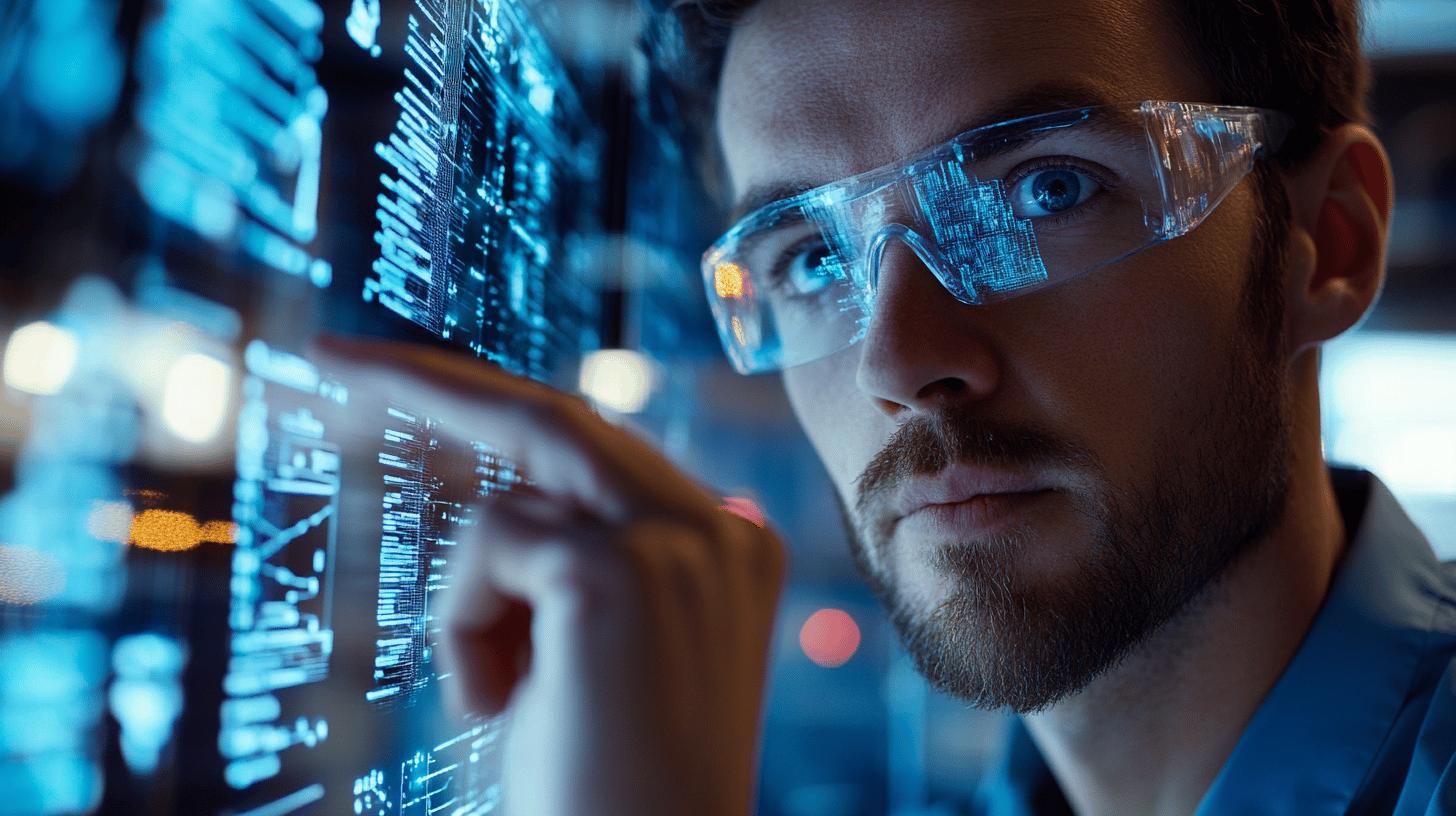
Continuous Improvement Programmes Boost Facility Traceability
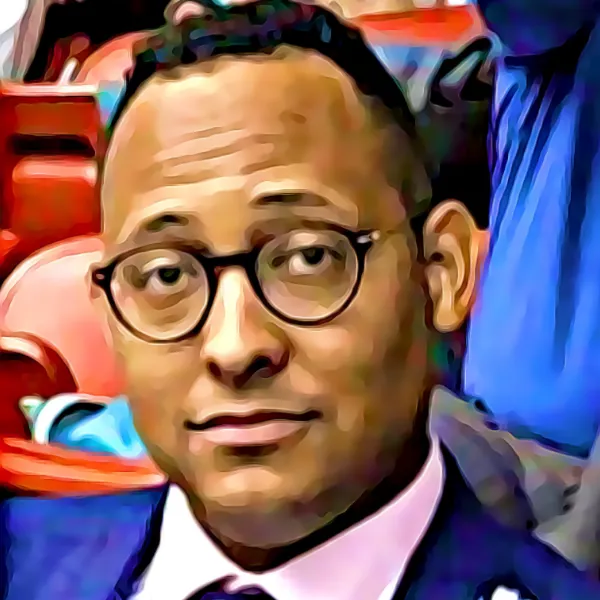
How Continuous Improvement Programmes Support Traceability in Facilities Supply Chains
Continuous improvement programmes like Lean and Six Sigma form the backbone of effective traceability in today's complex facilities supply chains. These methodologies transform fragmented processes into seamless, transparent systems where every component can be tracked with precision. Q-Hub's specialised QHSE software solutions integrate perfectly with these programmes, helping organisations establish clear data trails and eliminate redundancies that compromise traceability. Without such structured approaches, facilities management companies often struggle with visibility gaps and compliance challenges that undermine operational efficiency.
These improvement frameworks focus on end-to-end visibility—a critical requirement for effective supply chain management. Lean methodologies systematically eliminate waste, creating clearer data trails, while Six Sigma reduces process variations to ensure consistency in traceability protocols. Together, they create standardised practices that transform how information flows through your supply chain.
