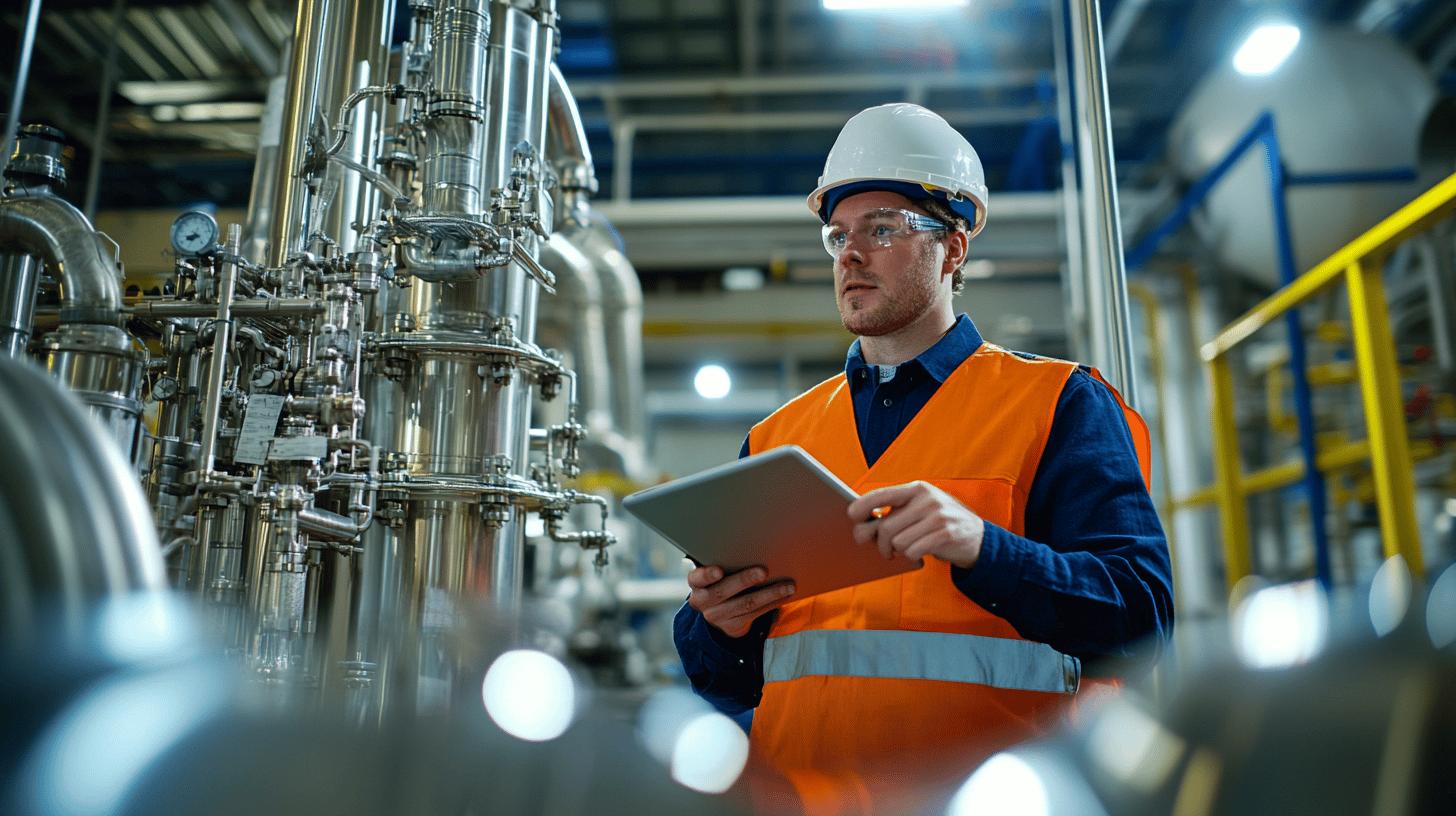
Custom Automation Tools Streamlining Food Manufacturing Workflows
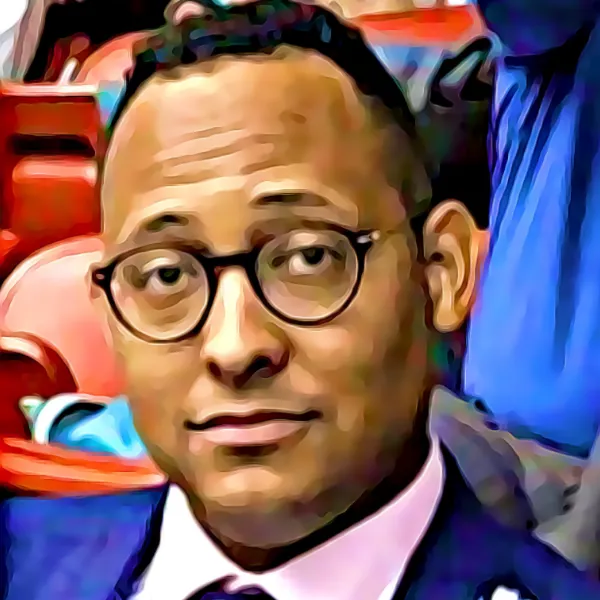
How Custom Automation Tools Optimise Incident Reporting in Food Manufacturing
Custom automation tools are revolutionising incident reporting in food manufacturing by streamlining essential processes that were once manual and error-prone.
With the implementation of custom automation tools, manufacturers can not only optimize incident logging but also enhance overall operational efficiencies. This integration paves the way for a digital transformation in the food manufacturing industry, ensuring quick responses and improved safety compliance. These tailored digital solutions automatically handle logging, categorising, and prioritising incidents—eliminating bottlenecks that traditionally plague food safety management. For manufacturers still relying on paper-based systems or outdated software, the consequences can be severe: missed reporting deadlines, compliance failures, and increased safety risks.
