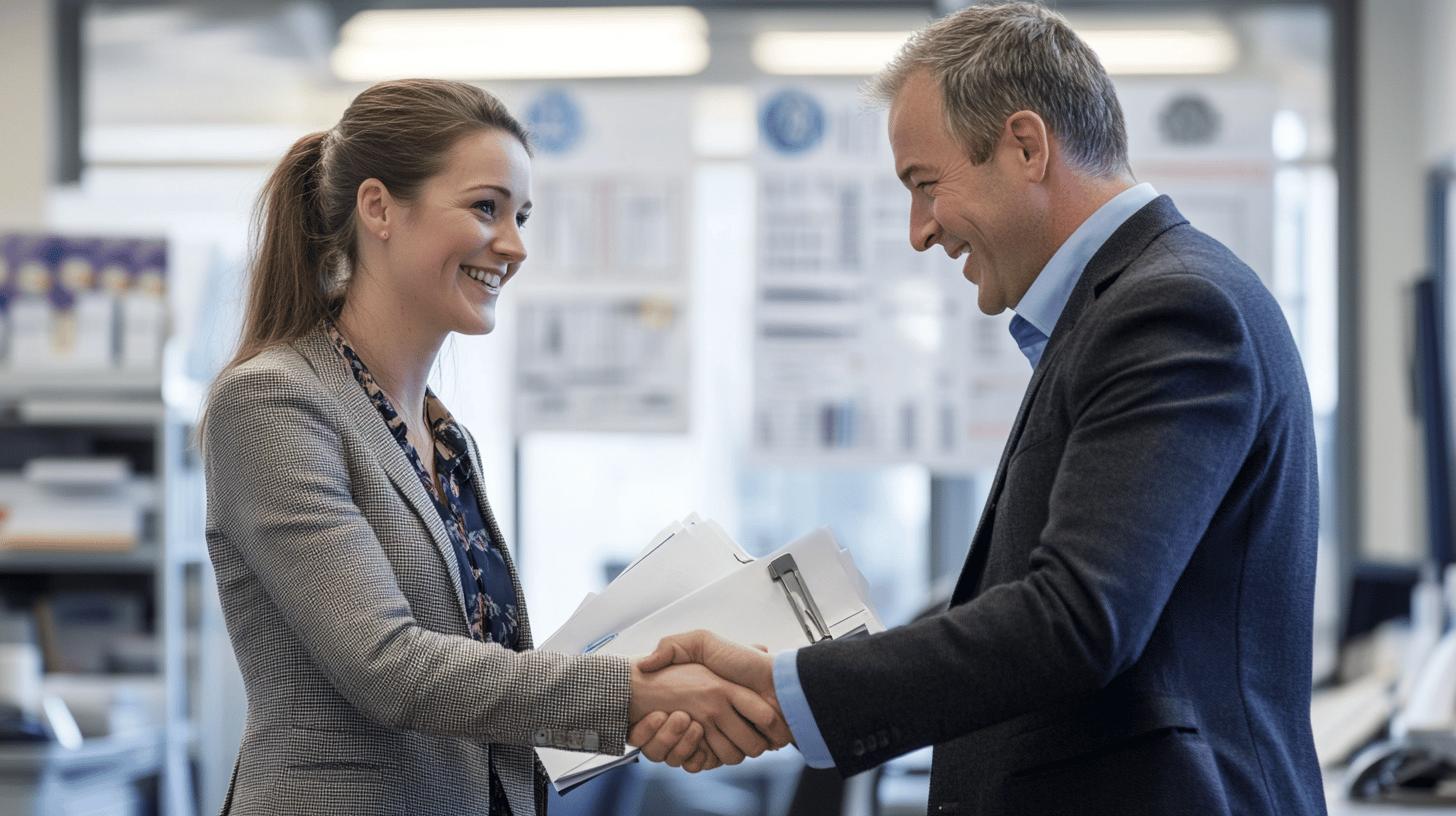
Supplier and Contractor Management: Ensuring Pharma Safety
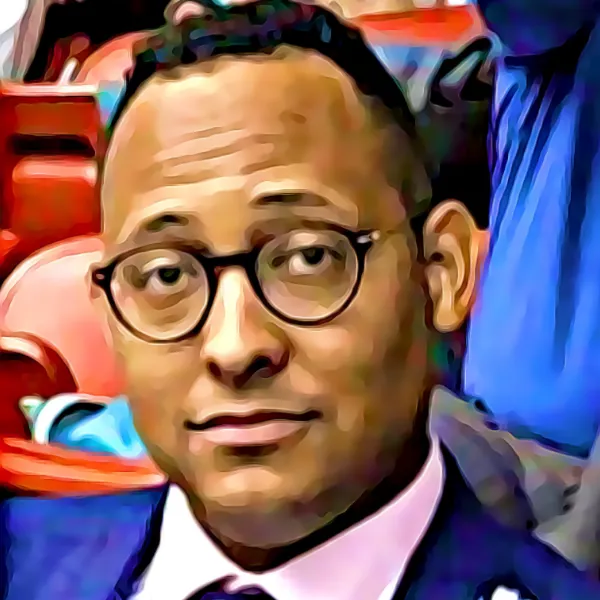
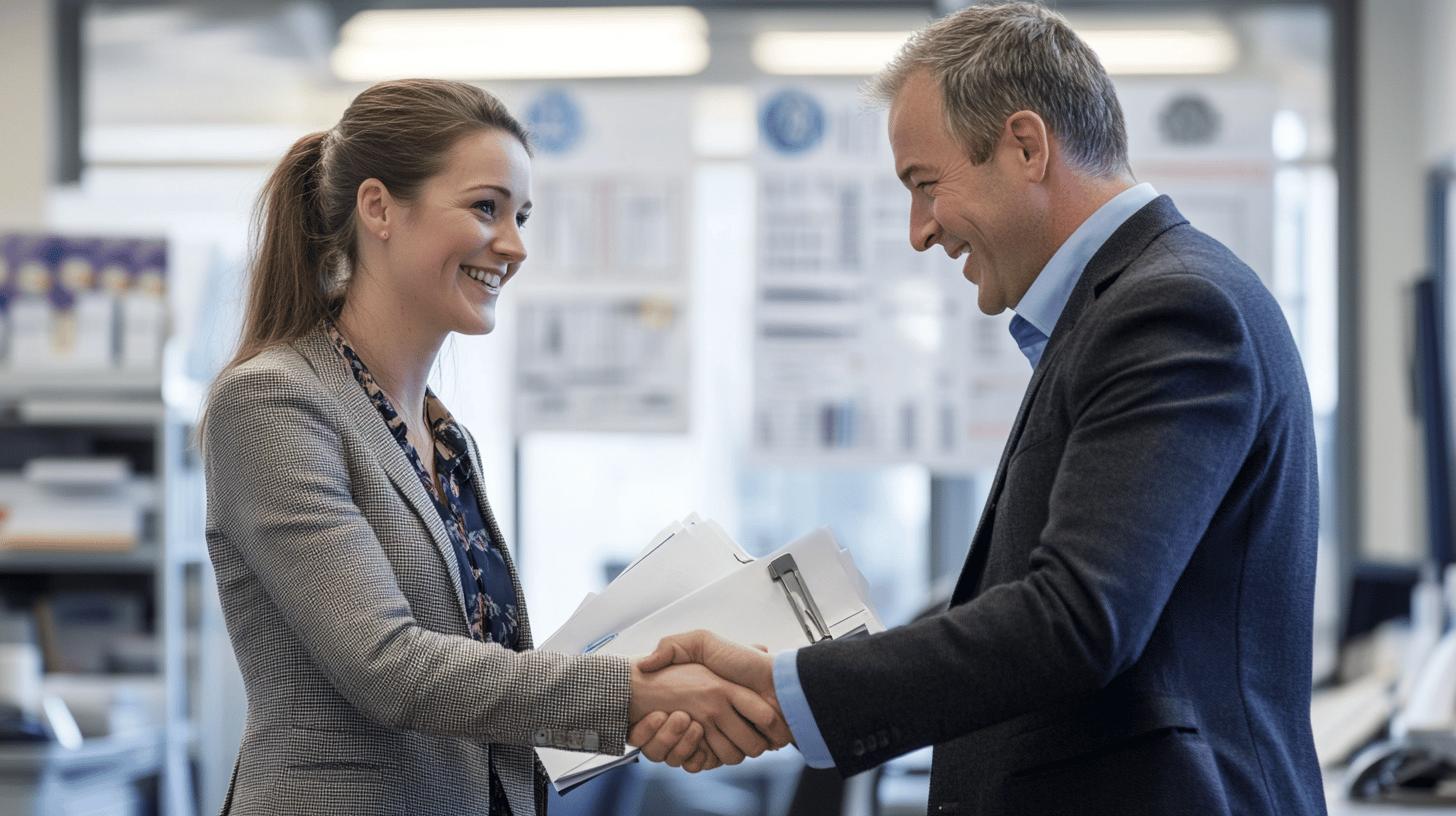
Supplier and Contractor Management: Ensuring Pharma Safety
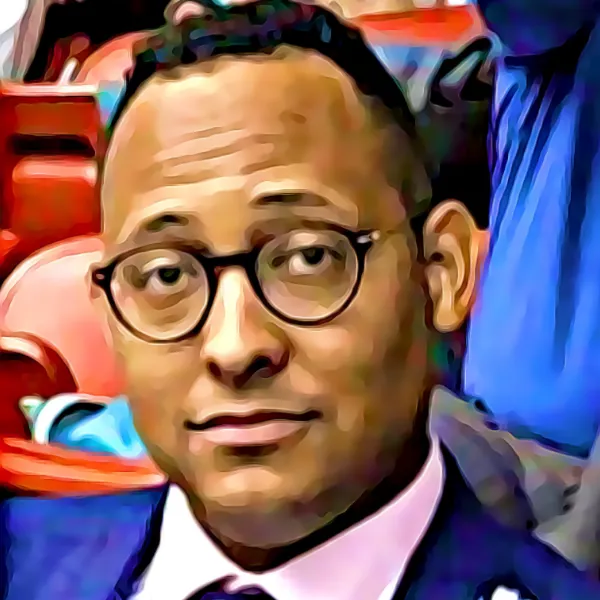
The Importance of Supplier and Contractor Management in Reinforcing Safe Sourcing in the Pharma Supply Chain
Supplier and contractor management forms the cornerstone of safe sourcing and operational integrity in pharmaceutical supply chains. Effective oversight ensures compliance with Good Manufacturing Practices (GMP) and Good Distribution Practices (GDP), creating a foundation for reliable product delivery. Without robust management systems, pharmaceutical companies face heightened risks of counterfeit products, supply disruptions, and quality inconsistencies that could compromise patient safety and regulatory standing.
At its core, this management approach is about fostering quality assurance throughout every link in the supply chain. Regular supplier evaluations and audits verify that partners meet stringent regulatory requirements while building trust between organisations. When pharmaceutical companies neglect verification of GDP compliance, they expose themselves to significant risks that could impact product integrity and patient outcomes.
Communication channels between all stakeholders—from raw material suppliers to final distributors—reinforce this integrity. Clear documentation and shared compliance criteria reduce errors and miscommunication, ultimately protecting public health through operational excellence. These systems don't just maintain standards; they create the resilience needed for pharmaceutical supply chains to withstand global challenges.
