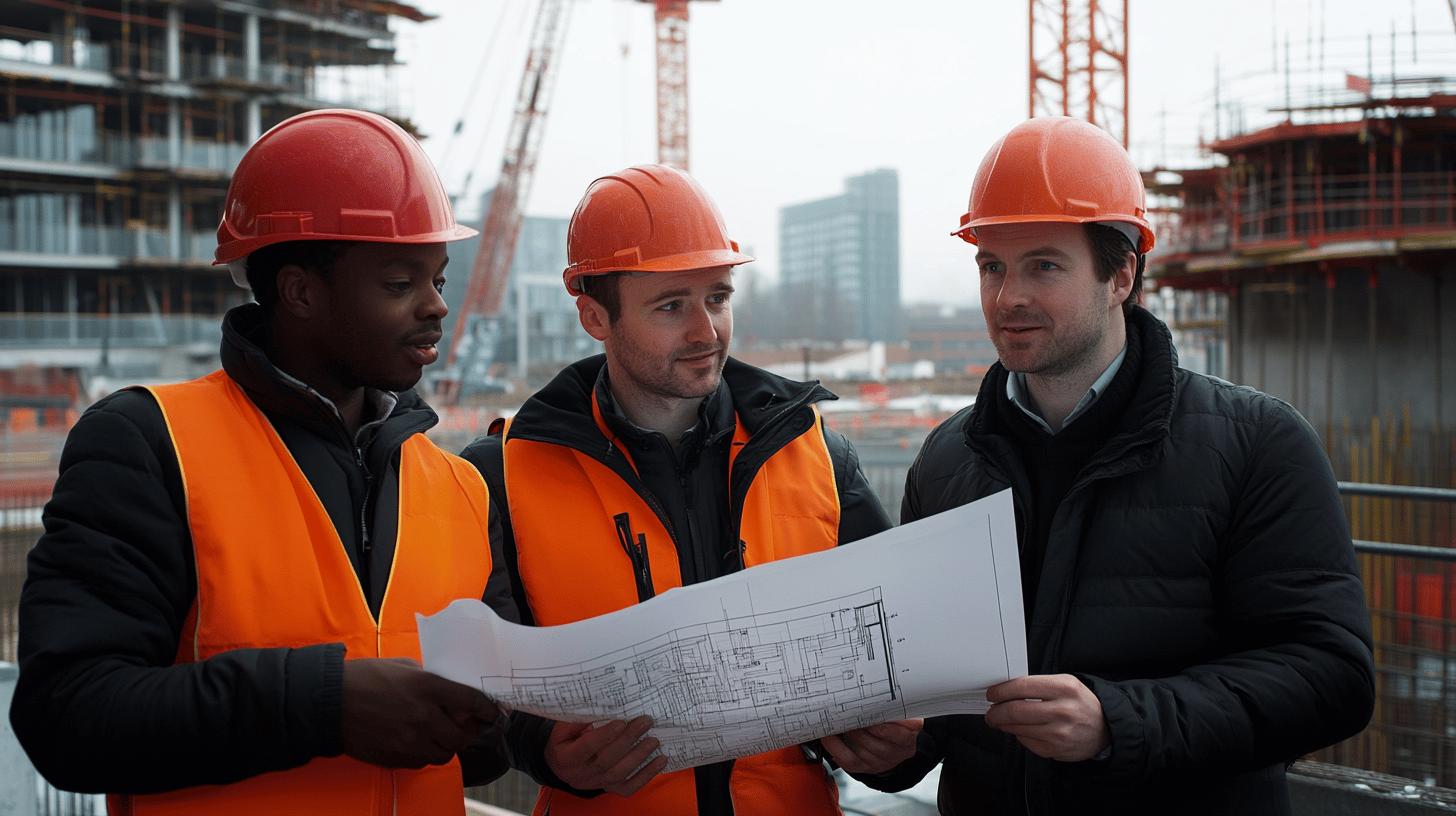
Supplier and Contractor Management: Boosting Compliance in Engineering
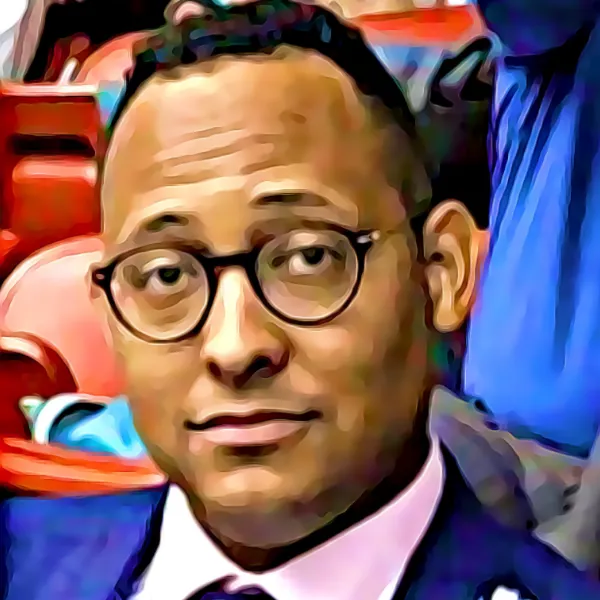
Best Practices for Supplier and Contractor Management in Engineering Sourcing
Supplier and contractor management reinforcing safety management compliance in engineering sourcing forms the backbone of operational efficiency and risk reduction. Without a structured approach, organisations face compliance gaps, project delays, and workplace hazards. Q-Hub's experience shows that effective vendor oversight ensures suppliers and contractors meet safety protocols, regulatory standards, and project objectives.
