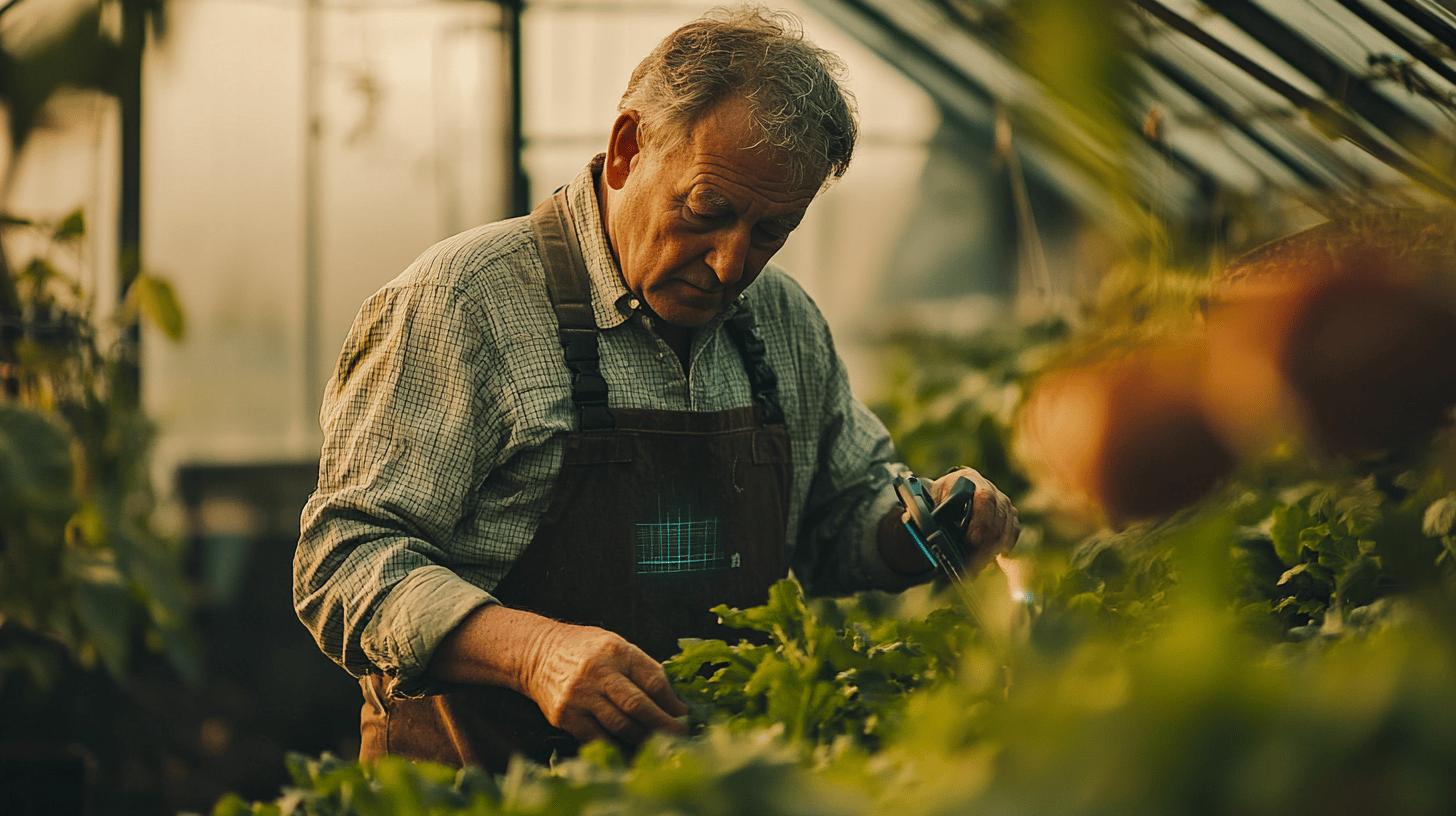
Supplier and Contractor Tools Enhance Food Production Audits
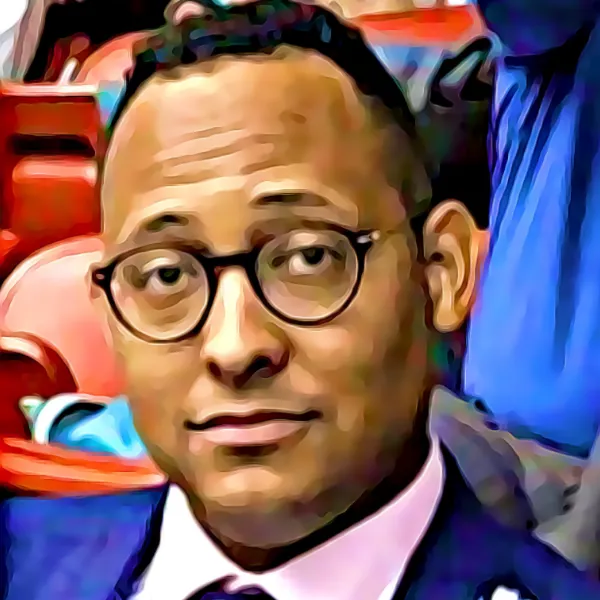
Why Supplier and Contractor Management Tools Are Essential for Food Production Audits
Supplier and contractor management tools have become crucial for food production companies facing increasingly stringent safety regulations. With standards like HACCP, ISO 22000, and the Food Safety and Hygiene (England) Regulations 2013 constantly evolving, these digital solutions help businesses navigate complex compliance requirements efficiently. Q-Hub's specialised software transforms what would otherwise be an overwhelming process into a streamlined workflow, enabling food producers to stay ahead of regulatory changes while reducing risks and avoiding costly penalties.