Building Blocks of Effective Pharma Supply Chain Management
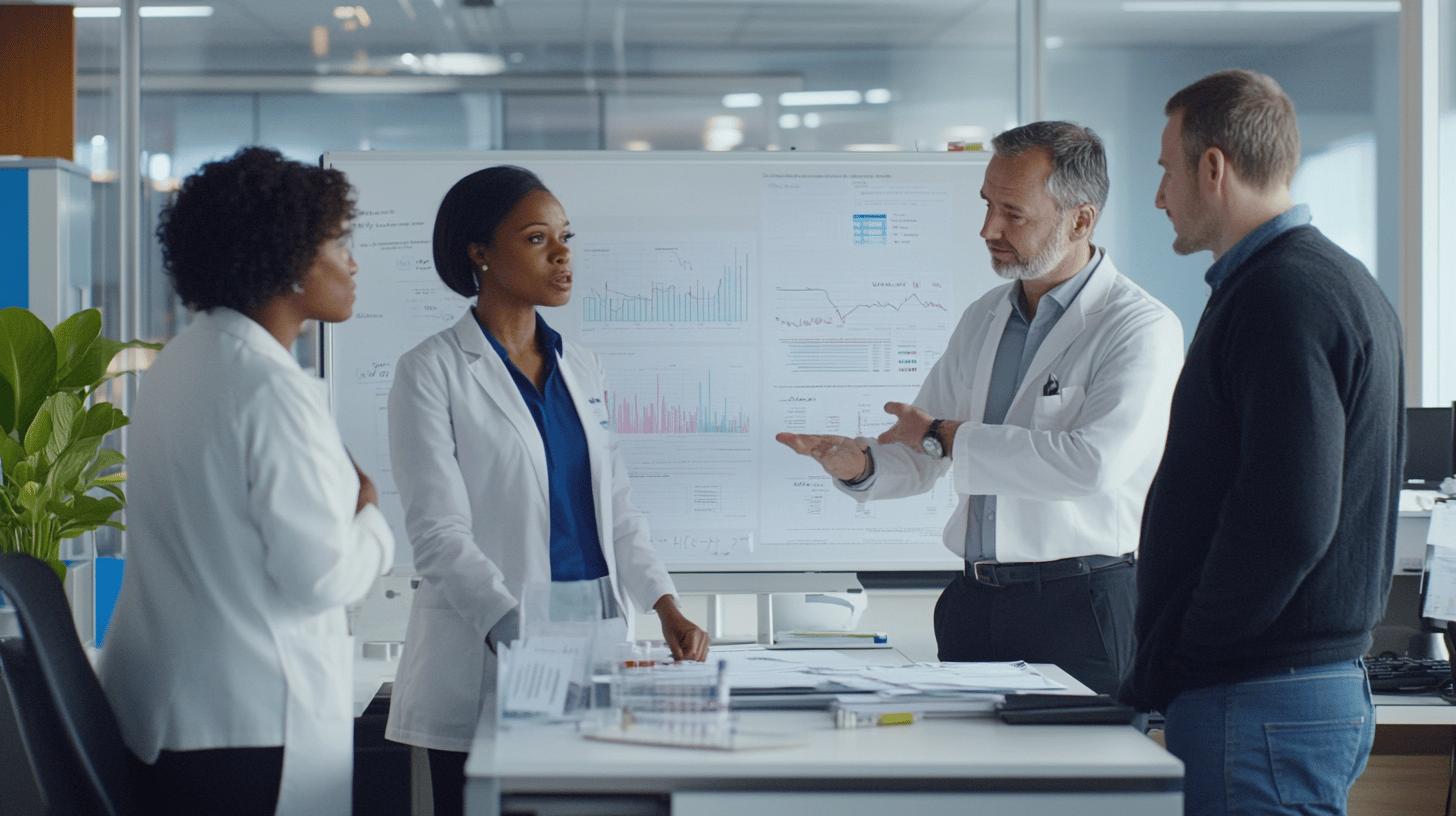
The pharmaceutical industry relies on interconnected systems where one weak link can compromise the entire chain. Q-Hub's digital transformation solutions address this vulnerability by providing integrated oversight of supplier and contractor performance through customised QHSE software. Companies using paper-based or fragmented systems often struggle with visibility across their supplier network.
Scottish Leather Group experienced this challenge firsthand, managing multiple ISO standards across various sites with limited resources before implementing Q-Hub's solutions. Their digital transformation streamlined audit preparation and reporting, creating unified processes that enhanced compliance management across all operations.