Clear role definition is essential—every contractor must understand their responsibilities, from safety adherence to quality delivery. For example, scaffolding contractors need comprehension of both technical specifications and ISO 45001 safety requirements. This clarity prevents compliance failures and operational disruptions.
Transforming Compliance Through Digital Innovation
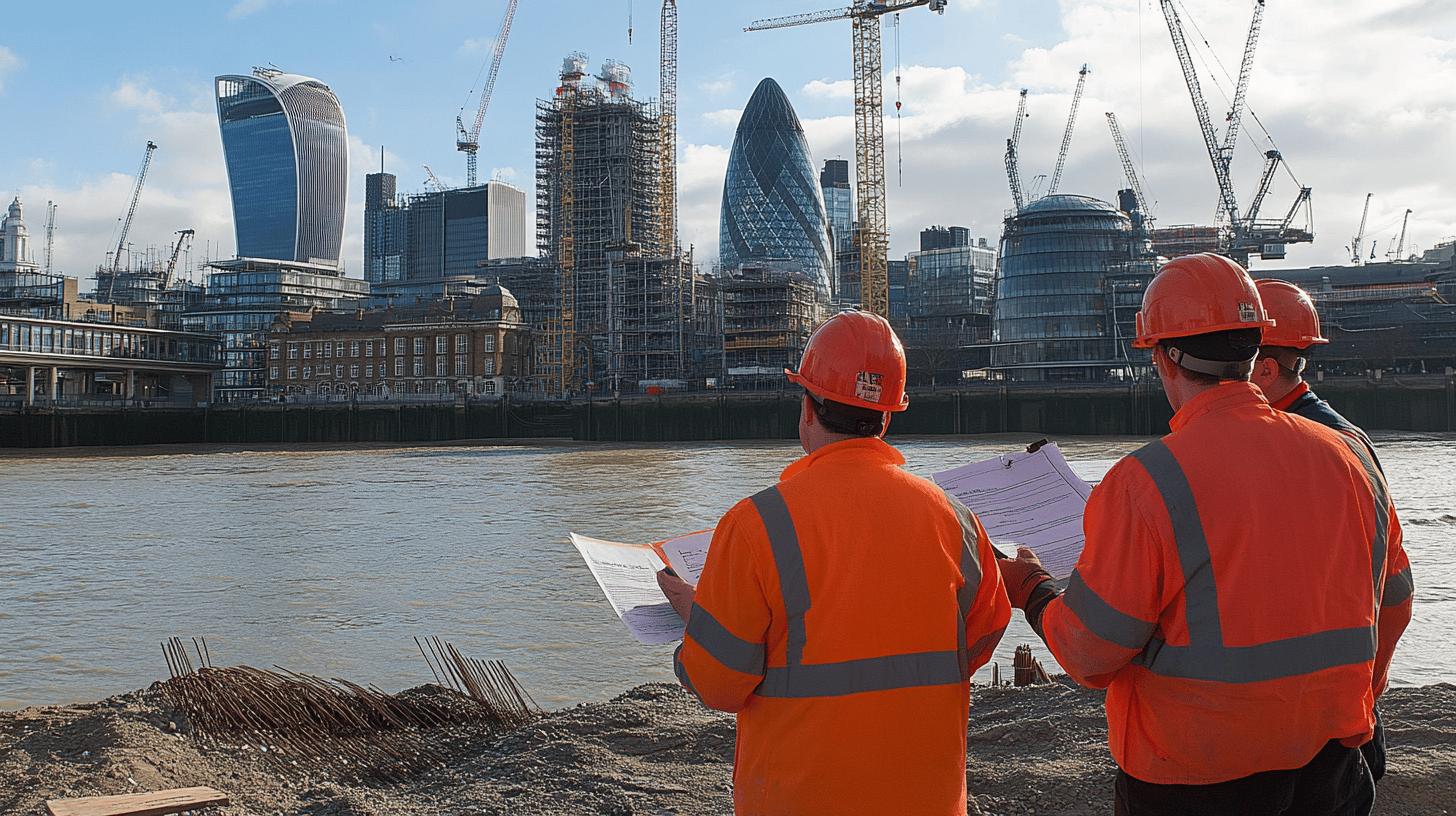
The traditional manual approach to contractor compliance creates significant vulnerabilities. Paper-based systems, like those used by Anglia Cathodic Protection before their digital transformation, lead to miscommunication and safety oversights. Modern digital platforms streamline compliance tracking, automate documentation, and flag risks in real-time.
