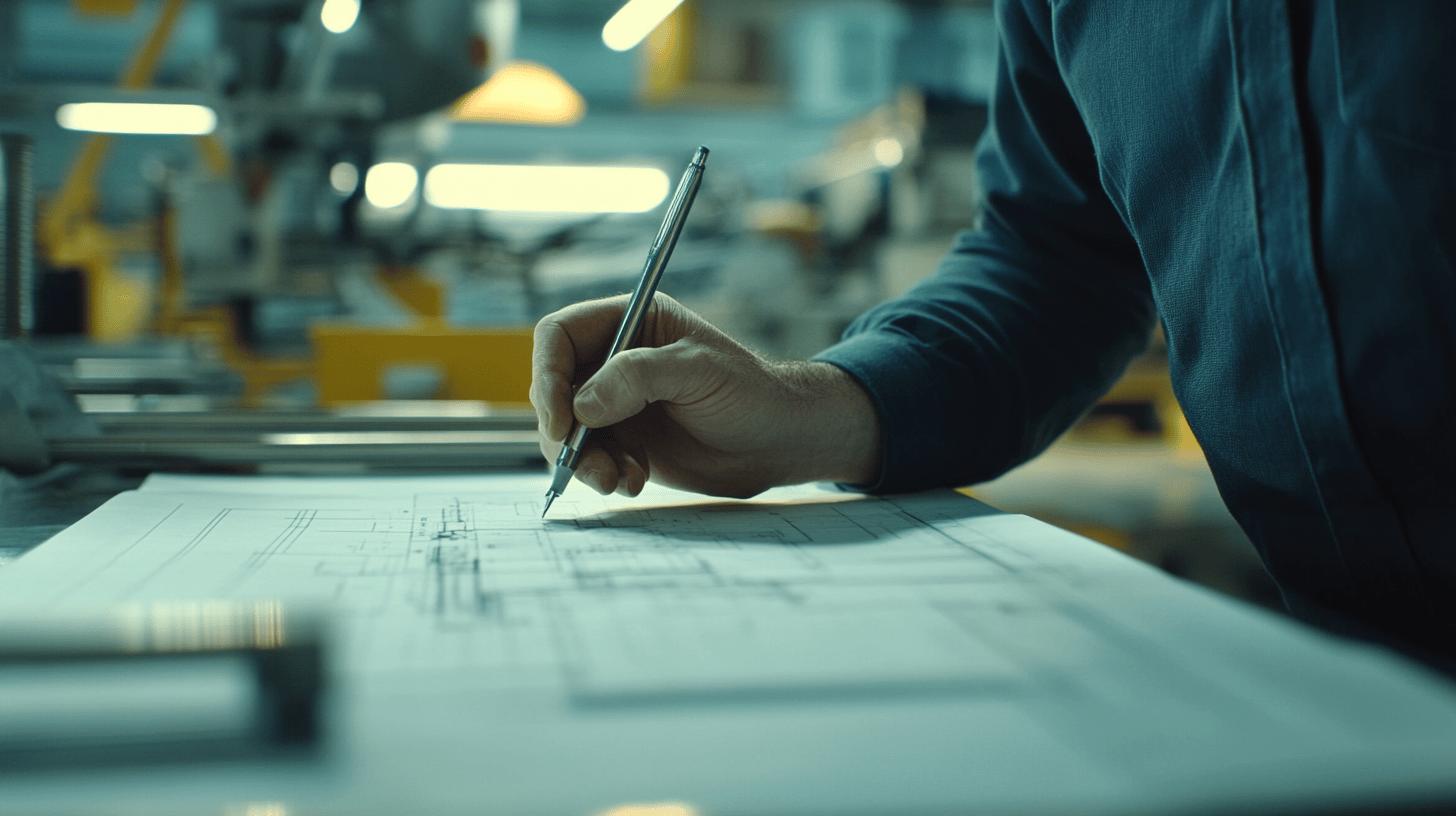
Custom Automation Tools Revolutionise Engineering Quality Control
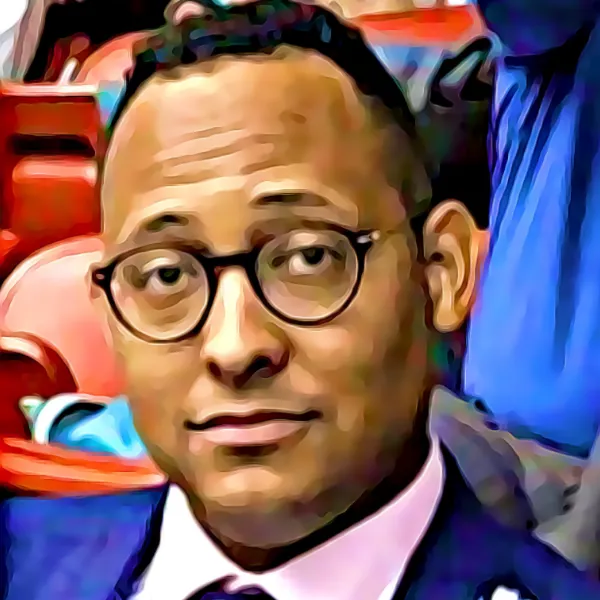
The Role of Custom Automation Tools in Automating Quality Control Tasks in Engineering Operations
Custom automation tools have revolutionised quality control in engineering operations, transforming manual, error-prone processes into streamlined, precise workflows. These tailored solutions automate repetitive tasks, significantly reducing human error while enhancing both accuracy and efficiency. Unlike traditional methods relying on manual inspection, modern automated systems provide real-time monitoring and immediate adjustments, detecting subtle defects that human inspectors might miss in sectors ranging from aerospace to automotive manufacturing.
By implementing these tools, companies achieve consistent product standards across production lines while gaining remarkable scalability.
Discover how custom automation tools are paving the way for innovative quality control methods in engineering. These advanced solutions integrate seamlessly into legacy systems, much like a master craftsman refining traditional techniques with modern precision, ensuring consistent output and heightened productivity.