"We needed a solution to unify our processes, streamline compliance, and digitise critical workflows to support growth and operational excellence."
Source: Scottish Leather Group case study
Establishing clear evaluation criteria represents another fundamental element. When pharmaceutical companies define explicit standards for suppliers and contractors, they create measurable benchmarks for performance while reducing ambiguity around expectations. These structured approaches often include:
- Detailed quality agreements with clearly defined responsibilities and performance metrics
- Regular assessment schedules to maintain ongoing compliance verification
- Risk-based approaches that prioritise critical suppliers and high-risk processes
- Transparent communication protocols for addressing quality issues
- Documentation requirements aligned with regulatory expectations
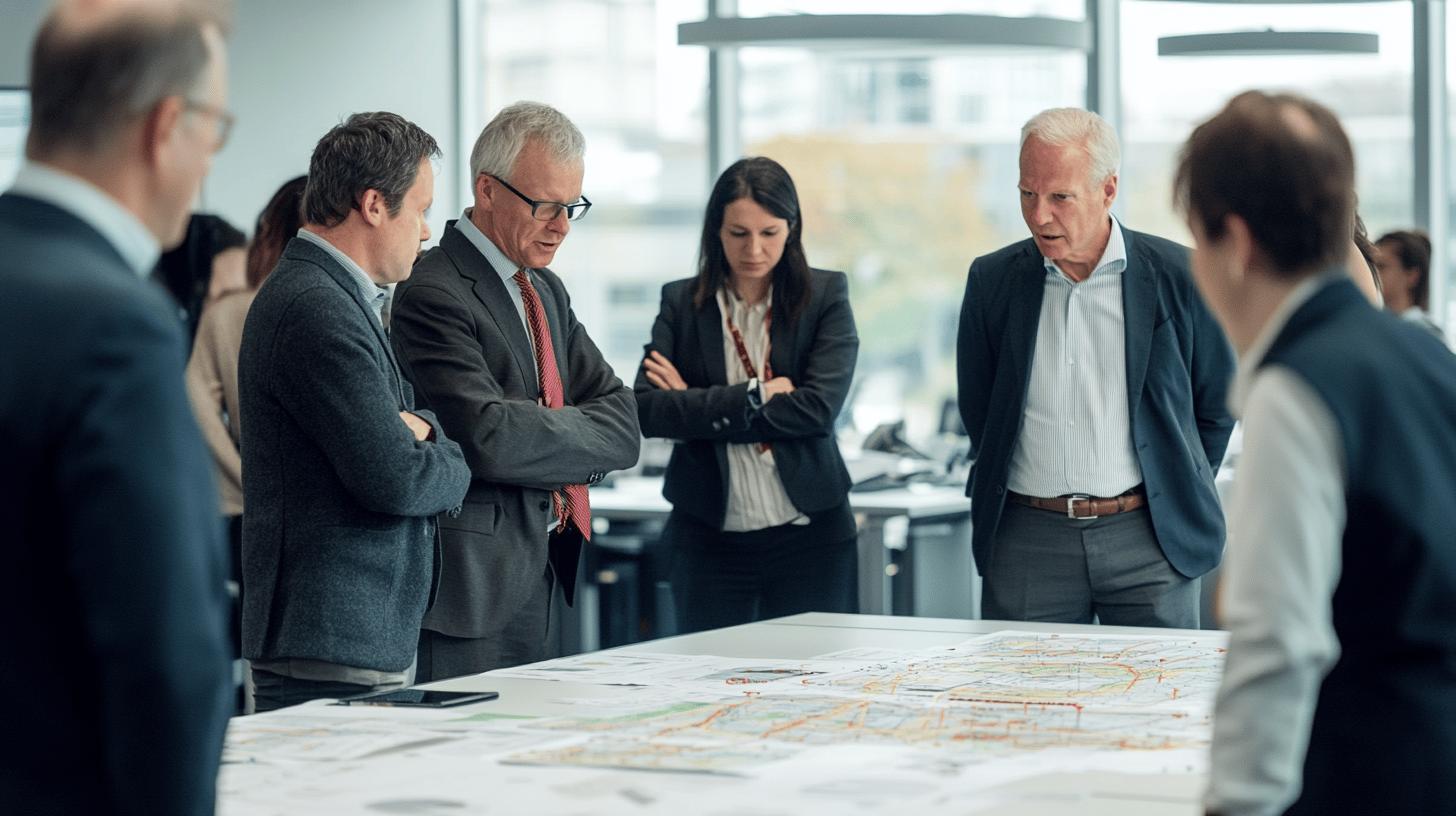
Tackling Common Compliance Hurdles Through Digital Solutions
Regulatory compliance represents one of the most significant challenges in pharmaceutical supply chain management. Companies must navigate complex requirements that vary by region while ensuring consistent implementation across all supplier relationships. Manual processes often struggle to keep pace with evolving regulations, creating compliance gaps that expose companies to significant risk.
