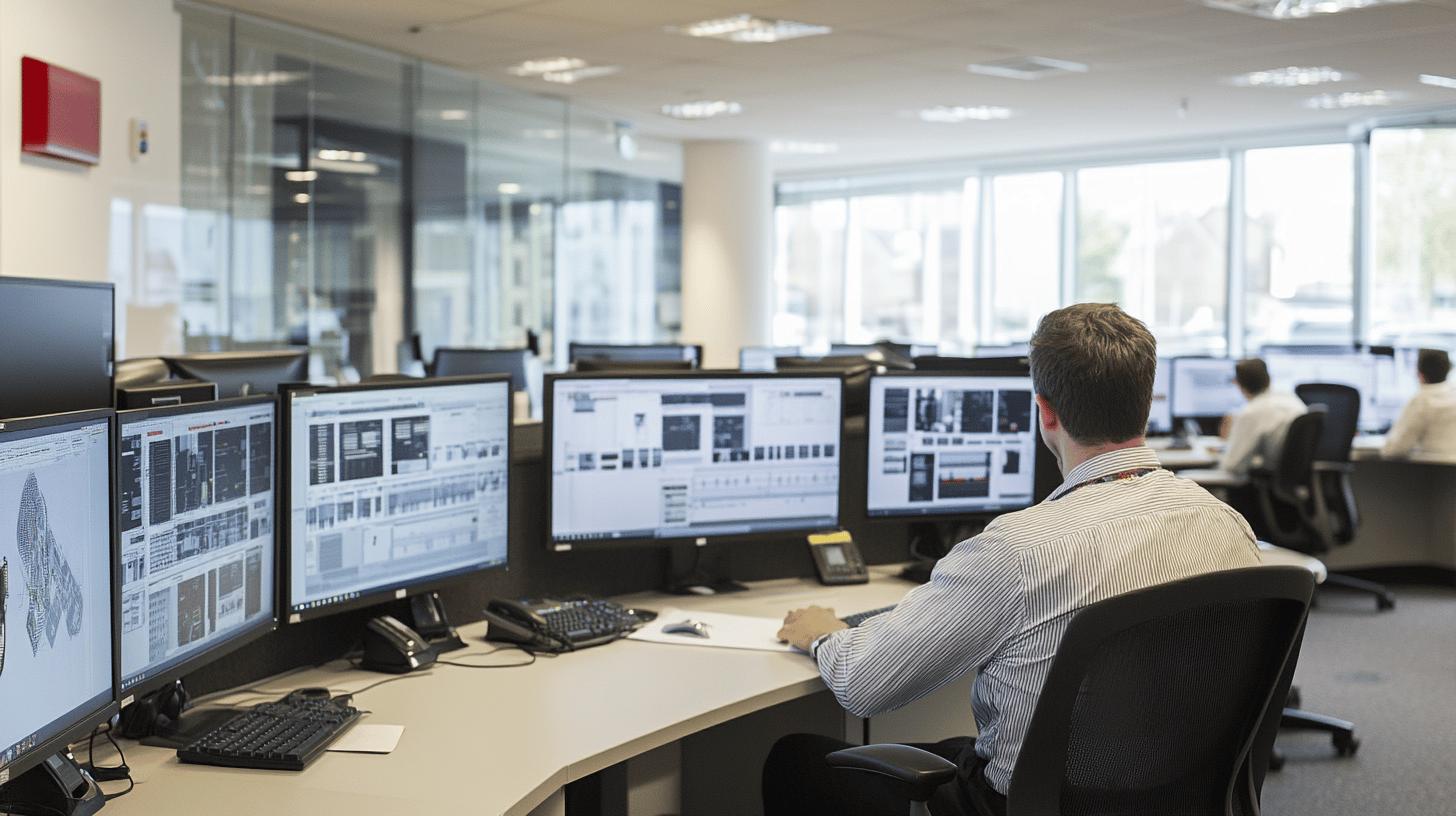
Custom Automation Tools Transform Engineering Risk Response
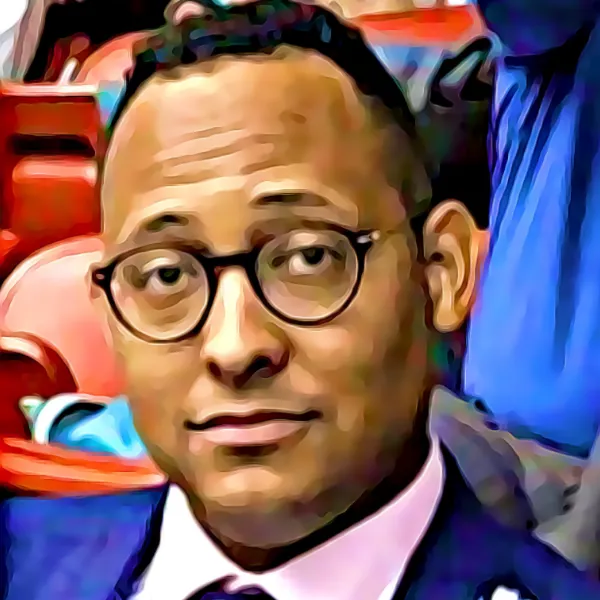
How Custom Automation Tools Enhance Risk Assessment in Engineering Operations
Custom automation tools are revolutionising risk assessment in engineering operations. By integrating AI and machine learning, these technologies replace error-prone manual methods with data-driven insights that identify and prioritise threats in real time. Q-Hub's tailored solutions help engineering teams transform fragmented processes into streamlined workflows, ensuring critical issues are addressed promptly while maintaining compliance with standards like ISO 9001 and ISO 45001.
In regulated industries such as aerospace and nuclear, where precision is non-negotiable, automated risk evaluation provides continuous monitoring that flags compliance gaps instantly. This proactive approach enables faster, more informed decision-making that prevents costly escalations and keeps operations running smoothly.
From Reactive to Proactive: The Evolution of Engineering Risk Management
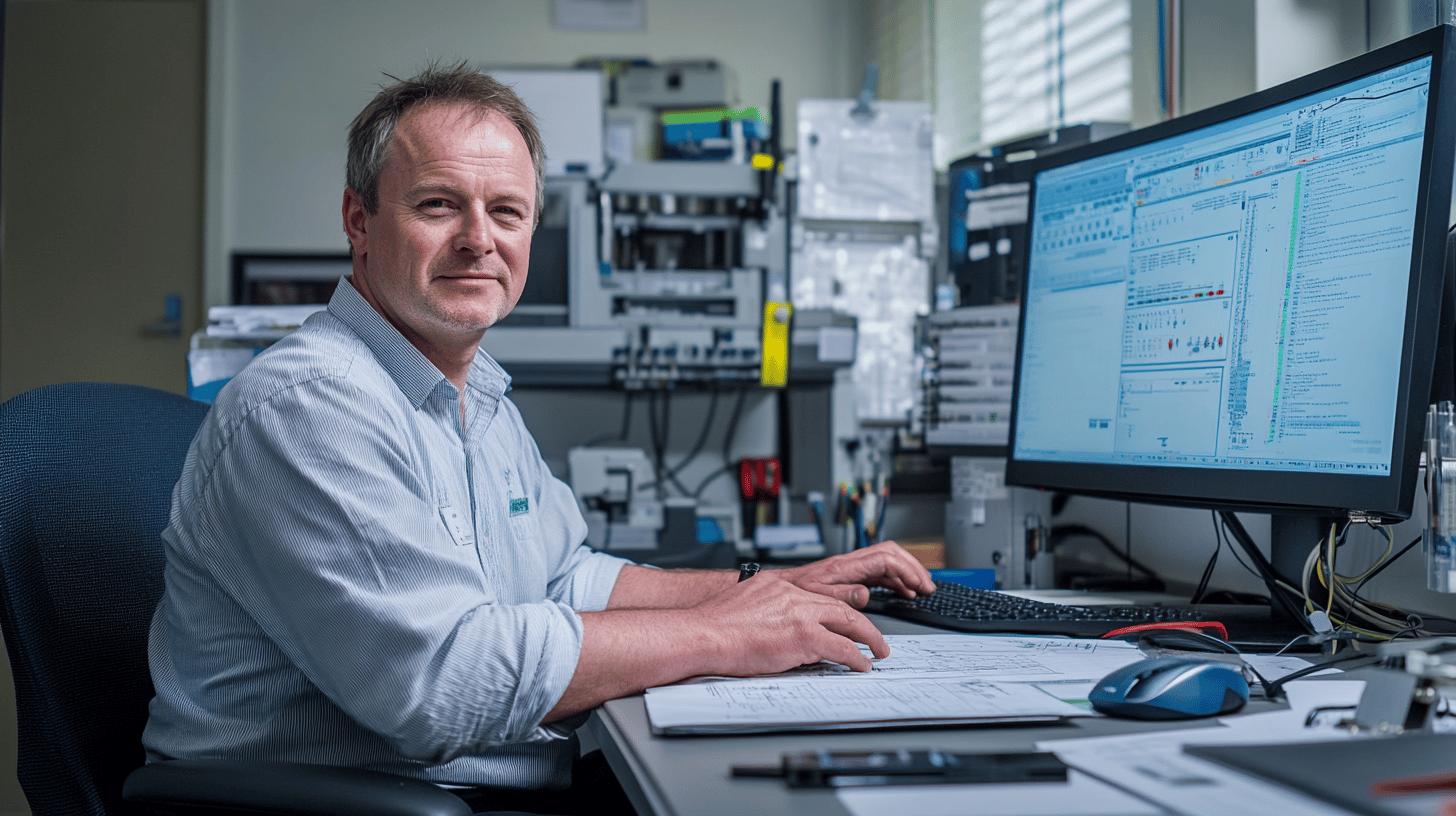
Traditional risk management struggles with fragmented data and inconsistent evaluations. Custom automation tools address these challenges by centralising information and standardising assessments. In automotive manufacturing, for example, these solutions can slash assessment timeframes by 40%, giving engineering teams the agility they need in dynamic environments.
