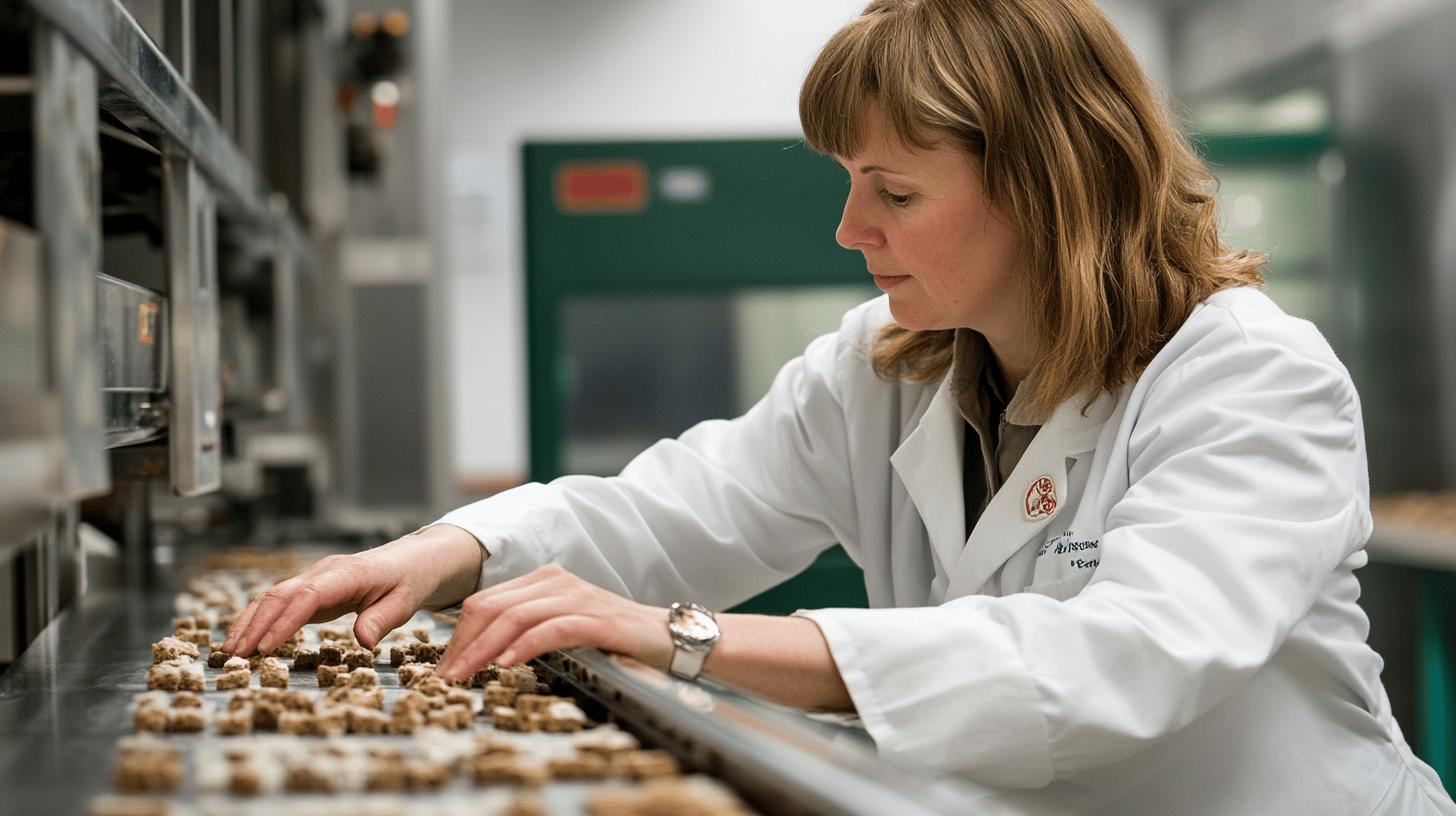
Enterprise Quality Control Solutions Enhance Food Processing
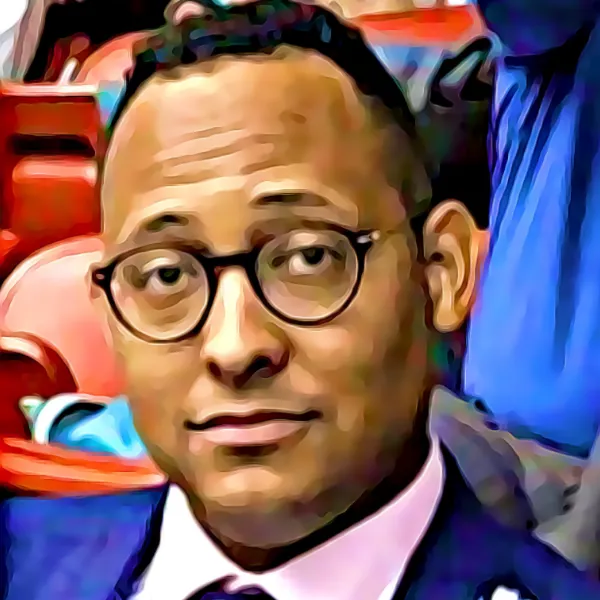
Advanced Enterprise Quality Control Solutions for the Food Processing Industry
Enterprise quality control solutions have become essential for modern food processing facilities striving to maintain high standards in today's competitive market. These digital management platforms combine software tools with automated processes to ensure safety, compliance and operational efficiency. Q-Hub's customised solutions enable large-scale operations to seamlessly integrate quality management into existing workflows, helping businesses meet increasingly stringent regulatory requirements while satisfying consumer demands.
