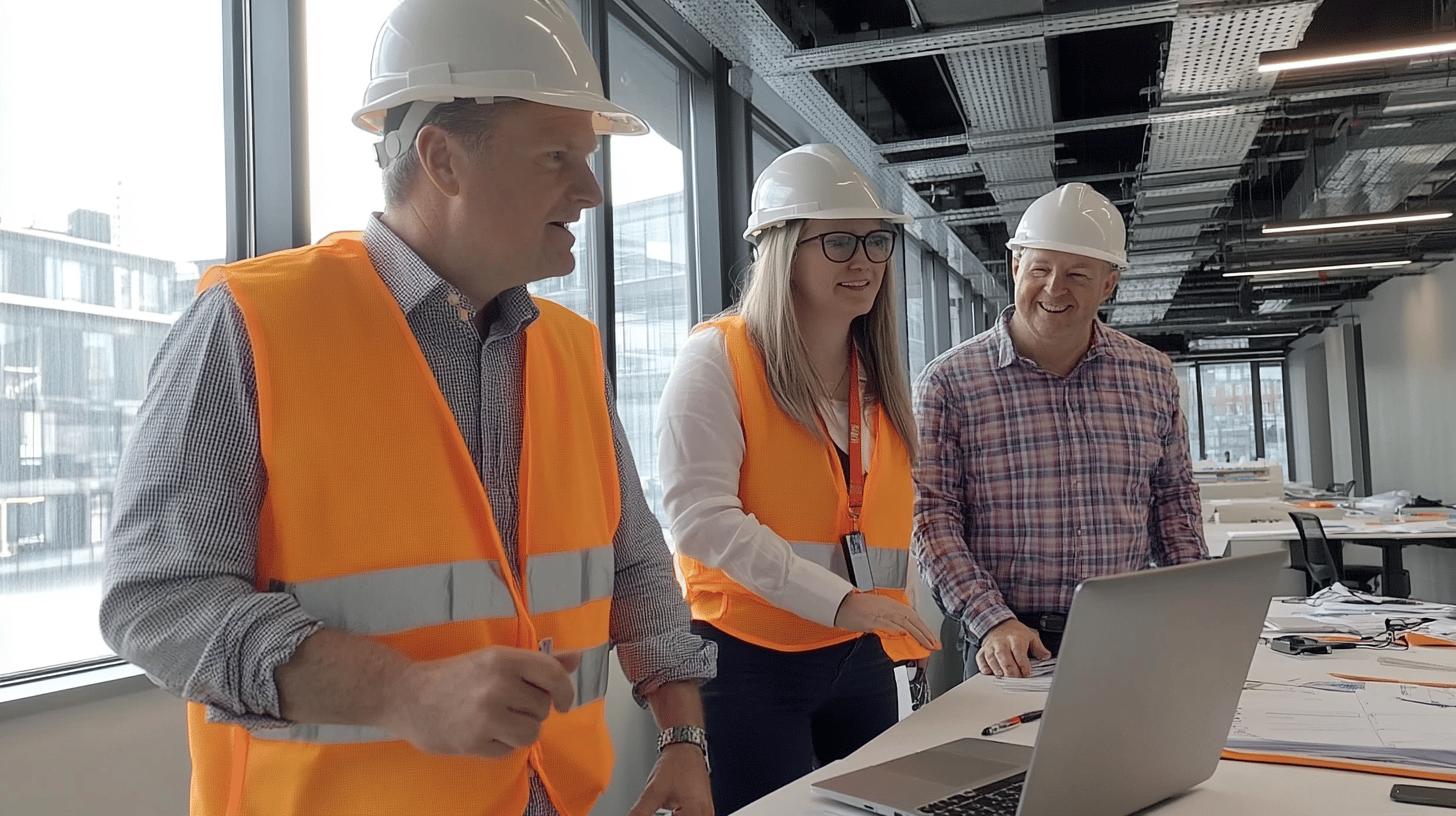
Enterprise Safety Management Solutions Enhancing Secure Workplaces
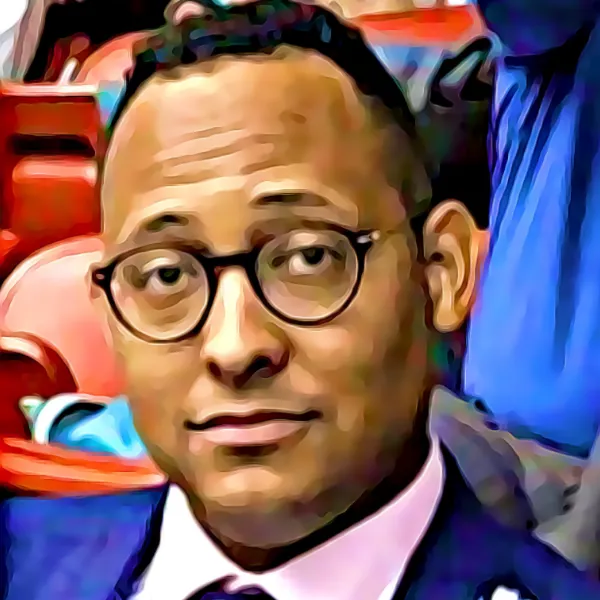
The Importance of Enterprise Safety Management Solutions in Securing Facilities and Workplaces
Enterprise safety management solutions are crucial for organisations seeking to protect workers and facilities effectively. These systems help identify, mitigate, and manage risks across operations through automation and enhanced compliance capabilities. Q-Hub's tailored safety management platforms transform outdated manual processes into streamlined digital workflows, ensuring nothing falls through the cracks. By integrating with existing infrastructure, these solutions form the backbone of modern safety strategies, particularly as facilities management grows increasingly complex.
In the UK, compliance with the Health and Safety at Work Act 1974 demands comprehensive risk assessments and robust safety measures. Modern safety platforms simplify this by leveraging real-time data to identify potential hazards before incidents occur. When IoT sensors detect a faulty component that could cause an accident, proactive intervention becomes possible, protecting employees while reducing operational disruptions and costs.