At its core, traceability isn't just about tracking—it's about building accountability into every step of your operational ecosystem. When implemented correctly, it becomes the foundation for both compliance and continuous improvement.
The impact on facilities management operations is substantial, with benefits that extend far beyond basic compliance:
- Enhanced Data Integrity: Standardised processes dramatically reduce collection errors, ensuring reliable traceability records
- Real-Time Visibility: Modern monitoring systems provide immediate insights into supply chain movements and status
- Simplified Compliance: Structured documentation and automated audit trails streamline regulatory adherence
- Operational Cost Reduction: Eliminating inefficiencies and redundancies delivers measurable savings
- Accelerated Problem Resolution: Clear data trails make identifying and addressing supply chain bottlenecks straightforward
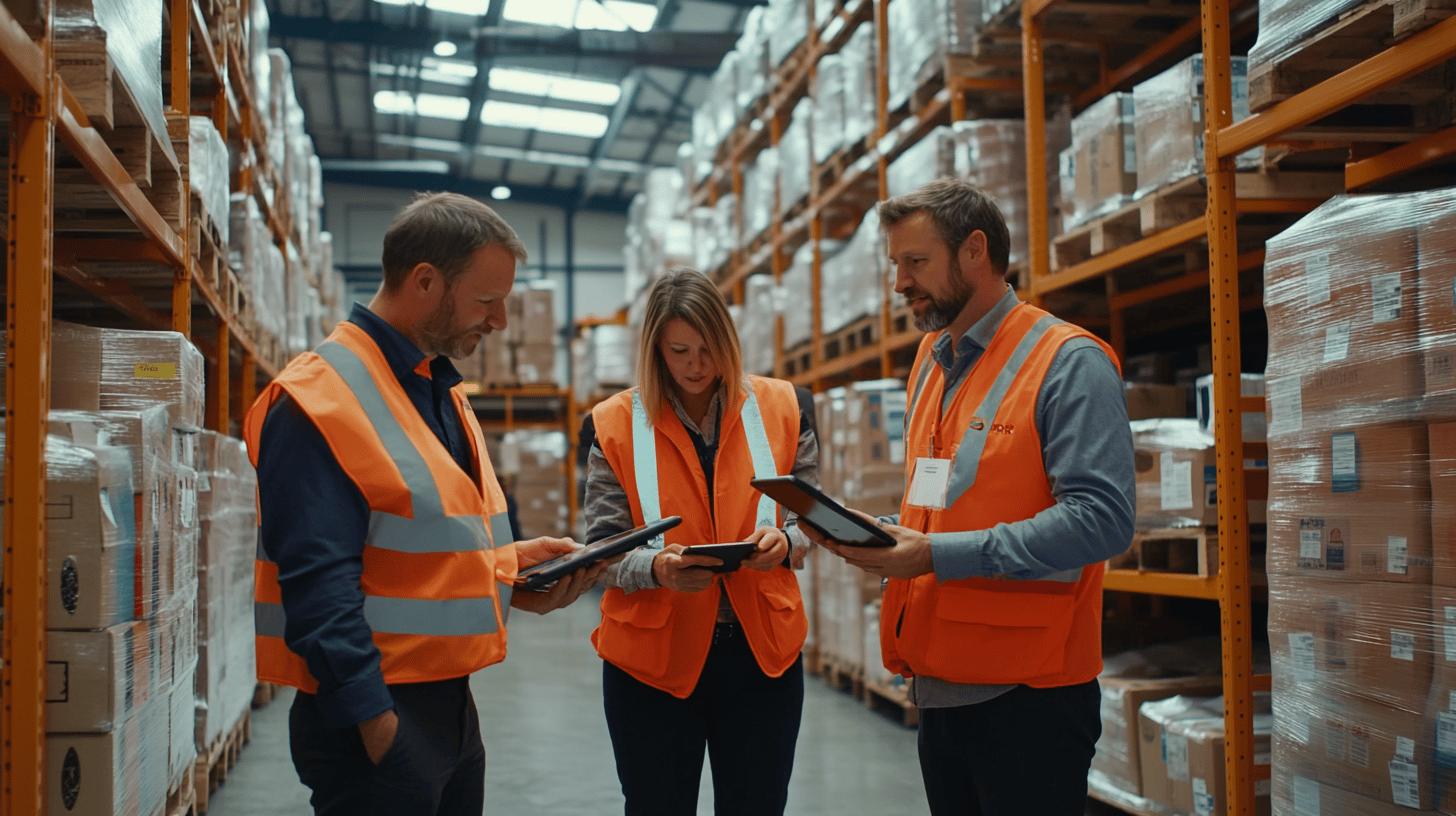
Breaking Through Traceability Barriers
The path to effective traceability isn't without challenges. Most facilities management operations face several key hurdles that continuous improvement programmes help overcome. The most persistent obstacle? Lack of standardisation across supply chain partners.
Imagine trying to trace an HVAC maintenance history when contractors, suppliers, and in-house teams all use different data formats and systems. It creates blind spots that make comprehensive tracking nearly impossible. Standardising these processes requires coordination across multiple stakeholders—precisely what continuous improvement frameworks excel at orchestrating.
Data fragmentation presents another significant challenge. When critical information lives in disparate systems, tracing processes from beginning to end becomes extraordinarily difficult. For instance, when Scottish Leather Group faced this exact issue across multiple sites, they implemented Q-Hub's integrated platform to create a unified data environment, dramatically improving their compliance management and interdepartmental communication.
Regulatory compliance adds further complexity. Facilities management companies must demonstrate traceability to satisfy standards like ISO 9001 and ISO 45001. Without structured systems, maintaining the necessary documentation becomes a burdensome, error-prone process. Continuous improvement methodologies address this by embedding compliance checkpoints directly into everyday workflows.
