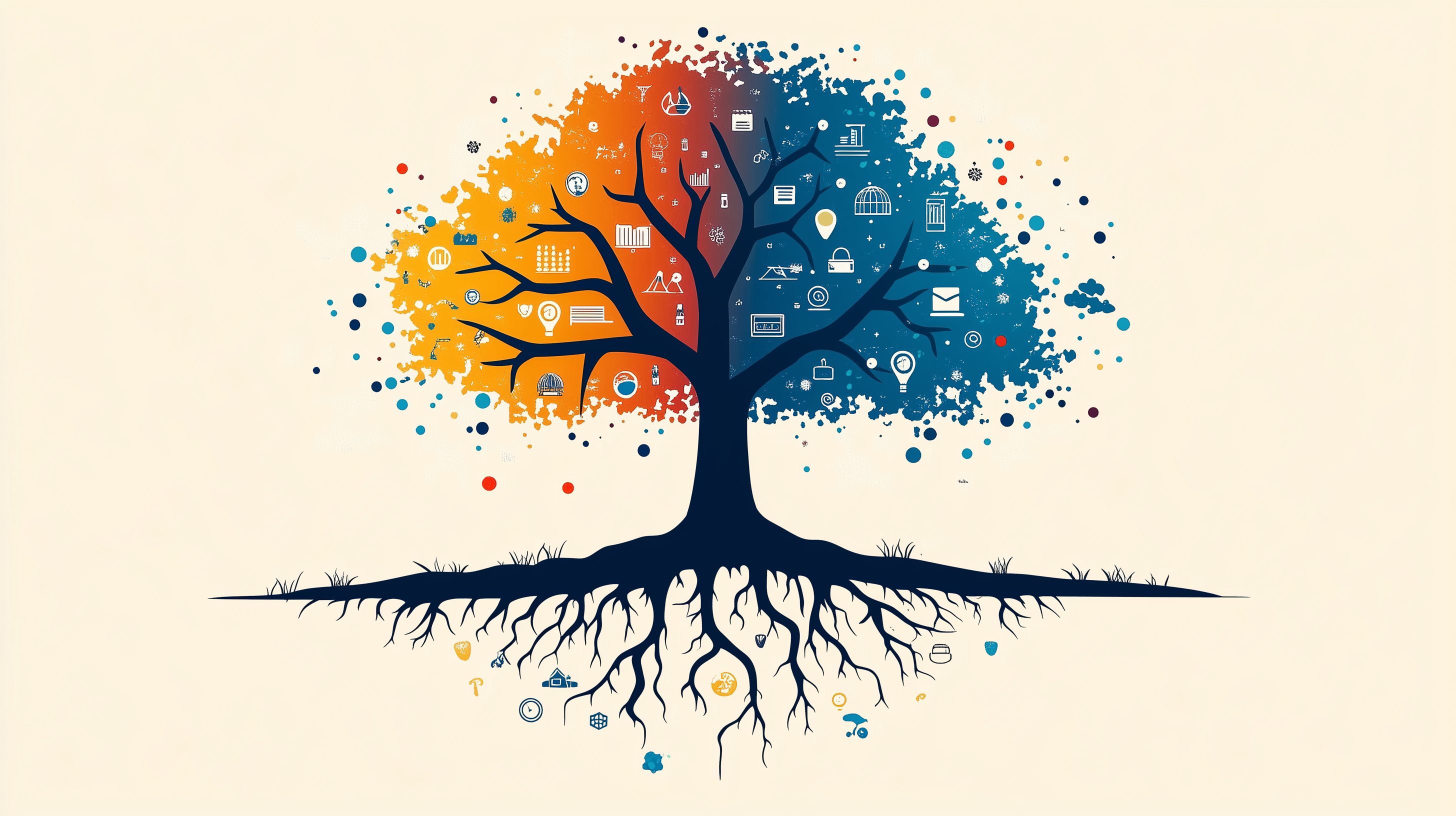
Determining Root Causes – 5Ys
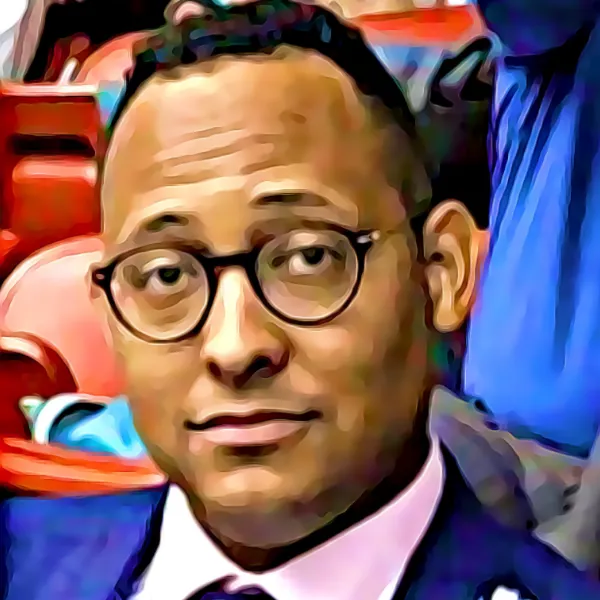
Key Takeaways
- Root Cause Analysis (RCA) is a methodology that helps determine the fundamental reasons for an issue. Most importantly, it addresses the root causes, not just the symptoms on the surface. It seeks to fix those systemic root causes so they don’t happen again and improve future performance.
- RCA is best used when dealing with repeatable problems, process optimization, and future issue avoidance. It gives organisations a forward-looking compass to orient their resilience-building efforts and improve operational sustainability over the long haul.
- Good RCA gets to the root of the matter, going beyond surface-level causes. It fosters a no-blame culture and focuses on evidence-based findings to inform the analysis process. These principles make for a correct diagnosis and invite all of us to do the work of collaborative problem-solving.
