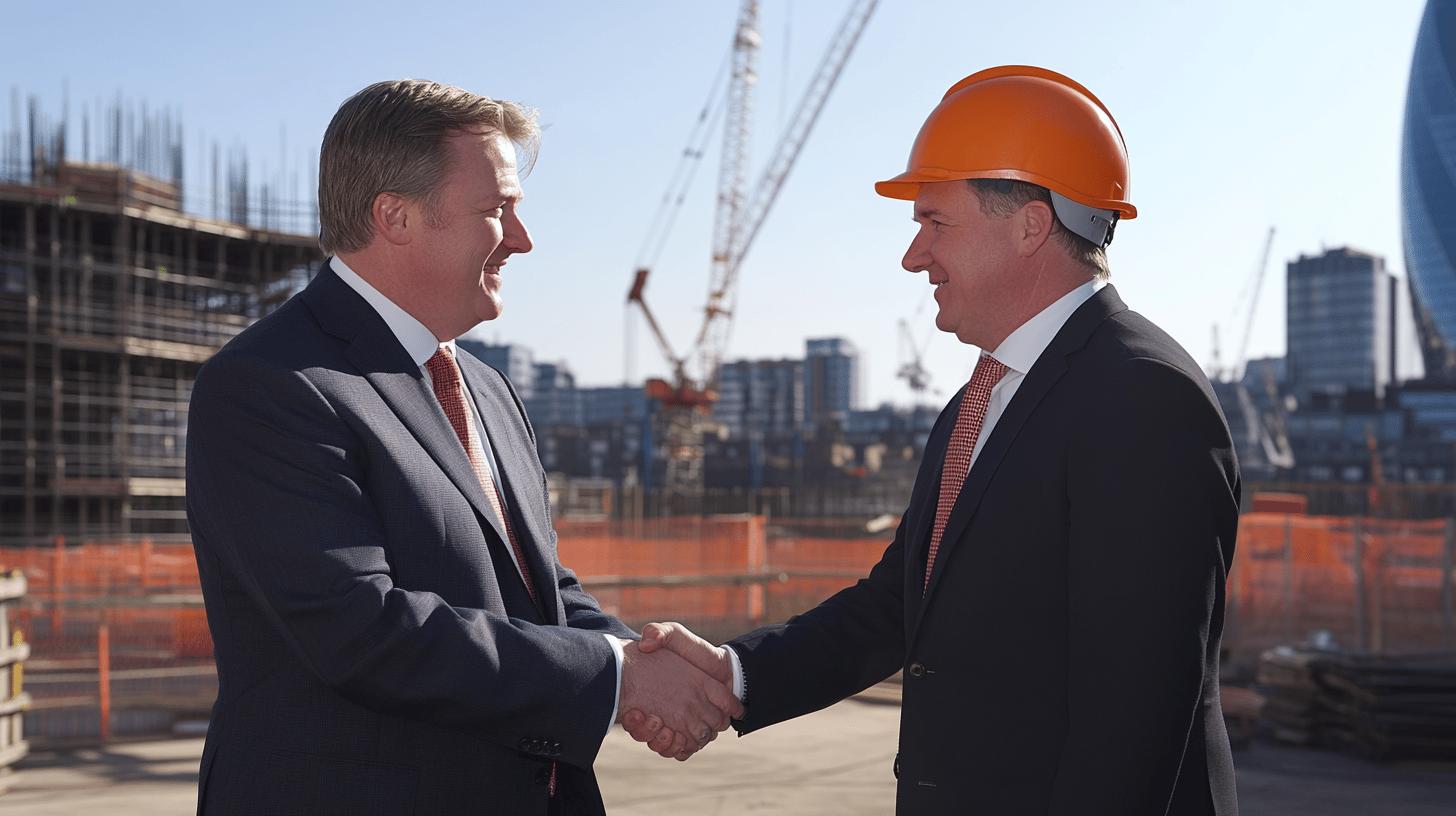
Supplier and Contractor Management Boosts Safety Compliance
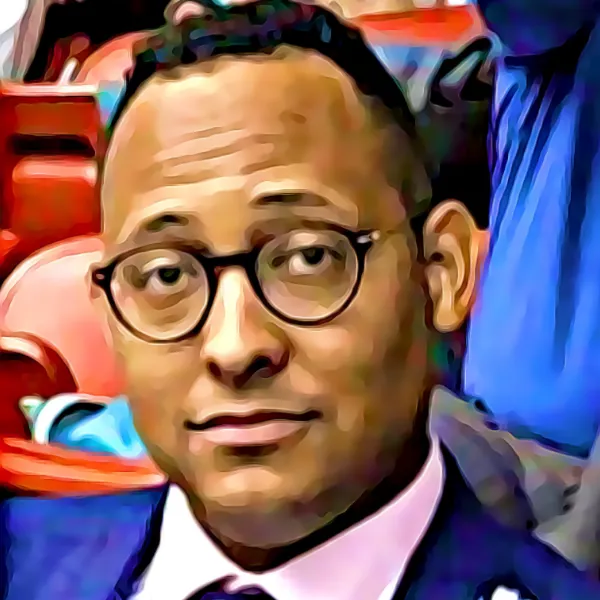
The Role of Supplier and Contractor Management in Reinforcing Safety Compliance
Effective supplier and contractor management is crucial for safety compliance in retail sourcing. This process ensures every participant in the supply chain follows established safety standards and regulatory requirements. Q-Hub's software solutions help businesses mitigate risks, protect their reputation, and maintain operational continuity through robust compliance frameworks. Without proper oversight, gaps in compliance can lead to legal consequences, financial losses, and disruptions.
Retail sourcing involves complex supplier networks where safety lapses at any point create significant ripple effects. According to the Health and Safety Executive, workplace injuries in UK retail are preventable yet costly. Compliance isn't merely about ticking boxes—it's about creating safer, more efficient environments where operations flow smoothly with fewer disruptions.
Effective supplier management doesn't just prevent problems—it transforms compliance from a burden into a competitive advantage.
