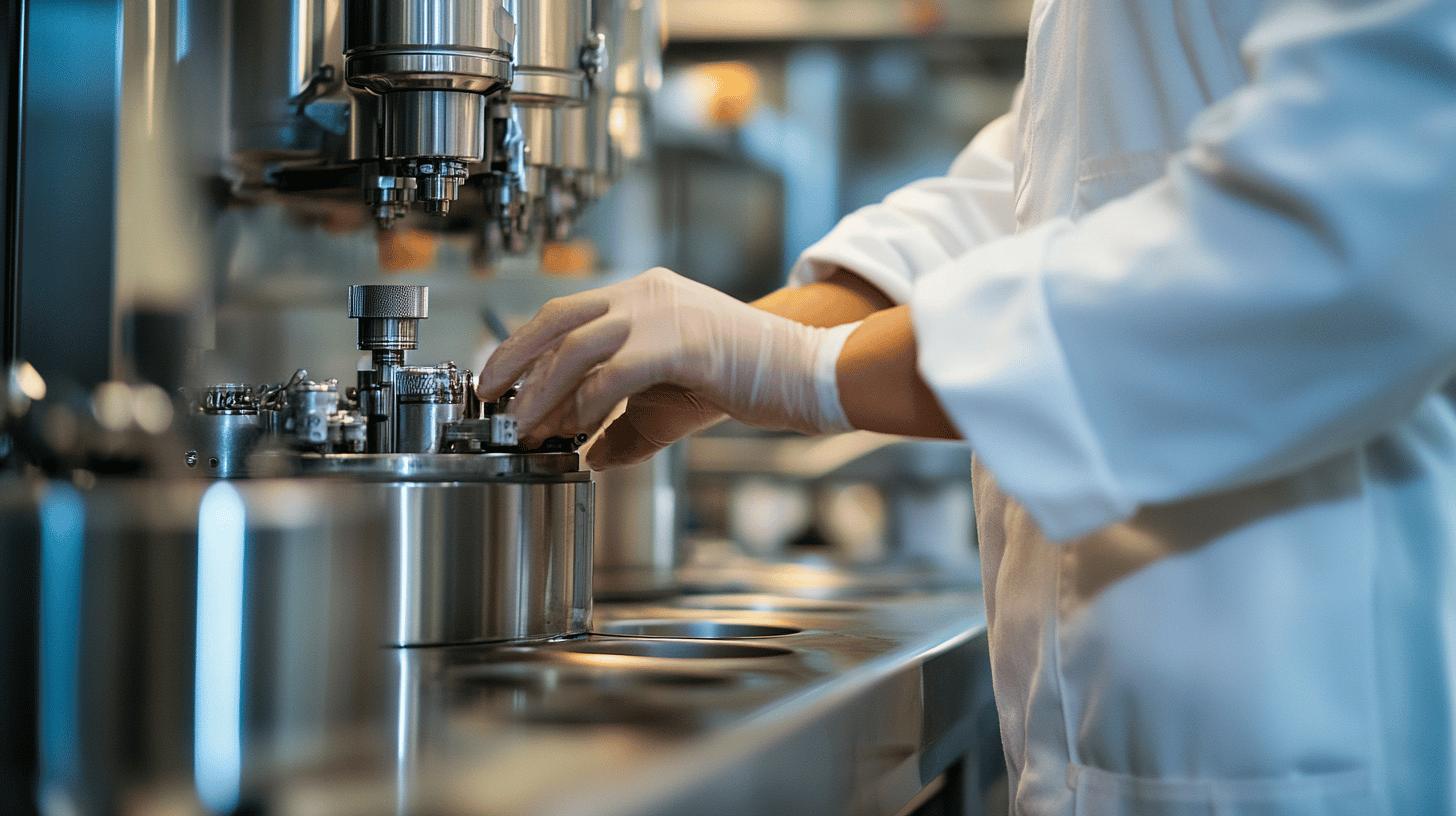
Custom Automation Tools: Elevating Food Production Workflows
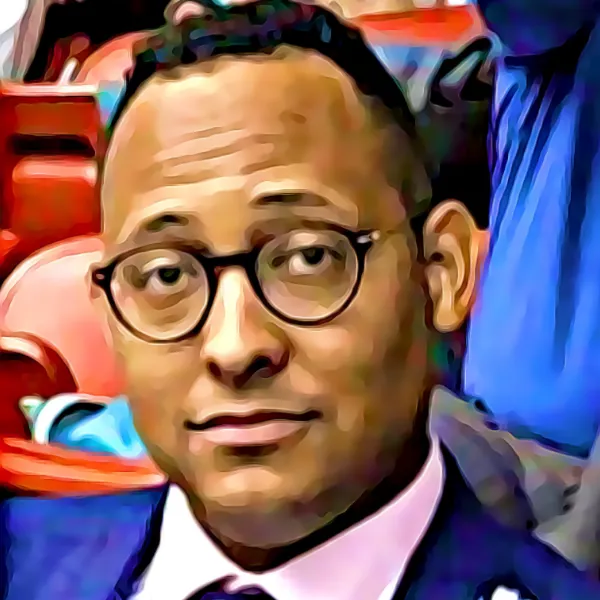
The Role of Custom Automation Tools in Refining Engineering Management Workflows for Food Production
Custom automation tools have revolutionised engineering management in food production, transforming traditional processes into streamlined, error-resistant workflows. These bespoke systems tackle the precision and compliance demands unique to food manufacturing, where even minor deviations can impact product quality and safety. Q-Hub's tailored digital solutions specifically address these challenges by automating repetitive tasks and creating interconnected systems that eliminate information silos. For food producers struggling with inefficient legacy processes, these tools aren't merely helpful—they're essential for maintaining competitive edge.
When implemented correctly, custom automation tools can reduce waste by up to 25% and improve production speeds by 20% in food manufacturing facilities.