- Different techniques and tools, such as the 5 Whys Technique, Fishbone Diagram, and Cumulative Causal Factor Analysis, increase the effectiveness of RCA. Choosing the right approach to address the targeted problem is key to producing impactful outcomes.
- Conducting RCA involves clear problem definition, thorough data collection, identifying and organising potential causes, determining the root cause, and implementing targeted solutions. By taking a structured approach, you’ll be sure to analyze the root cause thoroughly and with greater impact.
- Creating a culture of continuous improvement and proactive problem-solving lays the groundwork for RCA efforts. To maintain success in root cause identification, focus on what works. Prioritize identifying root causes, building off others’ work, collaboration and visual communication.
Root cause analysis is the process of discovering the primary factors that result in a given flaw or defect. When we’re able to identify root causes, we’re able to combat challenges more accurately, streamline processes, and avoid the same issues from popping up again.This strategy is used extensively in healthcare, engineering, and business, to guarantee optimal results. By applying methods like data analysis and process mapping, we find focus and direction, and most importantly, actionable insights.In the end, determining root causes leads to more informed decision-making and creation of long-term solutions.
What Is Root Cause Analysis
Root Cause Analysis (RCA) is a tool that digs deep to find out the root cause of issues. It starts to move us away from just treating external symptoms. RCA employs a systematic process to assist organizations in discovering the underlying causes of their problems. This helps make sure that the solutions they do implement are meaningful and sustainable.
This process looks to address ongoing issues at the source. It sets the stage for more lasting change by addressing the root of the issue rather than simply slapping on band-aid solutions.
Definition of Root Cause Analysis
Root Cause Analysis, at heart, is a rigorous methodology for investigating and solving problems. It’s all about getting to the root drivers of a problem, instead of just responding to its surface-level impact. Consider a situation, for instance, where an organisation observes a drop in customer satisfaction. Slow response times are the most obvious culprit.
The true issue might be a broken communication system, or not enough staff training. RCA takes a comprehensive look at every contributing factor to make sure no detail is missed. It employs tools such as the “5 Whys” approach. Through the power of asking “why” five times, we get to the core of the issue.
Just like other tools, including fishbone diagrams or Ishikawa charts, root cause analysis helps create a visual representation of potential causes. This comprehensive, step-by-step approach eliminates the possibility of making assumptions or educated guesses.
It’s important to make a distinction here between treating symptoms and root causes, as solving for symptoms usually results in the same issue coming back around. For instance, patching up a faulty production line may temporarily resolve disruptions, but identifying and repairing the underlying mechanical flaw is key to preventing future breakdowns.
Purpose of Root Cause Analysis
The ultimate aim of RCA should be to help diagnose systemic gaps or breakdowns that lead to said problems. Root cause analysis (RCA) is a method used to find the underlying cause of problems. That includes a meaningful investigation of manufacturing defects, software glitches, and logistical failures.
By addressing the root cause of the issue, organisations are able to introduce targeted corrective actions specifically designed to tackle the root of the issue. We know that superficial fixes — though easier, faster, and cheaper — do not provide long-term solutions.
For example, replacing a malfunctioning machine part without investigating why it failed in the first place might result in repeated failures. RCA is a process to go deep to find the root cause of any failures. It reveals causes such as inadequate maintenance, inferior materials, or operational lapses.
Preventing recurrence is the third and final, but just as important, aspect of RCA. By thoroughly tackling root causes, organisations minimize risks of the same issues resurfacing. This saves time and resources while increasing transparency and confidence among all stakeholders.
Importance in Problem-Solving
RCA greatly improves an organisation’s ability to solve problems. By zeroing in on the “why,” it promotes a culture of complete and honest inquiry. More broadly, it results in more evidence-based decision-making, which ultimately benefits us all.
This proactive approach equips teams with the tools to tackle challenges with confidence, ensuring they address problems at their source. Continuous improvement is perhaps the greatest benefit from RCA.
For instance, a health care provider might use RCA to identify the causes of longer patient wait times. They may find they’re creating inefficiencies by over or under scheduling resources or how they’re deploying resources. In doing so, by working to address these root causes, the provider is very quickly able to resolve the immediate issue.
This move further increases their long-term operational efficiency as well. In the end, the true long-term benefits of RCA are found in its potential to provide long-lasting performance enhancements.
By systematically focusing on root causes, organisations can strengthen their resilience, mitigate operational risk, and foster an ecosystem of ongoing improvement. Over the long-term, such a dedication to solving root causes helps guarantee that processes, systems, and strategies are sustainable and will lead to lasting change.
When to Use Root Cause Analysis
Root Cause Analysis (RCA) should be an invaluable tool. It gives you confidence to drill down and address the root causes of problems within your organization. It’s not just a reactive tool, it’s a proactive, forward-looking method that can lead to improvements beyond safety.
By understanding when to use RCA, organisations can prevent unnecessary disruptions, increase productivity, and lay a healthier groundwork for future growth.
Identifying Repeated Issues
Recurring or repeated problems are usually the first indication that RCA is warranted. These problems may be symptoms of larger systemic breaks that need to be addressed now. To identify such problems, consider the following indicators:
- Recurring negative feedback from customers or stakeholders on a specific process or policy.
- A clear trend of mistakes or breakdowns in a given procedure.
- Persistent deviations from expected performance metrics.
- High costs with fixing the same type of issue over and over again.
- Consistent downtime or impact to operations attributed to one cause.
Understanding these trends is essential. It is through these repeated occurrences that inefficiencies or vulnerabilities are found that do not present themselves at first glance.For example, a manufacturing line where an individual piece of equipment keeps breaking down could indicate poor maintenance procedures or a need for equipment replacement. By going beyond the surface level, organisations can identify the systemic root cause and be able to address it with effective, long-term solutions.
