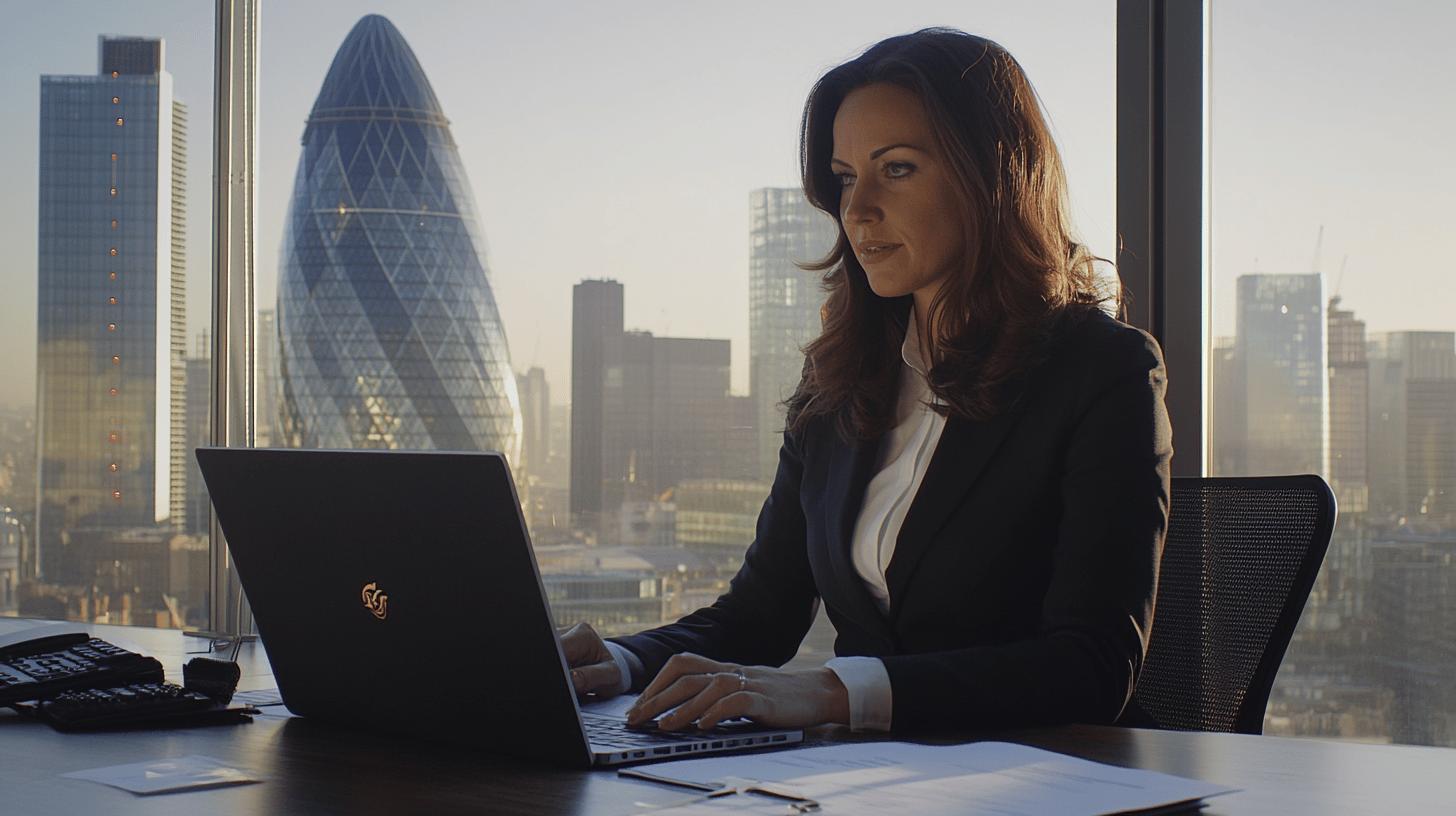
Supplier and Contractor Management: Boosting Compliance in Facilities
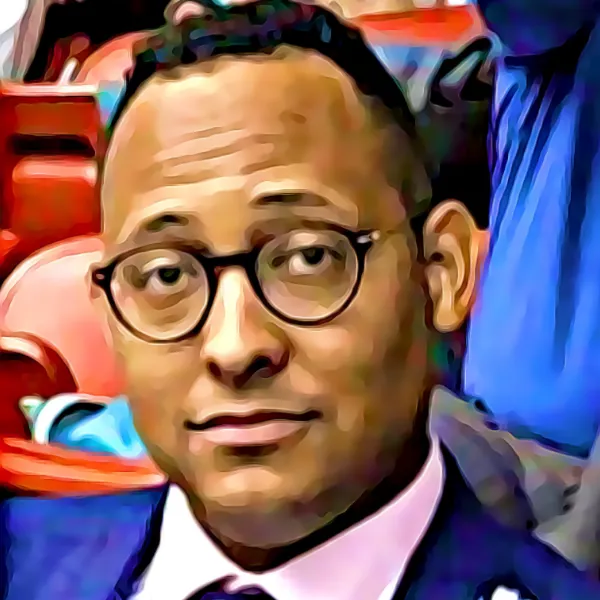
Importance of Supplier and Contractor Management in Facilities Management Partnerships
Effective supplier and contractor management isn't just administrative overhead—it's the backbone of successful facilities management operations.