The Scottish Leather Group demonstrates this transformation in action. Previously hindered by paper-based systems across multiple sites, they implemented Q-Hub's digital platform to unify their ISO compliance processes. The result was dramatically reduced audit preparation time and improved interdepartmental communication.
By streamlining our compliance processes through automation, we've eliminated silos and freed our team to focus on value-added activities rather than administrative tasks.
Automated systems excel by continuously monitoring operations and flagging anomalies immediately. This allows organisations to:
- Prioritise high-risk areas efficiently, optimising resource allocation
- Reduce human error through AI-driven consistency
- Adapt quickly to evolving compliance requirements
- Enhance operational resilience with faster response capabilities
Real-Time Intelligence: The Backbone of Modern Risk Response
Real-time data analysis forms the foundation of effective risk management in engineering. Automated systems continuously monitor operations, enabling instant detection of anomalies and potential hazards. This proactive approach represents a significant departure from traditional methods that often rely on retrospective evaluations.
Weston Aerospace exemplifies this shift. Before implementing Q-Hub's platform, their compliance team struggled with time-consuming manual processes for tracking NCRs and conducting audits. By digitising these workflows, they achieved real-time visibility into resolution progress and significantly reduced administrative burden.
<table border="0"> <tr><th>Engineering Challenge</th><th>Traditional Approach</th><th>Automation Solution</th></tr> <tr><td>Risk Identification</td><td>Manual inspections, delayed reporting</td><td>Real-time monitoring with instant alerts</td></tr> <tr><td>Compliance Management</td><td>Paper-based audits, fragmented records</td><td>Centralised digital platform with automated scheduling</td></tr> <tr><td>Data Analysis</td><td>Time-consuming manual review</td><td>AI-powered analytics with predictive capabilities</td></tr> <tr><td>Response Time</td><td>Hours to days</td><td>Minutes to hours</td></tr> </table>Bespoke Solutions: Tailoring Technology to Unique Engineering Challenges
One-size-fits-all approaches rarely work in engineering risk management. Bespoke automation tools excel by adapting to the specific requirements of different operations. These customised solutions integrate seamlessly with existing systems while addressing unique industry challenges.