Enhancing Process Efficiency
RCA is just as valuable for making workflows and processes more efficient. These inefficiencies usually come from root causes that, if not addressed, will hold back productivity and waste money. By applying RCA, organisations can identify these causes and enact real change.
If a project team begins to regularly deliver projects late, they need to do an RCA. This can reveal bottlenecks such as lack of clarity in communication channels or reliance on manual processes.
Combatting these root causes might mean bringing in new automated tools or reworking job descriptions to facilitate better workflow. This strategy addresses existing backlogs immediately. It also lays the groundwork for continuous process improvements, ensuring that operations are always running at peak performance.
Preventing Future Problems
Furthermore, RCA is an excellent proactive mechanism for mitigating risks and preventing potential issues before they happen. Implementing solutions that address the root causes establishes a more resilient foundation for organisations.
In the healthcare industry, RCA is used to examine medication errors. It aids in creating protocols that reduce the likelihood of such errors occurring again and protects patient safety.
Principles of Root Cause Analysis
Root cause analysis (RCA) is a systematic approach used to determine the underlying causes of issues. It’s all about getting to the root cause and not merely treating the symptoms. By adhering to clearly articulated principles, we can find meaningful lessons learned that produce lasting solutions.
Here, we dig into the principles that form the foundation for high-quality RCA, setting the stage for a systematic, team-based approach.
Focus on Underlying Causes
At the core of RCA is the art and science of going deeper than the surface problems to discover the real root causes. It takes teams willing to keep asking “why” at every level of the issue. Keep asking until they get to the root of the issue.
As an example, imagine a software crash that occurs repeatedly on a finance application. Treating the symptom would be patching the code to fix every crash when it happens. A little digging may reveal what’s really at stake. Yet the simple truth is that the legacy database architecture just isn’t equipped to meet the data needs of today.
By replacing or optimising the database with better technologies, the problem is solved in the long run, avoiding potential future disruptions. By addressing root causes, we set the stage for more enduring advances.
When we only address the symptoms, issues come back, requiring even more time and money in the long run. Hiring more staff can be an enticing solution to the chronic late project deliveries. This method usually fails to address the root cause of poor task prioritization.
Once root causes are addressed, organisations can prevent reoccurring failures, develop resilience, and work more effectively and efficiently. Separating symptoms from root causes is a key principle of RCA.
Symptoms are easier to see, feel, touch and hear – like a sudden decrease in customer satisfaction scores. The root cause behind this symptom could be anything from inadequate staff training all the way to obsolete service protocols. By focusing on the root cause, we can get to the heart of the matter and create solutions that are truly meaningful and lasting.
Avoiding Blame Culture
A productive RCA process can only flourish in a climate devoid of blame shaming. By changing our approach from blame-seeking to collaboration, we allow a safe space for team members. In this space, they feel free to share their observations and their insights.
Consider, for instance, a manufacturing defect that is later identified— a blame-centric approach would double down on individual operator errors. Instead, a collaborative culture encourages discussions around process flaws, such as ineffective quality checks or inconsistent training, leading to comprehensive solutions.
A blame-free environment allows for honest conversations, the key to working through complex problems. Team members will be more forthcoming with critical information when they don’t fear punishment.
In the case of an IT outage, your employees may be reluctant to disclose their part in the mistake. They’re afraid that if they act, they’re going to get in trouble. A non-blame culture encourages candid conversations that help resolve issues faster and more accurately.
Accountability, too, is still important, but should be positively reframed. Instead of determining who is to blame for the problem, RCA should be all about learning and improving. This approach helps to make sure that team members are not only accountable for their missteps, but enabled to drive solutions.
Emphasising Evidence-Based Findings
This is perhaps the most foundational principle of RCA. With the process rooted in factual, quantifiable findings, we eliminate guesswork and speculation. If a retail branch calls in with falling sales numbers, we must ask more questions.
Transaction records, customer and employee surveys or focus groups, and competitor analysis can help identify the root cause, be that a recession in your community or poor marketing. Findings backed by evidence are more likely to result in true, reliable root cause identification.
Imagine a situation where a manufacturing line has a persistent equipment failure. Without data, the blame will default to operator misuse. A detailed investigation of maintenance logs and operational data might reveal the root cause of equipment failures.
Further, it can identify that poor lubrication schedules were the root cause. This understanding allows for focused interventions that effectively address the root cause. Documenting observations, facts, etc., is critical from the beginning and throughout the RCA process.
Thorough and well-maintained documentation promotes transparency, transfer of institutional knowledge, and avoids the need for anecdotal evidence. A well-documented RCA is not just an important piece to solve existing problems — it can be a great resource for future issues.
Methods and Tools for Root Cause Analysis
Root Cause Analysis (RCA) is a logical and structured approach. It seeks to find the root causes of issues in order to avoid their recurrence. By applying the best methods and tools available, we can get to the bottom of not only symptoms, but root causes. This section outlines how different techniques and methodologies can be used to improve the RCA process.
1. The 5 Whys Technique
The 5 Whys technique is a simple but effective tool for getting to the root of issues. Document the problem. All RCA processes should begin with a clearly written problem statement. Next, ask “why” five times to get to the bottom of the issue and identify the true root cause.
For example, a software application that keeps crashing would cause us to drill down into the issue to ask why it crashes all the time. If we do find a coding error, we’ll want to know why that was introduced. This level of questioning might help us identify a more systemic cause, such as a lack of adequate testing standards.
This iterative line of questioning will often uncover surprising findings and develop a more nuanced understanding of the issue at hand. To make the process more effective, we frequently pair it with other tools such as Pareto charts or scatter diagrams. These tools uncover root causes that are often more systemic and show how variables interact with each other.