At their core, these enterprise-level tools use technology to optimise processes and enhance decision-making. Digital Quality Management Systems monitor operations in real-time, immediately flagging inconsistencies or defects. When integrated with existing business systems, they bring data-driven precision to quality control, standardising processes while enabling rapid responses to potential issues.
The Digital Revolution in Food Safety Management
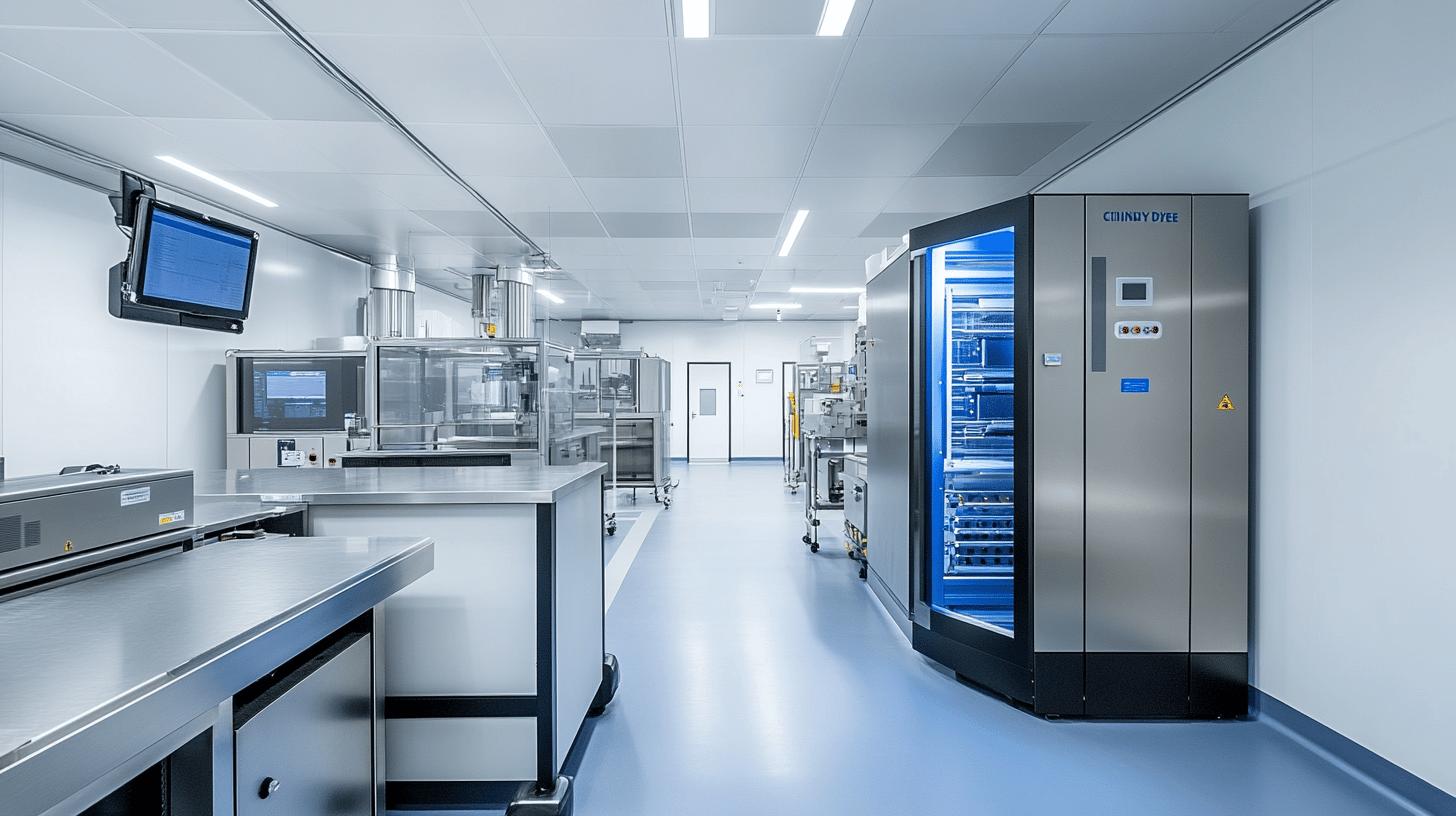
Modern food processing facilities are increasingly turning to digital solutions to replace manual, paper-based systems. These platforms create a central hub for all quality-related activities, from compliance documentation to audit management. The results are impressive: reduced errors, improved traceability, and significant time savings.