When organizations adopt a proactive approach, supplier and contractor management becomes a strategic lever. This process not only streamlines partner relationships but also sets the stage for enhanced compliance and operational excellence, echoing the article’s emphasis on structured and risk-mitigated vendor partnerships. When partnerships align with compliance standards, organisations achieve both regulatory adherence and operational excellence. Q-Hub recognises that in today's fast-paced facilities management landscape, where margins are tight and deadlines critical, strong vendor relationships directly impact bottom-line performance and risk mitigation.
Well-managed facilities management partnerships do more than tick compliance boxes—they create strategic advantages. When suppliers and contractors understand and follow frameworks like the Health and Safety at Work Act or ISO standards, organisations enjoy streamlined operations, reduced compliance risks, and enhanced project continuity. Conversely, fragmented supply chain management inevitably leads to delays, compliance gaps, and unnecessary costs.
The most successful facilities management operations understand that contractor compliance isn't a burden—it's a competitive advantage that drives efficiency and reduces organisational risk.
Here's what robust supplier and contractor management delivers:
- Stronger vendor relationships built on clear expectations and trust
- Streamlined procurement with reduced administrative burden
- Enhanced compliance with relevant safety and environmental standards
- Proactive risk management through consistent oversight
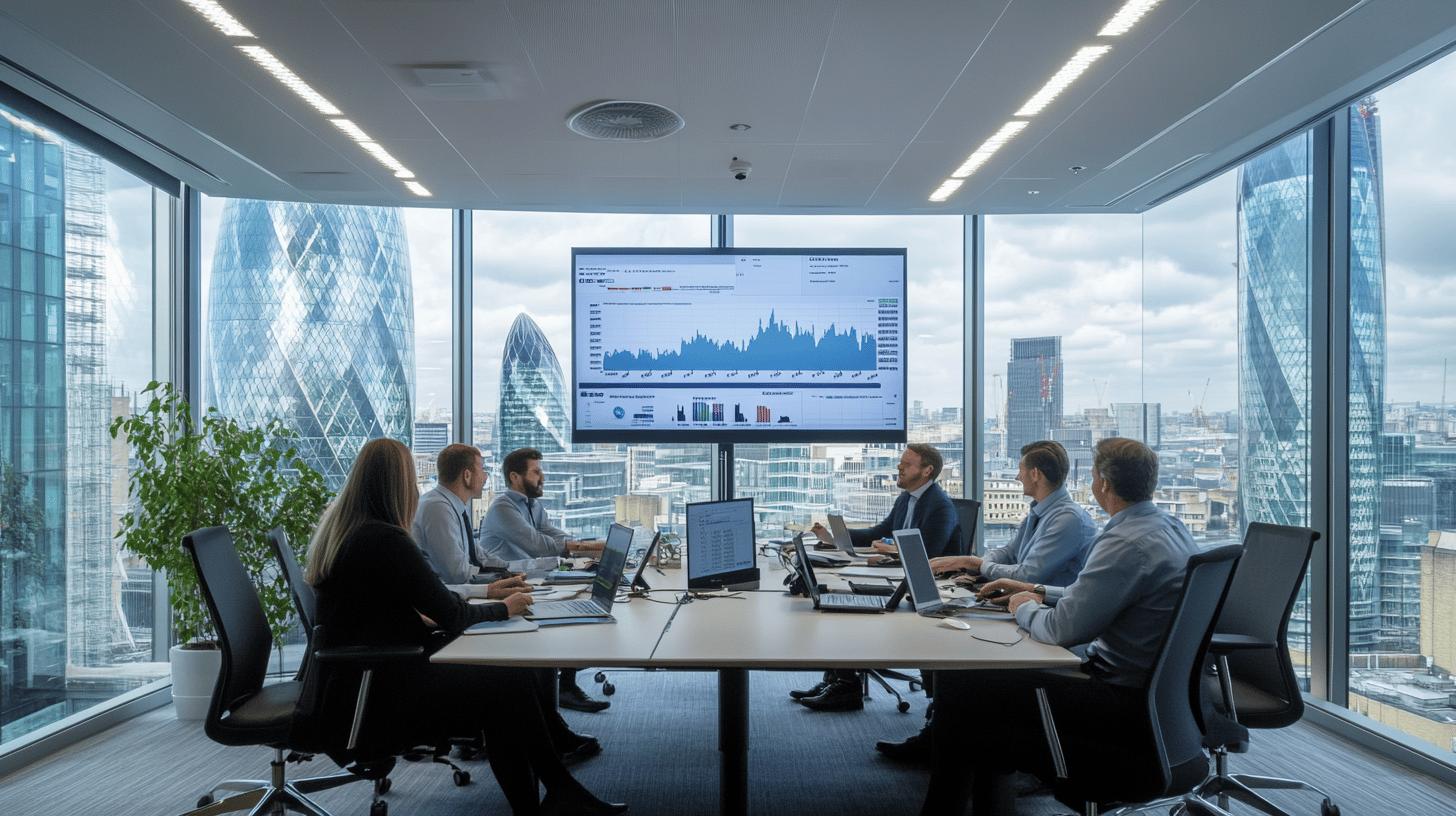
Understanding Essential Compliance Frameworks
Successful facilities management partnerships rely on clear compliance frameworks. The stakes are significant—non-compliance doesn't just disrupt operations, it exposes organisations to substantial legal and financial consequences that can impact long-term viability.
The Health and Safety at Work Act 1974 forms the cornerstone of compliance requirements, mandating that organisations ensure safety across all operational touchpoints. For facilities managers, this means selecting contractors who actively implement these standards throughout project lifecycles. Similarly, the Building Safety Act 2022 establishes critical requirements for structural integrity and fire safety assessments.
