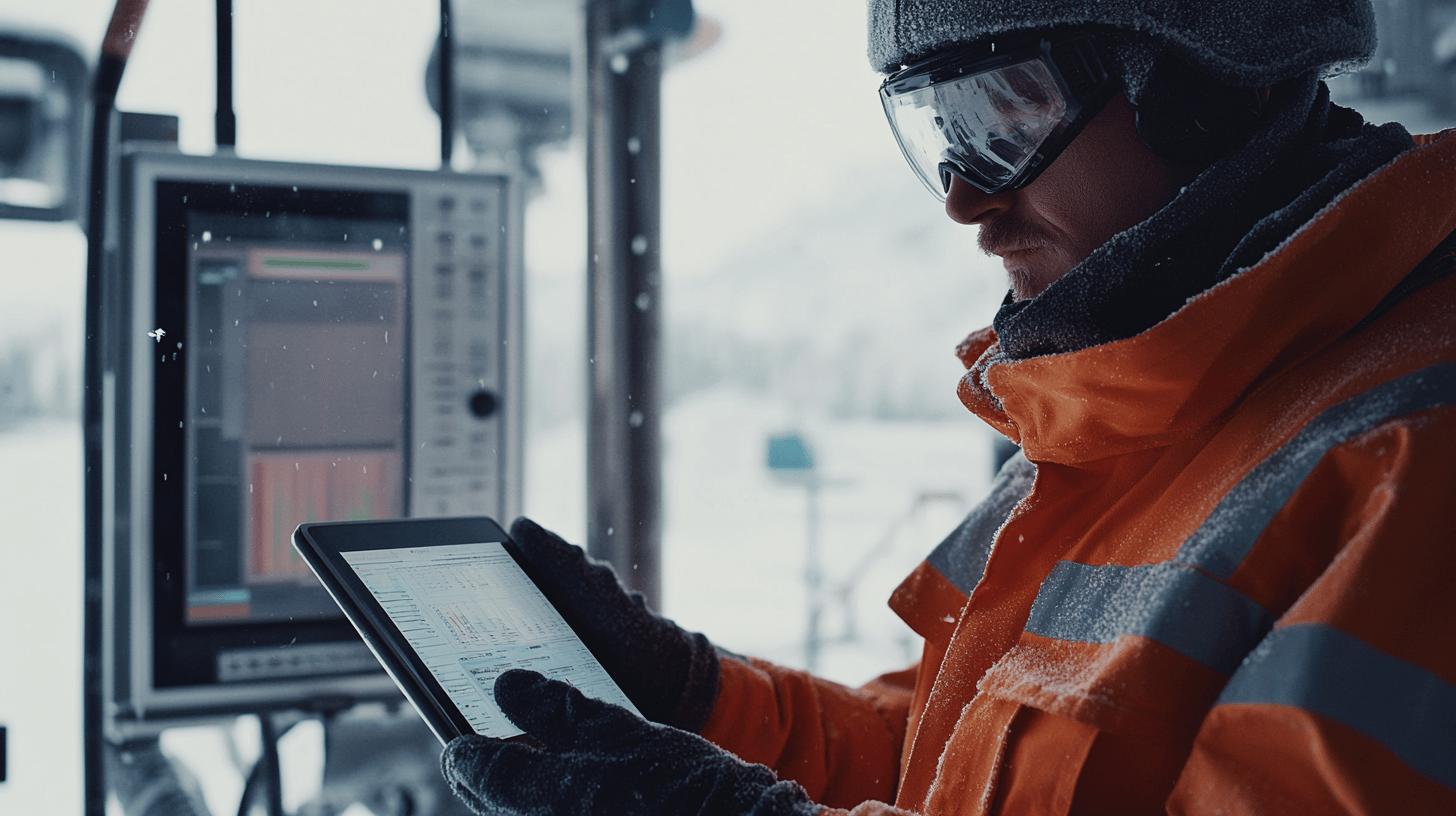
Data Management Solutions Boost Safety Accuracy in Facilities
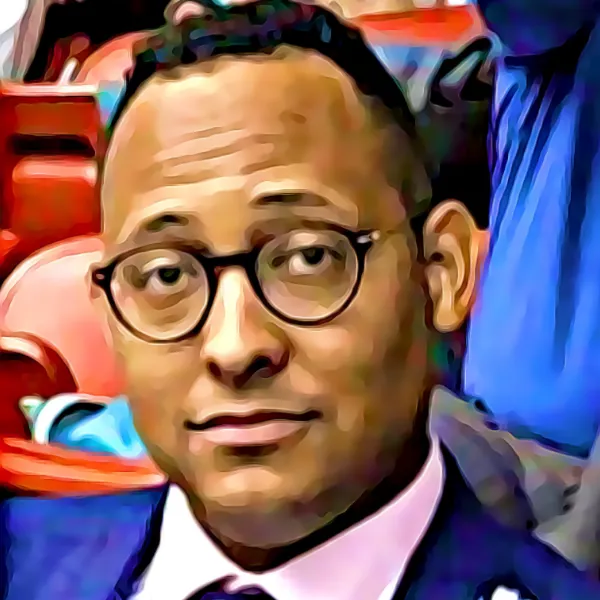
The Role of Data Management Solutions in Accurate Safety Management for Facilities Operations
In facilities operations, accurate safety management data makes the difference between a well-functioning system and a hazardous environment. Data management solutions provide centralised platforms to record, monitor, and analyse critical safety information. These systems ensure robust compliance while optimising operational efficiency. Without proper data organisation, facilities face costly errors, missed deadlines, and increased risks. Q-Hub's safety data management systems have become essential in modern facilities management, transforming reactive processes into proactive strategies.
