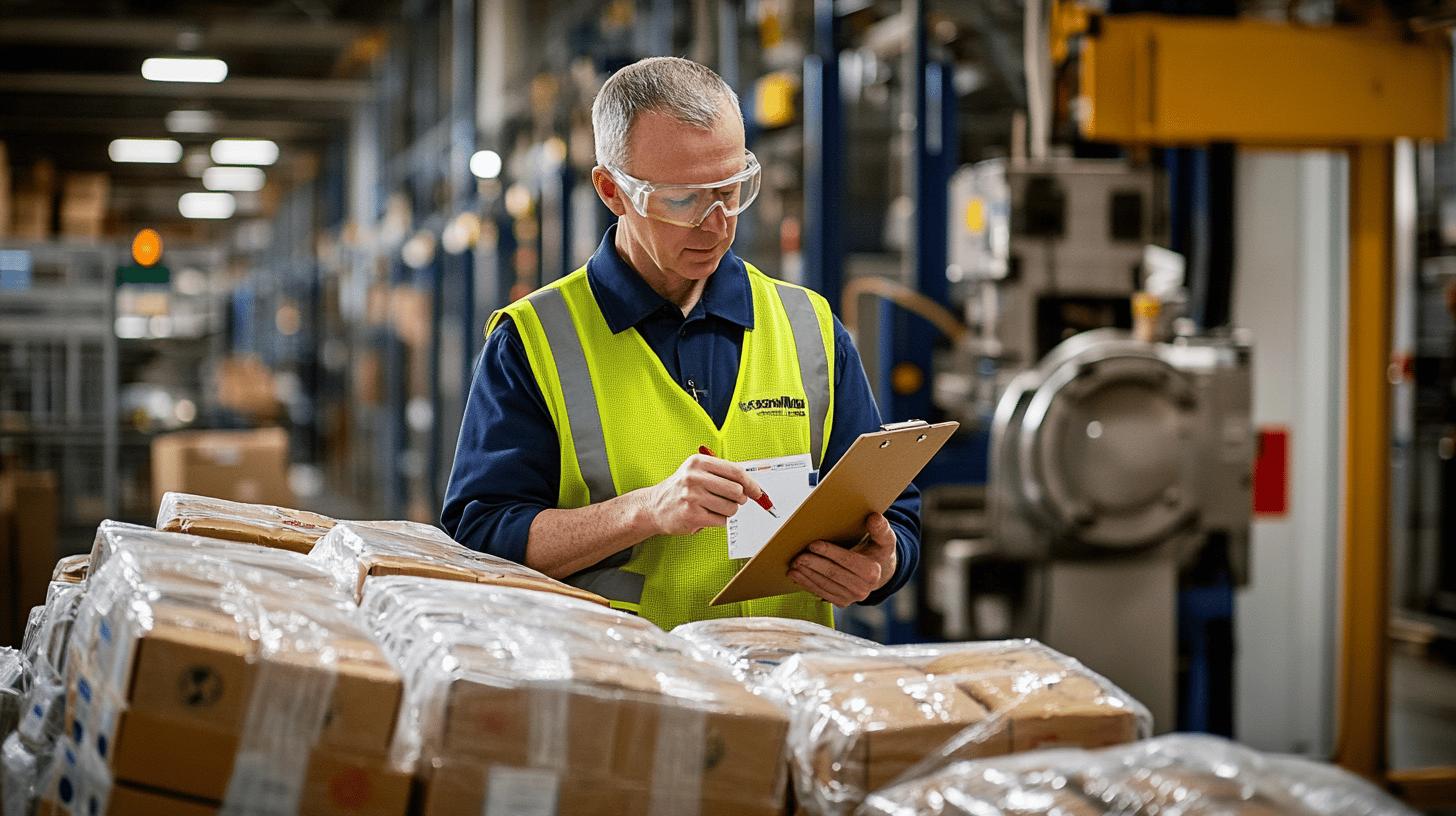
User Training Solutions Elevate Audit Quality in Food Manufacturing
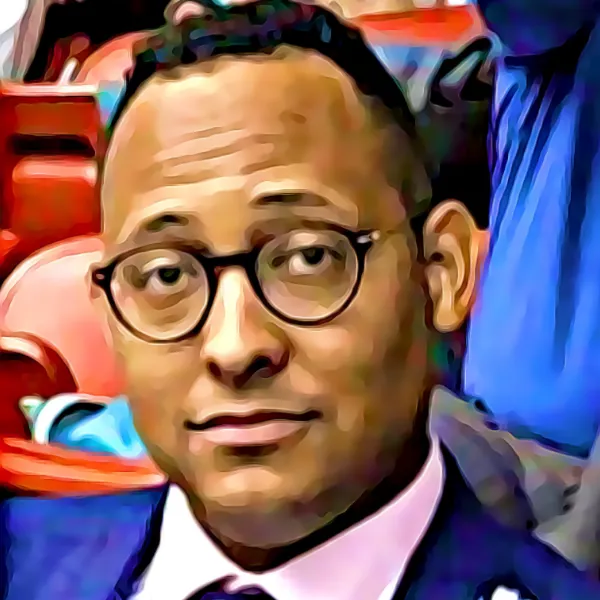
How User Training and Onboarding Solutions Enhance Audit and Inspection Quality in Food Manufacturing
Table of Contents
- How User Training and Onboarding Solutions Enhance Audit and Inspection Quality in Food Manufacturing
- Building Competence Beyond Compliance Checklists
- Essential Elements of Effective Food Safety Training
- Transforming Onboarding into Audit Excellence
- Digital Tools Revolutionising Training and Audit Readiness
- Measuring Training Impact with Data-Driven Insights
- Real-World Success Stories in Food Manufacturing
Effective training and onboarding are fundamental pillars for enhancing audit and inspection quality in food manufacturing. These structured approaches directly boost compliance and quality assurance by equipping teams with essential skills for navigating