Fowlers of Bristol illustrates this perfectly. Their journey from paper-based processes to Q-Hub's digital platform revolutionised document control and quality management. By implementing version controls and linking documents directly to tasks, they significantly reduced errors and streamlined their "Zero Defects" quality initiative.
- Customised solutions integrate smoothly with existing engineering workflows
- Sector-specific configurations address unique regulatory requirements
- Flexible platforms adapt as organisational needs evolve
- Centralised data improves cross-departmental collaboration
The scalability of these tools makes them particularly valuable for growing organisations. As operational complexities increase, bespoke automation systems expand accordingly without requiring proportional increases in resources or personnel.
Predictive Maintenance: Preventing Problems Before They Occur
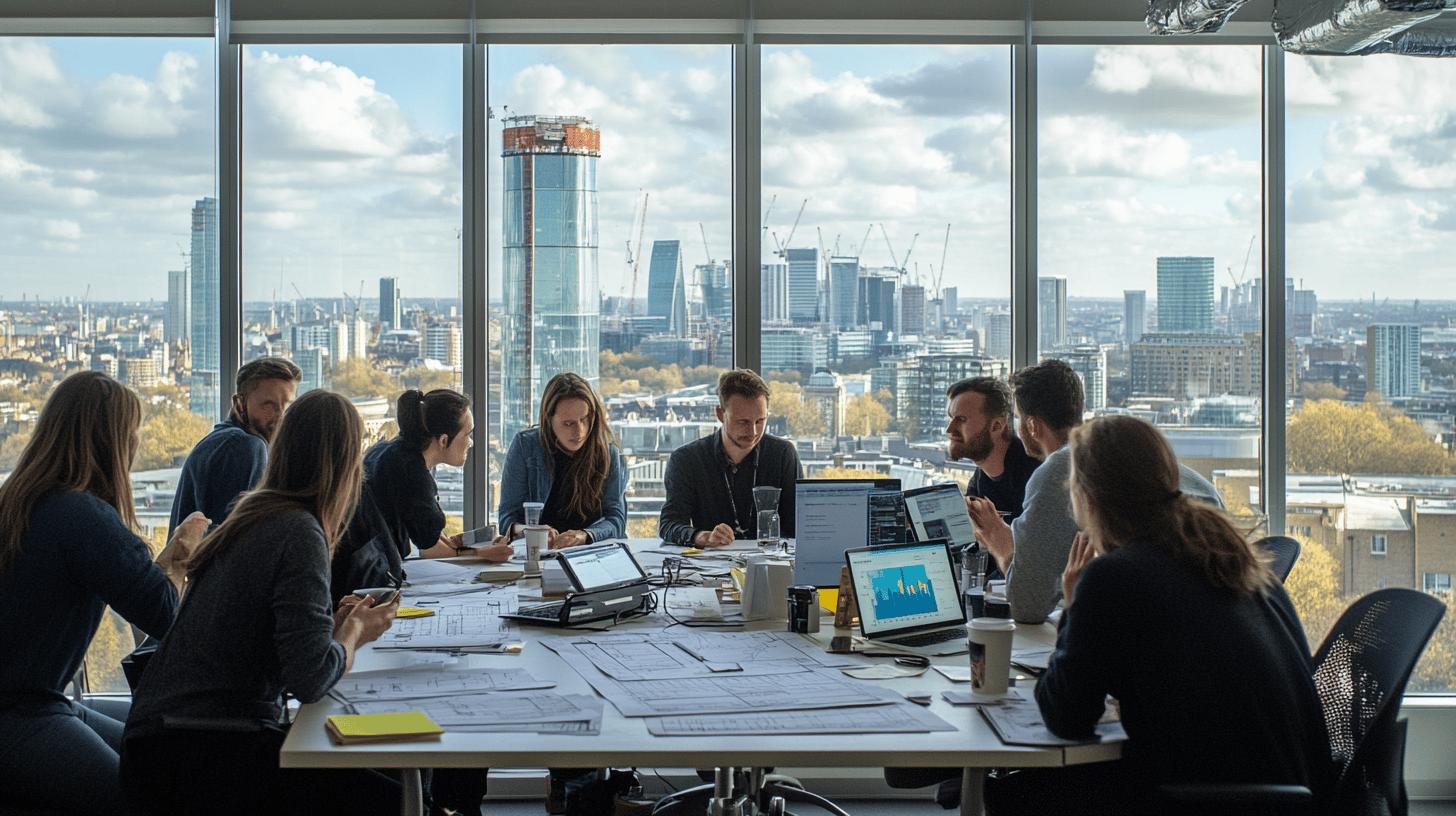
Predictive maintenance represents a quantum leap in engineering risk management. By leveraging IoT sensors and AI analytics, these systems identify potential failures before they occur, transforming maintenance from reactive to proactive. This approach delivers significant advantages: reduced downtime, extended equipment lifespan, and enhanced safety standards.