Leveraging accurate safety data isn't just about compliance—it's about creating an environment where risks are identified before they become incidents.
By automating reporting processes and providing real-time insights, these tools streamline complex compliance demands. Facilities can now focus on proactive risk reduction instead of struggling with fragmented records, ultimately creating safer working environments.
Why Traditional Safety Management Falls Short
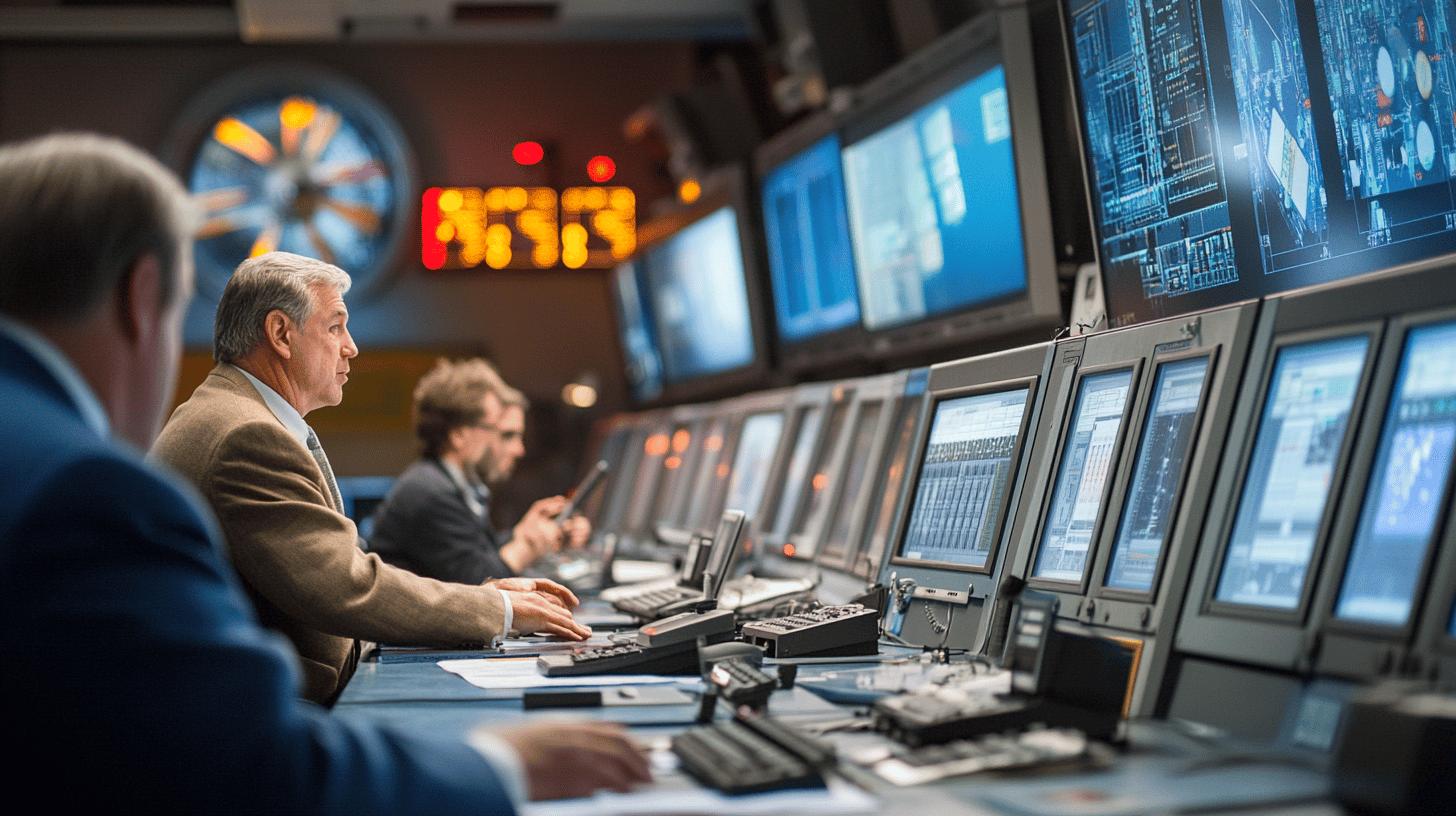
Paper-based systems and disconnected spreadsheets create significant blind spots in safety management. When information is scattered across multiple platforms, critical warnings can be missed and compliance deadlines overlooked. These fragmented approaches also make it nearly impossible to identify patterns that could prevent future incidents.
