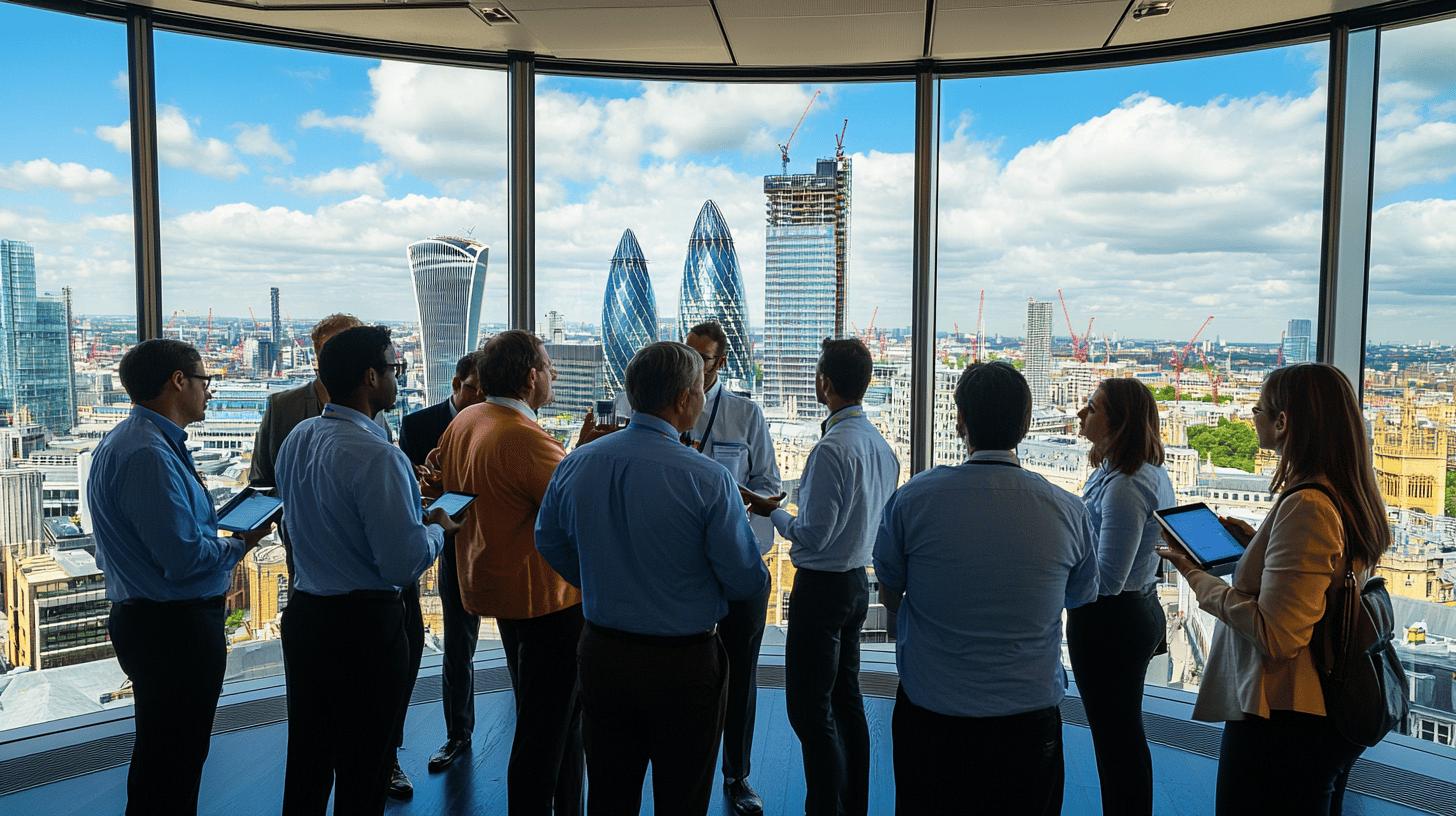
User Training and Onboarding Boosts Pharma Quality Standards
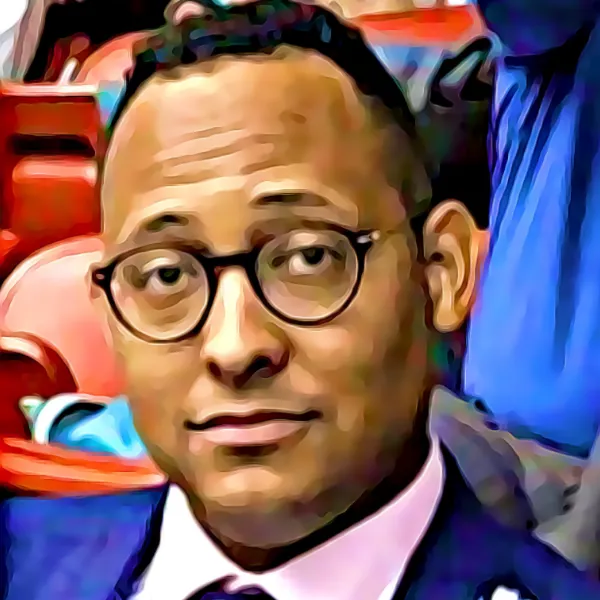
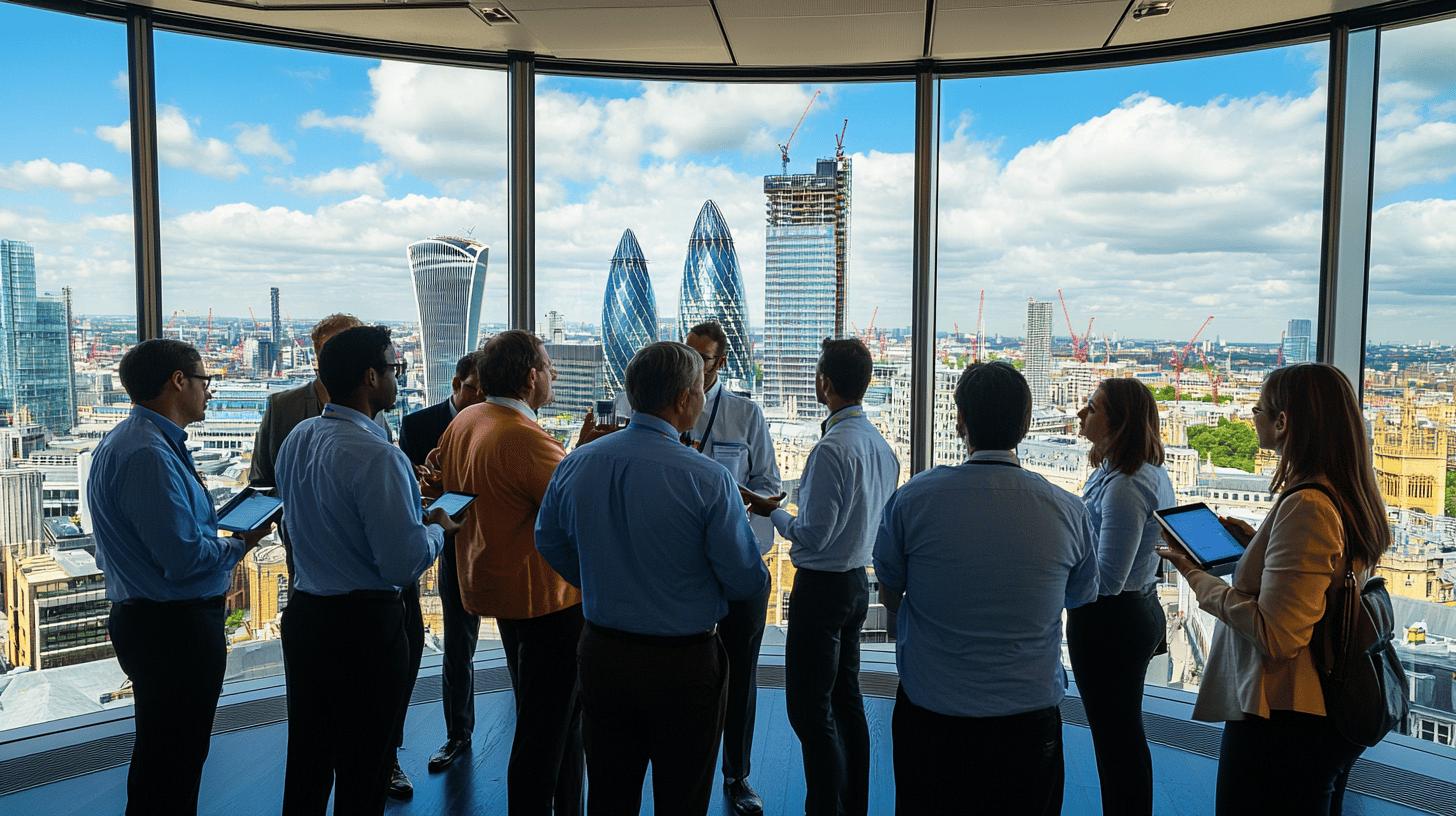
User Training and Onboarding Boosts Pharma Quality Standards
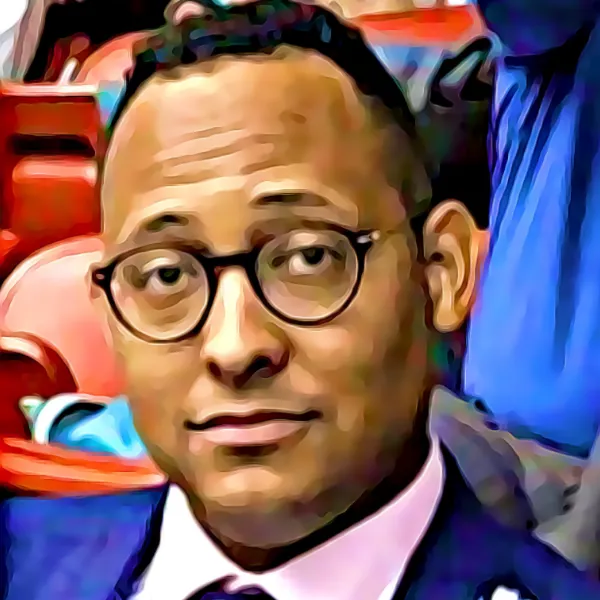
The Role of User Training and Onboarding in Improving Quality Control Standards in the Pharmaceutical Industry
User training and onboarding are essential pillars for elevating quality control standards in pharmaceutical operations. Without structured preparation, staff struggle to meet regulatory requirements like Good Manufacturing Practices (GMP), potentially leading to deviations, recalls or regulatory penalties. Q-Hub's approach to digital transformation recognises that effective training doesn't just tick compliance boxes—it creates a workforce that truly understands the "why" behind critical procedures.
Traditional training methods often fall short in practical application. While classroom sessions or basic SOP reviews might satisfy documentation requirements, they rarely translate to confident performance when unexpected