These tools automate critical audit aspects, allowing real-time monitoring of supplier and contractor performance. Digital platforms flag non-compliance issues, track corrective actions, and maintain transparent audit records—all essential for meeting regulatory requirements while minimising human error, one of the leading causes of audit failures in food production.
By implementing our supplier management system, food manufacturers typically reduce compliance-related administrative work by 40% while significantly improving audit readiness and response times.
Transforming Paper-Based Processes into Digital Efficiency
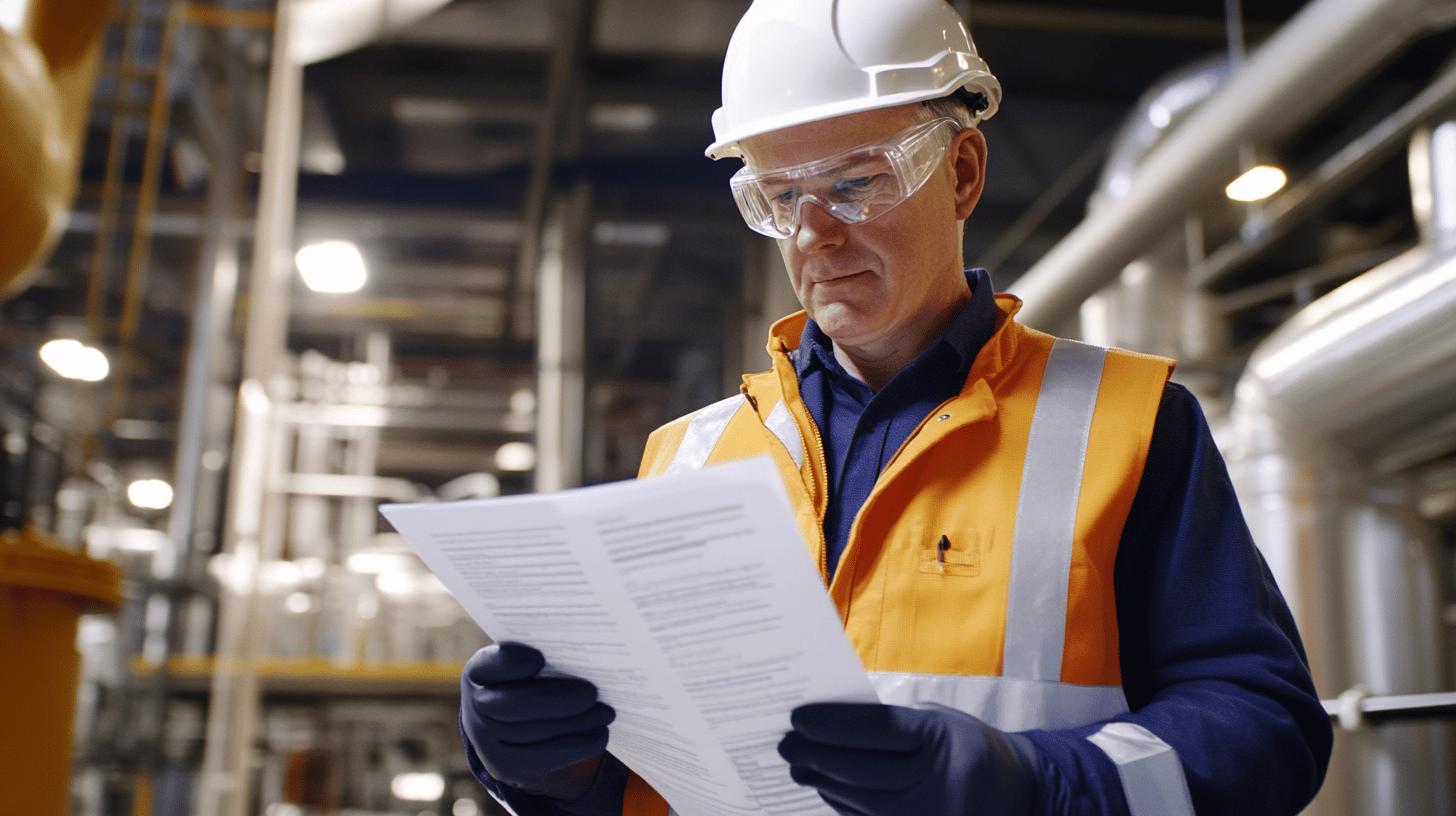
Traditional paper-based audit methods simply can't match the efficiency of digital solutions. Modern supplier management tools offer customisable audit templates tailored to specific regulatory requirements like HACCP or ISO 22000, ensuring every inspection is both relevant and thorough.