From Theory to Practice: Implementing Continuous Improvement
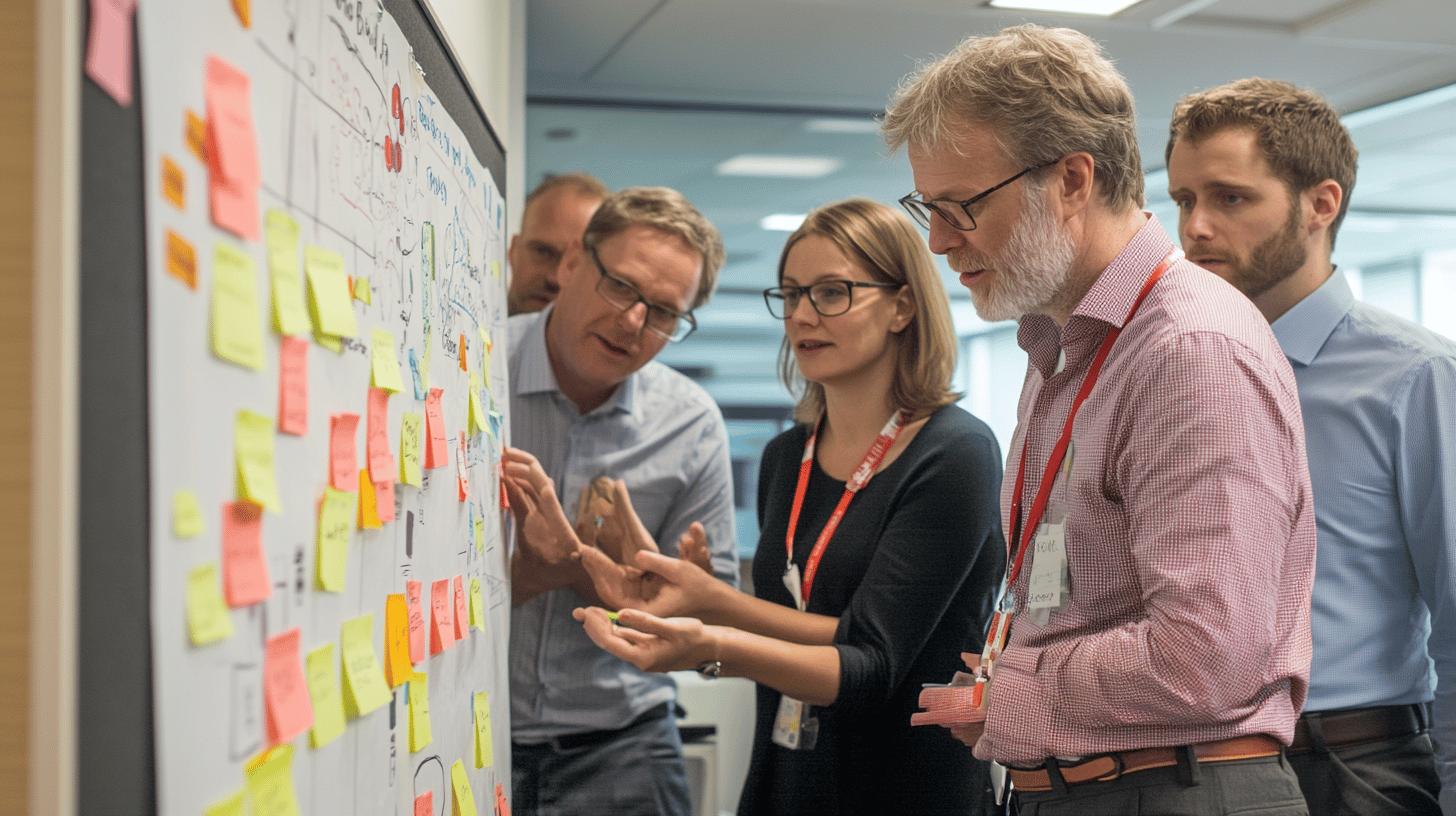
Implementing continuous improvement for better traceability follows a structured approach that delivers measurable results. The journey begins with clear objective-setting and careful analysis of your existing processes.
Start by defining exactly what you want to achieve. Are you focusing on improving maintenance traceability, enhancing supplier accountability, or streamlining compliance reporting? Each requires specific approaches within your improvement programme.
Next, conduct thorough value stream mapping of your supply chain. This reveals where value is being added and where inefficiencies are compromising traceability. For example, Anglia Cathodic Protection transformed their operations by digitising fragmented paper-based systems through Q-Hub's platform, which provided centralised oversight and streamlined non-conformance tracking.
Establishing meaningful KPIs is critical for measuring progress. These metrics should directly reflect your traceability goals and provide actionable insights:
<table border="0"> <tr><th>Metric</th><th>Before Digital Transformation</th><th>After Implementation</th></tr> <tr><td>Document Retrieval Time</td><td>Hours or Days</td><td>Seconds</td></tr> <tr><td>Audit Preparation</td><td>Weeks</td><td>Hours</td></tr> <tr><td>NCR Resolution Time</td><td>30+ Days</td><td>7-14 Days</td></tr> <tr><td>Data Accuracy</td><td>60-75%</td><td>95%+</td></tr> </table>Regular audits complete the implementation cycle, providing feedback that drives further refinements. This isn't a one-time exercise but an ongoing process of evaluation and enhancement that evolves with your supply chain needs.