issues arise. Modern, digitalised approaches focus on identifying competency gaps from day one, allowing new staff to align quickly with quality objectives through interactive learning rather than passive consumption.
When properly implemented, onboarding creates learning pathways that integrate regulatory requirements into daily workflows. This approach transforms compliance from a bureaucratic exercise into an ingrained mindset that supports continuous quality improvement.
Beyond Check-Box Training: Building True Quality Competence
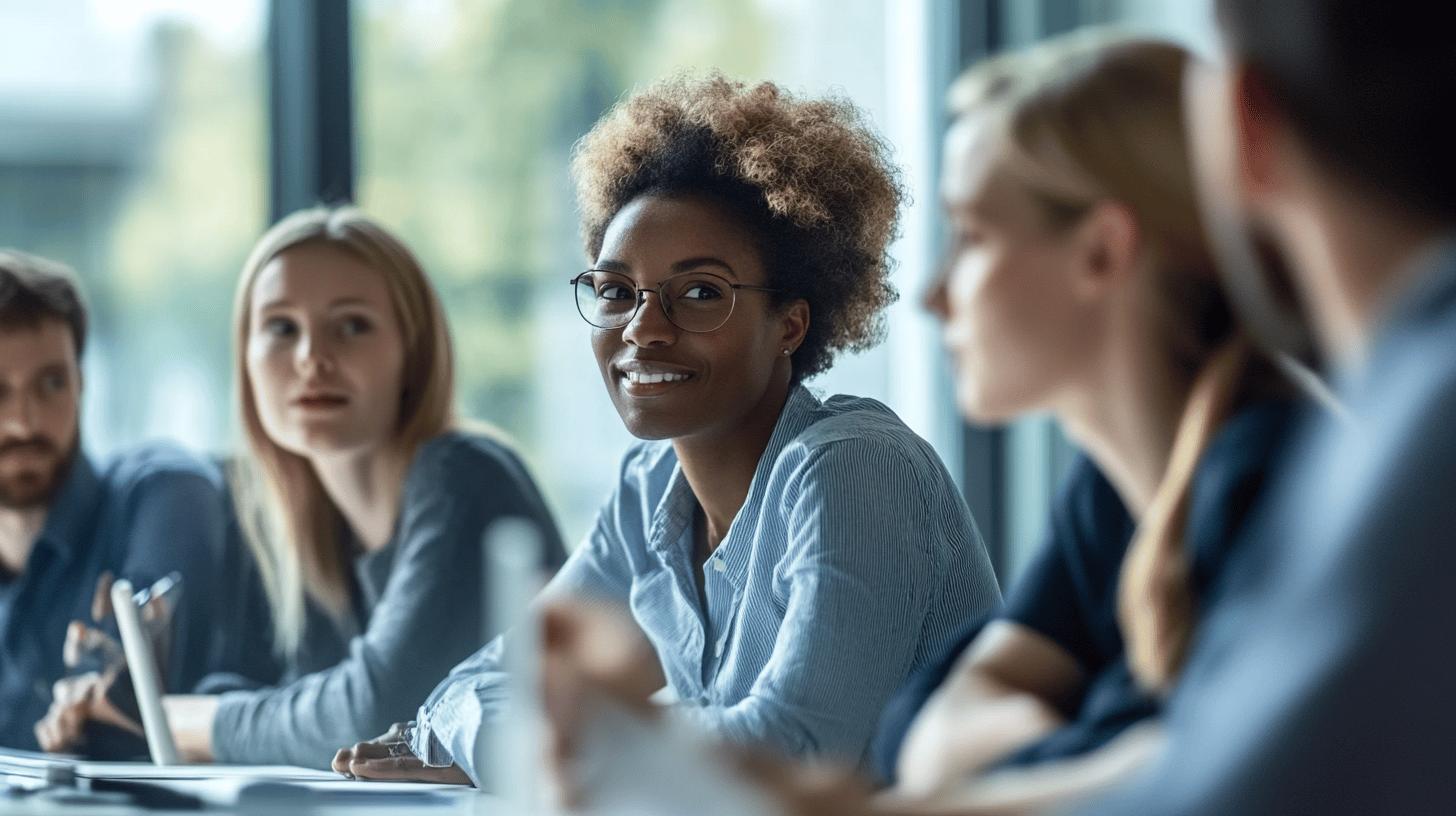
Effective pharmaceutical training is the backbone of consistent quality assurance—not just a formality to satisfy auditors. Well-structured programmes bridge competency gaps, ensuring staff can apply their knowledge when it matters most. Without such systems, employees remain unprepared for the complexities of modern pharmaceutical operations.
What makes training truly effective? Precision and practicality must take priority. Rather than abstract theory, successful programmes focus heavily on technical mastery through hands-on exercises. For example, instead of merely explaining an SOP verbally, employees should practice each step in controlled environments. This builds both understanding and confidence.