regulatory frameworks like HACCP and ISO 22000. Q-Hub's experience shows that companies implementing comprehensive training solutions experience fewer compliance breaches and smoother audit processes, while those with inadequate programmes face inconsistent practices and costly failures.
Building Competence Beyond Compliance Checklists
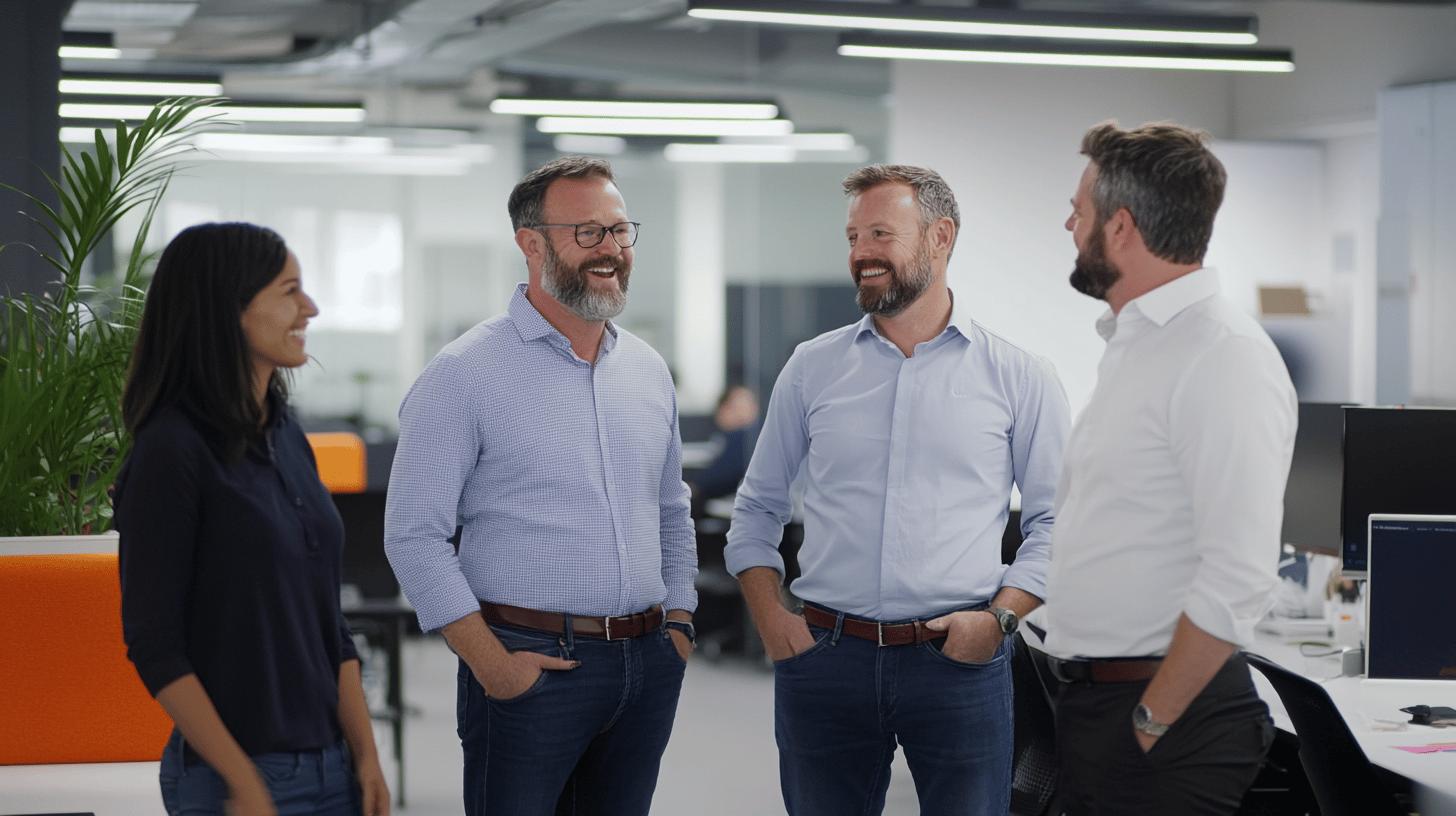
Training isn't merely about ticking boxes—it's about cultivating technical competence and confidence. When employees thoroughly understand critical procedures like cross-contamination prevention or non-conformance reporting, audit outcomes naturally improve.
A well-executed onboarding strategy ensures new hires align with both company processes and regulatory requirements from day one. Role-specific schedules with compliance-focused orientations help employees quickly adapt to internal quality standards and food safety practices.
Effective onboarding reduced our audit non-conformances by 22% within six months by ensuring consistent application of safety protocols across all production lines.
Technology solutions like Learning Management Systems (LMS) have revolutionised training delivery in food manufacturing. These platforms enable consistent, customised training at scale while simplifying documentation—providing readily available compliance records during audits.
Essential Elements of Effective Food Safety Training
Comprehensive training programmes cover several critical areas to ensure regulatory compliance. Without addressing these key elements, manufacturers risk falling short of standards like HACCP and ISO 22000, potentially leading to failed audits and reputational damage.
Training must be continuous rather than a one-time event. Ongoing education ensures teams adapt to evolving regulations, equipment changes, and internal process updates—especially crucial in the dynamic food manufacturing environment.