2. Fishbone Diagram Method
The Fishbone Diagram, known as Ishikawa Diagram, provides a useful visual framework for categorising possible causes of a problem. By categorising causes into broad groups, such as people, processes, or technology, teams can brainstorm systematically and uncover previously overlooked factors.
For example, you can illustrate a production flaw by graphing it. In this example, the systems thinking approach shows how maintenance of equipment, quality of raw materials, and employee training all contribute to the problem. That’s why this simple diagram pairs perfectly with the 5 Whys technique.
It allows teams to illustrate complicated relationships and drill down to the root of an area of concern efficiently. Visual tools such as this encourage transparency. They are most effective in a small group of 5-10 people, often the ideal size for productive problem-solving conversations.
3. Causal Factor Analysis
Causal Factor Analysis (CFA) goes beyond the symptoms. It creates a pathway model that identifies the most critical deficiencies leading to the problem. This approach is especially helpful in pinpointing interdependencies between factors.
In IT system failures, CFA reveals the interplay between hardware malfunctions and software bugs. This just goes to show how much these issues can snowball into cascading disasters. By mapping out these connections, we can create more targeted interventions to tackle several causes at once.
Modern tools such as Splunk ITSI provide a simple approach to data analysis and visualization. They make it easy to identify and rank causal factors in order very quickly and efficiently.
4. Change Analysis Approach
Change Analysis is about figuring out what changes in operations or systems will affect by analyzing how different changes will affect the outcome. It analyzes the situation pre- and post- change to determine what new root causes have developed.
For instance, a new piece of software could unintentionally create friction with other systems. Through a methodical side-by-side comparison of scenarios, we can identify where detailed changes led to adverse outcomes. Accompanying any change with close monitoring would avoid creating harmful unintended consequences.
By integrating this approach into RCA, we make certain that changes are implemented with foresight and precision.
5. Barrier Analysis Technique
Barrier Analysis is a method focused on determining the barriers that prevent us from effectively solving problems. This method seeks to determine if current protective measures, like policy or procedure, are sufficient to protect against potential harm.
For example, in the case of a data breach, barrier analysis would help identify a lapse in access controls or encryption protocols. Breaking down these barriers does more than solve the challenge at hand; it fortifies the entire system, making it more resilient to future shocks.
Adding barrier analysis to the RCA toolkit results in a more complete analysis of all factors contributing to the RCA. This simple shift can more than triple the impact of the process.
Steps to Perform Root Cause Analysis
Conducting a root cause analysis requires a step-by-step process designed to identify the root cause of a problem. Teams can do a comprehensive investigation by adhering to a methodology. Each step is dependent on the previous one, but taken together they form a straight line to resolution. Here, we detail the key steps to perform a successful RCA.
1. Define the Problem Clearly
The first step in RCA is to define the issue with a high degree of accuracy. A poorly defined problem statement will cause confusion and result in poor solutions. Teams need to ground their work by objectively documenting observable characteristics, including the “what,” the “where,” the “when,” and the “how.
If a software application closes unexpectedly, document the specific error message received. Additionally, take note of the time of day that it occurs and what procedures it impacts. A well-defined problem sets the stage for a more concentrated analysis, helping to keep the analysis focused and on-task.
2. Collect Relevant Data
Strong data collection is key to establishing the context of the problem. Your teams need to be able to get all the information they need. This might include logs, reports, user feedback, and environmental conditions that all pertain to the issue.
Drawing out a timeline of events can be particularly useful for spotting patterns or anomalies. For instance, if a manufacturing system experiences downtime, documenting machine performance leading up to the failure can reveal contributing factors. By taking a deep dive into the data, teams are less likely to miss key insights that could prove essential.
3. Identify Potential Causes
After you better understand the problem and begin collecting data, it’s time to brainstorm possible causes. Tools such as fishbone diagrams or the 5 Whys technique can provide structure to the process.
It’s important to bring a variety of perspectives to the table at this stage, as people with different areas of expertise can offer valuable insights. In a major IT outage, network engineers, software developers, and end-users have all played key roles in providing those insights. Their feedback sheds light on the many possible root causes, from configuration errors to coding bugs to unexpected user behavior.
4. Organise and Sequence Causes
Arranging the identified causes in a clear order of cause and effect allows for the development of relationships and pathways of influence. This step usually includes developing process flowcharts or cause-and-effect diagrams to map out relationships and see the bigger picture.
For example, if the project timeline is lagging behind schedule, we may identify a connection between resource allocation, task prioritization, and external constraints. Sequencing these causes not only makes the complex problem more manageable, but helps prepare teams for more targeted investigation.
5. Determine the Root Cause
Determining what the root cause is where the heart of the analysis lies. Teams should work to understand the actual root cause rather than treating the symptoms. In this manner, they can spend their time, money, and resources on solving the main problem.
This sometimes takes the form of a more iterative process of questioning and validation. If a data center experiences an overheating event, then it is important to identify the failed cooling system as the root cause. This kind of specific identification is much more useful than simply communicating “high temperatures.
Getting it right on the identification here means it doesn’t happen again and we’re working on the right solutions.
6. Develop and Execute Solutions
Once the root cause is identified, teams can produce a highly focused, specific corrective action plan that directly tackles the identified deficiencies. This plan needs to be a public-facing document with clear responsibilities, timelines, and measurable outcomes.
Repairing an electric cooling system means replacing broken parts. That includes planning for routine maintenance and temperature monitors to detect issues before they become emergencies. Implementing the solution is only the beginning of the RCA process.
It is ongoing monitoring that makes the corrective actions truly effective and sustainable.
Strategies for Effective Root Cause Analysis
Root Cause Analysis (RCA) is a very useful, structured method. It goes beyond merely addressing the symptoms of issues to determine the underlying reason for problems. When we address root causes, we can stop problems from coming back and build solutions that last.