"Implementing a digital quality management system transformed our operations, reducing audit preparation time from days to just hours while giving us unprecedented visibility into our processes."
Key benefits of implementing enterprise quality control solutions include:
- Improved supply chain traceability for better accountability
- Real-time monitoring for immediate issue detection and resolution
- Enhanced compliance with ISO 22000 and BRCGS standards
- Reduced operational errors, minimising waste and costly recalls
- Streamlined audits with automated documentation capabilities
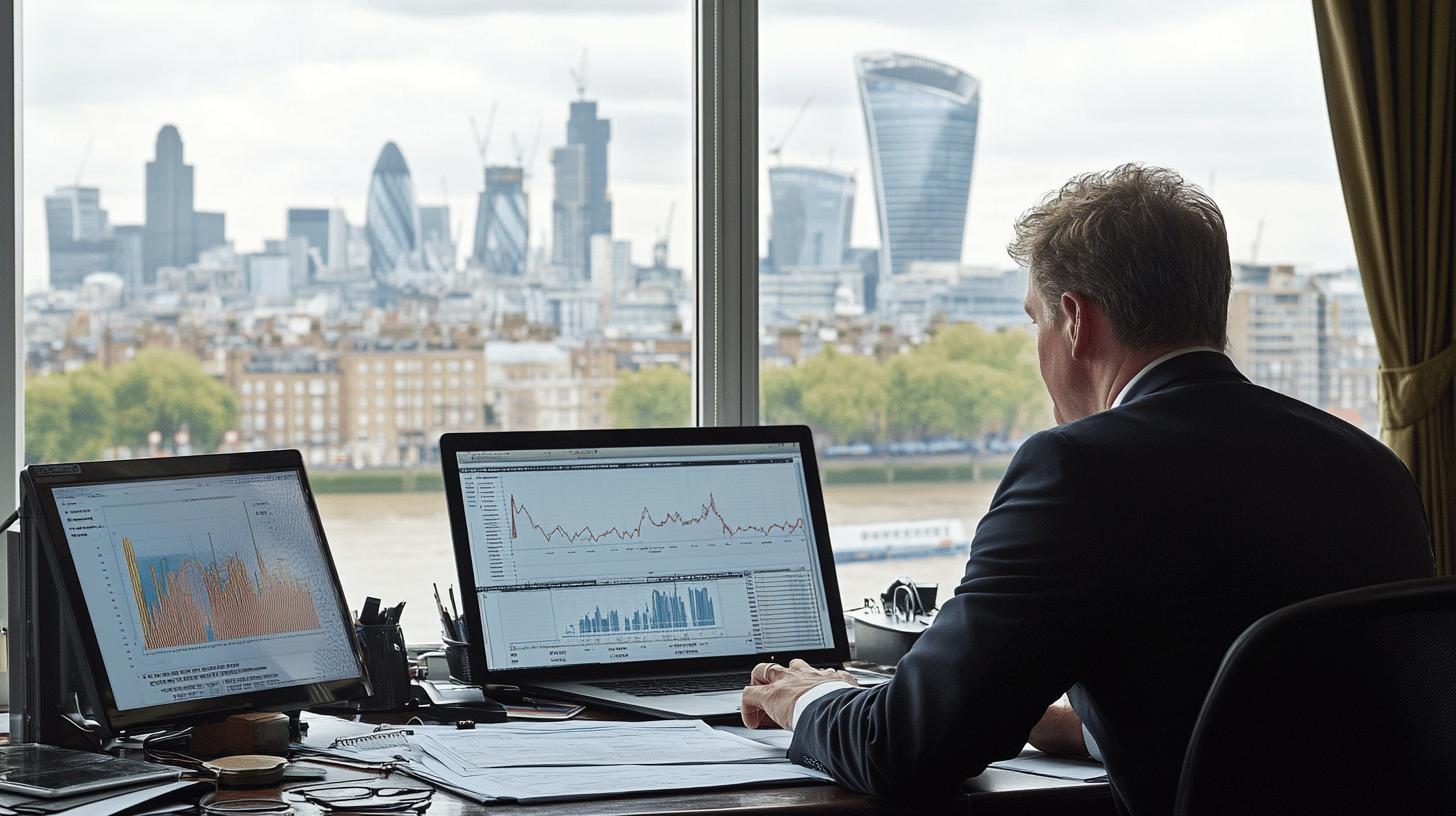
Critical Food Safety Standards That Drive Compliance
Food safety standards form the foundation of effective quality control in the processing industry. These frameworks ensure every step in production adheres to safety measures, protecting both consumers and businesses. For enterprise operations, implementing robust digital systems to manage these standards isn't optional—it's essential for market survival.