What happens when these standards aren't met? The answer is straightforward: accountability flows upward. Non-compliance can trigger regulatory penalties, legal actions, and even operational shutdowns. However, compliance isn't just about avoiding negative outcomes—it strengthens operational resilience and creates more predictable project execution.
Documentation Systems That Drive Compliance Success
Proper documentation isn't bureaucratic busywork—it's evidence that partnerships meet regulatory requirements.
Integrating robust data management solutions further enhances this framework by ensuring that all compliance documentation is accurately maintained and easily retrievable. This addition not only reinforces the importance of digital transformation in facilities management but also supports the strategic tracking and management of regulatory requirements. Contractor certifications like ISO 9001 (quality management) and ISO 45001 (occupational health and safety) demonstrate commitment to standardised best practices that reduce operational risks.
Maintaining current compliance documentation—from safety audits to risk assessments and insurance records—provides the verification backbone needed during regulatory inspections or dispute resolution. Without systematic documentation, organisations cannot demonstrate compliance when it matters most.
Key compliance standards and their corresponding frameworks include:
<table border="0"> <tr><th>Compliance Area</th><th>Legal Framework</th><th>Impact on Partnerships</th></tr> <tr><td>Health and Safety</td><td>Health and Safety at Work Act 1974</td><td>Establishes baseline safety requirements for all operations</td></tr> <tr><td>Building Safety</td><td>Building Safety Act 2022</td><td>Mandates structural and fire safety assessments</td></tr> <tr><td>Quality Management</td><td>ISO 9001</td><td>Creates standardised quality processes across partnerships</td></tr> <tr><td>Occupational Safety</td><td>ISO 45001</td><td>Establishes workplace safety systems and accountability</td></tr> </table>Building Effective Supplier Management Systems
Strategic supplier management requires a structured approach focused on compliance, quality, and risk reduction. When implemented effectively, these systems transform vendor relationships from transactional interactions into true partnerships that drive business value.