- Real-time hazard identification
- Centralised documentation for compliance
- Enhanced emergency preparedness
- Improved training and awareness
- Streamlined incident reporting
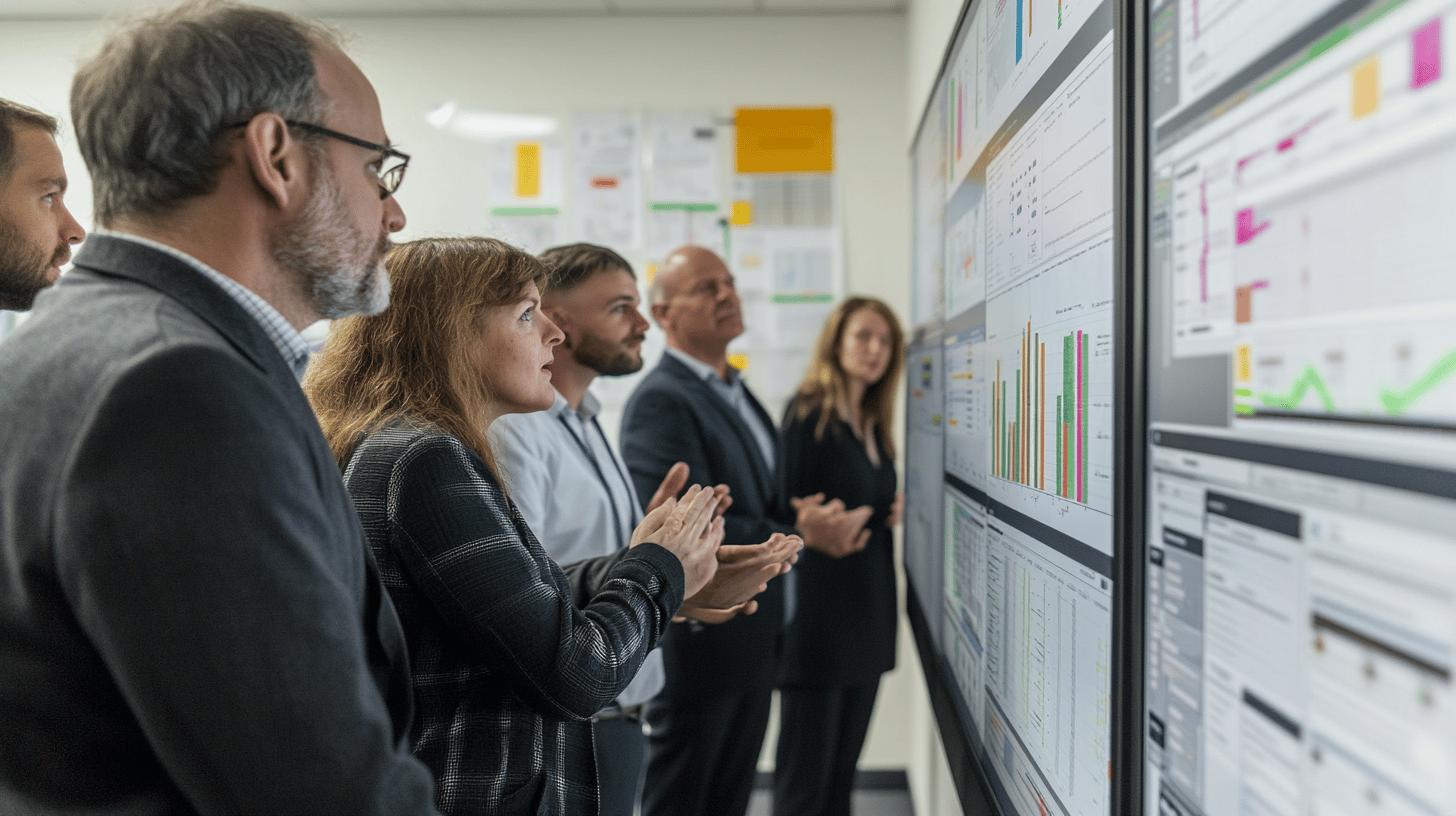
Transforming Safety Through Digital Innovation
Safety management systems create secure workplaces by integrating advanced technologies with practical risk management approaches. Scottish Leather Group faced significant challenges managing compliance across multiple sites before implementing Q-Hub's solution. Their paper-based systems struggled to keep pace with ISO standards requirements, consuming valuable resources and hindering interdepartmental communication.
The implementation of Qhub resulted in transformative outcomes. SLG now seamlessly manages multiple ISO standards within a single platform. Audit hub has significantly reduced audit preparation time, freeing resources for value-added activities.
By digitising processes, organisations move beyond reactive measures to embrace proactive safety approaches. Without these systems, companies find themselves constantly firefighting problems rather than preventing them, resulting in higher costs and increased risk to employees.
Streamlining Critical Safety Processes
Modern safety platforms excel at simplifying incident reporting and analytics. When an incident occurs, these systems enable immediate logging, categorisation, and escalation to relevant teams. Advanced analytics then identify patterns and high-risk areas, allowing organisations to implement preventative measures before issues escalate.
Compliance modules ensure organisations meet regulatory requirements by tracking adherence to standards and managing inspections. Automated reminders for upcoming audits and centralised documentation storage eliminate missed deadlines and lost records. This builds accountability while helping avoid costly penalties.
The integration capabilities of these systems provide unmatched flexibility in safety management. When a facility manager identifies a hazard during an audit, mobile-enabled technology allows immediate documentation, task assignment, and resolution tracking in real time, supporting better decision-making across teams.