Digital inspection checklists standardise procedures across your operation, reducing oversight risks while enabling real-time updates. This flexibility is critical for maintaining consistency whether audits are conducted on-site or remotely—effectively bridging the gap between regulatory demands and operational efficiency.
The Scottish Leather Group experienced this transformation firsthand when implementing Q-Hub's solutions. By digitising their previously paper-based systems, they eliminated hours of manual work while gaining real-time access to critical compliance data across multiple sites and departments.
How Automation Revolutionises Food Safety Compliance
Automation eliminates repetitive tasks, dramatically reducing human error while accelerating the entire audit process. Real-time analytics provide actionable insights into supplier performance, allowing food businesses to identify potential risks before they escalate into serious compliance issues.
Weston Aerospace saw this benefit directly after implementing Q-Hub's system. Their quality team gained instant visibility into resolution progress through digitised non-conformance workflows and integrated KPIs, enabling faster and more accurate decision-making across departments.
Many of these tools offer mobile accessibility, enabling inspectors to conduct audits from anywhere without being tied to a desk. The combination of automation and data-driven insights improves audit accuracy while helping businesses stay proactive about food safety standard compliance—even under tight deadlines.
Key capabilities that make these tools invaluable include:
- Mobile accessibility for conducting audits on-site or remotely
- Customisable digital inspection templates meeting specific standards
- Automated reporting for streamlined documentation
- Real-time analytics for actionable performance insights
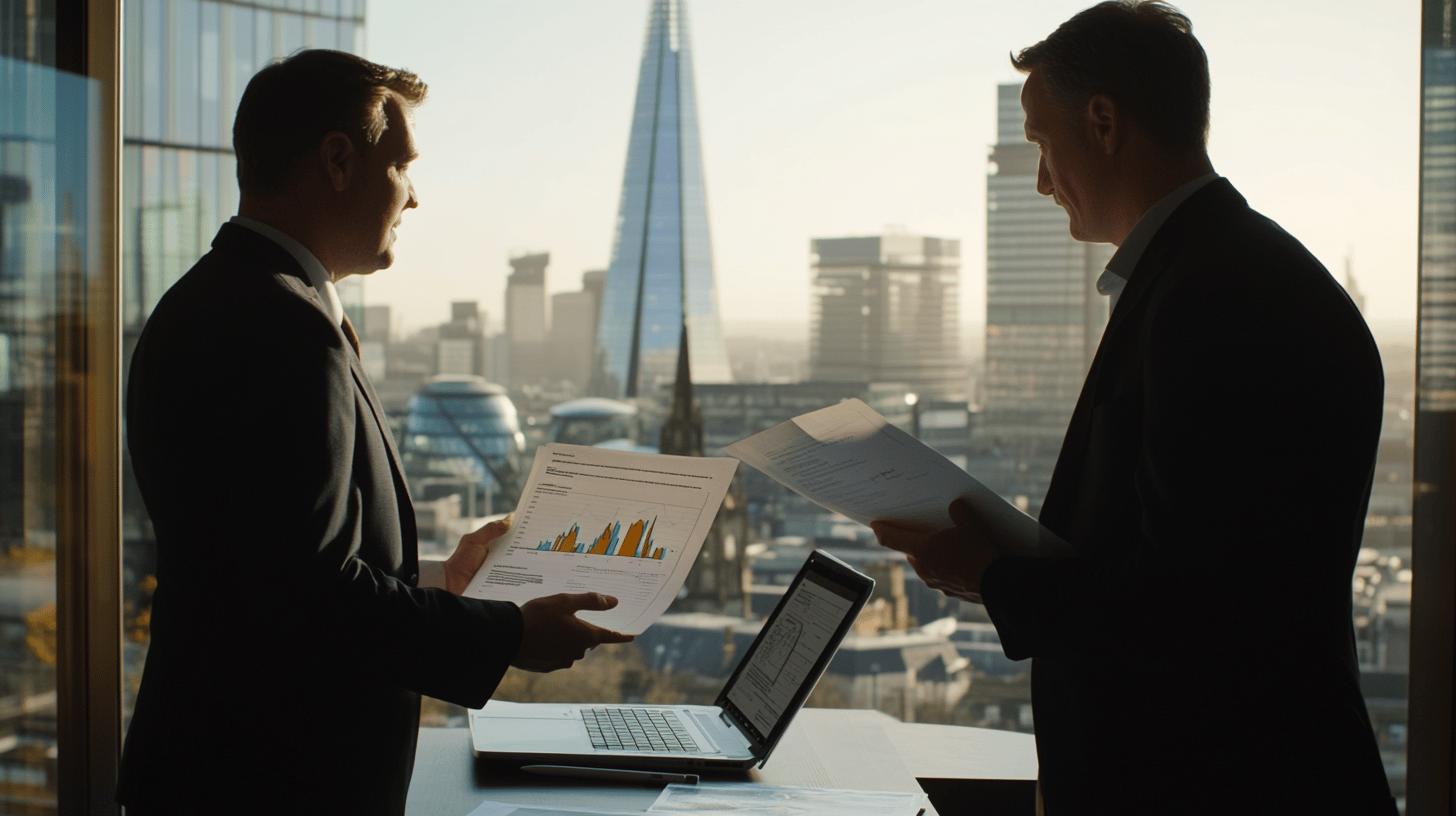
Regulatory Navigation Made Simple
Food safety standards evolve frequently, making it challenging to stay updated with new requirements. Modern supplier management tools keep businesses informed through automated alerts and reminders about regulatory changes and upcoming compliance deadlines.
For example, if a regulation update impacts supplier audit criteria, the system can notify relevant teams and suggest process adjustments. This functionality improves audit readiness while fostering accountability across the organisation—creating a safety net that ensures no critical updates slip through the cracks.
Documentation capabilities are another area where these tools excel. Regulatory bodies like the Food Standards Agency expect comprehensive reporting during audits, and digital systems simplify this by automating compliance record creation and storage, providing easily accessible reports tailored to specific requirements.
Real-World Success Stories: Measurable Improvements