Companies implementing Q-Hub's digital training solutions typically focus on these essential areas:
- HACCP principles and practical application
- Cross-contamination prevention protocols
- Equipment maintenance and sanitation procedures
- Traceability system implementation
- Allergen control management
- Incident reporting workflows
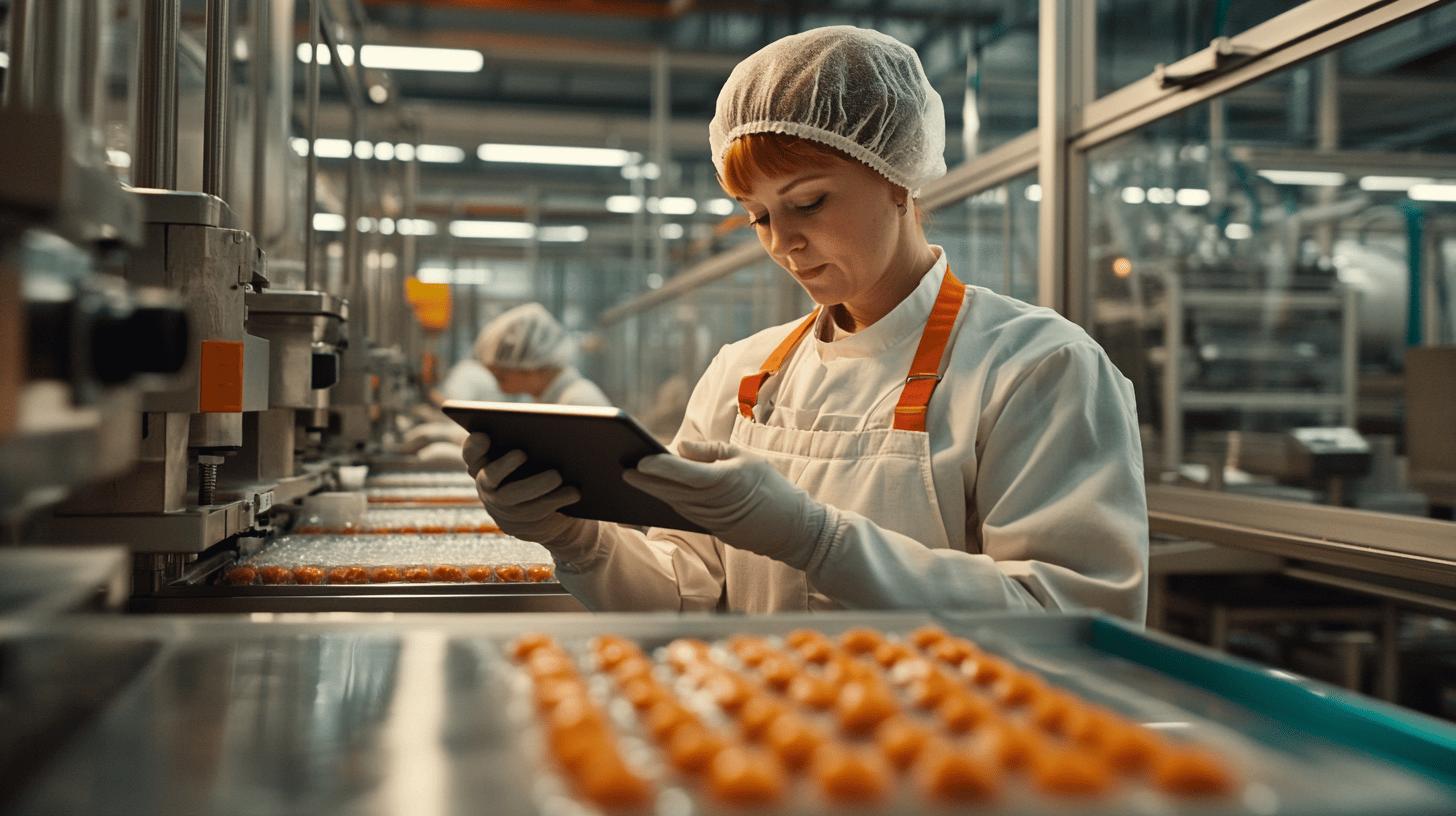
Digital learning platforms significantly enhance training effectiveness. For example, Q-Hub's customisable modules allow role-specific training—ensuring line workers focus on allergen controls while quality assurance personnel concentrate on traceability systems.
Transforming Onboarding into Audit Excellence
Effective employee onboarding forms the critical bridge between hiring and operational readiness. In food manufacturing, where inspections demand precision, structured onboarding significantly enhances audit quality by aligning new employees with compliance protocols from day one.
