
Data Management Solutions Elevate Oil and Gas Reporting
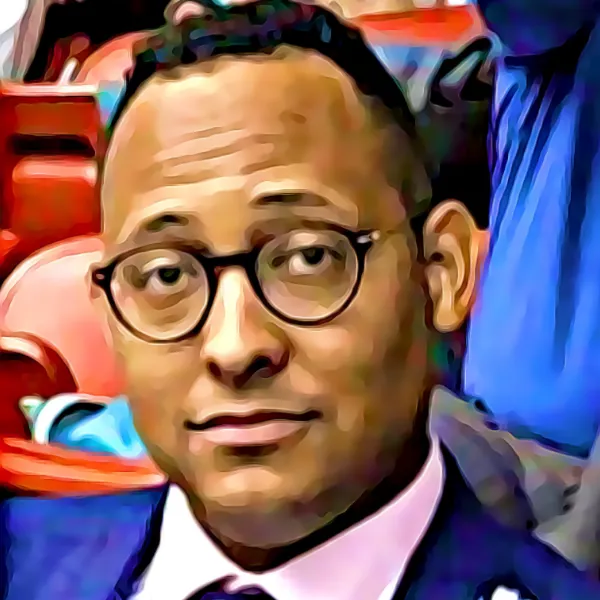
How Data Management Solutions Enhance Incident Reporting Accuracy in the Oil and Gas Sector
Data management solutions are revolutionising incident reporting accuracy in the oil and gas sector. By automating data collection and streamlining processes, these systems significantly reduce human error in safety documentation. Q-Hub's digital solutions transform fragmented reporting systems into cohesive frameworks that enhance precision and reliability in documenting critical safety events. Without proper data governance, inaccuracies cascade across teams, creating delays, compliance issues, and operational risks that high-stakes environments simply cannot afford.
Automation serves as the backbone of effective incident reporting. Real-time data capture ensures information is processed without delay, while integrated systems eliminate the silos that typically plague oil and gas operations. Advanced analytics add another layer of precision by identifying patterns, spotlighting potential risks, and predicting future hazards—empowering companies to shift from reactive to proactive safety management.
The difference between good and great safety performance often lies in data quality. When companies can trust their incident data, they make better decisions that save lives and protect assets.
Breaking Down the Barriers to Accurate Reporting
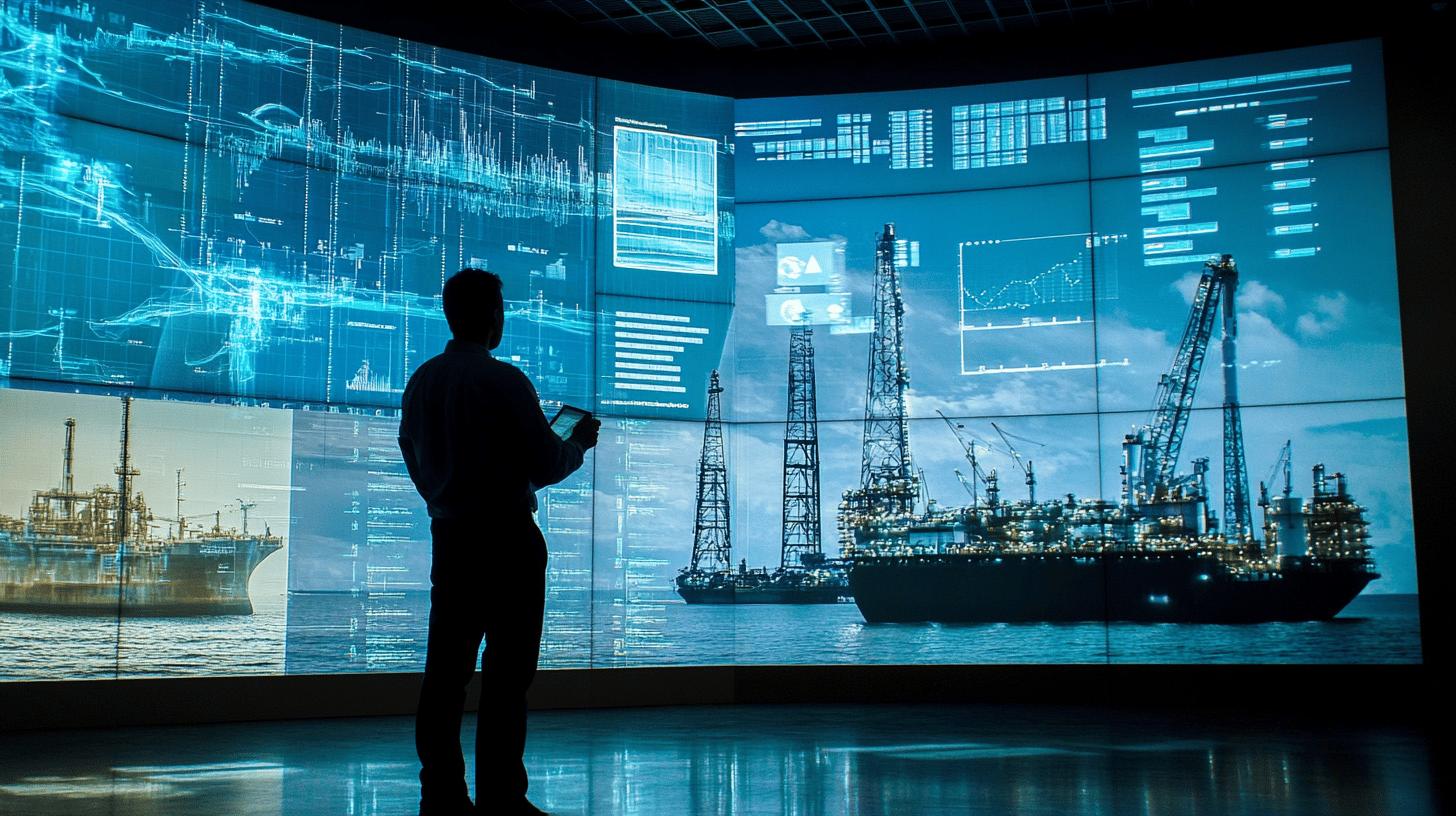
The oil and gas industry faces unique challenges in incident reporting. Data silos created by proprietary systems fragment critical safety information, while manual processes increase error risks and slow down documentation. These issues combine to create serious operational vulnerabilities in an industry where precision is non-negotiable.