To make sure RCA efforts are worthwhile as well as realistic, here are some strategies to consider. These strategies encourage collaboration, clarity, prioritisation, and documentation — all essential ingredients to any successful outcome.
Collaborate with Team Members
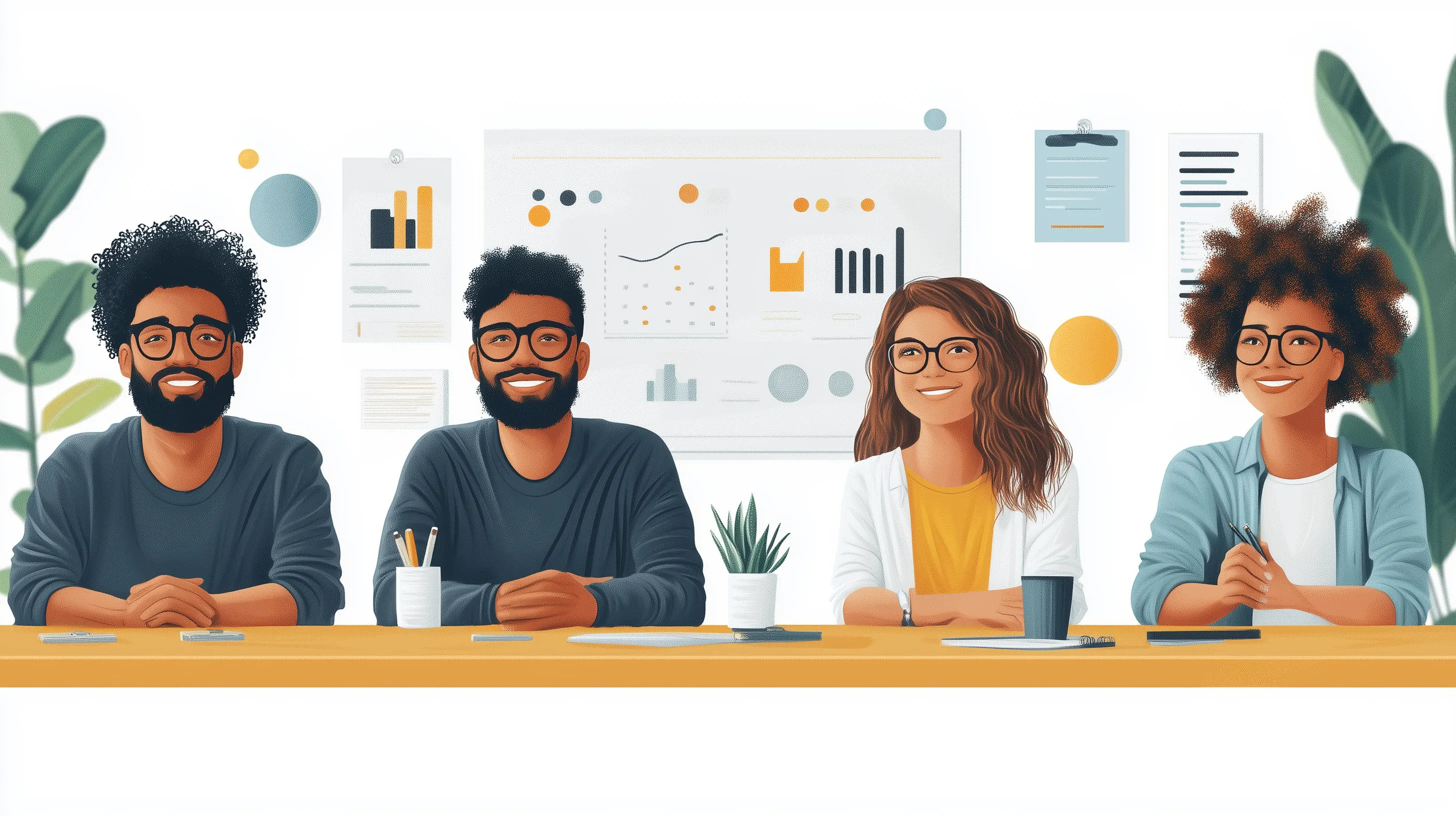
Teamwork is the best resource in RCA. Encouraging collaboration among team members allows us to draw on diverse perspectives, which often reveal insights that might be overlooked individually. For example, a software bug can only be identified if both the developer and tester provide their insights.
By including team members representing multiple roles, we create a richer, more colorful analysis. Meeting for group brainstorming lunches is another simple but effective strategy. These sessions provide a safe forum for discussion, and so participants are able to voice their observations and suggestions without fear of reprimand.
This type of collaboration can be invaluable in helping to reveal the complexities of how multiple factors might be working together to contribute to a problem. For instance, in the case of a logistics delay, brainstorming might bring to light a breakdown in communication, scheduling, or resource allocation.
Engaging relevant stakeholders at every step of the process is just as critical. Stakeholders offer invaluable perspectives, informed by their roles and responsibilities. In a manufacturing problem, it’s important to have floor operators and quality control people involved.
This understandable approach misses out on hearing all the necessary and important perspectives from supply chain managers.
Use Visual Tools for Clarity
Visual tools such as flowcharts, fishbone diagrams, and scatter plots make complex problems more manageable. These tools help to simplify complex findings, allowing you to better communicate key findings and identify causal relationships between contributing factors.
For example, a fishbone diagram is a great tool for visualizing the possible root causes of a production defect. It divides these causes into categories, for example equipment, materials, or processes. Visualisation further improves team collaboration.
A detailed process map, for example, can identify bottlenecks or inefficiencies in a workflow. By taking complex, often abstract information and turning it into something concrete and visual, these tools help build a shared understanding and keep everyone aligned.