The impact is particularly profound in high-stakes industries. BMC Analysis struggled with manual asset management until implementing Q-Hub's Asset Hub. The automated calibration and maintenance schedules ensured nothing fell through the cracks, dramatically improving operational accuracy and compliance.
- Cost reductions through prevention rather than repair
- Enhanced safety through continuous system monitoring
- Improved equipment reliability and operational continuity
- Optimised maintenance scheduling based on actual conditions
Implementation Success Stories: Real-World Evidence
Anglia Cathodic Protection Services showcases the transformative power of automation in engineering risk management. Facing challenges with fragmented paper-based systems, they turned to Q-Hub to unify their compliance processes. The platform digitised their quality management workflows, streamlined non-conformance tracking, and enhanced team accountability.
Similarly, Rocal Insulating Panels revolutionised their safety management by migrating from cluttered document systems to Q-Hub's centralised platform. This transformation simplified accident reporting, improved visibility across departments, and created actionable insights through integrated dashboards.
These case studies demonstrate how custom automation tools deliver measurable improvements in engineering operations:
Key Performance Improvements
• 40% reduction in compliance review time
• 25-30% decrease in project delays
• Significant improvement in first-time-right performance
• Enhanced visibility across multi-site operations
Best Practices: Implementing Automation for Maximum Impact
Successful implementation of custom automation tools requires strategic alignment with organisational objectives. It's not merely about adopting technology—it's about solving specific challenges and optimising workflows. Q-Hub's approach focuses on understanding unique engineering needs before configuring solutions that address them precisely.
The most effective implementations follow a structured methodology:
- Needs Assessment: Identify specific operational challenges and inefficiencies
- Solution Design: Configure automation tools that align with engineering workflows
- Pilot Testing: Validate performance in controlled environments before full deployment
- Team Training: Ensure all stakeholders understand how to leverage the new capabilities
- Continuous Evaluation: Monitor performance and refine processes for optimal results
Cross-departmental collaboration is crucial throughout this process. When teams from engineering, quality, safety, and operations contribute their perspectives, the resulting solution addresses broader organisational needs while avoiding potential blind spots.
The Digital Horizon: Engineering's Automated Future
The future of engineering risk management lies in deeper integration of advanced technologies. AI, IoT, and blockchain are converging to create increasingly sophisticated automation systems that will transform how engineering operations identify and mitigate risks. By 2030, these innovations are projected to reduce risk management costs by 25% while improving response times by 40%.
Q-Hub continues to pioneer these advancements, developing solutions that help engineering organisations navigate complex compliance requirements while optimising operational efficiency. Their platform's modular architecture allows companies to start with critical needs and expand capabilities as they grow.
The digital transformation journey in engineering risk management isn't just about technology adoption—it's about creating resilient, responsive operations that can thrive in increasingly complex environments. With custom automation tools from specialists like Q-Hub, organisations can turn compliance challenges into opportunities for operational excellence.