Regulatory complexity adds another hurdle, as companies must constantly adapt to evolving compliance requirements like RIDDOR in the UK. High staff turnover and inadequate training leave teams ill-equipped to use reporting tools effectively, further compromising data quality when it matters most.
These challenges highlight why robust data management solutions have become essential for companies serious about safety and compliance. Let's examine how these systems address these critical pain points:
<table border="0"> <tr><th>Challenge</th><th>Traditional Approach</th><th>Q-Hub Solution</th></tr> <tr><td>Data Fragmentation</td><td>Information siloed across departments</td><td>Centralised platform with cross-functional visibility</td></tr> <tr><td>Manual Processing</td><td>Paper forms and spreadsheets</td><td>Automated workflows with digital validation</td></tr> <tr><td>Regulatory Compliance</td><td>Reactive adaptation to changes</td><td>Built-in compliance frameworks with automatic updates</td></tr> <tr><td>Training Inconsistency</td><td>Sporadic, one-size-fits-all approach</td><td>Role-specific guidance embedded in software</td></tr> </table>The Game-Changing Capabilities of Modern Incident Management
Advanced data management platforms are transforming how the oil and gas sector handles safety incidents. These systems go beyond basic documentation to provide actionable intelligence that prevents future incidents. Through predictive analytics, organisations can identify potential hazards before they materialise, shifting from reactive to proactive safety management.
IoT integration represents another leap forward in safety monitoring. Field sensors on critical equipment continuously transmit data to centralised platforms, enabling immediate anomaly detection without human intervention. This real-time capability is crucial in environments where conditions can change in seconds, eliminating dangerous blind spots in safety oversight.
Artificial intelligence further enhances reporting accuracy by processing vast data volumes to identify irregularities human operators might miss. When unusual readings occur in a pipeline, for instance, AI systems can detect the anomaly, correlate it with other data points, and suggest corrective actions—often preventing incidents entirely.
From Theory to Practice: Real-World Success Stories
The transformation from manual to digital incident reporting systems delivers measurable results. Scottish Leather Group demonstrates this shift clearly, having revolutionised their compliance management across multiple ISO standards using Q-Hub's platform. By implementing digital audit processes and centralised document control, they eliminated information silos while dramatically reducing preparation time for compliance audits.
Similarly, Weston Aerospace transformed their approach to managing Non-Conformance Reports (NCRs)—critical for incident tracking in aerospace manufacturing. Their previous manual methods led to delayed resolution and poor visibility. After implementing Q-Hub's Process Hub, they achieved automated tracking, faster resolution times, and comprehensive compliance reporting that previously required hours of manual effort.