The regulatory landscape in food production is particularly demanding, requiring consistent compliance with ever-evolving standards. Manual oversight often proves inadequate for maintaining this precision across thousands of daily operations. Automated systems excel at maintaining this consistency through real-time monitoring and instant alerts that human teams simply cannot match in speed or accuracy.
Transforming Production Through Intelligent Automation
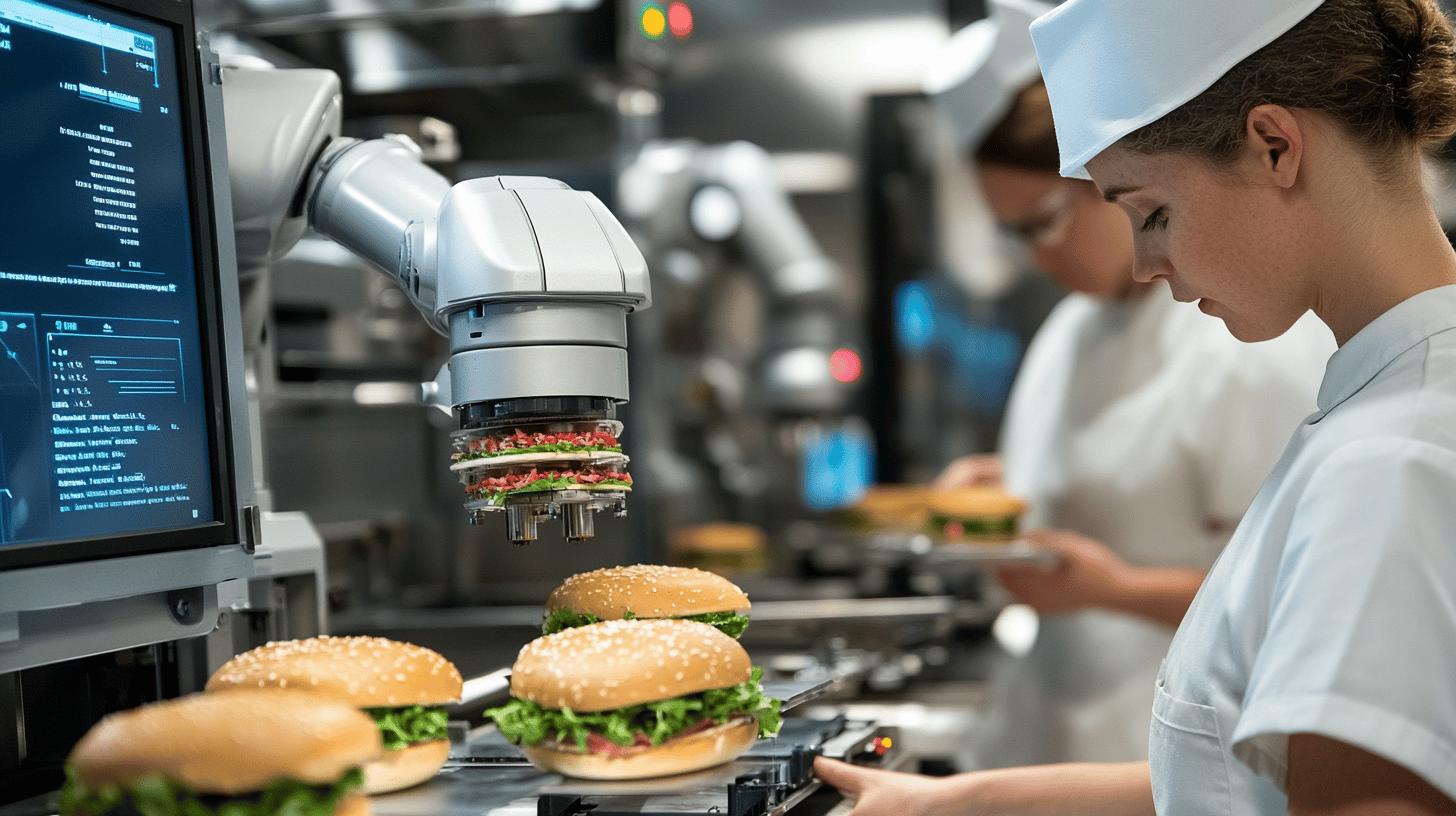
One of the most significant advantages of custom automation in food production is the elimination of workflow bottlenecks. Traditional production environments often suffer from communication gaps between departments, creating delays and errors during critical handoffs. Q-Hub's automation solutions bridge these gaps by creating a centralised platform where information flows seamlessly between teams.
Think about what happens when production data must pass between quality control, manufacturing, and packaging teams. Without automation, this often involves manual data transfer, paper records, and time-consuming communication. Custom tools establish digital pathways that ensure each department automatically receives the exact information they need, precisely when they need it.
For instance, when a dairy plant implemented Q-Hub's automated workflow solutions, they discovered temperature fluctuations in pasteurisation were being detected and corrected within minutes rather than hours. This improvement not only prevented potential product loss but also ensured consistent quality across batches—a critical factor in consumer brand loyalty.
Key Operational Benefits That Drive ROI
Food producers implementing custom automation tools typically experience multiple operational improvements that directly impact their bottom line. These systems do far more than simply digitise existing processes—they fundamentally transform operations.