Research shows interactive methods dramatically improve retention, with hands-on learning achieving up to 75% retention compared to passive lectures. Consider these approaches that transform traditional training:
- Simulation-based learning for high-risk procedures
- Role-playing exercises that prepare staff for regulatory inspections
- Competency-based modules tailored to specific job functions
- Technology-enhanced learning using AR/VR for complex environments
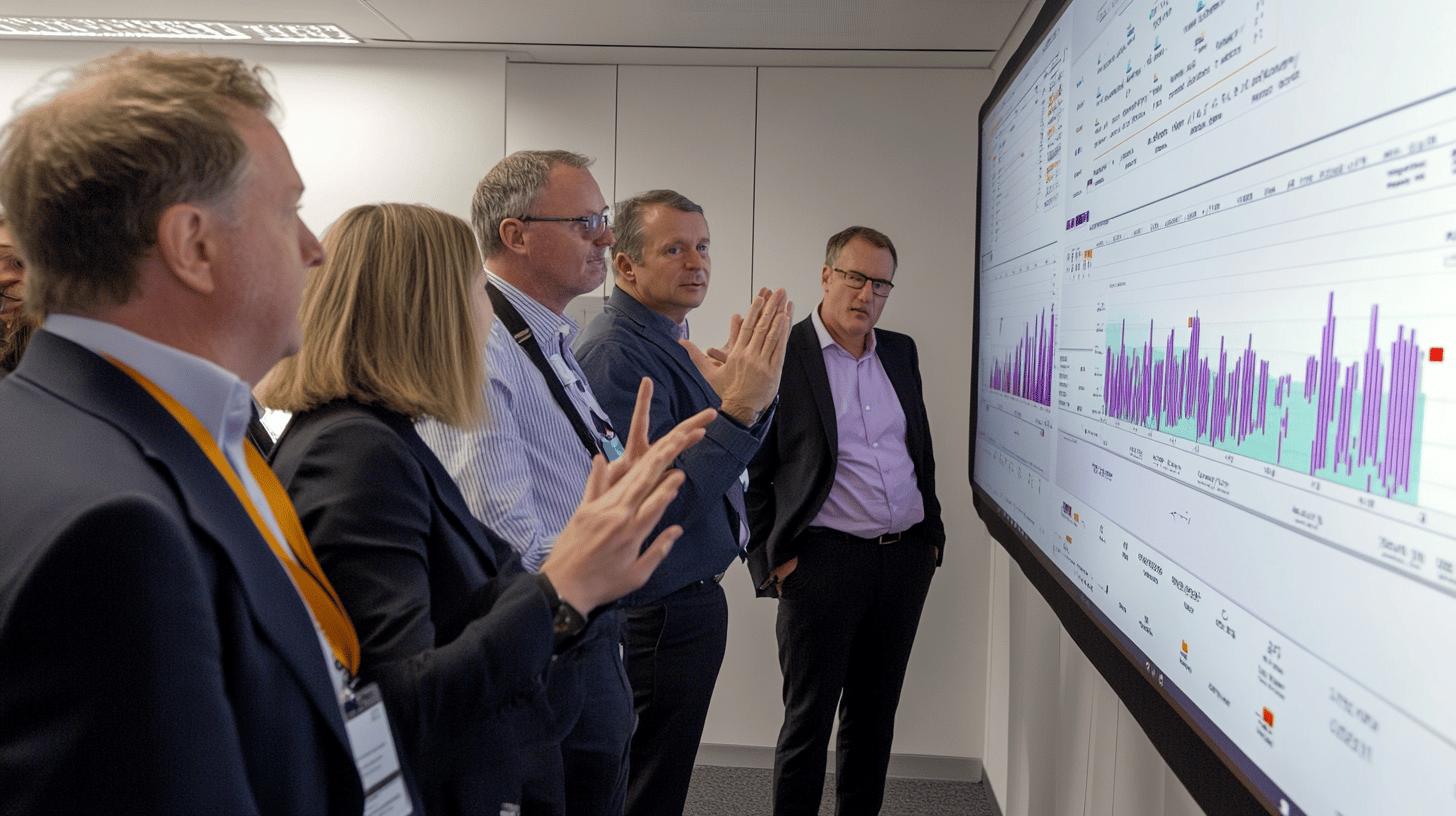
These innovations aren't just theoretical—they're driving real results across the pharmaceutical sector. By integrating such methods into comprehensive training programmes, companies ensure staff don't just understand what to do but why their actions matter to product quality and patient safety.
Creating Structured Onboarding Pathways for Quality Excellence