When incidents occur on the production floor, automated systems instantly capture critical data, assign severity levels, and alert relevant team members. This real-time response capability significantly reduces resolution time while maintaining comprehensive documentation. The difference becomes particularly apparent during regulatory audits, where organised digital records replace frantic searches through paper files.
When we implemented Q-Hub's custom automation system, our incident response time decreased by 40% within the first quarter. The structured workflow ensures nothing falls through the cracks, even during our busiest production periods.
The Hidden Power Behind Modern Food Safety Management
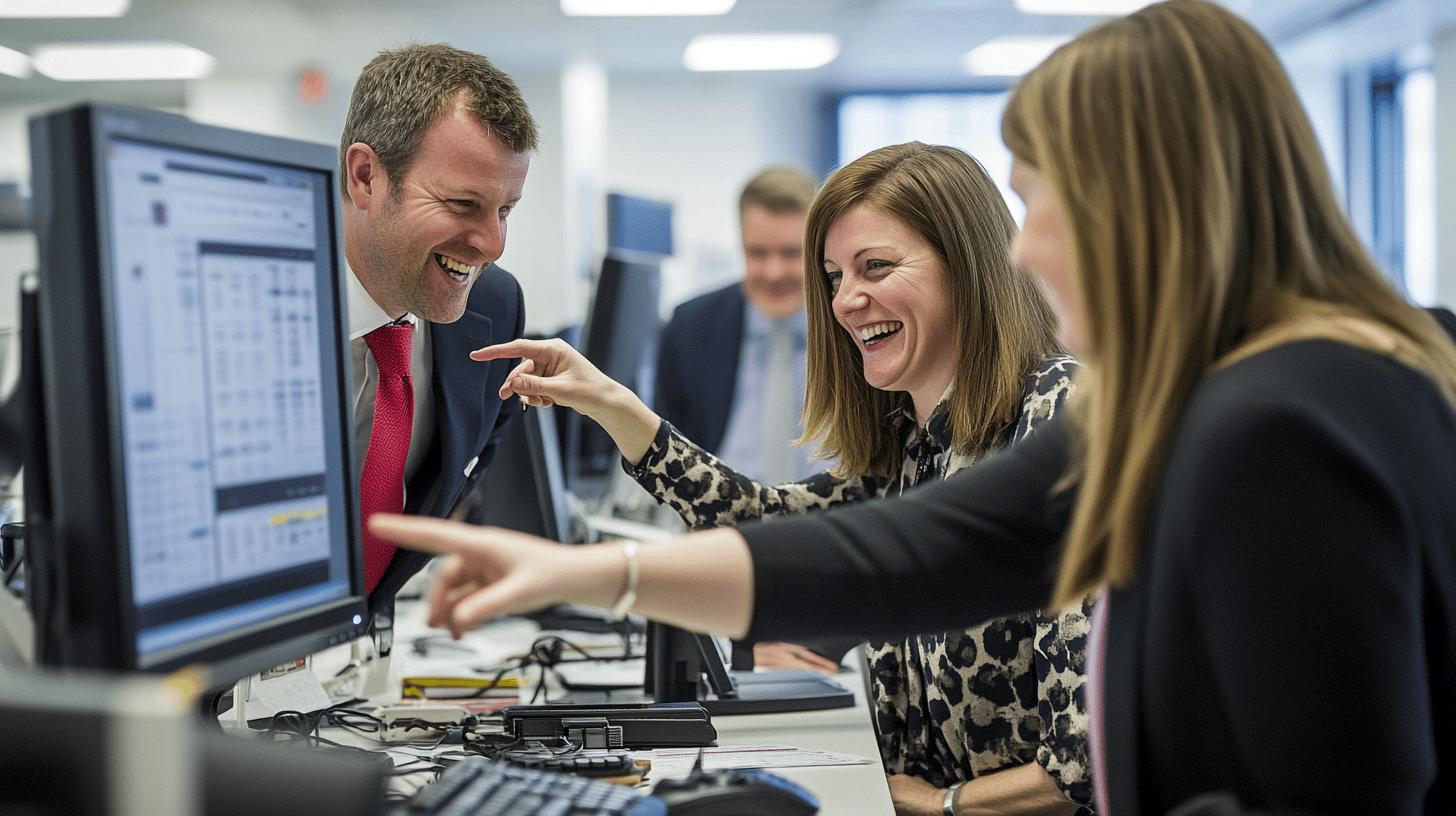
Custom automation tools—whether called digital workflow platforms or tailored incident management solutions—deliver remarkable efficiency improvements while maintaining regulatory compliance. The UK's RIDDOR 2013 regulations, for example, demand precise documentation and timely reporting of workplace incidents, which automated systems handle with ease.
These platforms eliminate repetitive tasks that once consumed valuable staff time. Rather than manually logging every detail of equipment failures or contamination risks, systems can auto-populate fields, categorise incidents based on predefined criteria, and maintain complete audit trails.
Cost savings materialise in multiple forms. Beyond the obvious labour efficiencies, automated systems prevent costly errors that lead to regulatory penalties or production shutdowns. When Scottish Leather Group implemented Q-Hub's solution, they transformed their compliance management across multiple ISO standards, creating a unified system that significantly reduced administrative burden.
