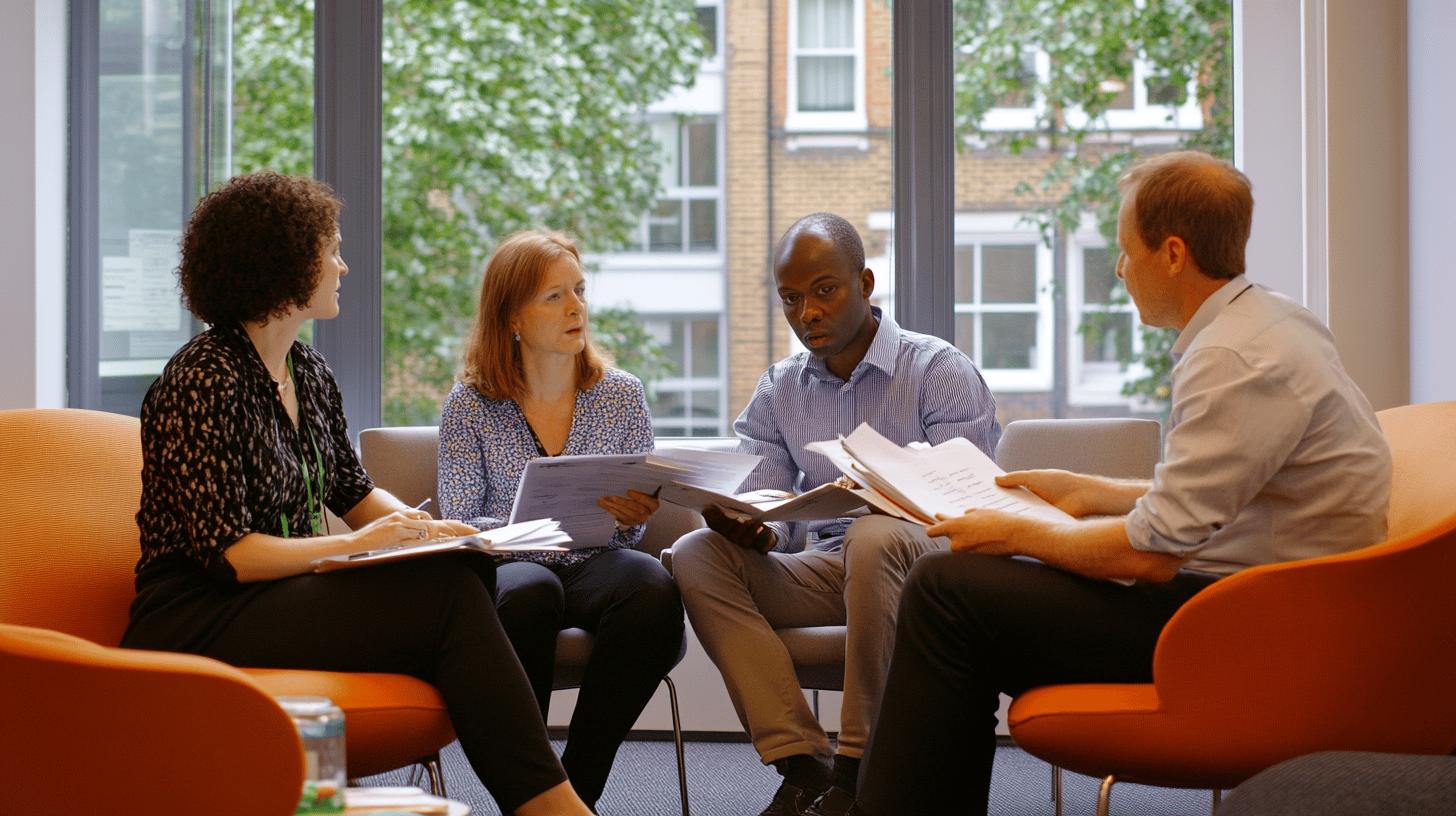
Supplier and Contractor Management Boosts Pharma Accuracy
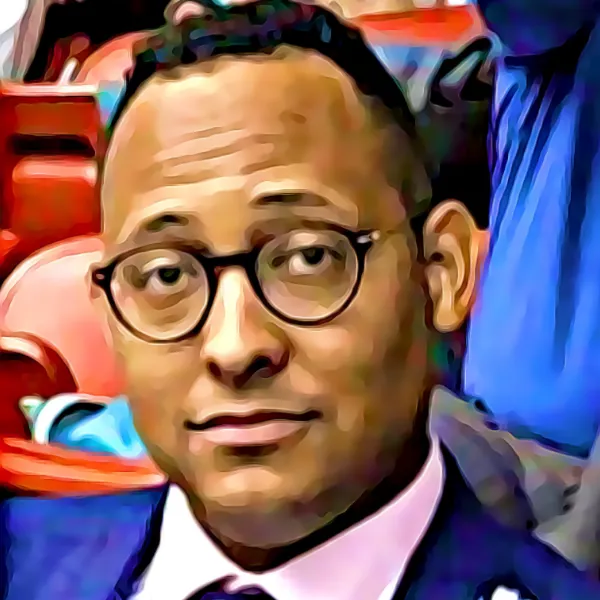
The Role of Supplier and Contractor Management in Enhancing Incident Reporting Accuracy in Pharma Operations
Supplier and contractor management plays a pivotal role in improving incident reporting accuracy in pharmaceutical operations. When properly managed, external partners become integral to maintaining compliance with stringent regulatory standards like GMP and ISO. Ineffective oversight, however, can lead to inaccurate reporting, exposing organisations to non-compliance risks, costly product recalls, and reputational damage. The stakes are high—with MHRA penalties exceeding £1 million in some cases—making precision in incident reporting essential for operational success.
Building Frameworks That Ensure Accountability
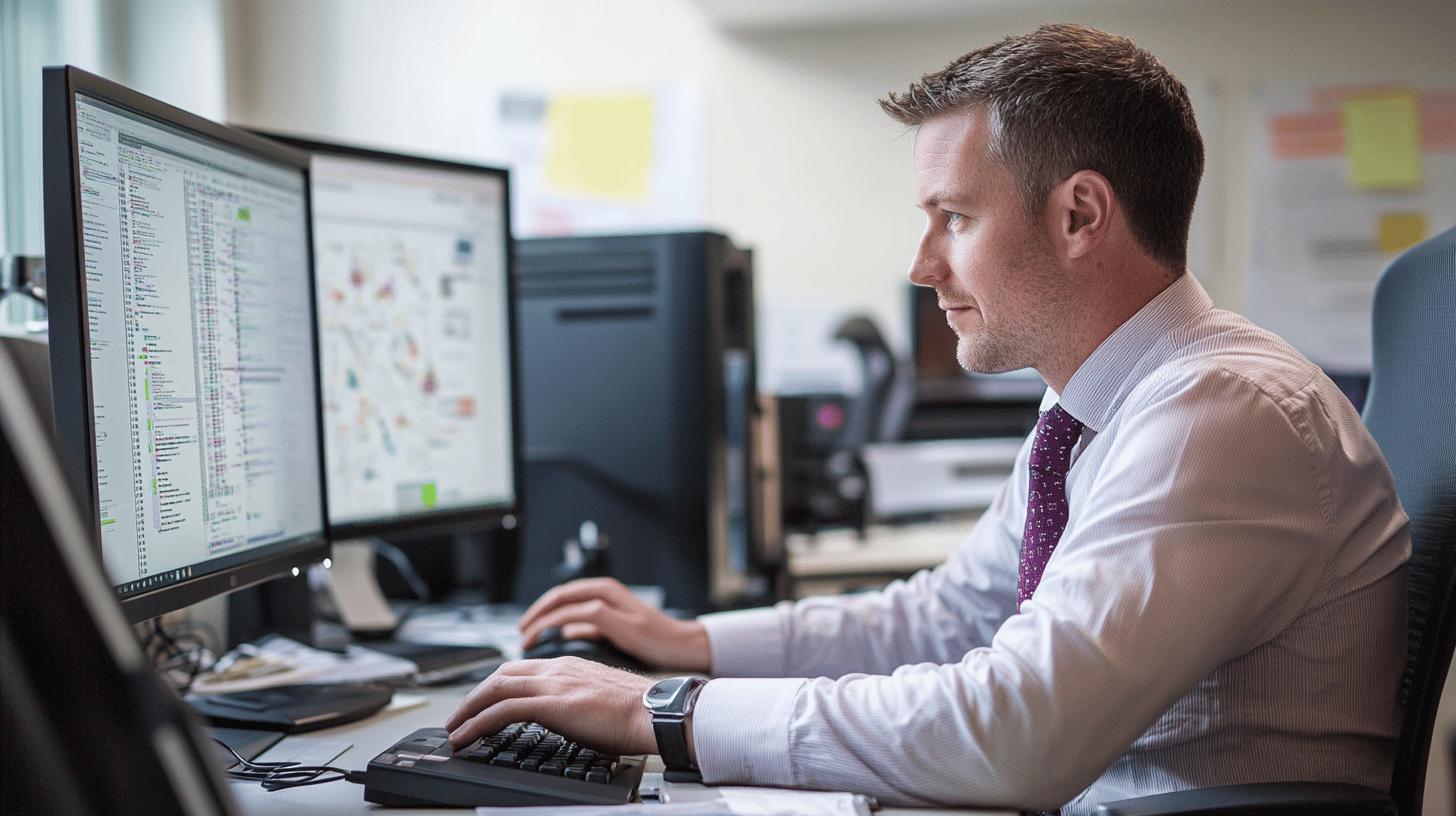
Effective management of external partners requires implementing clear guidelines, robust communication channels, and standardised reporting protocols. This creates a framework ensuring all parties understand their responsibilities around incident documentation. When suppliers and contractors are held accountable through these processes, reporting becomes not only more accurate but also faster.