The real-time analysis capabilities enable immediate corrective actions, preventing costly defects from progressing through the production cycle.Enhance your operations by exploring how integration with ERP systems complements these automation technologies, merging data from various processes to streamline decision-making and improve overall engineering quality. Just as a well-oiled machine harmonises different components, ERP integration brings a cohesive approach to managing production and quality control standards.
Q-Hub's digital transformation solutions help engineering operations leverage these technologies to streamline quality assurance while reducing operational costs.The shift from manual quality control to automated systems has reduced defect rates by up to 50% while improving overall product quality by 25-40% across engineering sectors.
Revolutionary Vision Systems Transforming Defect Detection
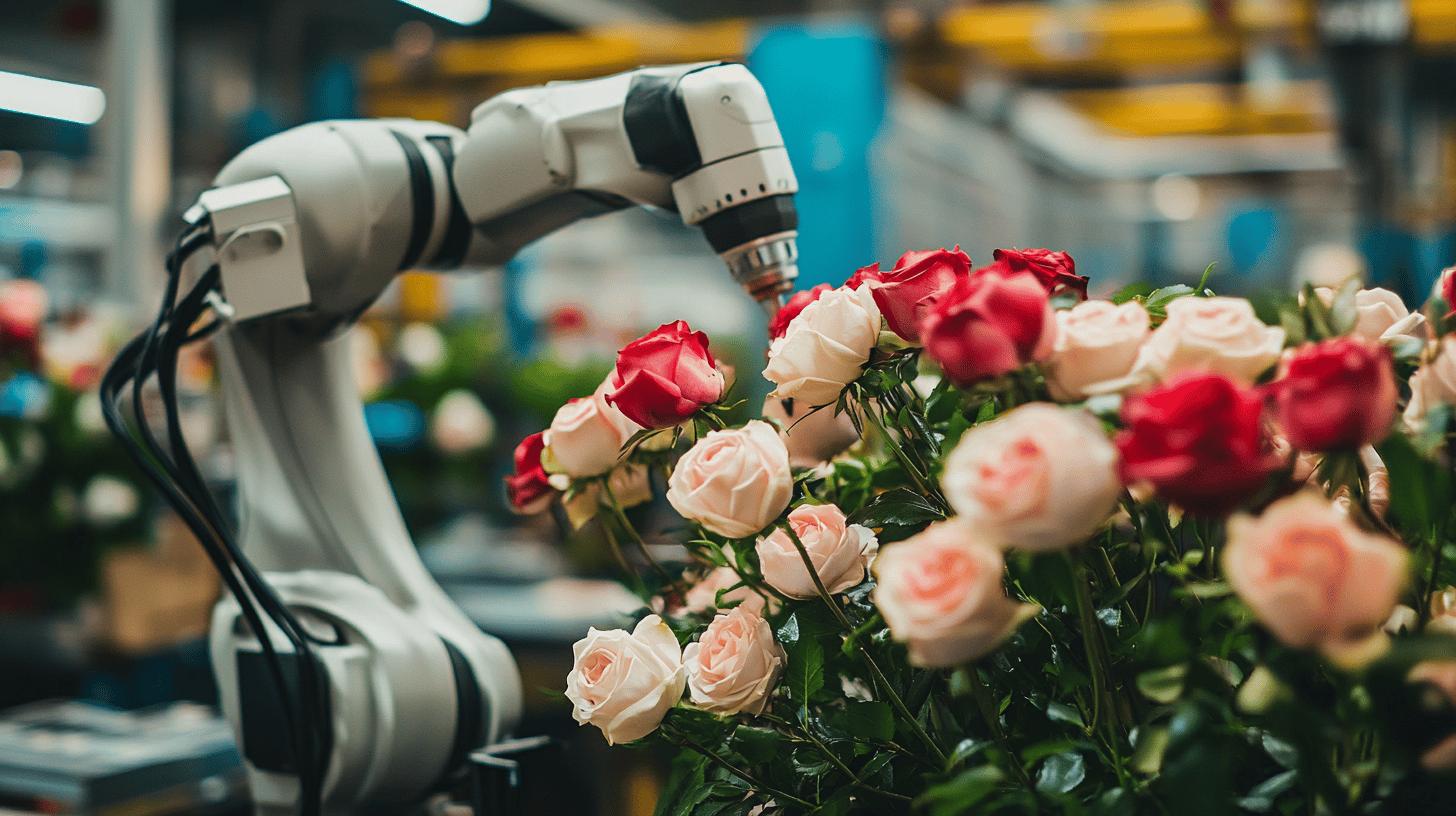
Vision-based inspection systems represent the cutting edge of quality control automation. Using high-resolution cameras and sophisticated algorithms, these systems can identify micro-cracks, surface irregularities, and dimensional anomalies invisible to the human eye. In automotive manufacturing, these systems scan critical engine components with unmatched precision.
The impact is immediate: faster inspections, significantly reduced error rates, and consistent quality standards. For example, Weston Aerospace implemented automated inspection systems that transformed their quality assurance process, enabling real-time defect detection that traditional methods simply couldn't match.
How Collaborative Robotics Creates Perfect Harmony Between Human and Machine
Collaborative robots (cobots) are redefining quality control by complementing human capabilities rather than replacing them. These flexible systems handle repetitive precision tasks like dimensional verification and component sorting with remarkable accuracy and consistency.
Unlike conventional automation, cobots adapt to changing production requirements, working alongside human operators in a symbiotic relationship. This flexibility makes them particularly valuable for engineering operations transitioning from manual processes to automated workflows, creating a bridge between traditional methods and fully automated systems.