The foundation begins with clear qualification criteria—specific benchmarks for certifications, experience, and safety performance that ensure partners can meet both regulatory and operational requirements. However, initial qualification is just the starting point; continuous oversight maintains standards throughout the relationship lifecycle.
Organizations should implement these proven best practices to strengthen their contractor management:
- Define clear qualification protocols that establish minimum standards for certifications, safety records, and operational capabilities
- Implement regular supplier audits to verify ongoing compliance with standards like ISO 9001 and ISO 45001
- Track performance through objective metrics including delivery timeliness, quality outcomes, and safety incidents
- Create accountability frameworks with clearly assigned responsibilities and defined consequences for non-compliance
- Deploy digital management tools that automate compliance monitoring and contract oversight
- Establish transparent communication channels to address compliance concerns proactively
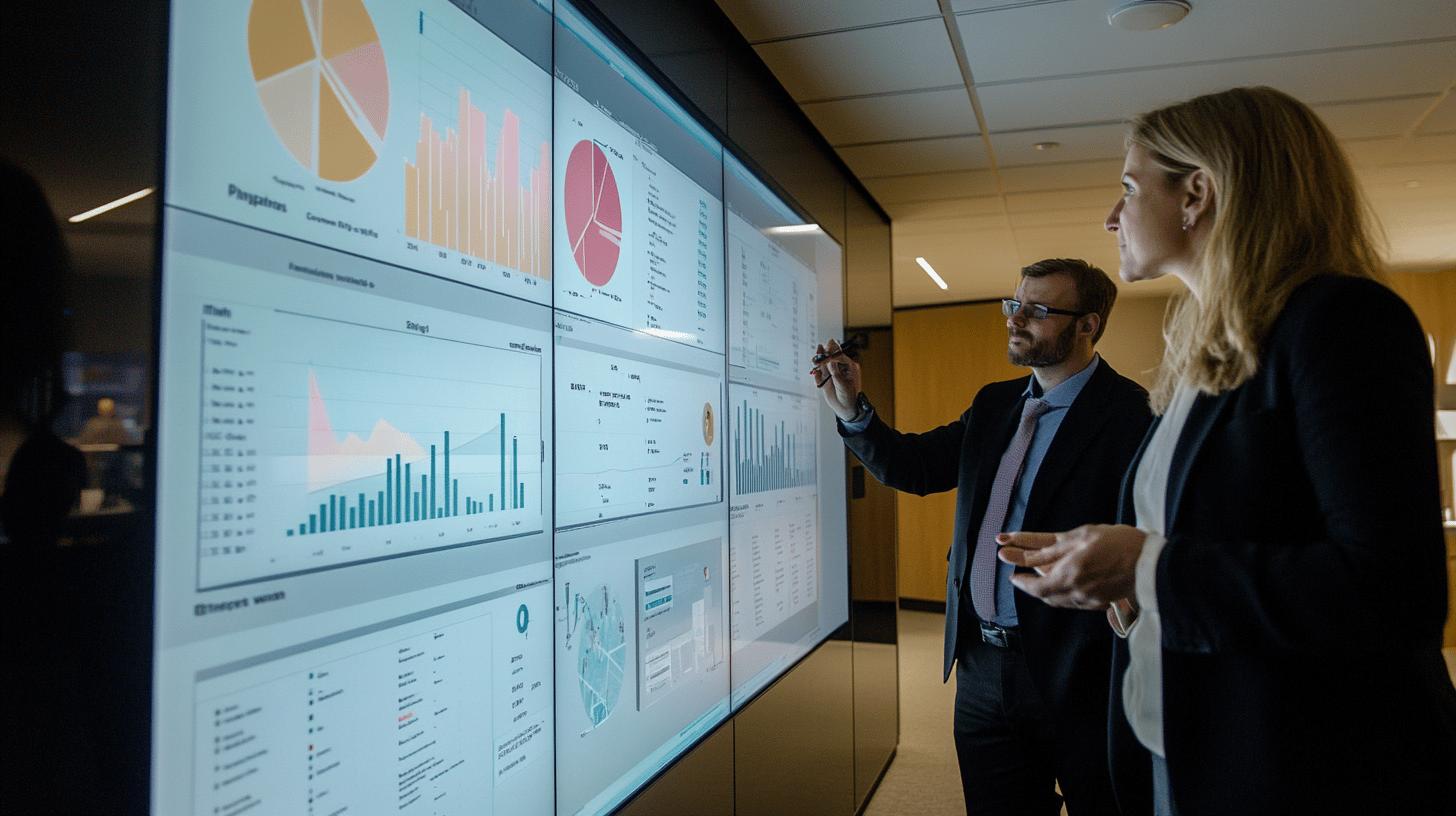
Leveraging Technology for Compliance Excellence
Modern supplier management increasingly relies on digital tools that transform compliance from a manual burden into a streamlined, automated process. These technologies do more than ensure adherence to standards—they enhance efficiency, improve visibility, and strengthen accountability across the entire supply chain.