Q-Hub's digital solutions help pharmaceutical companies create these frameworks by providing centralised systems where reporting protocols are clearly defined and easily accessible. As seen in the Scottish Leather Group case study, implementing structured digital solutions significantly improves compliance management across multiple ISO standards.
The implementation of a digital solution resulted in enhanced compliance management, with SLG now seamlessly managing multiple ISO standards within a single platform. Audit preparation time was significantly reduced, freeing resources for value-added activities.
Essential Practices for Strengthening Contractor Accountability
Clear contractual agreements form the foundation of accountability. These should outline specific requirements for incident reporting, including timelines, data accuracy standards, and escalation procedures. Service Level Agreements (SLAs) that define reporting protocols set performance baselines, allowing organisations to take corrective action when necessary.
Regular audits provide structured oversight of reporting practices. Companies conducting bi-annual audits typically see fewer instances of underreporting and faster incident resolution. These audits aren't just about identifying gaps—they create opportunities for continuous improvement that benefit both the organisation and its external partners.
Transparency in operations is equally critical. Open communication channels between stakeholders can significantly reduce documentation discrepancies. Companies adopting transparent practices often see a 30% improvement in compliance and a 20% reduction in underreporting.
Technology Solutions That Transform Reporting Accuracy
Digital solutions have revolutionised how pharmaceutical companies manage incident reporting with external partners. These systems automate workflows, eliminating manual errors and enhancing data accuracy. Customisable software that integrates supplier and contractor data can reduce documentation errors by as much as 25%—significant in such a tightly regulated industry.
Quality management systems (QMS) provide another layer of precision by centralising compliance reporting and enabling audit trails. These platforms are particularly valuable for meeting regulatory demands outlined by MHRA or ISO standards. Studies show digital QMS tools can cut documentation time by up to 30%, freeing resources and ensuring quicker resolutions during audits or inspections.