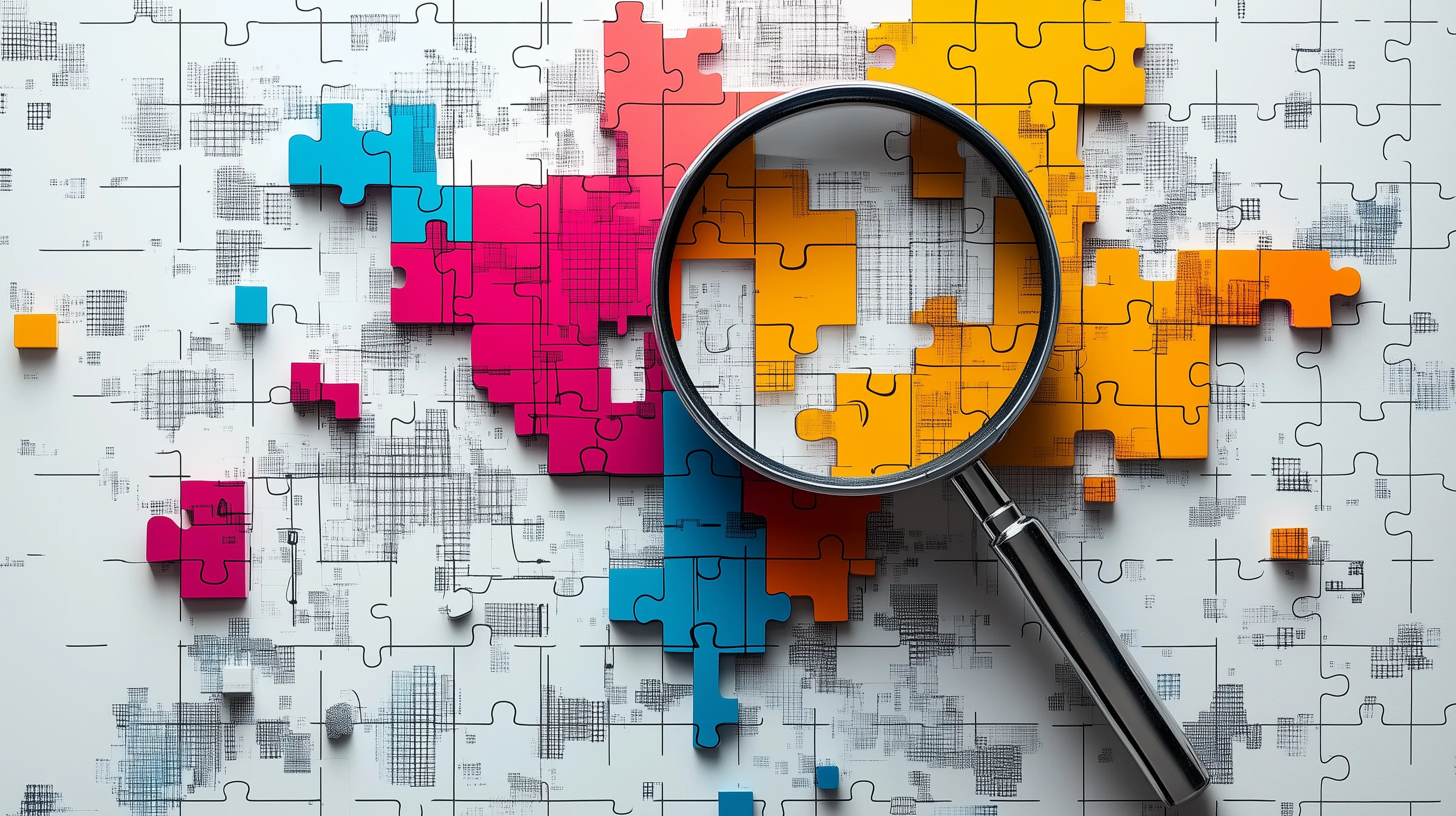
Prioritise Identified Causes
All causes are not equal in a root cause analysis. Applying the 80/20 rule, we understand that about 80% of issues can be traced back to 20% of causes. Prioritising these critical causes ensures efforts are directed where they matter most.
For example, equipment failure may be a top contributor to downtime—address this root cause first. Taking the right approach can make all the difference in making real improvements. By ranking causes according to their potential impact and likelihood of occurrence, teams can prioritize their efforts in the most important areas.
Addressing these first avoids squandering time and money on secondary, less important causes. Prioritisation leads to better resolutions that really do close performance gaps, providing a real – and measurable – value to the organisation.
Ensure Clear Documentation
By documenting observations, procedures, and final determinations, we develop a repository of information that can be referenced in the future. This is especially useful when the same root cause is identified, as this removes the need to reinvent the wheel.
I.e., recording all the steps taken and the resulting solution from a major network outage could help other teams respond faster to the same situation in the future. Well-organized documentation can help ensure accountability as well.
When actions, decisions and discussion points are kept on record, it becomes much simpler to keep progress moving forward and hold the appropriate parties responsible. Additionally, distributing these records between the various teams encourages further knowledge transfer, allowing others to learn from previous difficulties and resolutions.
Practical Applications and Examples
Root cause analysis (RCA) is a proven technique for problem solving. It’s designed to get to the root of whatever’s bothering you — not just mask the symptoms. Its applications across industries and contexts provide powerful insights that drive impactful solutions. Here’s how RCA is being used; below we dive into real-world examples, methods, and actionable steps.
Example Problem Overview
Imagine a production line that keeps running into the same delays over and over again. The catch has been that completed products are regularly lagging days behind schedule, forcing them to miss delivery commitments and lose customer trust.
With significant financial strain due to delays, the factory is currently producing consumer electronics. Missing deadlines is having a huge impact on our bottom line. Knowing the history of this issue is key to being able to truly apply RCA the right way.