<table border="0"> <tr><th>Safety Management Feature</th><th>Before Digital Solutions</th><th>After Q-Hub Implementation</th></tr> <tr><td>Audit Preparation</td><td>Days of manual work</td><td>Hours with automated tools</td></tr> <tr><td>Non-Conformance Tracking</td><td>Fragmented across emails</td><td>Centralised with automated alerts</td></tr> <tr><td>Document Control</td><td>Cluttered shared drives</td><td>Structured digital library</td></tr> </table>Implementation Success Factors: Building a Safety-First Culture
Implementing enterprise safety management requires leadership commitment and clear objectives. Weston Aerospace discovered this when tackling inefficiencies in their quality and compliance management. Their legacy systems failed to deliver actionable data, creating bottlenecks in key operations, while NCRs faced delays in resolution due to manual tracking.
The first critical step is gaining senior management approval and establishing measurable safety objectives. Leaders must actively communicate the importance of safety initiatives across the organisation, creating a shared purpose. Without this foundation, even the most sophisticated system will struggle to gain traction.
Effective employee training forms the backbone of successful implementation. BMC Analysis found this when they digitised their operations with Q-Hub, transforming how they managed NCRs, document acknowledgment, and asset calibration. Training programs should be tailored to specific roles—what a facility manager needs differs from what frontline workers require.
- Conduct a thorough needs analysis
- Define clear system requirements aligned with safety goals
- Develop role-specific training programs
- Launch with pilot testing in critical departments
- Schedule regular reviews to optimise performance
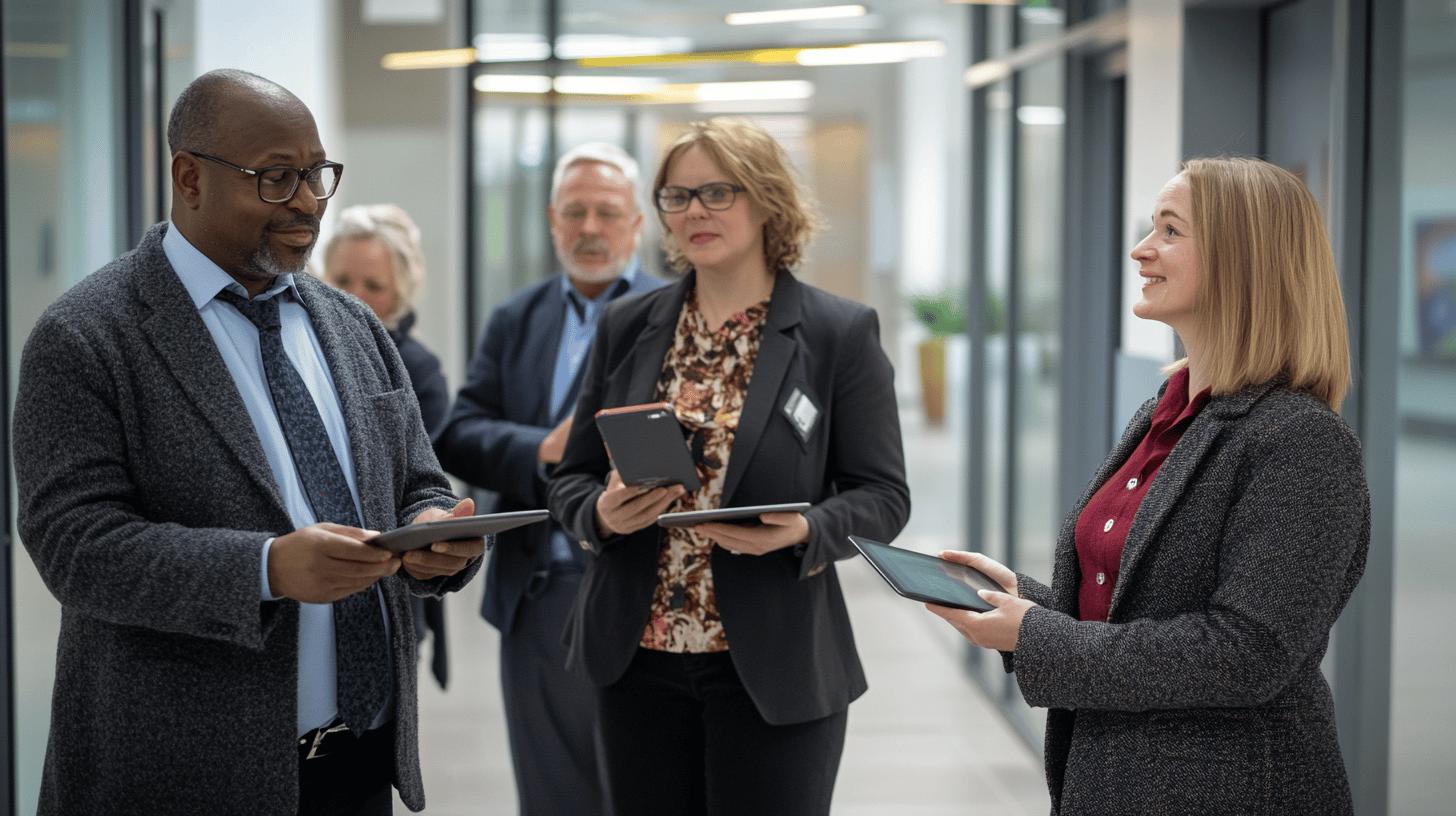
Leveraging Data for Proactive Risk Management
The power of analytics in identifying safety risks cannot be overstated. Advanced safety platforms collect and analyse data from multiple sources to reveal patterns that human observation might miss. Rocal Insulating Panels experienced this transformation when they partnered with Q-Hub to revolutionise their health and safety operations.
Before implementing a digital solution, Rocal relied on paper-based accident reporting and investigations, which led to incomplete records and lengthy delays. Q-Hub's automated workflows transformed their process, enabling quicker resolution and better departmental involvement. Reporting became faster and more detailed, with real-time access to all relevant information.