HACCP (Hazard Analysis and Critical Control Points) represents the core of food safety regulations, identifying potential hazards and establishing controls to mitigate them. Rather than reacting to problems after they occur, HACCP takes a proactive approach, systematically addressing biological, chemical, and physical risks before they impact products.
Good Manufacturing Practices (GMP) complement HACCP by focusing on maintaining safe, hygienic production environments. These practical standards cover facility design, equipment maintenance, and employee training—essential elements for contamination prevention.
Standard | Traditional Management | Digital Management |
---|---|---|
HACCP | Paper-based records | Real-time monitoring dashboards |
GMP | Manual inspection logs | Automated compliance tracking |
ISO 22000 | Fragmented documentation | Integrated management system |
Transforming Operations Through Automated Inspection
Automated inspection systems are revolutionising quality control in food processing. Unlike traditional methods relying on manual checks, these advanced technologies use artificial intelligence, sensors and machine learning to deliver precision and efficiency that human inspection simply cannot match.
Companies implementing these technologies benefit from significant improvements across their operations. For example, real-time monitoring enables immediate detection of quality issues before products leave the facility, dramatically reducing recall risks and associated costs.
Predictive maintenance represents another game-changing application in food processing. By using IoT sensors and machine learning algorithms, equipment performance can be monitored in real-time, with potential issues flagged before failures occur. This proactive approach reduces unplanned downtime, extends equipment lifespan, and prevents contamination risks that could arise from malfunctioning machinery.
Building Transparency Through Digital Traceability
Traceability has become non-negotiable in modern food production. Digital traceability systems provide a complete record of every product's journey from raw material sourcing to final distribution. This transparency meets growing consumer demands while satisfying increasingly strict regulatory requirements.
Audit trail documentation represents a cornerstone of effective traceability. These detailed digital records track every action, decision and transaction within the supply chain. When contamination issues arise, companies can quickly identify affected products, pinpoint the source, and take targeted action—minimising the scope and cost of recalls.
Key Benefits of Digital Traceability Systems
- Mitigates contamination and mislabelling risks
- Prevents fraud through verification of material authenticity
- Builds consumer trust through transparent practices
- Ensures regulatory compliance across jurisdictions
- Enables faster, more accurate recall management
Strategic Risk Management for Contamination Prevention
Effective risk management in food processing requires a comprehensive approach spanning multiple disciplines. Digital solutions from Q-Hub enable businesses to implement robust frameworks for identifying, assessing and mitigating potential hazards before they impact product safety or quality.
Contamination prevention relies on thorough protocols addressing various risk types. Allergen management demands precise labelling and production segregation, while microbial testing involves regular sampling to detect harmful pathogens. Chemical residue testing ensures cleaning agents and pesticides don't compromise product integrity.
Employee training forms the foundation of successful risk management implementation. A well-trained workforce understands the importance of following established procedures and can identify potential issues before they escalate. Digital training management ensures all staff receive appropriate instruction and that completion is properly documented for compliance purposes.
Measuring the ROI of Quality Management Solutions
Enterprise quality control platforms deliver measurable returns on investment that extend far beyond basic compliance. In an industry with thin margins and high standards, efficiency improvements translate directly to profitability. Q-Hub's solutions help businesses realise these gains through strategic digital transformation.
Cost savings represent the most immediate benefit. By minimising recalls, reducing waste, and preventing production errors, businesses significantly lower operational expenses. Automated monitoring identifies inefficiencies in real-time, ensuring optimal resource utilisation. Similarly, streamlined compliance management prevents costly non-conformance penalties that can erode profits.
The Scottish Leather Group demonstrates the transformative impact of implementing comprehensive quality management solutions. By moving from paper-based systems to Q-Hub's digital platform, they unified processes across multiple sites, streamlined compliance with various ISO standards, and dramatically improved interdepartmental communication. Their audit preparation time decreased significantly while overall operational efficiency improved.
Balancing quality demands with cost constraints remains a significant challenge for food processors. Digital quality management helps achieve this balance by optimising labour, materials and time resources. Automated workflows reduce errors while predictive analytics ensure maintenance occurs only when necessary, eliminating wasteful interventions and supporting continuous improvement.
Ready to transform your food processing quality management with tailored digital solutions? Q-Hub's customised software helps businesses ensure compliance, streamline processes and support long-term growth through strategic digital transformation. Discover how our expertise can elevate your quality control operations while delivering measurable efficiency improvements across your enterprise.