The benefits of robust supplier management include reduced legal risks, ethical sourcing assurance, enhanced supply chain transparency, stronger stakeholder trust, and improved operational efficiency through streamlined safety workflows.
Beyond Checkbox Compliance: Creating Sustainable Safety Standards
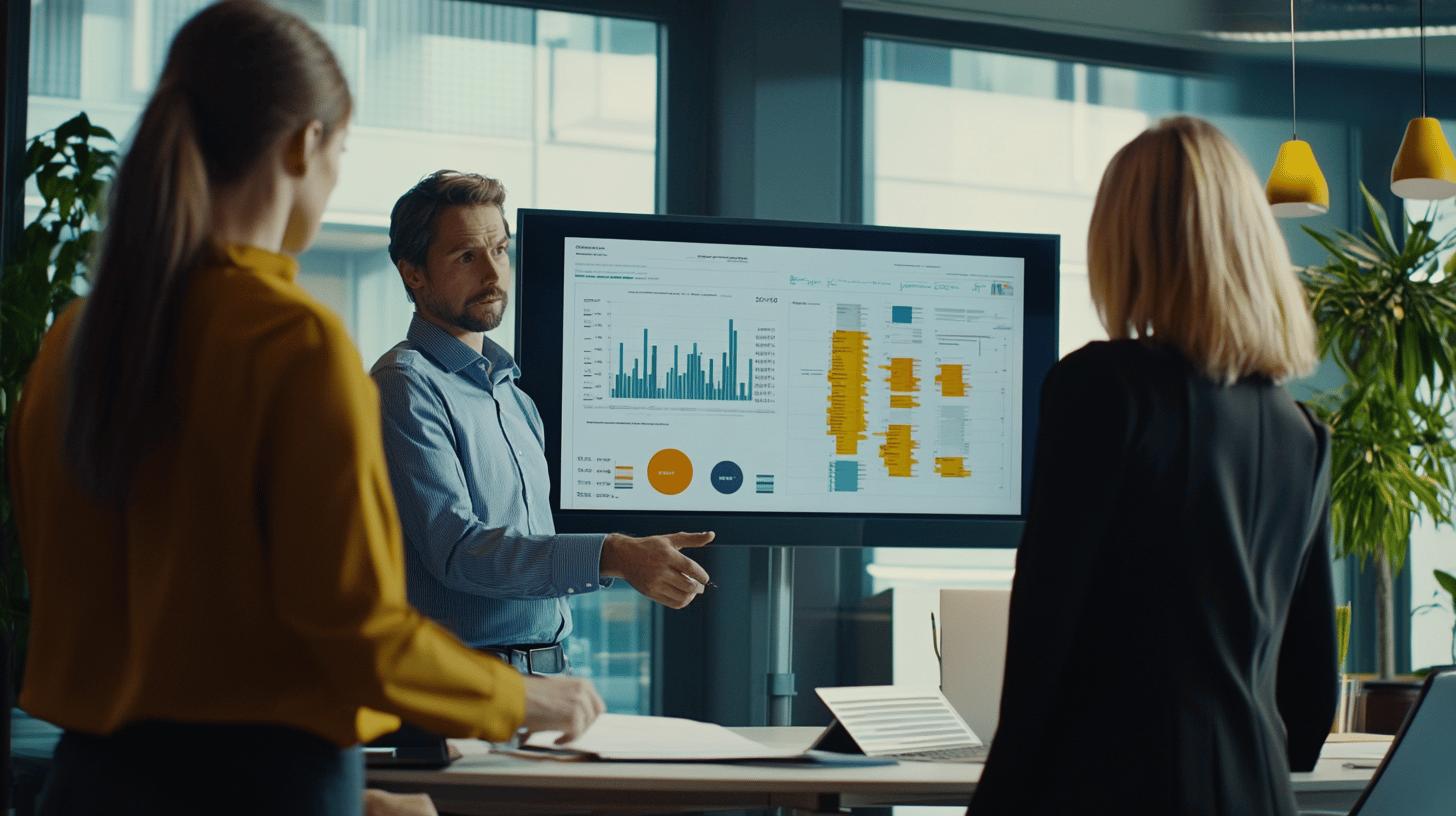
Risk assessment forms the foundation of effective supplier management. Whether called vendor oversight or third-party evaluation, the goal remains consistent: ensuring everyone in the supply chain maintains safety standards. Precision matters in identifying hazards—every overlooked risk represents a potential incident.
Contractor vetting acts as a critical safety filter. Only suppliers aligning with your specific protocols and holding proper certifications should make it through this process. Background checks, performance reviews, and certification verification create a thorough screening system that prevents safety compromises.
Operational risk management takes a broader view by evaluating the entire supply chain's safety landscape. This approach identifies communication gaps or operational bottlenecks that could create unsafe conditions, helping uncover risks that might otherwise remain hidden.
Digital platforms and standardised frameworks provide consistency in how assessments are conducted across multiple suppliers and contractors. This creates a structured, proactive approach to measuring and addressing risks throughout the supply network.
Setting Clear Expectations Through Measurable Standards
Vendor compliance assessment creates reliable, transparent, and accountable supply chains. Starting with clearly defined benchmarks ensures expectations aren't negotiable. Suppliers must demonstrate adherence to industry regulations, maintain relevant certifications like ISO 45001, and meet ethical sourcing standards. When criteria remain vague, accountability becomes impossible.
Regular supplier audits are essential since even thorough initial vetting can't anticipate ongoing compliance issues. Compliance requires dynamic monitoring with regular check-ins to uncover potential risks. These audits create valuable audit trails that demonstrate due diligence during regulatory inspections.
Digital compliance reporting tools drastically improve efficiency by streamlining tracking and management. Q-Hub's solutions offer real-time insights into vendor performance, allowing businesses to instantly access supplier incident histories, quality control measures, and environmental compliance metrics.
