and when – critical for both security and compliance purposes.
Harnessing Predictive Analytics for Proactive Risk Management
The most forward-thinking aspect of ERP integration is its ability to transform risk management from reactive to proactive through predictive analytics. By leveraging historical data and AI-driven insights, these systems forecast potential disruptions before they materialise, giving facilities managers crucial lead time to implement preventative measures.
Real-world applications demonstrate the tangible value of this approach. Rocal Insulating Panels implemented Q-Hub's dashboards to centralise safety operations, making it easier to track near misses, daily inspections, and identify accident trends before they resulted in serious incidents. This visibility extended across all levels of the organisation, ensuring consistent safety processes and rapidly identifying emerging risks.
The ROI of such implementations can be substantial. Beyond immediate cost savings from preventing disruptions, organisations typically see improvements across three key metrics:
<table border="0"> <tr><th>Metric</th><th>Before ERP Integration</th><th>After ERP Integration</th></tr> <tr><td>Compliance Management</td><td>Manual, error-prone processes</td><td>Automated workflows with real-time monitoring</td></tr> <tr><td>Risk Identification</td><td>Reactive response after incidents</td><td>Proactive detection through predictive analytics</td></tr> <tr><td>Operational Efficiency</td><td>Siloed data with delayed reporting</td><td>Centralised information with real-time visibility</td></tr> </table>What's Next? Future-Proofing Supply Chain Risk Management
Looking ahead, the integration of ERP systems with emerging technologies is reshaping facilities supply chain risk management. IoT sensors now provide continuous data streams on equipment performance and environmental conditions, feeding directly into ERP systems to trigger automated alerts before failures occur. Meanwhile, digital twins – virtual replicas of physical assets – enable scenario planning and stress-testing without operational disruption.
Cloud-based solutions, like those offered by Q-Hub, deliver the agility to adapt quickly as conditions change. They enable seamless collaboration across geographies and departments while maintaining data integrity and security. When combined with blockchain for enhanced traceability and edge computing for faster local processing, these integrated systems create unprecedented supply chain resilience.
The most successful implementations share a common element: they're built on flexible platforms that evolve alongside business needs. Q-Hub's modular approach enables organisations to start with their most pressing challenges – whether that's compliance management, document control, or operational efficiency – and expand functionality as their digital maturity grows.
As supply chains grow increasingly complex and regulatory requirements more demanding, integrated ERP solutions will continue to be the foundation of effective risk management. By partnering with specialists like Q-Hub who understand both the technical requirements and operational realities of facilities management, organisations can transform potential vulnerabilities into strategic advantages through digital transformation.