These improvements aren't merely administrative—they translate directly to enhanced safety outcomes. Companies typically experience:
- 40-60% reduction in incident response times
- Near-perfect compliance rates with regulatory requirements
- Significant improvements in accurate environmental impact tracking
- Greater employee engagement in safety processes
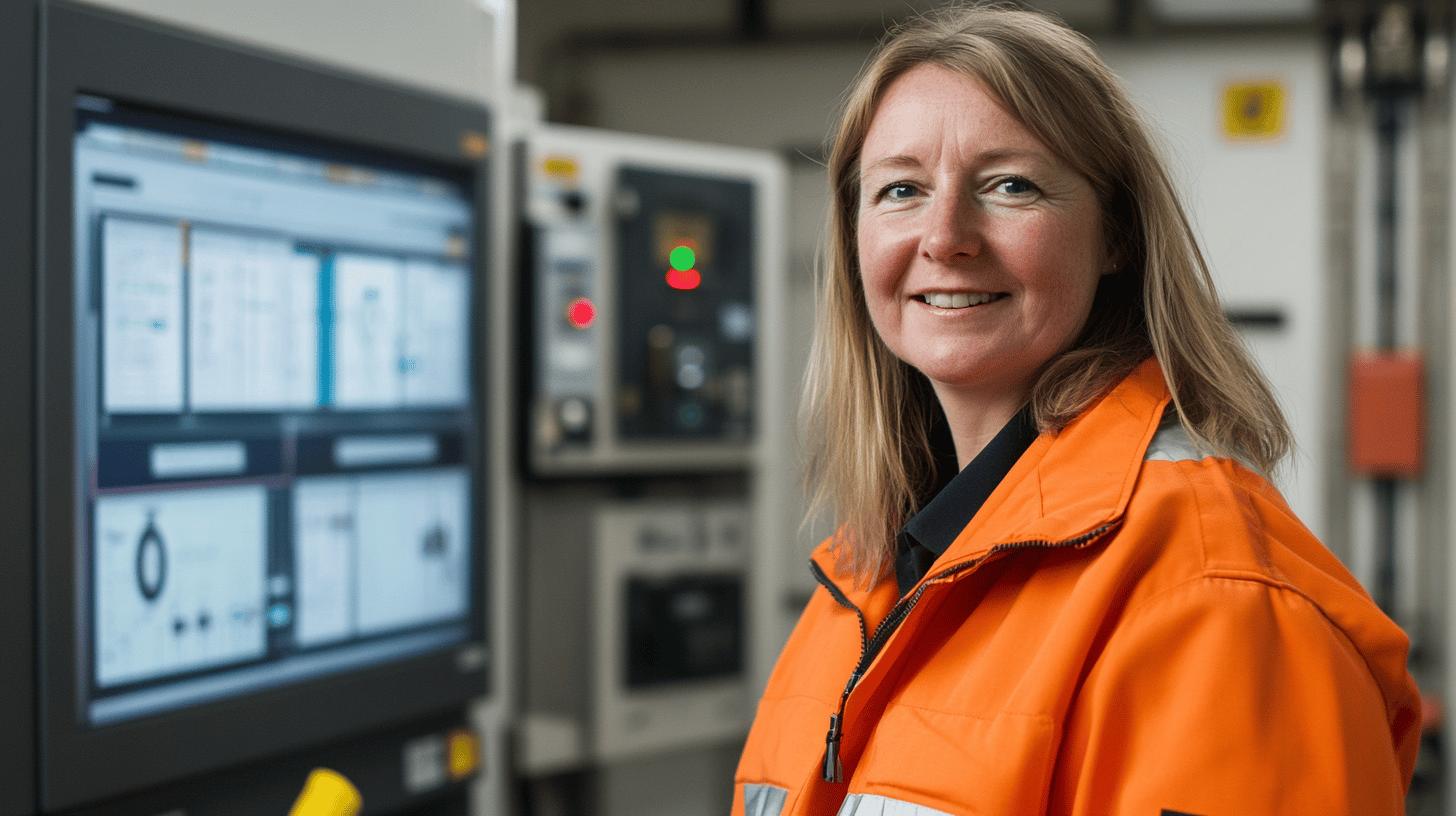
Practical Steps for Successful Implementation
Implementing effective data management solutions begins with a comprehensive audit of your current systems. This assessment reveals gaps and inefficiencies that might compromise your incident reporting accuracy. For instance, Rocal Insulating Panels discovered their paper-based accident reporting system created substantial delays and information gaps—issues they resolved by migrating to Q-Hub's digital platform.
Clear data governance policies prove equally vital for success. These frameworks define roles, responsibilities, and protocols for managing safety information—creating accountability at every level. When Fowlers of Bristol established these structures using Q-Hub, they saw immediate improvements in document control and reporting precision.
Employee training deserves particular attention when implementing new systems. BMC Analysis found that by focusing on user adoption through Q-Hub's intuitive interfaces, they achieved rapid uptake across departments—transforming their NCR management from a fragmented process to a streamlined workflow with built-in accountability.
Embracing the Digital Future of Safety Management
Digital transformation is fundamentally changing how the oil and gas sector approaches incident reporting. Cloud-based systems enable teams to access critical safety data from anywhere, while automation eliminates the manual workload traditionally associated with compliance documentation. This shift creates more than efficiency—it builds a culture where safety becomes embedded in daily operations.
AI-driven analysis tools represent the next frontier in this evolution. These systems can detect subtle patterns in incident data that human reviewers might miss, enabling earlier intervention before minor issues escalate into serious events. For companies operating in high-risk environments like offshore drilling, this predictive capability provides invaluable protection for both personnel and assets.
Q-Hub stands at the forefront of this transformation, providing tailored digital solutions that address the unique challenges of incident reporting in the oil and gas sector. By combining intuitive interfaces with powerful analytics, their platforms enable companies to achieve compliance excellence while building stronger safety cultures.
Ready to transform your approach to incident reporting and compliance management? Discover how Q-Hub's customised solutions can help your organisation achieve greater accuracy, efficiency and safety outcomes through digital transformation.