- Automated workflow systems eliminate manual errors and standardise reporting formats
- Real-time tracking capabilities ensure incidents are logged, monitored, and escalated without delays
- Predictive analytics can identify patterns in incident data, allowing proactive issue management
- Integrated performance metrics allow monitoring of compliance trends across suppliers
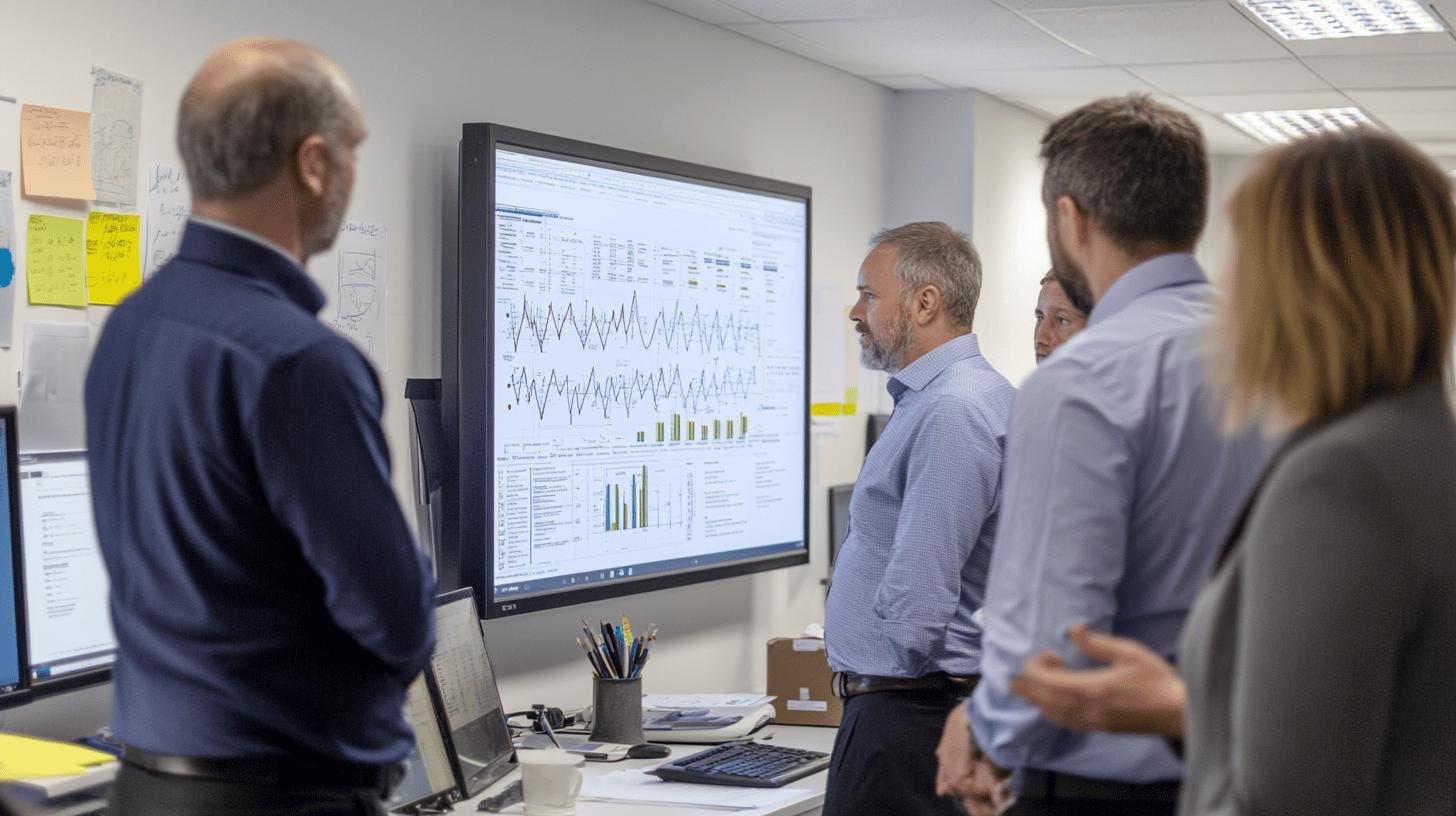
The transformation Anglia Cathodic Protection experienced after implementing Q-Hub's digital platform demonstrates these benefits. Their previous paper and spreadsheet-based systems created fragmented processes and limited visibility. After digitising their system, they achieved streamlined non-conformance tracking and enhanced audit capabilities, saving hours of administrative work while improving compliance visibility.