Pharmaceutical onboarding must place GMP guidelines at its centre from day one. When new employees understand not just procedures but the reasoning behind stringent requirements, they're better equipped to maintain quality standards consistently. This foundation-building approach pays dividends in reduced errors and stronger compliance.
A well-structured onboarding checklist is non-negotiable for pharmaceutical companies serious about quality. This ensures consistency and prevents critical training gaps that could lead to compliance issues. Effective checklists include:
"When we implemented structured, digital onboarding processes, we saw non-conformances decrease by 30% in just six months. The right training from day one means fewer quality issues down the line." Source: Quality Director, leading UK pharmaceutical manufacturer
Early engagement through mentoring and structured learning paths reinforces technical skills while improving motivation. This support system helps employees develop confidence in quality-critical roles while embedding standards into their daily routines.
Goal-setting during onboarding creates measurable outcomes tied directly to quality objectives. For instance, achieving proficiency in a specific inspection protocol within the first month gives employees clear targets that align personal development with organisational quality goals.
Sustaining Knowledge: The Continuous Learning Imperative
Continuous learning is vital in pharmaceuticals because regulations and technologies constantly evolve. Even the most thorough onboarding becomes outdated without ongoing skill development. Companies must build systems that regularly assess competencies and identify development needs before knowledge gaps create compliance risks.
Effective knowledge retention requires structured refreshers for complex procedures like equipment calibration or cleanroom management. These sessions reinforce critical tasks where even minor deviations could have significant consequences.
Adaptive learning platforms enhance this approach by customising content to address individual competency gaps. When a system identifies that an employee struggles with documentation during audits, it can automatically tailor subsequent training to strengthen that specific skill—creating targeted, efficient learning experiences.