Emerging technologies like IoT sensors and AI systems are revolutionising safety management. IoT devices monitor conditions in real time, while AI analyses large datasets to uncover subtle risk patterns. Together, these technologies create a safety network that constantly evolves and improves, shifting organisations from reactive to proactive approaches.
Building Employee Engagement Through Digital Safety Tools
Employee training plays a pivotal role in bridging the gap between safety policies and practice. When Fowlers of Bristol implemented Q-Hub's safety platform, they transformed how teams communicated about safety issues. Before the change, their communication relied heavily on emails and in-person follow-ups, creating delays and inefficiencies.
Digital tools have revolutionised safety training delivery, making it more accessible and engaging. Modern platforms come equipped with interactive modules, real-time feedback mechanisms, and progress tracking. Gamified safety quizzes transform what might otherwise be dry topics into engaging activities that employees actually complete.
For Anglia Cathodic Protection, Q-Hub's ability to share documents and track "read and understood" acknowledgments transformed their safety culture. The entire workforce gained access to the tools and information needed to perform their roles effectively, improving compliance while fostering stronger accountability and engagement.
Measuring Real-World Safety Improvements
Determining if safety management solutions are truly effective requires tracking key performance indicators (KPIs) and conducting regular audits. By implementing centralised safety operations with intuitive dashboards, organisations gain visibility into near misses, daily inspections, and accident trends.
Consistent drops in incident rates indicate that preventative measures are working, while improved compliance scores reflect alignment with regulations. Safety audit processes help organisations uncover blind spots and refine strategies, ensuring programs evolve alongside changing workplace dynamics.
Employee feedback plays a crucial role in enhancing safety management effectiveness. Workers are often the first to notice gaps in protocols or training. By creating open channels for feedback, Q-Hub helps organisations identify overlooked hazards, refine training programs, and improve safety culture. This collaborative approach creates an environment where continuous improvement thrives.
As workplace safety requirements continue to evolve, Q-Hub's enterprise safety management solutions provide the flexibility and comprehensive capabilities organisations need to protect their people and facilities. By transforming manual processes into streamlined digital workflows, Q-Hub helps businesses not just comply with regulations but build truly safety-conscious cultures where prevention becomes second nature.