Q-Hub's supplier management platforms centralise compliance data, creating dashboards that instantly reveal which contractors meet safety standards and which require intervention. This level of transparency ensures nothing slips through the cracks—a crucial factor when managing multiple contractors and complex safety requirements.
Before implementing a digital compliance system, tracking non-conformances was challenging with resolutions often delayed due to lack of structure. Qhub's Process Hub provided a centralised space for managing NCRs, linking them to audits, and ensuring accountability at each step.
The Scottish Leather Group experienced similar benefits after implementing Q-Hub's solutions, moving from paper-based systems that struggled with ISO standard compliance to a unified digital platform that streamlined multi-site safety management.
Essential Steps for Effective Contractor Governance
Implementing robust contractor management requires strategic action. Consider these core practices:
- Establish clear communication protocols ensuring safety requirements are understood at all levels
- Conduct thorough supplier evaluations focusing on safety records and compliance history
- Develop structured contractor selection processes prioritising certifications and compliance capabilities
- Provide targeted safety training aligned with your organisation's standards
- Implement regular compliance audits and performance reviews to maintain accountability
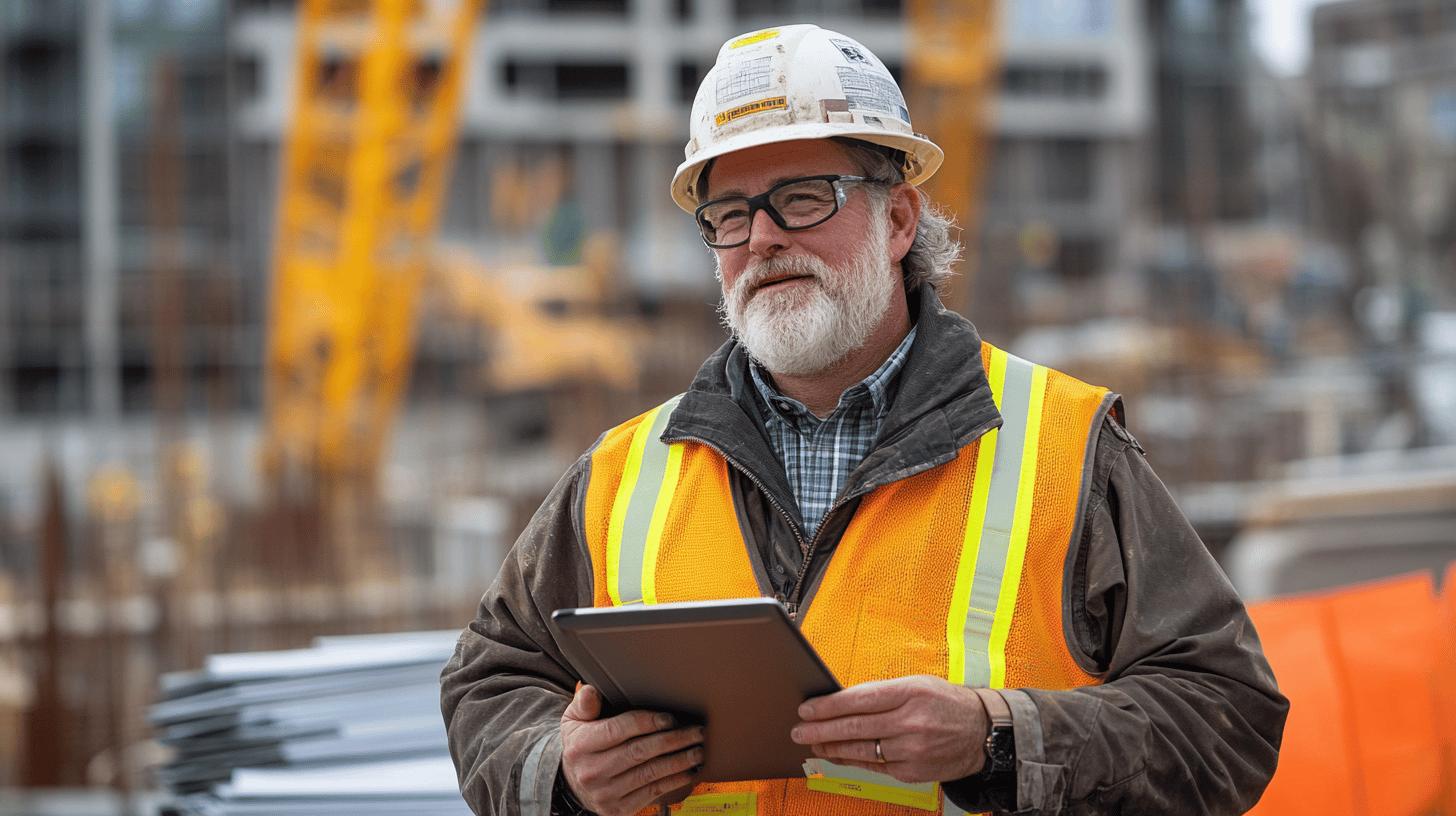
Digital transformation has revolutionised these processes. For example, Rocal Insulating Panels replaced their paper-based accident reporting system with Q-Hub's automated workflows, enabling quicker resolution of safety incidents and better departmental involvement.
Regulatory Frameworks That Drive Compliance
Understanding the regulatory landscape is crucial for effective contractor management. Key frameworks include:
<table border="0"> <tr><th>Regulation</th><th>Requirement</th><th>Implementation</th></tr> <tr><td>ISO 9001</td><td>Quality management systems</td><td>Supplier evaluation processes</td></tr> <tr><td>ISO 45001</td><td>Occupational safety standards</td><td>Contractor safety protocols</td></tr> <tr><td>Health and Safety at Work Act</td><td>Legal duty of care</td><td>Risk assessment procedures</td></tr> <tr><td>SSIP Accreditation</td><td>Pre-qualification for safety</td><td>Contractor selection criteria</td></tr> </table>Non-compliance consequences are severe, including financial penalties, legal prosecution, and reputational damage. Companies like Weston Aerospace have found that integrating regulatory requirements into supplier and contractor management isn't just about avoiding penalties—it's about building sustainable operational excellence.