The impact of these digital solutions is both measurable and meaningful for food producers. Anglia Cathodic Protection transformed their non-conformance tracking after implementing Q-Hub's Process Hub, which provided a centralised space for managing NCRs, linking them to audits, and ensuring accountability at each step.
Similarly, BMC Analysis streamlined their NCR management by replacing Word documents and fragmented email communication with Q-Hub's Process Hub. With automated tracking and reporting, NCRs could be resolved efficiently, ensuring no action was overlooked while providing immediate insight into process progress.
These improvements translate to concrete metrics that demonstrate the value of digital transformation:
<table border="0"> <tr><th>Metric</th><th>Before Automation</th><th>After Automation</th></tr> <tr><td>Audit Preparation Time</td><td>3-5 days</td><td>4-8 hours</td></tr> <tr><td>NCR Resolution Time</td><td>14-21 days</td><td>5-8 days</td></tr> <tr><td>Documentation Access</td><td>Minutes to hours</td><td>Seconds</td></tr> </table>Building the Digital Foundation for Food Safety Excellence
Automated systems create a reliable audit trail invaluable for regulatory compliance and future reference. When inspectors request information, food businesses can quickly retrieve organised reports without searching through mountains of paperwork—a capability that Rocal Insulating Panels benefited from after implementing Q-Hub's document control system.
Beyond compliance, automation enhances traceability—a critical factor in food production. Digital tools provide real-time updates, ensuring every audit step is transparent and traceable. This visibility not only boosts confidence during inspections but strengthens overall operational integrity.
With faster corrective actions and efficient scheduling, automation transforms audits from a reactive chore into a strategic advantage for food producers committed to excellence.
Choosing the Right Solution for Your Food Production Operation
When selecting a supplier management tool, carefully consider your unique business requirements. If your food production operates across multiple sites, prioritise solutions with robust scalability like those offered by Q-Hub. Similarly, tools with advanced reporting capabilities help streamline compliance with regulations like HACCP or ISO 22000.
Customer reviews and case studies provide invaluable real-world insights. Fowlers of Bristol, for example, centralised all critical workflows, datasets, and communications into Q-Hub's digital space, enabling instant access to real-time data while fostering collaboration between teams.
Don't overlook vendor support when evaluating options. Even the most feature-rich system can falter without reliable support for troubleshooting or customisation. Request demonstrations to validate claims and ensure the system aligns with your specific needs.
Q-Hub specialises in customised software solutions that grow with your business, seamlessly connecting with existing systems while adapting to evolving food safety standards. By selecting a flexible system today, you're investing in long-term operational excellence and compliance readiness.