<table border="0"> <tr><th>Reporting Aspect</th><th>Before Digital Solutions</th><th>After Q-Hub Implementation</th></tr> <tr><td>Document Control</td><td>Fragmented across spreadsheets and paper</td><td>Centralised digital library with version tracking</td></tr> <tr><td>NCR Resolution Time</td><td>Days/Weeks</td><td>Hours/Days</td></tr> <tr><td>Audit Preparation</td><td>Manual, time-consuming process</td><td>Automated scheduling and real-time reporting</td></tr> <tr><td>Stakeholder Visibility</td><td>Limited, often delayed</td><td>Real-time access across departments</td></tr> </table>The Critical Role of Regulatory Compliance
Supplier and contractor management is inseparable from regulatory compliance in pharmaceutical operations. Standards such as GMP and ISO require detailed documentation, audit trails, and corrective action plans. GMP guidelines mandate thorough reporting and investigation of all deviations, while ISO standards emphasise consistent processes across the supply chain.
The consequences of non-compliance are severe. Beyond financial penalties, companies face product recalls and reputational damage that erode market confidence and patient trust. Aligning suppliers and contractors with compliance standards requires setting clear expectations and verifying compliance through regular audits and performance reviews.
Integrating External Partners Seamlessly Into Reporting Ecosystems
Successful integration starts with clear communication. Every stakeholder must understand their role in the reporting process. Regular meetings serve as checkpoints for discussing challenges, reviewing performance, and ensuring protocol compliance. Organisations using collaborative frameworks typically see a 15% reduction in incident resolution times.
Training bridges operational gaps between different systems and workflows. Sessions focusing on specific reporting tools, data requirements, and regulatory standards significantly improve data quality and reduce delays. Collaborative platforms centralise data submission, track incident progress, and flag reporting delays, providing comprehensive performance visibility.
Key Elements of Successful External Partner Integration
1. Establish clear roles and responsibilities for all stakeholders
2. Provide targeted training on reporting tools and requirements
3. Implement collaborative digital platforms for centralised management
4. Use regular performance reviews to maintain accountability
5. Develop escalation procedures for addressing issues promptly
Uncovering Root Causes For Lasting Improvements
Root cause analysis (RCA) allows pharmaceutical companies to move beyond surface issues and identify fundamental problems leading to incidents. Techniques like the "Five Whys" method and fishbone diagrams help categorise potential causes into areas such as processes, equipment, or human error.
Once identified, corrective actions address root causes to prevent recurrence. These might include process changes or training programmes targeting specific skill gaps. For example, if reporting errors stem from inconsistent data entry practices among contractors, standardising input protocols and providing training can resolve the issue while strengthening the overall reporting framework.
Companies employing robust RCA techniques have reduced repeat incidents by 20%. This approach transforms incident investigation from a reactive measure into a proactive strategy for continuous improvement, creating a stronger culture of accountability throughout the supply chain.
Fostering Continuous Improvement Through Data-Driven Insights
Continuous improvement in supplier and contractor management requires structured approaches to refining relationships and processes. Performance benchmarks like incident frequency, resolution times, and audit outcomes provide tangible indicators for measuring progress. Tracking these metrics can reveal recurring issues and highlight areas needing additional attention.
Regular performance reviews create opportunities for constructive feedback and collaboration. Quarterly evaluations discussing compliance gaps, reporting successes, and areas for improvement ensure suppliers and contractors remain accountable for their contributions to incident management.
Data analysis uncovers systemic issues by examining trends in reporting data. This information helps tailor compliance programmes and adjust workflows for optimal performance. Q-Hub's digital solutions provide the analytics capabilities needed to drive these insights, enabling pharmaceutical companies to make data-driven decisions that enhance reporting accuracy.
Fowlers of Bristol's experience with Q-Hub demonstrates how centralising communication and data management transforms reporting accuracy. By bringing critical workflows, datasets, and communications into a single digital space, they achieved instant access to real-time data, fostering collaboration between teams and significantly reducing errors.
Ready to transform your supplier and contractor management for enhanced incident reporting accuracy? Q-Hub offers tailored digital solutions that streamline compliance, improve accountability, and drive operational excellence in pharmaceutical operations.
<