Companies embracing these innovations typically experience the following benefits:
- Real-time production monitoring that catches quality issues before they affect entire batches
- Predictive maintenance systems that prevent costly unplanned downtime
- Automated compliance reporting that reduces regulatory documentation burden
- Inventory optimization that prevents shortages while minimizing excess stock
- Labour reallocation from repetitive tasks to higher-value activities
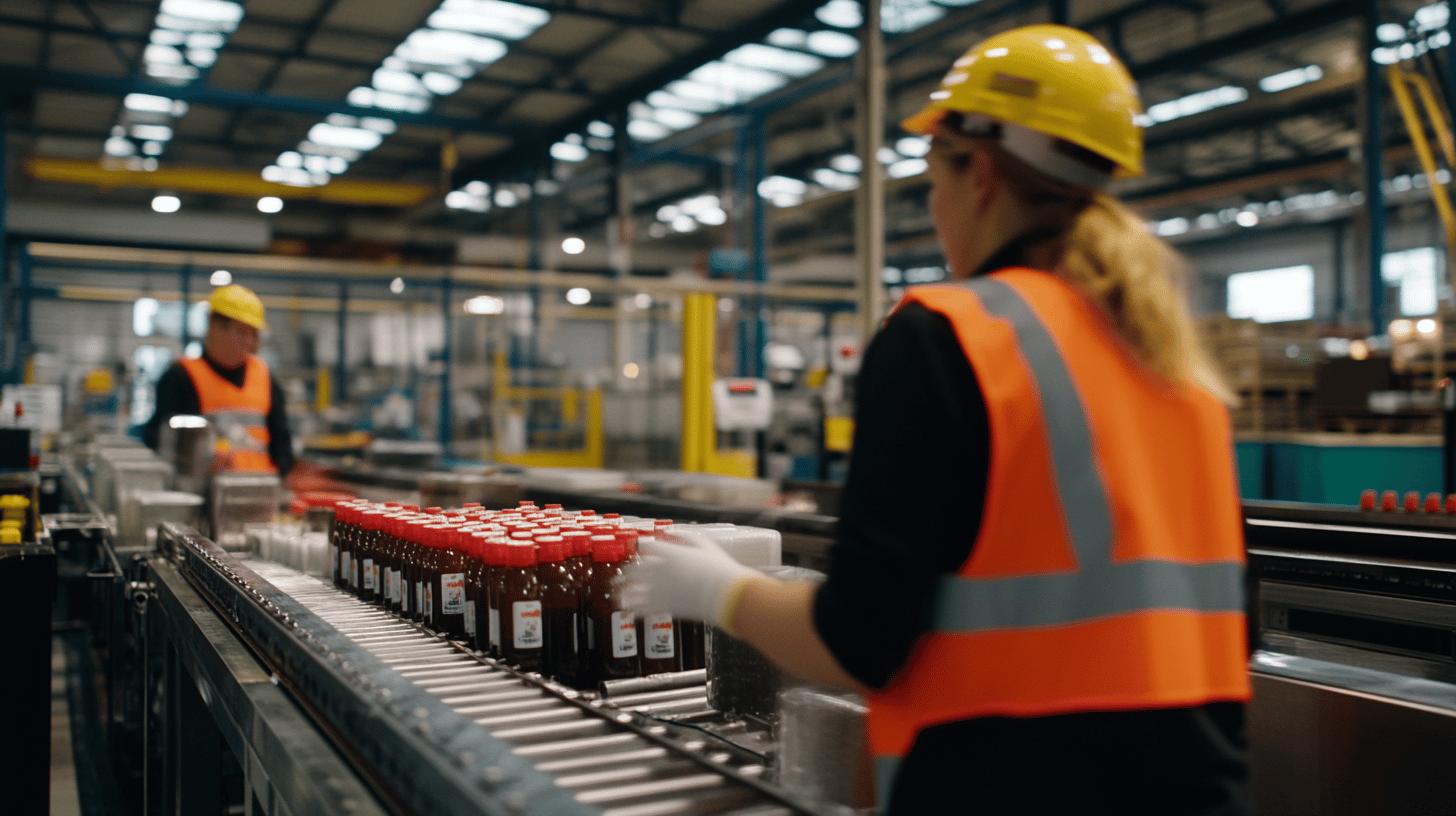
The Scottish Leather Group experienced these benefits firsthand after implementing Q-Hub's automation platform. By digitising their compliance processes across ISO standards, they significantly reduced the administrative burden while improving consistency. What previously took days of preparation now required just hours, freeing their quality team to focus on process improvements rather than paperwork.