Key Features That Drive Operational Excellence
What makes these custom automation tools truly transformative? Several standout capabilities consistently deliver value in food manufacturing environments:
- Real-time monitoring dashboards provide instant visibility into incidents as they happen, allowing immediate response rather than delayed reactions
- Automated alerts and escalations ensure critical incidents receive appropriate attention based on severity and type
- Customisable workflows that adapt to specific operational needs rather than forcing standardised processes
- Data validation mechanisms that eliminate common reporting errors and ensure complete information capture
- Integration capabilities connecting incident data with other business systems for comprehensive operational oversight
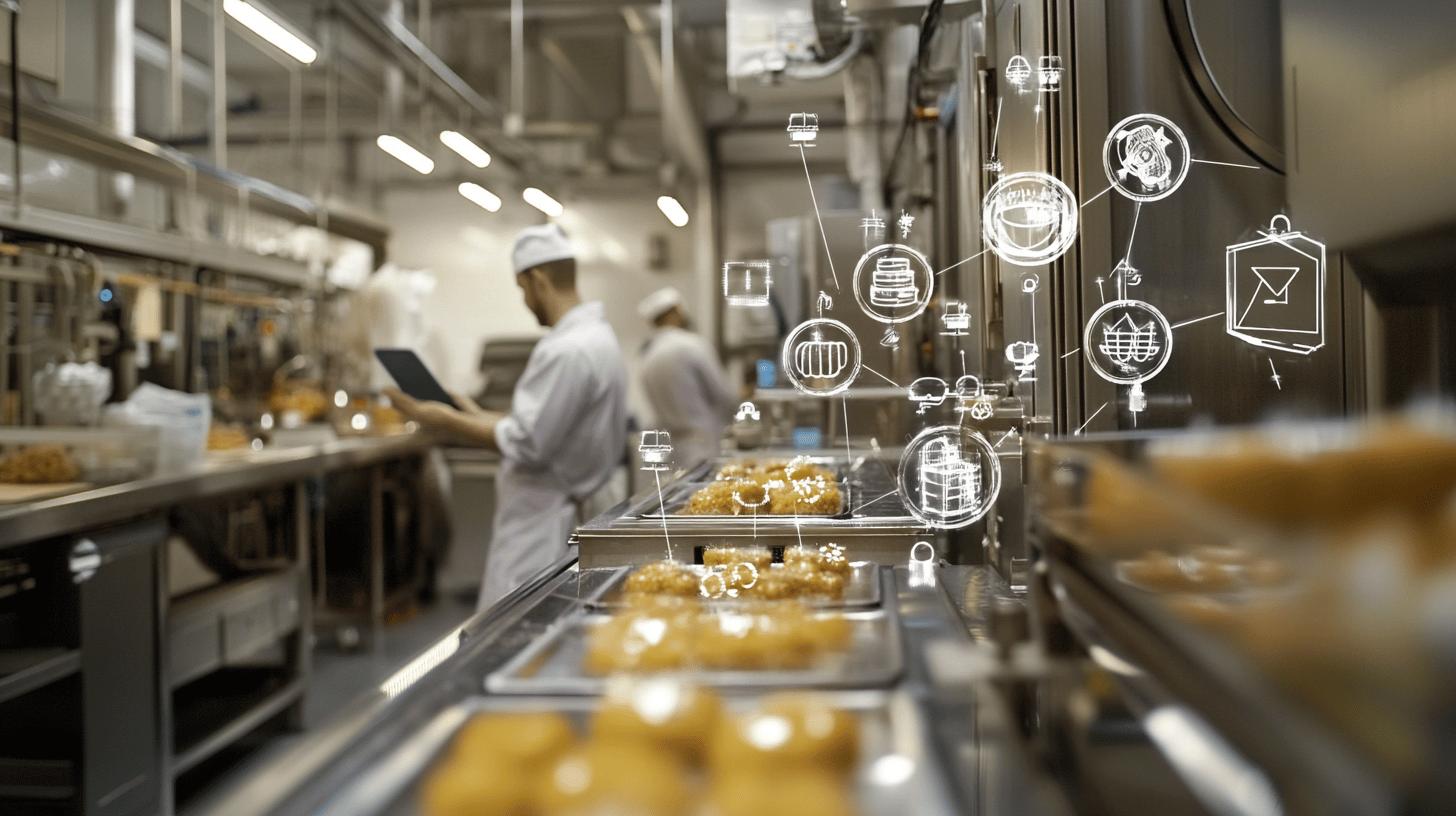
When Rocal Insulating Panels transitioned to Q-Hub's system, they experienced a remarkable transformation in their accident reporting processes. Their previous paper-based system created bottlenecks and incomplete records. The automated solution provided faster resolution times and better involvement from department managers, with real-time access to all relevant safety data.