The impact of continuous learning on quality control can be measured through these key indicators:
<table border="0"> <tr><th>Quality Metric</th><th>Before Structured Training</th><th>After Implementation</th></tr> <tr><td>Documentation Errors</td><td>8-12 per month</td><td>1-2 per month</td></tr> <tr><td>Deviation Resolution Time</td><td>14-21 days</td><td>5-7 days</td></tr> <tr><td>Audit Findings</td><td>15+ observations</td><td>3-5 observations</td></tr> <tr><td>Time to Competency</td><td>90+ days</td><td>45-60 days</td></tr> </table>Ultimately, a culture of continuous learning ensures pharmaceutical staff remain confident and capable in maintaining the highest quality standards as industry requirements evolve.
Digital Transformation: How Technology Revolutionises Pharmaceutical Training
Technology has transformed pharmaceutical training from static presentations to dynamic, engaging experiences. Modern digital solutions enhance knowledge retention and practical application far beyond what traditional methods could achieve.
Learning Management Systems (LMS) centralise training resources, ensuring consistent content delivery across global operations. This standardisation is crucial for maintaining uniform quality control practices that meet GMP requirements worldwide.
Adaptive learning takes personalisation further by adjusting content based on individual performance. If an employee struggles with cleanroom procedures, the system automatically provides additional tutorials to strengthen that specific skill—ensuring no one falls behind in critical competencies.
Virtual reality offers perhaps the most transformative potential, creating risk-free environments where staff practice complex procedures before performing them in production settings. Consider these implementation examples:
Virtual Reality Training Applications
• Cleanroom gowning procedures with real-time feedback
• Aseptic technique practice in virtual filling lines
• Emergency response scenarios for containment breaches
• Equipment troubleshooting without production impact
Companies implementing these technologies report significant improvements in training effectiveness and error reduction. The Scottish Leather Group used Q-Hub's digital platform to implement structured training across multiple sites, reducing documentation errors dramatically while improving audit outcomes.
Measuring Training Impact: Beyond Completion Rates
Evaluating training effectiveness requires looking beyond simple completion metrics to understand real-world impact. Knowledge retention rates directly correlate with how well employees apply information in daily tasks. Regular assessments reveal whether staff truly grasp concepts like SOPs or deviation handling.
Performance metrics provide concrete evidence of training success. When a facility implements new onboarding for equipment calibration and errors drop by 20% within six months, that's clear validation of the approach. These measurable outcomes justify investment in advanced training tools.
Return on investment calculations should consider the substantial costs of quality failures. In pharmaceuticals, where recalls can cost millions, even modest improvements in error rates deliver significant financial benefits. A 15% reduction in quality incidents can translate to substantial cost savings.
By focusing on these outcome-based measurements, companies create feedback loops that continuously enhance their training processes. This isn't merely about compliance—it's about fostering a workforce that consistently delivers the highest quality standards.
Real-World Success: Transforming Quality Through Digital Training
When implemented effectively, digital training solutions deliver remarkable results. Companies that migrate from paper-based systems to structured digital platforms consistently report significant improvements in compliance adherence and error reduction.
Take Anglia Cathodic Protection, which partnered with Q-Hub to transform its fragmented training approach. By digitising processes and creating structured learning paths, they eliminated bottlenecks and enhanced operational oversight. The platform's ability to track "read and understood" acknowledgments fostered greater accountability across teams while improving compliance standards.
Similarly, Fowlers of Bristol revolutionised document control through Q-Hub's digital platform. Prior to implementation, maintaining accurate documentation was a major obstacle. With robust version controls and documents linked directly to tasks, the company dramatically reduced errors while supporting their "Zero Defects" quality initiative.
These success stories highlight a common theme: when pharmaceutical organisations implement digital training strategies rooted in best practices, the benefits extend far beyond basic compliance. Staff become more engaged, errors decrease, and quality standards rise across operations.
Q-Hub's comprehensive software solutions specialise in exactly this kind of digital transformation—helping pharmaceutical companies streamline training processes, improve compliance, and build stronger quality cultures. By leveraging technology to enhance user training and onboarding, businesses can ensure staff are fully equipped to maintain the highest quality standards in this highly regulated industry.
Start using Q-Hub today
- Manage compliance in one place
- Streamline your teams and tasks
- Use Q-Hub free for 30 days