Implementation Strategies: From Assessment to Execution
Successfully implementing custom automation tools requires a structured approach that begins well before any technology is deployed. The most successful implementations follow a clear methodology that prioritises understanding existing workflows before attempting to automate them.
The process typically begins with a comprehensive workflow assessment to identify inefficiencies, redundancies, and bottlenecks. This critical first step revealed that Anglia Cathodic Protection Services was struggling with fragmented paper and spreadsheet-based systems that couldn't scale with their growing workload. By identifying these pain points early, Q-Hub could develop targeted solutions for their specific challenges.
Once core issues are identified, the selection phase begins. The right tools should address your specific production requirements rather than forcing your operation to adapt to generic software. For example, a bakery might prioritise batch scheduling automation, while a dairy producer might focus on temperature monitoring tools.
Testing on a smaller scale before full deployment is essential. Rocal Insulating Panels took this approach when implementing Q-Hub's safety management system, running pilot programs that allowed them to refine the system before company-wide rollout. This measured approach minimized disruption while maximizing adoption.
Cost vs. Value: The Investment Perspective
While the initial investment in custom automation tools can seem substantial, understanding the complete financial picture requires looking beyond upfront costs. The most successful implementations deliver ROI through multiple streams of operational improvements.
Operational Area | Before Automation | After Automation |
---|---|---|
Quality Control Time | 4-6 hours daily | 30-60 minutes daily |
Compliance Documentation | 2-3 days per audit | 2-3 hours per audit |
Unplanned Downtime | 8-12% of production time | 2-3% of production time |
Error Rate in Production | 3-5% waste | 0.5-1% waste |
Initial investments typically include software licensing (£20,000-£50,000), hardware components (£30,000-£100,000), and staff training (£10,000-£25,000). However, these costs are offset by substantial operational savings within the first 12-24 months for most implementations.
BMC Analysis found that after implementing Q-Hub's solutions, they eliminated hours of manual documentation work while improving their compliance posture. Their staff could reallocate time previously spent on administrative tasks to process improvement initiatives that further enhanced productivity.
Building Systems That Grow With Your Business
One of the most valuable aspects of custom automation tools is their ability to evolve alongside your business. Unlike rigid off-the-shelf solutions, bespoke systems can be adapted as production requirements change and new challenges emerge.
Customisation capabilities that prove particularly valuable include:
- API integration with existing ERP and inventory management systems
- Configurable dashboards that can be tailored to different departmental needs
- Customisable reporting templates that meet specific regulatory requirements
- Scalable architecture that accommodates production growth
- Modular design that allows for phased implementation
Fowlers of Bristol leveraged these customisation capabilities when implementing Q-Hub's document control tools. By tailoring the system to their specific workflow requirements, they created a solution that not only addressed current challenges but could also adapt to their future growth plans.
The Future of Food Production Automation
As we look toward the future, emerging technologies are set to further transform food production workflows. AI and machine learning are already enhancing quality control systems, enabling visual inspection algorithms to detect product defects with greater accuracy than human inspectors.
IoT sensors integrated throughout production facilities are creating unprecedented visibility into operations. These connected devices monitor everything from equipment performance to environmental conditions, generating valuable data that feeds into predictive maintenance systems and quality control processes.
The concept of the "digital twin"—a virtual replica of physical production processes—is gaining traction in advanced food manufacturing. These simulations allow production engineers to test process changes virtually before implementing them on the production floor, reducing risk and optimizing outcomes.
Q-Hub continues to integrate these emerging technologies into our custom automation solutions, helping food producers not only solve today's challenges but prepare for tomorrow's opportunities. By partnering with industry leaders, we develop systems that enhance operational efficiency while maintaining the agility needed in today's rapidly evolving marketplace.
For food producers ready to transform their engineering management workflows, custom automation tools offer a clear path forward. With Q-Hub's tailored digital solutions, businesses can achieve the precision, compliance, and efficiency needed to thrive in this demanding industry.
<