When we dig in and look at the production process, we see bottlenecks occurring at different stages. The true reason behind these delays is unknown. RCA is critical here to use a structured process to unpack the problem and understand what’s really causing these delays.
Applying the 5 Whys Method
The 5 Whys technique provides a simple but effective method to get to the root of the manufacturing delay issue. What’s causing the slowdown in manufacturing? That question brings us to the first response—assembly is taking longer than we thought.
If we ask “why” a second time, we see that one of the most important pieces usually comes in much later. As we progress through this process, we learn that the supplier cannot keep up with demand.
We ultimately find the underlying cause to be mis-specification of forecasting the needed elements. This iterative questioning ultimately exposes the root cause—poor demand forecasting—and provides a path forward to rectify it. With these insights in focus, the team is able to go beyond and fix the root cause to avoid future delays.
Using a Fishbone Diagram
A Fishbone Diagram, or Ishikawa Diagram, allows us to visually group the possible causes of the production delays. To illustrate this example, we could group causes into broader categories like Materials, Methods, Manpower, and Machinery.
For example, under “Materials” we could name delayed component shipments, and “Methods” might feature an inefficient scheduling practice. This new structured visualization helps with understanding the broader contributing factors and helps to focus in on the major areas needing further investigation.
We take a deep dive into each category. This is a better approach, as it allows us to see how various elements intersect and play a role in the issue.
Identifying the Root Cause
This step is about focusing the 5 Whys and Fishbone Diagram’s findings. In this example, the public record repeatedly indicates forecasting miscalculation as the key culprit behind the project’s delays.
Being able to differentiate between closely linked issues, like supplier performance and communication gaps, allows us to hone in on what needs the most attention. This strategic clarity enables the team to focus time and money on addressing the root cause of the problem, not just treating the more peripheral symptoms.
Suggested Solutions and Actions
We found out what was really at the heart of the problem. To improve it, we can use better forecasting software and increase coordination between factory and supplier.
Customizing these solutions to the factory’s particular needs helps to make sure they’re actually fixing what’s deficient. Continued oversight is key.
Keeping improvements consistent and avoiding going back to the old ways comes from regularly reviewing forecasting accuracy and supplier performance. This forward-looking approach allows for long-term efficiency and reliability in the production process.
Preparing for Future Analyses
Understanding the underlying causes of issues means more than just addressing the short-term solution. It lays the groundwork for future analyses to improve. Let’s learn from our previous analyses and make our process more efficient. Through developing a continuous problem-solving culture, root cause analysis (RCA) can be made a cornerstone of our organizational success.
Let’s take a look at how each of these features helps you to be ready for future analyses.
Learn from Previous Findings
Looking back on RCA findings is a valuable exercise in making future analyses better. All teams should regularly go back through historical data to identify trends, patterns, or issues that may be cyclical. If a particular manufacturing defect is found again and again on different projects, it is a sign of a systemic problem.
This issue may be due to either the production process or the supply chain. Learnings from history like this are invaluable for teams to sharpen their focus and find deeper trends below the surface that would otherwise go overlooked.
Additionally, learning from history improves RCA practices by allowing teams to prevent making the same mistakes again. As an example, the use of the 5 Whys technique begins with writing a clear description of the problem. This straightforward, formulaic method can identify shortcomings in previous RCAs, providing an opportunity to improve procedures and techniques.
Good brainstorming works best in smaller groups of 5–10 people. This format allows for a wide range of perspectives to be shared and heard, while maintaining a tight, productive discussion.
Continuously Improve Processes
Integrating lessons learned from RCA back into organisational processes is key to ensuring that the organisation constantly improves itself. Cloud-based project management software, such as ProjectManager, keeps all your project docs in one central hub. Having this infrastructure in place allows for more intentional tracking of RCA findings and proactive implementation.
Planning tools such as Gantt charts, kanban boards, and work breakdown structures actively identify bottlenecks that affect workflows. They offer more transparent information on cost and schedule. Continuous improvement creates organizational development and innovation.
Continuous improvement ensures that innovative, resilient teams move to fix a vulnerability before it is tested. By applying RCA findings we can dramatically improve response times, sometimes by as much as 75%. Organizations can further reduce manpower costs by 50%.
These concrete impacts show the ways in which RCA clearly leads to long-term operations efficiency and effectiveness.