Measurable Benefits in Real-World Applications
The practical advantages of implementing custom automation tools extend far beyond theoretical improvements. Food manufacturers consistently report concrete benefits that directly impact their bottom line and operational performance:
<table border="0"> <tr><th>Performance Metric</th><th>Before Automation</th><th>After Automation</th></tr> <tr><td>Incident resolution time</td><td>Days to weeks</td><td>Hours to days</td></tr> <tr><td>Quality-related recalls</td><td>Baseline</td><td>25% reduction</td></tr> <tr><td>Production efficiency</td><td>Baseline</td><td>15% increase</td></tr> <tr><td>Audit preparation time</td><td>Days</td><td>Hours</td></tr> </table>These improvements aren't isolated to larger manufacturers. When Anglia Cathodic Protection Services implemented Q-Hub's solutions, they successfully managed their growing workload and client base by digitising previously fragmented processes. Their system for tracking non-conformances became centralised, with improved accountability and visibility.
Why manual incident reporting fails food manufacturers
Manual incident reporting creates multiple failure points: delayed recognition of serious issues, inconsistent documentation, lost paperwork, and inability to identify recurring patterns. These gaps not only violate regulatory requirements but also prevent manufacturers from addressing systemic problems before they escalate into costly shutdowns or recalls.
Seamless Integration: Overcoming Implementation Hurdles
One of the biggest concerns for food manufacturers considering automation tools is integration with existing systems. Bespoke solutions shine here by adapting to current processes rather than forcing disruptive changes.
Legacy systems—from inventory management to quality control databases—often operate in isolation. Custom automation platforms act as connective tissue, enabling data to flow seamlessly between previously siloed operations. This interoperability eliminates duplicate data entry and provides a complete operational picture.
For growing companies, scalability is another crucial consideration. Unlike rigid off-the-shelf software, custom solutions evolve with changing needs. Food manufacturers can start with basic incident reporting functionality and progressively add capabilities like advanced analytics or supplier management as operations expand.
The Future: AI-Powered Predictive Safety
The most exciting developments in food safety automation leverage artificial intelligence and machine learning to move beyond reactive reporting to predictive risk management. These technologies analyse historical incident data to identify patterns that human observers might miss.
For example, AI algorithms might detect that a particular combination of temperature fluctuations, humidity levels, and production speed consistently precedes quality failures. The system could then automatically flag these conditions before contamination occurs.
Integration with IoT sensors further enhances these capabilities. Temperature monitors, vibration sensors, and quality inspection cameras feed real-time data into machine learning models, enabling continuous monitoring without human intervention.
BMC Analysis experienced this transformation when they implemented Q-Hub's platform. Their previously manual systems for tracking non-conformances and managing assets became fully digital, with automated reminders ensuring nothing was overlooked. Their audit processes also improved dramatically with centralised findings and observations.
Making the Transition: Strategic Implementation Approaches
Successful implementation of automation tools requires thoughtful planning and execution. Based on Q-Hub's experience with food manufacturers, these strategies consistently yield positive results:
- Begin with a comprehensive audit of existing workflows to identify high-impact automation opportunities
- Implement solutions in phases, starting with the most critical processes
- Ensure thorough training and support during the transition period
- Establish clear metrics to measure success and ROI
- Create feedback mechanisms to continuously refine and improve the system
Weston Aerospace followed this approach when implementing Q-Hub's platform. Their transformation included digitising NCR management and calibration tracking, which significantly reduced administrative burden while improving compliance. The phased approach ensured minimal disruption to ongoing operations.
Custom automation tools are transforming food manufacturing by streamlining incident reporting and enhancing safety compliance.
Leveraging custom automation tools food sector compliance solutions further strengthens the operational framework, addressing food safety challenges while ensuring conformity to regulatory standards. This strategic enhancement not only reduces the risk of compliance breaches but also supports a culture of proactive quality control within the modern food manufacturing landscape. Q-Hub's specialised solutions help manufacturers eliminate manual inefficiencies while providing real-time visibility into critical processes. As AI and predictive analytics capabilities advance, these systems will continue to evolve—not just documenting incidents but preventing them entirely. Ready to transform your incident reporting workflows? Discover how Q-Hub's tailored automation solutions can enhance your food safety management while driving operational excellence.