Implementing digital solutions transforms this landscape. Weston Aerospace demonstrates how technology adoption can overcome compliance bottlenecks by centralising audit management and documentation. Their implementation of Q-Hub's Audit Hub created automated scheduling, reporting, and real-time dashboards that significantly reduced administrative burden while improving regulatory readiness.
Risk management presents another critical challenge that benefits from technological intervention. Companies need systematic approaches to identify vulnerabilities before they become problems. Digital risk assessment frameworks provide structured evaluation processes that help pharmaceutical companies:
<table border="0"> <tr><th>Risk Management Aspect</th><th>Manual Approach</th><th>Digital Solution</th></tr> <tr><td>Supplier Qualification</td><td>Paper documentation, lengthy review cycles</td><td>Automated assessment with real-time tracking</td></tr> <tr><td>Compliance Verification</td><td>Periodic audits with limited visibility</td><td>Continuous monitoring with alerts</td></tr> <tr><td>Performance Tracking</td><td>Retrospective analysis</td><td>Real-time dashboards and KPIs</td></tr> <tr><td>Issue Resolution</td><td>Email chains and manual follow-up</td><td>Automated workflow with accountability</td></tr> </table>Best Practices That Transform Supplier Relationships
Successful pharmaceutical supply chain management relies on implementing proven strategies that build reliability and compliance. Pre-qualification stands as perhaps the most essential practice, ensuring suppliers meet GMP and GDP standards before partnerships begin. This upfront investment prevents costly disruptions and compliance issues later.
Diversification represents another vital strategy. Companies that rely on single suppliers for critical components face significant vulnerability to disruptions. By cultivating relationships with multiple qualified suppliers, pharmaceutical companies create resilience against supply shortages and other challenges.
BMC Analysis demonstrated the power of digitising supplier management processes through their implementation of Q-Hub's solutions. Their transformation included:
- Centralised tracking of non-conformance reports through Process Hub, replacing fragmented email communications
- Digitised document acknowledgment systems that eliminated manual signing sheets
- Automated asset calibration schedules with built-in reminders
- Streamlined audit processes with integrated findings management
When implemented through technological solutions like Q-Hub's platform, these practices create transparent, efficient supplier management systems that enhance pharmaceutical supply chain integrity.
Leveraging Technology to Transform Supplier Oversight
Digital transformation has revolutionised how pharmaceutical companies manage supplier relationships. Compliance monitoring systems provide automated tracking of regulatory adherence, flagging potential issues before they escalate. For example, these systems can alert managers to approaching certification expirations or compliance gaps, enabling proactive intervention.
Supplier performance tracking tools deliver real-time visibility into critical metrics like delivery reliability, quality consistency, and regulatory compliance. Instead of relying on periodic reviews, companies gain continuous insight into supplier performance, allowing for immediate corrective action when issues arise.
Fowlers of Bristol exemplifies this transformation through their partnership with Q-Hub:
"Before Q-Hub, communication between teams relied heavily on emails and in-person follow-ups, which created delays and inefficiencies. With Q-Hub's intuitive portal, Fowlers brought all critical workflows, datasets, and communications into a single digital space."