Build a Culture of Problem-Solving
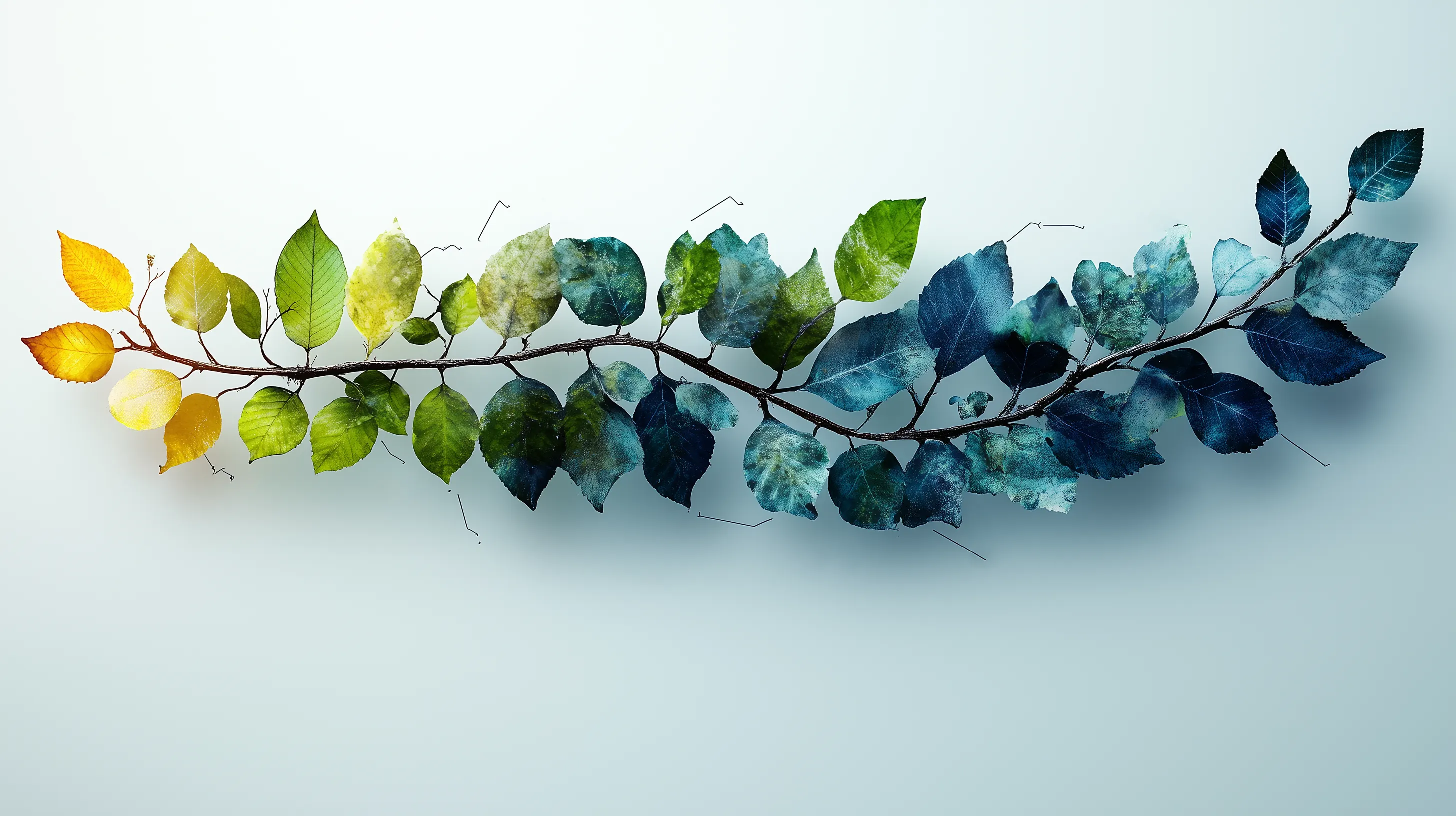
Fostering a proactive, problem-solving culture starts with incorporating RCA principles into daily operations.
Building on this mindset is essential for continuous improvement programmes. By embracing the continuous improvement programmes, organizations can systematically refine processes, ensuring that root cause analysis not only addresses immediate issues but also builds a robust framework for future resilience. When open communication is encouraged, team members feel comfortable providing valuable insights early and often, resulting in more robust analyses.
For example, fostering a workplace culture where staff feel comfortable raising their concerns can surface problems that would have gone unnoticed. The long-term health impacts of this alternative would be profound.
Setting up a strong RCA process takes time and effort. The payoff is permanent problem solving and better overall infrastructure performance. When RCA is imbued into organisational culture, teams are able to cultivate a mindset built around the practice of addressing root causes instead of symptoms.
Conclusion
Root cause analysis gives us the power to address issues at their foundation. By working upstream, we find the root causes and stop problems from coming back. The process requires patience, clear-headedness, and the right approach. Whether you choose fishbone diagrams or the 5 Whys, each tool is instrumental when used strategically. Pragmatic use cases of the real-world implementation, ranging from enhancing provider workflows to streamlining system error resolution, demonstrate its practicality.
Continually being ready to face the next challenge puts us in the driver’s seat in an increasingly accelerating world. Developing these skills, in turn, hones our capacity to find solutions and deepens our practice with thorny, multi-faceted challenges.
So in 2023, let’s keep honing our craft and sharing what we learn. Together, we can do a lot to transform those issues into opportunities. Find other tools and resources on our blog, and continue to learn and grow with us.
Frequently Asked Questions
What is root cause analysis?
Root cause analysis (RCA) is a systematic problem-solving approach used to determine the fundamental reason for a problem. It makes future issues less likely by treating the root cause instead of the symptoms. RCA is not a new discipline — it already has a long track record across industries, from healthcare to manufacturing to IT.
When should you use root cause analysis?
Use RCA for persistent problems that need solving, or when a major issue is affecting the day-to-day flow of work. It’s perfect for process improvement, failure prevention, and long-term solutions instead of short-term fixes.
What are the key principles of root cause analysis?
Key principles include starting with the root cause, not the symptoms, employing a systematic approach, and using cross-functional teams. The purpose of RCA is to figure out the “why” of an issue and put solutions in place to ensure it doesn’t happen again.
What are some common tools for root cause analysis?
Some of the more popular ones are the 5 Whys, Fishbone Diagram (Ishikawa), Pareto Analysis, Fault Tree Analysis. These tools assist with categorising data, visualising root causes, and identifying the root cause in a timely manner.
How do you perform root cause analysis?
Follow these steps: define the problem, collect data, identify potential causes, analyse to find the root cause, implement solutions, and monitor results. From start to finish, consistency and collaboration are imperative.
What are the benefits of root cause analysis?
RCA can increase uptime, stop issues from re-appearing, save you money, and make you more productive. By focusing on the root causes it achieves sustainable solutions increasing operational and organisational effectiveness.
How can you prepare for future root cause analyses?
Create case studies from previous analyses, keep careful documentation, and educate new teams on the use of RCA tools. Always be on the lookout for things that can go wrong, and encourage a spirit of problem prevention to be one step ahead.