Technology: The Catalyst for Traceability Excellence
Technology forms the backbone of modern traceability systems, amplifying the effectiveness of continuous improvement programmes. Without robust digital tools, even the best-designed processes struggle to deliver comprehensive supply chain visibility.
Real-time monitoring technologies give supply chain managers immediate insights into inventory levels, maintenance schedules, and operational workflows. This instant access to information transforms decision-making capabilities. For instance, BMC Analysis revolutionised their asset management by implementing Q-Hub's Asset Hub, which introduced structured calibration schedules with automated reminders.
Automation represents another technological cornerstone, streamlining data collection and reducing human error. When Fowlers of Bristol adopted Q-Hub's document management tools, they eliminated version control problems and ensured every team accessed the latest information, significantly reducing errors.
The technologies driving the most significant traceability improvements include:
- IoT Sensors: Provide real-time condition monitoring and location tracking for critical assets
- Digital Workflow Systems: Automate approvals and documentation, maintaining comprehensive audit trails
- Centralised Data Repositories: Create single sources of truth for all supply chain information
- Mobile Accessibility: Enable field personnel to capture and access data in real-time
- Analytics Dashboards: Transform raw data into actionable insights for continuous improvement
Measuring Success: The Metrics That Matter
Effective performance measurement is essential for evaluating and enhancing traceability improvements. Without concrete metrics, it's impossible to determine whether your continuous improvement initiatives are delivering results or requiring refinement.
The most valuable traceability metrics focus on both efficiency and effectiveness. On-time delivery rates reveal how smoothly your supply chain operates, while defect rates highlight quality issues requiring attention. Rocal Insulating Panels demonstrated this approach by using Q-Hub's dashboards to track safety metrics and near misses, gaining actionable insights that drove meaningful improvements in their safety culture.
Key Performance Indicators for Traceability
Beyond the standard metrics, leading organisations are adopting more sophisticated indicators:
- Mean Time to Detect Issues: How quickly problems are identified within the supply chain
- First-Time-Right Percentage: Proportion of processes completed correctly without rework
- Traceability Coverage: Percentage of supply chain with complete, gap-free tracking
- Supplier Compliance Rate: Measurement of how consistently suppliers meet traceability requirements
Weston Aerospace's journey exemplifies effective metric utilisation. After implementing Q-Hub's solutions, they transformed administrative-heavy processes like NCR management and CAPA into streamlined digital workflows with built-in performance tracking. This provided immediate visibility into resolution progress and enabled faster, more accurate decision-making.
Transforming Theory Into Operational Excellence
The real power of continuous improvement in traceability becomes evident when examining real-world implementations. Companies across various sectors have achieved remarkable transformations by systematically applying these principles.
One compelling example comes from the Scottish Leather Group, which faced significant challenges managing compliance across multiple sites with paper-based systems. By implementing Q-Hub's digital platform, they unified their processes, streamlined compliance documentation, and established centralised monitoring across all facilities. The result was enhanced visibility, dramatically improved audit preparation, and more effective interdepartmental communication.
The transformation pattern typically follows a predictable path:
- Identification of critical traceability gaps through systematic process analysis
- Implementation of standardised data collection and management systems
- Integration of real-time monitoring and notification capabilities
- Establishment of automated compliance documentation processes
- Continuous refinement based on performance metrics and stakeholder feedback
These implementations deliver tangible operational benefits that extend far beyond basic traceability. They create environments where data-driven decisions replace gut feelings, where compliance becomes a natural outcome rather than a burdensome exercise, and where continuous improvement becomes embedded in organisational culture.
Q-Hub's comprehensive digital transformation solutions provide the technological foundation for these improvements, offering customised QHSE software that adapts to your specific operational requirements. By bridging the gap between continuous improvement methodologies and practical implementation, Q-Hub enables organisations to achieve the full potential of their traceability initiatives. Ready to transform your facilities supply chain with advanced traceability solutions? Discover how Q-Hub's tailored software can streamline your operations and drive sustainable growth through improved transparency and efficiency.