Balancing technical training with cultural integration creates truly effective onboarding. While understanding allergen control procedures on paper is important, real success comes when employees confidently apply these protocols in daily operations—understanding not just what to do, but why it matters.
Best practices for audit-enhancing onboarding include:
- Assigning experienced mentors for real-time guidance
- Implementing digital tracking tools to monitor progress
- Gathering continuous feedback to refine programmes
- Developing role-specific compliance training modules
- Conducting post-onboarding evaluations
Companies using Q-Hub's digital onboarding solutions report significant improvements in inspection readiness. Digital tools flag potential knowledge gaps before they impact audit performance, while structured feedback mechanisms ensure programmes evolve with regulatory changes.
Digital Tools Revolutionising Training and Audit Readiness
Modern technology solutions are transforming how food manufacturers prepare for audits and inspections. Digital platforms—from learning management systems to augmented reality modules—streamline compliance training and optimise processes, significantly elevating inspection quality.
LMS platforms serve as the backbone of effective training systems, offering automated scheduling, progress tracking, and targeted content delivery. For instance, quality assurance officers receive specialised allergen management modules while production staff focus on sanitisation protocols—creating consistent knowledge delivery across the workforce.
Advanced technologies take training effectiveness to new levels:
Digital Tool | Key Function | Impact on Audits |
---|---|---|
Learning Management System | Automated training delivery | 20% fewer non-conformances |
Augmented Reality Modules | Immersive scenario training | 35% better knowledge retention |
AI Performance Analytics | Gap identification | Proactive compliance management |
The real power emerges when these tools work together. Combining Q-Hub's LMS capabilities with analytics allows manufacturers to customise training while continuously improving content based on performance trends—ensuring employees are fully prepared for audit challenges.
Measuring Training Impact with Data-Driven Insights
Evaluating the effectiveness of training and onboarding requires robust measurement frameworks. Key performance indicators like non-conformance rates and competency scores provide clear visibility into how well teams navigate inspections.
Enhanced onboarding directly reduces compliance errors by aligning employees with requirements from day one. For example, when new hires receive structured onboarding that covers HACCP principles and allergen controls, they implement these standards more effectively during inspections.
Critical metrics for measuring training impact include:
- Audit non-conformance rates and severity
- Time efficiency during inspections
- Knowledge assessment and retention scores
- Frequency and patterns of audit findings
Consistent tracking reveals valuable trends that guide improvement efforts. Companies implementing Q-Hub's training solutions have reported correlations between higher knowledge scores and smoother inspections—insights that not only optimise training but foster accountability throughout the organisation.
Real-World Success Stories in Food Manufacturing
Leading food manufacturers have achieved measurable improvements through strategic training and onboarding initiatives. Their experiences highlight the transformative impact of well-implemented programmes on audit outcomes and operational excellence.
Scottish Leather Group revolutionised their compliance management by implementing Q-Hub's digital training platform. By centralising learning content and automating scheduling, they created a unified approach to ISO standards compliance. The result was significantly reduced audit preparation time and improved communication between departments and sites.
Weston Aerospace transformed their quality management through streamlined onboarding. By digitising critical workflows and implementing automated training schedules, they addressed compliance bottlenecks that previously hindered operations. Their implementation of Q-Hub's Process Hub enabled the digitalisation of business-critical workflows, including NCR management.
Metric | Before Q-Hub | After Q-Hub |
---|---|---|
Audit Prep Time | 5-7 days | 1-2 days |
Non-Conformances | 15-20 per audit | 3-5 per audit |
Employee Engagement | Limited participation | Organisation-wide involvement |
These case studies demonstrate that investment in robust training and onboarding solutions delivers substantial returns. By leveraging Q-Hub's digital transformation expertise, food manufacturers can significantly enhance audit performance while building stronger compliance cultures throughout their organisations.
Ready to transform your food manufacturing compliance through effective training and onboarding? Q-Hub specialises in designing customised QHSE software solutions that streamline processes, enhance efficiency, and ensure long-term compliance through digital transformation and expert guidance.
<