Building Stronger Supplier Relationships
Effective contractor management isn't just about oversight—it's about partnership. Strong relationships drive compliance and operational success, while poor management leads to communication breakdowns and missed safety targets.
Fowlers of Bristol transformed their approach by centralising communication through Q-Hub's portal, bringing critical workflows and data into a single digital space. This improved collaboration between engineering teams, shop floor workers, and compliance managers.
To strengthen these relationships:
- Establish consistent communication channels to align on safety expectations
- Provide regular performance feedback highlighting both strengths and compliance gaps
- Engage in collaborative problem-solving around compliance challenges
- Define clear contractual terms regarding safety responsibilities
The Future of Digital Compliance Management
Tomorrow's compliance landscape will be defined by smart, integrated systems. Q-Hub's solutions demonstrate how digital platforms are transforming contractor management through:
Real-time compliance dashboards: BMC Analysis used Q-Hub to create live KPIs for non-conformance resolution, dramatically improving their ability to track and resolve issues quickly.
Automated workflow management: When Rocal Insulating Panels implemented Q-Hub's digital tools, they eliminated hours of manual work through automated document control and streamlined accident investigations.
Centralised data systems: Scottish Leather Group leveraged Q-Hub to manage compliance across multiple sites and standards within a single platform, simplifying what was previously an overwhelming challenge.
These innovations don't just improve compliance—they transform how organisations approach safety culture and contractor relationships. By digitising these processes, companies gain visibility, control, and efficiency.
Q-Hub's software solutions provide the foundation for robust supplier and contractor management by streamlining compliance, enhancing transparency, and building accountability. As engineering sourcing becomes increasingly complex, digital transformation isn't just an advantage—it's essential for maintaining safety excellence and operational efficiency.