Scottish Leather Group faced this exact challenge before implementing Q-Hub solutions. Their paper-based systems struggled to keep up with the complexities of adhering to various ISO standards, consuming resources and hindering efficiency across multiple sites.
With Q-Hub's data management platform, they unified their processes, streamlined compliance, and digitised critical workflows to support growth and operational excellence.
- Centralised storage of safety protocols and documentation
- Real-time safety data monitoring and reporting
- Automated compliance tracking with industry standards
- Enhanced risk assessment capabilities
- Data-driven decision-making through analytics
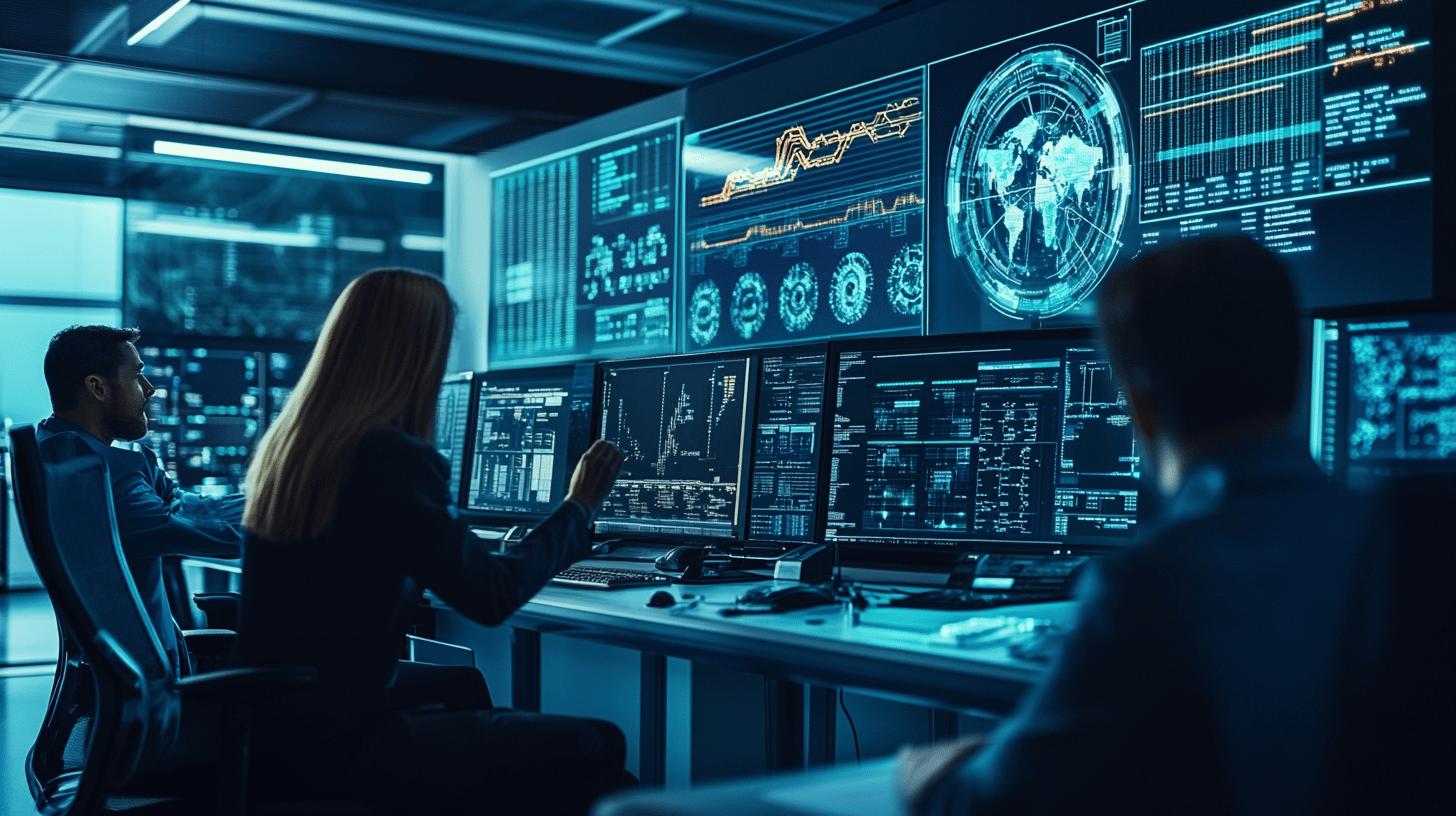
Transformative Features That Drive Safety Excellence
Modern safety data management systems offer several core capabilities that revolutionise facilities operations. The most effective solutions combine these features to create a comprehensive safety ecosystem.
