
Data Management Solutions for Accurate Guest Compliance
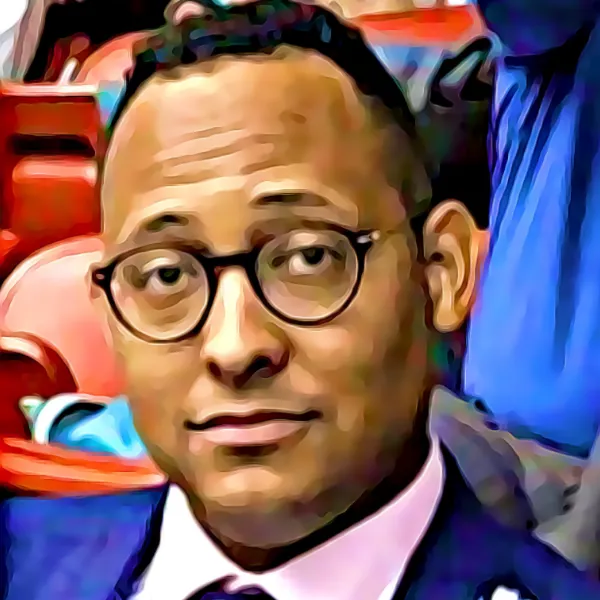
The Role of Data Management Solutions in Ensuring Accurate Guest Compliance Tracking in Engineering Projects
Tracking guest compliance in engineering projects presents significant challenges when navigating stringent safety standards and regulations. Data management solutions have become essential tools for engineering firms looking to streamline this complex process. These systems enable organisations to meet obligations under the Health and Safety at Work Act 1974 while minimising risks associated with manual tracking methods. Q-Hub's advanced compliance software helps engineering companies integrate real-time monitoring, centralised data storage, and automated reporting to address these operational challenges effectively.
Engineering sites typically host numerous visitors and contractors, each with specific safety requirements and credentials. Without robust systems in place, organisations risk missed inductions, incomplete records, and potentially serious compliance breaches. The constantly evolving regulatory landscape further complicates matters, requiring companies to maintain clear, auditable records that can withstand scrutiny.
We found that replacing our paper-based compliance processes with a digital system reduced audit preparation time by 40% while significantly improving visibility across departments. The entire workforce can now access the tools needed to perform their roles effectively.
How Digital Solutions Transform Compliance Management

Modern data management systems are revolutionising how engineering firms handle guest compliance. By implementing real-time tracking capabilities, organisations can instantly identify when contractors enter sites without proper credentials or safety inductions. As demonstrated in Weston Aerospace's implementation of Q-Hub's Audit Hub, automated alerts provide immediate notification when compliance issues arise, preventing potential safety incidents before they occur.
Centralised data storage eliminates the fragmentation that plagues manual systems. When Scottish Leather Group transitioned from paper-based processes to Q-Hub's digital platform, they consolidated compliance information across multiple sites and standards into a single source of truth. This integration significantly reduced the administrative burden while improving data accuracy and accessibility.
The impact of these solutions extends beyond simple record-keeping. Engineering firms using comprehensive compliance platforms report substantial operational improvements:
- Reduced time spent preparing for regulatory audits
- Decreased safety violations through proactive monitoring
- Improved visibility across departments and sites
- Enhanced accountability for safety protocols

Breaking Down Barriers to Effective Compliance
Engineering organisations face several obstacles when managing guest compliance. Data silos create inconsistent records across departments, while manual tracking systems introduce errors and inefficiencies. BMC Analysis encountered these exact challenges before implementing a digital solution, struggling with fragmented communication and delayed issue resolution.
Integration gaps between compliance and project management systems further compound these difficulties. When documentation exists in separate systems, maintaining a complete compliance picture becomes nearly impossible. For example, Fowlers of Bristol previously relied on emails and in-person follow-ups for critical compliance communications, creating significant operational delays.
Q-Hub's compliance management platform addresses these challenges by breaking down information barriers. The system creates seamless connections between previously isolated processes, ensuring data flows smoothly between departments and systems.