The Predictive Revolution: Stopping Defects Before They Happen
AI-powered predictive analytics represents perhaps the most significant advance in quality control automation. Rather than simply identifying existing defects, these systems forecast potential issues before they materialise, allowing engineers to take preventive action.
In aerospace manufacturing, where component failure can have catastrophic consequences, predictive systems identify performance anomalies long before they become critical issues. This proactive approach dramatically reduces downtime, minimises waste, and ensures compliance with stringent safety regulations.
Here's how these technologies compare in practical applications:
<table border="0"> <tr><th>Metric</th><th>Before Automation</th><th>After Automation</th></tr> <tr><td>Defect Detection Rate</td><td>60-75%</td><td>95-99%</td></tr> <tr><td>Inspection Time</td><td>Hours</td><td>Minutes</td></tr> <tr><td>Quality Consistency</td><td>Variable</td><td>Highly Consistent</td></tr> <tr><td>Compliance Management</td><td>Manual Tracking</td><td>Automated Verification</td></tr> </table>Unlocking Success: Best Practices for Implementing Custom Automation
The journey to successful automation begins with precisely identifying operational pain points. Before implementing any solution, engineering teams must pinpoint exactly where quality issues arise. Is it dimensional accuracy? Surface finish? Material consistency? Without this clarity, even sophisticated automation tools will fail to deliver optimal results.
Cross-functional collaboration forms the backbone of effective implementation. Quality control doesn't exist in isolation—it intersects with design, production, IT, and procurement. By bringing these perspectives together, companies ensure their automation solutions address the full spectrum of requirements and constraints.
Companies implementing custom automation should follow these steps for success:
- Conduct a comprehensive needs analysis identifying specific quality pain points
- Design solutions with cross-functional input from all stakeholders
- Test rigorously under actual production conditions
- Integrate seamlessly with existing systems
- Provide thorough training for all personnel
Real-World Transformation Through Intelligent Automation
The impact of custom automation tools extends beyond theoretical benefits, delivering measurable improvements across various engineering sectors. For instance, Scottish Leather Group revolutionised their quality management by implementing Q-Hub's digital platform, which streamlined their compliance processes across multiple ISO standards while significantly reducing audit preparation time.