Automated compliance tracking eliminates the risk of missing deadlines while reducing administrative burdens. When Rocal Insulating Panels implemented Q-Hub's solutions, they transformed their paper-based accident reporting and investigation system into streamlined digital workflows. This enabled quicker resolution and better involvement of department managers across their operations.
Predictive Intelligence: The Future of Facility Safety
Integration with IoT devices takes safety management to a new level. Sensors can capture detailed data from facility operations, feeding it directly into the safety management system. This enables predictive analytics that can forecast potential equipment failures before they occur.
Weston Aerospace leveraged Q-Hub's predictive capabilities to address recurring equipment issues. By integrating analytics into their safety management tools, they significantly reduced equipment downtime while enhancing workplace safety by preventing unexpected machinery failures.
Seamless Integration: The Key to Operational Success
One of the biggest challenges in facilities management is connecting new safety systems with existing operations. Modern solutions must bridge the gap between isolated systems, enabling all technologies to function cohesively.
This need for seamless integration mirrors the benefits provided by integration with ERP systems, where comprehensive connectivity enhances overall operational efficiency. Much like the careful synchronization of gears in a well-tuned machine, integrating ERP systems with safety management platforms ensures that every part of the operation communicates effectively, boosting accuracy and reducing risk across facilities.
Centralised data platforms serve as a single source of truth for safety management. They consolidate protocols, incident reports, and hazard assessments into one accessible system. This eliminates the need to search through spreadsheets or email chains to locate compliance records.
Anglia Cathodic Protection Services experienced this transformation firsthand. Before implementing Q-Hub, their safety data was stored across spreadsheets and paper-based systems, leading to miscommunication and errors. Q-Hub digitised these processes, making the system more accessible and actionable for all employees.
Facilities using integrated data management solutions report these key benefits:
<table border="0"> <tr><th>Metric</th><th>Before Automation</th><th>After Automation</th></tr> <tr><td>Compliance Rate</td><td>65-75%</td><td>95-100%</td></tr> <tr><td>Audit Preparation Time</td><td>3-5 days</td><td>4-6 hours</td></tr> <tr><td>Incident Response Time</td><td>Hours/Days</td><td>Minutes</td></tr> <tr><td>Documentation Accuracy</td><td>60-70%</td><td>98%+</td></tr> </table>The Road Ahead: Innovations Reshaping Safety Management
The future of data management in facility safety is evolving rapidly. Innovative safety solutions now harness predictive safety analytics—technologies that analyse patterns to forecast potential safety issues before they occur.
BMC Analysis experienced this evolution after implementing Q-Hub solutions. Their Process Hub revolutionised workflows by offering a centralised digital platform with automated tracking and reporting. With notifications and due dates built into the system, issue resolution became significantly faster, while live KPIs provided immediate insight into process progress.
Looking ahead, these trends will continue to shape facility safety:
- IoT and AI Integration: Real-time monitoring devices coupled with artificial intelligence can detect potential hazards before they manifest and optimise maintenance schedules proactively.
- User-Friendly Mobile Interfaces: Enhanced mobile access allows safety managers to retrieve and act on critical data while on the move, dramatically improving response times.
- Sustainability Integration: Advanced systems now combine safety and environmental monitoring, helping facilities reduce their overall ecological footprint while maintaining rigorous safety standards.
As these technologies mature, the line between safety management and operational excellence continues to blur. Q-Hub's comprehensive solutions enable facilities to not only meet compliance requirements but to transform safety data into strategic business intelligence that drives growth and operational resilience.
Ready to transform your facilities operations with accurate safety management data? Q-Hub's customised QHSE software solutions can help you ensure compliance, streamline processes, and support long-term growth through digital transformation tailored to your specific operational needs.