When integrating compliance metrics into assessment processes, focus on these key areas:
- Safety certifications and validity
- Regulatory adherence history
- Incident tracking and resolution
- Quality control implementation
- Ethical sourcing verification
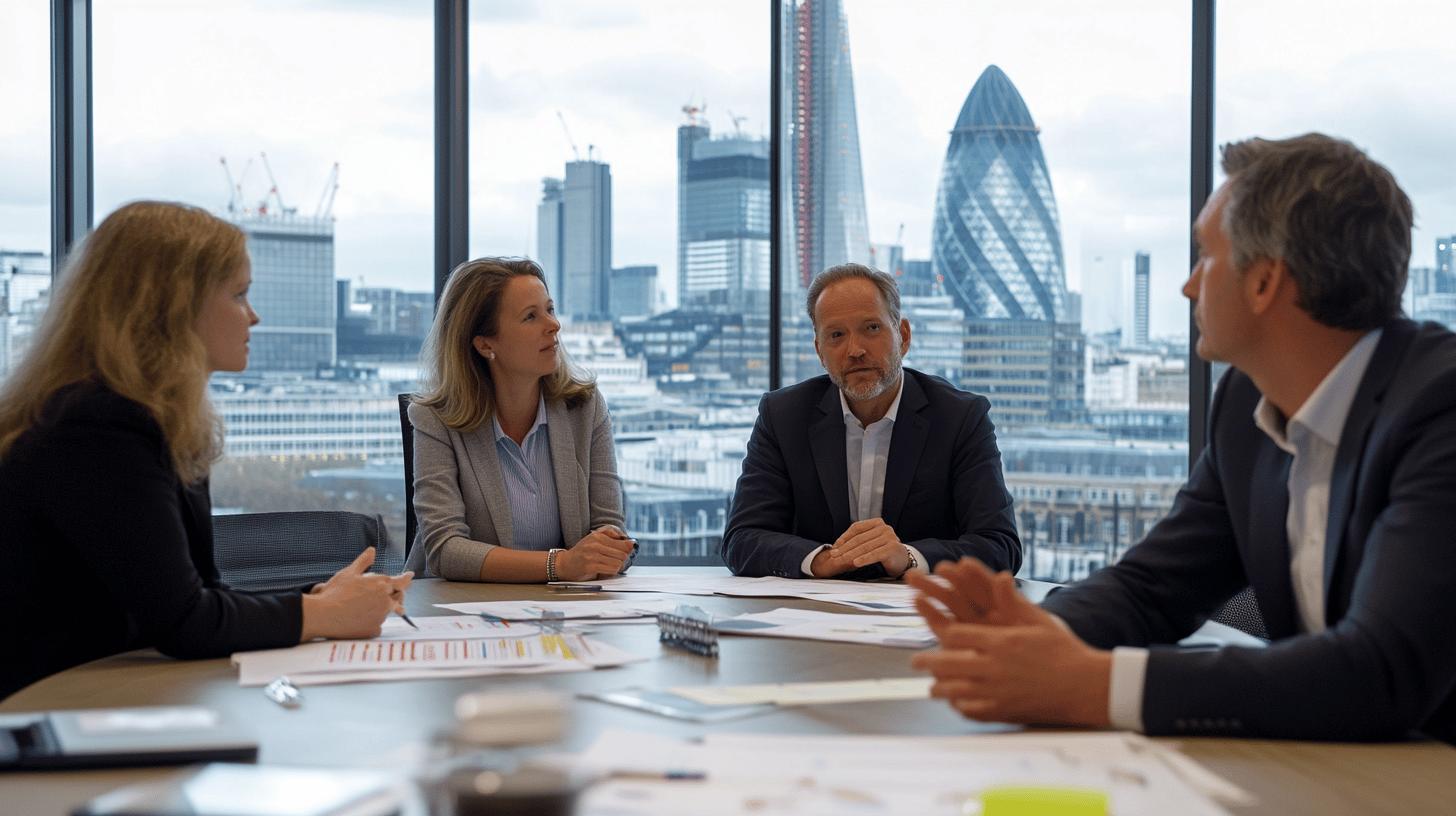
This structured framework creates clarity and builds resilience across your supply chain. As demonstrated in the Scottish Leather Group case study, digital compliance management tools can effectively unify processes across multiple sites while streamlining ISO standard adherence.