What makes these tools valuable in facilities management? Their ability to automate routine tasks, monitor performance in real-time, and consolidate documentation in accessible systems. Contract management platforms automatically track regulatory clauses, while audit management tools flag compliance gaps before they become significant issues.
Q-Hub's Audit Hub exemplifies this approach, as seen in their work with the Scottish Leather Group. By implementing digital audit management across multiple ISO standards, Q-Hub helped transform compliance from a resource-intensive task to a streamlined operation that freed staff to focus on high-value activities. This digitised approach reduced audit preparation time from days to hours while improving documentation quality.
Developing Risk-Focused Partnership Strategies
Without robust risk management, supplier and contractor relationships can become compliance vulnerabilities. Structured risk assessment and proactive mitigation measures ensure every partner operates within required parameters and contributes to organizational resilience rather than creating exposure.
Risk assessments provide systematic evaluation frameworks to measure vendor performance against compliance standards, such as ISO 9001 for quality management or ISO 45001 for occupational safety. These evaluations go beyond certifications to track real-world adherence to agreed standards.
Weston Aerospace demonstrates how this approach transforms operations. By adopting Q-Hub's Process Hub, they digitised critical workflows including non-conformance reporting (NCR) and corrective action processes. The system's built-in alerts and accountability tracking ensured compliance issues received prompt attention, significantly reducing resolution times and compliance risks.
Creating Systems for Continuous Improvement
Effective partnership management isn't a one-time setup—it requires ongoing assessment and refinement. Continuous improvement processes ensure relationships remain compliant, efficient and aligned with evolving business needs.
Setting clear, measurable success metrics provides the foundation for evaluation. These benchmarks—from delivery schedule adherence to health and safety compliance rates—generate actionable insights that drive targeted improvements. When gaps emerge, structured performance improvement plans create accountability and clear paths to resolution.
For example, Fowlers of Bristol transformed their quality management approach through Q-Hub's dashboard systems. By implementing "Zero Defects" tracking with integrated compliance metrics, they gained visibility into performance patterns and could address issues proactively rather than reactively.
Building Compliance Through People and Communication
The most sophisticated compliance systems ultimately depend on people understanding requirements and communicating effectively. Training and clear communication channels transform compliance from an imposed requirement into a shared commitment across the partnership network.
Structured training programmes ensure all parties understand both regulatory requirements and organizational expectations. When contractors receive focused training on areas like contract management, documentation requirements, and safety protocols, they become active participants in compliance rather than passive recipients of rules.
BMC Analysis demonstrates this principle through their implementation of Q-Hub's document control systems. By digitising document acknowledgment processes, they created transparent confirmation trails showing that partners had received, reviewed and understood critical compliance information—dramatically reducing communication gaps and compliance risks.
Effective supplier and contractor management creates cascading benefits across facilities management operations. From streamlined compliance to reduced operational risks and improved partnership quality, these systems transform administrative requirements into strategic advantages. Q-Hub's digital compliance solutions help organisations achieve this transformation by automating routine tasks, enhancing visibility, and creating accountability frameworks that drive continuous improvement across the entire supplier ecosystem.