Similarly, Fowlers of Bristol transformed their document control and quality verification processes through Q-Hub's automation tools. Their pursuit of "Zero Defects" became more achievable with automated tracking of key performance indicators and streamlined issue resolution workflows, demonstrating how custom solutions drive real-world quality improvements.
Weston Aerospace provides another compelling example. By implementing custom automation tools for quality control, they overcame challenges with legacy systems that were creating compliance bottlenecks. Their new automated quality management system delivered immediate improvements in audit efficiency and defect detection while freeing staff to focus on strategic initiatives rather than administrative tasks.
The Future Landscape: Where Quality Automation Is Heading
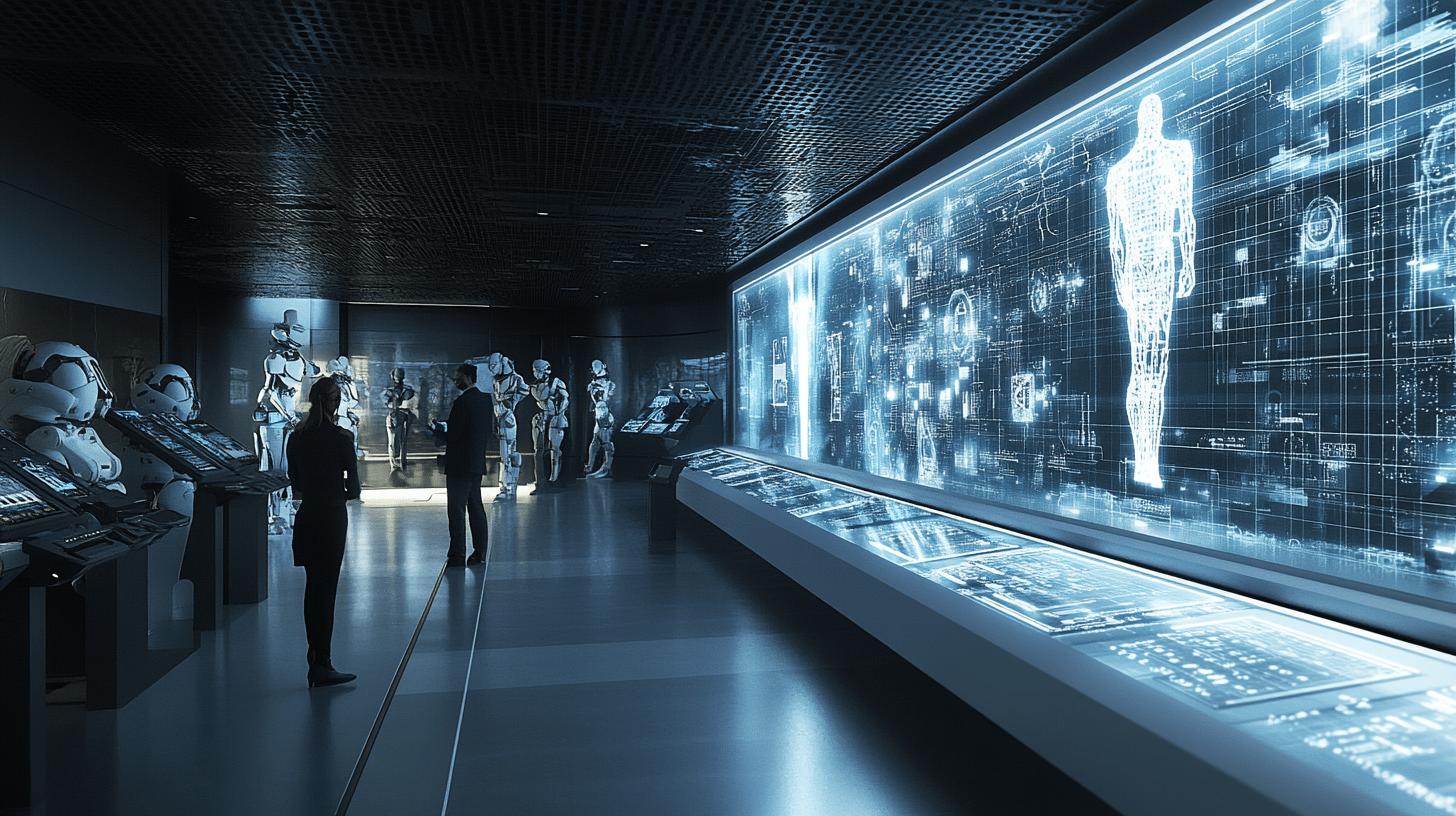
The convergence of AI and IoT is creating unprecedented opportunities in quality control automation. Connected sensors across production environments feed continuous data streams to AI systems that not only detect anomalies but learn and adapt over time, creating increasingly accurate quality predictions with minimal human intervention.
Human-centric design principles are reshaping how these systems interact with their users. Modern automation tools feature intuitive interfaces and contextual guidance that complement human decision-making rather than obscuring it. This approach recognises that even the most advanced automation requires human oversight and expertise to deliver maximum value.
Looking ahead, we can expect these emerging trends in quality control automation:
- Self-optimising AI systems that continuously refine quality parameters
- Edge computing enabling real-time quality decisions at the production point
- Augmented reality interfaces for enhanced human-machine collaboration
- Carbon-neutral automation solutions supporting sustainability goals
- Blockchain integration for immutable quality verification records
As engineering operations continue evolving, Q-Hub remains at the forefront of custom automation solutions that drive quality excellence. By combining deep industry expertise with innovative digital tools, we enable businesses to transform their quality management processes while reducing costs and improving operational efficiency. Ready to revolutionise your quality control operations? Discover how Q-Hub's tailored automation solutions can help you achieve unprecedented precision and productivity.