Technology as the Compliance Catalyst
Technology has revolutionised safety compliance in retail sourcing. Contractor management systems consolidate certifications, training records, and incident histories into accessible platforms. This reduces manual workload while ensuring critical compliance requirements remain visible. For example, Weston Aerospace implemented Q-Hub's Process Hub to digitise business-critical workflows, including NCR management and CAPA processes.
Compliance monitoring tools offer real-time tracking of safety protocols throughout the supply chain. When suppliers deviate from agreed standards, the system immediately flags issues for swift correction. This proactive approach improves risk visibility while keeping all stakeholders accountable.
Reporting tools generate detailed performance analysis, simplifying audit demonstrations and regulatory inspections. These insights help identify trends across suppliers, enabling targeted interventions for recurring issues.
<table border="0"> <tr><th>Compliance Aspect</th><th>Before Digital Systems</th><th>With Q-Hub Solutions</th></tr> <tr><td>Audit Preparation</td><td>Days/weeks of manual work</td><td>Hours with automated systems</td></tr> <tr><td>Compliance Visibility</td><td>Fragmented across systems</td><td>Centralised real-time dashboards</td></tr> <tr><td>Issue Resolution</td><td>Delayed by manual tracking</td><td>Accelerated by automated workflows</td></tr> </table>Automation significantly reduces manual errors while providing real-time insights that make compliance second nature. When decisions rely on accurate, current data, businesses maintain safety standards confidently throughout their supply chains.
Building a Culture of Continuous Improvement
Continuous improvement drives effective compliance management. Setting performance benchmarks provides clear, measurable standards that define success. For example, evaluating suppliers on maintaining ISO certifications or achieving zero incidents over defined periods ensures expectations remain quantifiable.
When compliance gaps emerge, structured Performance Improvement Plans (PIPs) create focused roadmaps for addressing shortcomings. These plans outline targeted training, timeline-based corrective actions, and regular progress reviews that transform challenges into growth opportunities.
Collaborative approaches foster shared accountability by engaging partners in open dialogue and joint problem-solving. As shown in BMC Analysis's implementation of Q-Hub solutions, this collaborative approach significantly improved audit processes and compliance while streamlining NCR management.
Regular benchmarking against industry standards helps identify relative performance positions and motivates suppliers to meet or exceed norms. This comparative approach continually raises standards across the supply chain.
Real-World Success: Digital Transformation of Compliance
Successful implementation cases demonstrate how technology and collaboration strengthen supplier compliance strategies. One UK retailer adopted a digital auditing system for supplier oversight after struggling with manual tracking methods. This platform enabled real-time data collection and automated compliance checks, yielding impressive results.
Within one year, the retailer reduced workplace incidents linked to supplier non-compliance by 30%. Audit preparation time decreased by 40%, significantly improving regulatory responsiveness. Enhanced supply chain transparency allowed proactive risk identification and management.
Another multinational retailer addressed safety compliance gaps across its complex global supply chain by implementing a collaborative partnership programme. Through joint workshops and co-developed safety protocols, the company created standardised approaches applicable across regions. This collaborative model reduced compliance violations by 25% within two years, while audit scores improved by 15%.
Q-Hub's digital solutions have transformed organisations like Rocal Insulating Panels, where paper-based systems were causing inefficiencies in safety management. By centralising document control and automating accident reporting, the company dramatically improved visibility and accountability across departments.
Ready to strengthen your supplier and contractor management with Q-Hub's digital compliance solutions? Discover how our tailored software can transform your compliance processes from administrative burdens into strategic advantages while ensuring safety standards remain consistently high across your supply chain.