<table border="0"> <tr><th>Challenge</th><th>Traditional Approach</th><th>Q-Hub Solution</th></tr> <tr><td>Document Management</td><td>Paper-based filing systems</td><td>Centralised digital document library with version control</td></tr> <tr><td>Audit Preparation</td><td>Days of manual compilation</td><td>Automated reporting with real-time data access</td></tr> <tr><td>Compliance Monitoring</td><td>Reactive responses to issues</td><td>Proactive alerts and real-time tracking</td></tr> </table>Key Features That Drive Compliance Excellence
Effective compliance management systems share several critical capabilities that transform how engineering firms track and manage guest compliance. Real-time monitoring stands at the forefront of these features, providing immediate visibility into visitor movements and credential status. When Anglia Cathodic Protection Services implemented Q-Hub's platform, they gained the ability to instantly identify compliance gaps and address them before they became serious issues.
Integration with existing project management systems represents another crucial advantage. Rather than operating in isolation, modern compliance tools synchronise seamlessly with platforms already managing workflows and resource allocation. Rocal Insulating Panels experienced this benefit firsthand when their new system eliminated hours of wasted time searching for critical files by connecting document management with operational processes.
Automated reporting capabilities deliver perhaps the most significant time savings. These systems generate audit-ready reports at the click of a button, compiling data on inductions, certifications, and safety checks in formats that satisfy regulatory requirements. This automation not only saves valuable time but also dramatically reduces human error in compliance documentation.
Implementation Best Practices for Engineering Environments
Successfully implementing compliance management solutions requires a strategic approach focused on people as much as technology. Comprehensive training forms the foundation of any successful implementation, ensuring staff understand both the system and the compliance principles it supports. When Scottish Leather Group deployed Q-Hub across their organisation, they prioritised training at all levels, from shop floor workers to management.
Robust data governance frameworks must accompany any new system implementation. These frameworks standardise how guest data is captured, stored, and processed, preventing the inconsistencies that often lead to compliance failures. Effective governance includes clear roles and responsibilities, well-defined data access protocols, and alignment with regulations like GDPR.
Scalability represents another critical consideration for engineering firms. As Weston Aerospace discovered, compliance needs evolve constantly, requiring systems that can adapt to changing requirements without significant redevelopment. Q-Hub's modular approach allows organisations to implement specific functionality initially, then expand capabilities as needs grow.
Real-World Impact Across Engineering Sectors
The construction industry has seen remarkable improvements through digital compliance management. By implementing real-time guest tracking systems, construction firms have achieved significant reductions in safety violations. These tools ensure every visitor completes required safety inductions and follows site-specific protocols, substantially reducing accident risks.
Manufacturing operations benefit similarly from streamlined compliance processes. When Rocal Insulating Panels digitised their safety management system with Q-Hub, they transformed accident reporting and investigations from a time-consuming paper process to an efficient digital workflow. This change enabled faster issue resolution and improved accountability across departments.
Oil and gas operations face particularly stringent environmental and safety regulations. Digital compliance tools help these companies monitor contractor credentials and certifications in real-time, preventing costly regulatory violations. The ability to maintain comprehensive audit trails proves invaluable during regulatory inspections, demonstrating due diligence and commitment to compliance.
The Future of Compliance Technology
The evolution of compliance management continues at a rapid pace, with several emerging technologies reshaping possibilities. AI-driven compliance monitoring represents a particularly promising advancement, using machine learning to identify patterns and predict potential compliance issues before they occur. These systems continuously analyse data to highlight anomalies and suggest preventive actions.
Blockchain technology offers unprecedented data integrity for compliance records, creating immutable audit trails that stand up to the most rigorous scrutiny. Meanwhile, IoT-enabled tracking provides real-time monitoring of personnel movements throughout facilities, automatically confirming compliance with zone restrictions and safety requirements.
As these technologies mature, Q-Hub continues developing solutions that help engineering firms navigate increasingly complex compliance requirements. By combining innovative technology with deep industry expertise, Q-Hub enables organisations to transform compliance from a burdensome obligation into a strategic advantage that enhances safety, efficiency, and operational excellence.
Ready to transform your approach to guest compliance management? Discover how Q-Hub's tailored solutions can streamline your compliance processes while enhancing safety and operational efficiency across your engineering projects.