Source: Fowlers of Bristol case study
Emerging technologies like artificial intelligence and blockchain further enhance these capabilities. AI analyses complex data patterns to predict potential supply chain disruptions, while blockchain creates immutable records of transactions that ensure traceability throughout the pharmaceutical supply chain.
Strategic Audit Approaches That Ensure Compliance
Supplier audits represent a critical tool for verifying compliance and quality standards. Effective audit programmes require careful preparation, including gathering information about supplier processes and previous performance before on-site visits. This preparation creates both efficiency during the audit and better cooperation from suppliers.
Rocal Insulating Panels transformed their safety management system by implementing Q-Hub's digital platform. Their previous paper-based processes for accident reporting and investigations created significant inefficiencies and delays. The implementation of automated workflows dramatically improved resolution times and management involvement in safety processes.
Different audit types serve specific purposes in comprehensive supplier management:
- Compliance audits verify adherence to regulatory requirements and industry standards
- Performance audits evaluate operational efficiency and reliability metrics
- Safety audits assess workplace conditions and risk management practices
- Quality audits examine product specifications and consistency
Implementing digital audit management through Q-Hub's platform enables pharmaceutical companies to schedule, conduct, and track these various audit types within a single system, ensuring no compliance aspects fall through the cracks.
Building Resiliency Through Proactive Risk Management
Effective risk mitigation strategies form the foundation of reliable pharmaceutical supply chains. Regular operational risk assessments identify vulnerabilities before they cause disruptions. These structured evaluations examine areas like supplier financial stability, quality control processes, and contingency planning to reveal potential weaknesses.
Third-party risk management frameworks provide systematic approaches to evaluating external partners. These structured systems ensure consistent assessment of all suppliers against established criteria, creating standardised evaluation processes that reduce subjective decision-making.
Anglia Cathodic Protection Services Limited experienced the benefits of digital transformation through Q-Hub's platform implementation. Their previous fragmented systems created compliance management challenges across multiple sites. By implementing Q-Hub's digital solutions, they gained:
- Streamlined non-conformance tracking with accountability at each step
- Real-time audit scheduling and reporting capabilities
- Improved document sharing with verification of understanding
- Enhanced visibility across operations for better decision-making
Diversification and contingency planning represent equally important risk mitigation strategies. By developing relationships with multiple qualified suppliers and creating detailed response plans for potential disruptions, pharmaceutical companies build resilience against supply chain threats.
Fostering Continuous Improvement Through Partnership
Supplier and contractor management requires ongoing evaluation and improvement to maintain effectiveness. Regular performance reviews create structured opportunities to assess supplier adherence to quality, delivery, and compliance expectations. These evaluations identify both strengths to leverage and weaknesses to address.
Implementing feedback loops ensures that performance insights translate into meaningful improvements. Clear communication channels allow pharmaceutical companies to share concerns and expectations while giving suppliers opportunities to address issues before they become significant problems.
Key performance indicators provide measurable metrics for tracking supplier performance over time. Effective KPIs might include:
- On-time delivery percentage
- Quality acceptance rates
- Compliance audit scores
- Response time to quality issues
- Documentation accuracy and completeness
Q-Hub's digital QHSE solutions enable pharmaceutical companies to track these metrics through intuitive dashboards that provide real-time visibility into supplier performance. This technological approach transforms supplier management from a periodic assessment activity into continuous oversight that drives ongoing improvement.
By implementing these comprehensive strategies through Q-Hub's customised software solutions, pharmaceutical companies can build stronger, more reliable supplier networks that enhance compliance, quality, and operational efficiency throughout their supply chains. Ready to transform your supplier and contractor management approach? Discover how Q-Hub's tailored digital solutions can reinforce safe sourcing while driving operational excellence in your pharmaceutical supply chain.
<Start using Q-Hub today
- Manage compliance in one place
- Streamline your teams and tasks
- Use Q-Hub free for 30 days